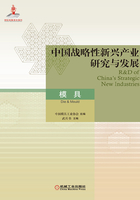
1.1 模具是工业生产的关键工艺装备
模具成形(型)是现代产品制造业中最主要的加工工艺之一,而模具是其中重要的工艺装备。
我国目前通过模具成形(型)制造(也称等材制造)的金属制品约为9000万t,与切削加工(减材制造)的数量相当;而7000万t左右的塑料制品和600万t的橡胶制品,几乎全部由模具成形(型)制造;3D打印(增材制造)的产品总量目前不超过10万t。2014—2016年3种主要制造方法年加工数量见表1-1。
表1-1 2014—2016年3种主要制造方法年加工数量

注:*为主要成形(型)方式。
1.1.1 模具成形(型)工艺流程
模具成形(型)的基本工艺流程:原料(材料)→送料机构→成形机床(锻压机床、压铸机、塑料机械等)+模具=制品、制件、零部件。不同材料的模具成形工艺不尽相同。
1.金属制品的模具成形(型)工艺
金属制品的模具成形(型)工艺主要有以下几种:
(1)铸造工艺 铸造生产是将加热熔化的金属(主要是钢、铁、非铁金属),在重力或外力(压力、离心力、电磁力等)的作用下通过浇(流)道,进入铸型(模具)型腔中并使其充满型腔,经冷却凝固成铸件(或零件)的一种金属成形方法。
压力铸造(简称压铸)是指将熔融合金在高压、高速条件下填充模具型腔,并在高压下冷却成形的铸造方法,是铸造工艺中应用最广、发展速度最快的金属热加工成形工艺方法之一。压铸是一种精密的铸造方法,压铸件的大部分表面不需再车削加工即可装配应用,从一般的照相机、打字机、电子计算器件及装饰品等小零件,到汽车、机车、飞机等交通工具的大型复杂零件都可用压铸法制造。压铸作为一种先进的有色合金精密零部件成形技术,适应了现代制造业中产品复杂化、精密化、轻量化、节能化、绿色化的要求,应用领域不断拓宽。压铸分热室压铸和冷室压铸。前者是将在金属池内熔化的液态、半液态金属通过压力的作用填充模具。其优点是循环速度快(每分钟可以完成15个循环),容易实现自动化运作,金属熔化的过程方便,适用于锌、锡以及铅的合金等低熔点合金小型铸件生产。冷室压铸是将在独立坩埚中熔化的金属按要求的数量转移到未被加热的注射室或注射嘴中,通过压力将其注入模具中。适用于各种尺寸的包括铝、镁、铜以及含铝量较高的锌合金的铸件生产。这种工艺的主要缺点是循环时间较长。
随着压铸件形状越来越复杂、尺寸越来越大,压铸模具的设计和制造技术要求越来越高。同时,由于压铸模要承受熔融金属的冲蚀和高频次的冷热冲击,模具的用材和处理成为压铸模具的关键制造技术。压铸模的使用寿命随压铸件的不同而有所差别,一般在10万~30万模次。压铸生产线和压铸件分别如图1-1、图1-2所示。
据中国铸造协会统计,2015年我国生产各种铸件4560万t,其中铝(镁)铸件占13.4%,超过600万t。汽车制造所用铸件占27.4%,达到1250万t。

图1-1 压铸生产线

图1-2 压铸件
2015年我国各类材质铸件产量占比及各行业所用铸件占比如图1-3、图1-4所示。

图1-3 2015年我国各类材质铸件占比

图1-4 2015年各行业铸件占比
(2)冲压工艺 冲压加工是利用金属塑性变形特性,通过冲压设备和模具对金属板料施加压力,使其产生塑性变形或分离,从而获得具有一定形状、尺寸和性能的零件(冲压件)的一种金属加工方法,是金属塑性加工的主要方法之一。
冲压加工是借助于冲压设备的动力,使板料在模具里直接受到变形力并进行变形,从而获得一定形状、尺寸和性能的产品零件的生产技术。因此,板料、模具和设备是冲压加工的三要素。
冲压加工具有生产效率高(压力机的行程次数从每分钟几十次到数千次,多工位级进冲压可把数十个冲压工步集成在一副模具上),冲压件的尺寸与形状精度高且一致性好,可加工冲压件的尺寸范围大、复杂程度较高,材料利用率高且易于实现自动化生产的优越性,因此,广泛应用在航空航天、军工、汽车、电子电器、信息产业、轨道交通、医疗器具、家用电器及轻工等国民经济各个领域。我国目前有5000万t左右的金属板材通过冲压加工成数千亿件冲压件或零部件。
按工艺分类,冲压可分为分离工序和成形工序两大类。分离工序也称冲裁,其目的是使冲压件沿一定轮廓线从板料上分离,同时保证分离断面的质量要求。成形工序的目的是使板料在不破坏的条件下发生塑性变形,制成所需形状和尺寸的工件。冲裁、弯曲、剪切、拉深、胀形、旋压、矫正是几种主要的冲压工艺。在实际生产中,常常是多种工序综合应用于一个工件。
按冲压加工温度分为热冲压和冷冲压。前者适合变形抗力高、塑性较差的板料加工;后者则在室温下进行,是薄板常用的冲压方法。
汽车覆盖件自动化冲压生产线如图1-5所示。汽车车身部分冲压件如图1-6所示。

图1-5 汽车覆盖件自动冲压生产线

图1-6 汽车车身部分冲压件
(3)锻造工艺 锻造(模锻)是利用锻压机械和模具对金属坯料施加压力,使其产生塑性变形并充满模膛,以获得具有一定力学性能、一定形状和尺寸锻件的加工方法。模锻工艺一般由制坯、预锻、终锻、冲孔、切边工序组成。根据模锻时坯料的温度,又分为热锻、温锻和冷锻。
热锻时,坯料加热到950~1200℃,大大降低了材料的变形抗力,使得许多高强度合金钢零件(如内燃机连杆、曲轴,汽车转向节,大功率汽轮机叶片,钛合金涡轮盘等复杂锻件)的成形成为可能。冷、温锻工艺由于在室温或中等温度下成形,锻件的精度和表面质量大大提高,可以实现复杂零件(如某些汽车齿轮)工作部位的近净成形。因此,模锻工艺广泛用于汽车、航空航天、电站设备和军工产品的制造中。
由于模锻工艺在高温、高压下进行,对模具的强韧度(特别是高温强韧性)要求很高,因此模具寿命一般在10万件以内。
据中国锻压协会统计,2015年我国共生产锻件1005万t,其中模锻件占60%,达到600万t。模锻件中,用于汽车制造的锻件为420万t,占模锻件总量的70%。
63MN扭模锻压力机为主机的锻造生产线如图1-7所示。汽车转向节锻件如图1-8所示。

图1-7 63MN热模锻压力机为主机的锻造生产线

图1-8 汽车转向节锻件
(4)挤压工艺 金属挤压加工是利用金属挤压机使金属锭坯产生塑性变形,并通过模具加工成管、棒、复杂断面型材或零件的加工方法。根据挤压时金属坯料的温度,又分为热挤压和冷挤压。
挤压加工工艺应用之一是金属零件的成形,大部分情况下是在室温下通过通用或专用压力机和模具,使金属坯料产生塑性变形而成形为零件。零件的挤压有冷挤压和热挤压两种工艺,前者主要用于挤压小型精密轴销类金属零件,后者可用于中大型管、筒、轴类零件的成形加工。
挤压加工工艺应用之二是金属型材的加工,其中以铝合金型材为主。2015年我国铝型材产量约为2500万t。
铝合金型材挤压生产线如图1-9所示。挤压铝合金型材(断面)如图1-10所示。

图1-9 铝合金型材挤压生产线

图1-10 挤压铝合金型材(断面)
2.塑料制品的模具成形(型)工艺
塑料制品的模具成形(型)工艺主要有:
(1)注射成型 又称注射模塑成型,是在一定温度下,通过注射机螺杆搅拌完全熔融的塑料材料,并将其高压射入模具模膛,经模具内冷却固化得到成型制品的加工方法。该方法的特点是生产效率高,操作可实现自动化,可生产各种花色品种、各种形状和各种尺寸的制件,而且制品尺寸精确、品质好。特别适用于大量生产与形状复杂产品等成型加工。注射机及注射用模具如图1-11、图1-12所示。

图1-11 注射机

图1-12 安装在注射机上的模具
(2)吹塑成型 也称吹塑模塑,是借助于气体压力使闭合在模具中的热熔型坯吹胀形成中空制品的方法,也是最常用的塑料加工方法。热塑性树脂经挤出或注射成型得到的管状塑料型坯,加热到软化状态(或利用制坯温度),置于对开模中,模具闭合后即向型坯内通入压缩空气,使塑料型坯吹胀而紧贴在模具内壁上,经冷却脱模,即得到各种中空制品。吹塑用的模具只有阴模(凹模),与注射成型相比,设备造价较低,适应性较强,可成型性能好(如低应力)、可成型具有复杂起伏曲线(形状)的制品。吹塑制品主要有瓶、桶、罐、箱以及所有包装食品、饮料、化妆品、药品和日用品的容器以及各种工业品包装容器或零部件,如用于化工产品、润滑剂和散装材料的大型吹塑容器、汽车燃油箱、轿车减振器、座椅靠背、头枕覆盖层等。机械、家具、玩具等制造中也大量使用吹塑零件。三维吹瓶机如图1-13所示。吹塑成型的汽车燃油箱总成如图1-14所示。

图1-13 三维吹瓶机

图1-14 吹塑成型的汽车燃油箱总成
(3)吸塑成型 又叫真空成型,利用吸塑成型机将加热软化的塑料硬片吸附于模具表面,在模具内冷却后形成凹凸形状的塑料制品。该方法所用的设备较简单,模具承压较小,成型速度快。
(4)挤塑成型 又称挤出成型,是热塑性塑料成型的重要方法之一。挤塑成型是将塑料原料加热,使之呈黏流状态,在加压的作用下,通过挤塑模具而成为截面与口模形状相仿的连续体,然后进行冷却定型为玻璃态,经切割而得到具有一定几何形状和尺寸的塑料制品。可制取管、筒、棒、中空板、膜、片、异型材、电线等塑料制品。
2015年,我国塑料制品的产量约为7500万t,其中注射制品约为4300万t。
3.其他制品的模具成形(型)工艺
其他制品的模具成形(型)工艺主要有以下4种:
(1)橡胶制品成形 首先,通过各种加工手段,使得弹性的橡胶变成具有塑性的塑炼胶,再加入各种配合剂制成半成品,然后放入模具进行硫化,从而使具有塑性的半成品又变成弹性高、力学性能好的橡胶制品。
(2)玻璃制品成型 通常的工艺是将玻璃融化,通过模具成型。工艺之一是将玻璃熔液放入模具中,通过施加一定的外力进行成型;其二是在模具中叠放玻璃碎料,并一起放进熔炉中进行熔化,待玻璃与模具完全吻合后实现成型;其三是将切割成一定形状的玻璃块或平板玻璃覆盖在模具上,送入窑炉中加热成型。
某些玻璃制品也可通过简单工具人工成型。
(3)陶瓷制品成型 陶瓷制品制造流程:制坯→干燥→施釉→烧成。制坯方法主要有:可塑成型(坯料中加水和添加剂形成可塑性后,通过模具挤压、热压注或通过辊压、旋压、车削制成坯)、注浆成型(将浆料注入石膏或树脂等模具中进行制坯)和压制成型(将含水和添加剂的粉料加压进行成型制坯,如等静压法)。
(4)粉末冶金制品 粉末冶金是制取金属粉末或用金属粉末(或金属粉末与非金属粉末的混合物)作为原料,经过成形和烧结,制取金属材料、复合材料以及各种类型制品的工业技术。粉末冶金技术具备显著节能、省材、性能优异、产品精度高且稳定性好等一系列优点,非常适合于大批量生产。目前,粉末冶金技术已被广泛应用于交通、机械、电子、航空航天、兵器、生物、新能源、信息和核工业等领域,成为新材料科学中最具发展活力的分支之一。另外,部分用传统铸造方法和机械加工方法无法制备的材料和复杂零件也可用粉末冶金技术制造,因而备受工业界的重视。
1.1.2 模具分类
按照材料或零部件(制品)的成形工艺不同,模具可以分为冲压模具、铸造模具(含压铸模具)、锻造模具、挤压模具、注射模具、拉丝模具、玻璃成型模具、橡胶成形模具和粉末冶金模具等。随着成形工艺的发展和融合以及新材料的应用,新的成形工艺不断出现,如汽车(超)高强钢板热冲压工艺、压铸挤压工艺等,因此,根据成形工艺进行的模具分类也将不断补充和完善。
最近制定的“模具 术语”国家标准中对模具的定义:将材料成形(成型)为具有特定形状与尺寸的制品、制件的工艺装备。包括:冲模、塑料模、压铸模、锻模、粉末冶金模、拉制模、挤压模、辊压模、玻璃模、橡胶模、陶瓷模、铸造模等类型。模具分类与模具零部件及机构见表1-2。
表1-2 模具分类与模具零部件及机构

(续)

(续)

(续)

(续)

根据模具用户的行业特点,又可分为汽车模具、家电模具、电子模具等,也称产业模具。其中汽车制造所用的模具类型最多,汽车模具几乎涵盖了目前技术分类中所有的模具类型。
1.1.3 模具结构
模具一般由上模、下模(上模、下模也称凸模、凹模或动模、定模)、模具标准件〔模架、顶杆、推管、热流道、(氮气)弹簧等〕和其他模具零部件组成。上模、下模是实现制件(制品)形状和精度的主要工作部分,其他模具零部件(包括模具标准件)的作用是保证上模、下模的定位精度、运动精度,并配合上、下模顺利完成送料、合模、成形、开模、出件等模具成形的全过程。通常情况下,驱动模具各运动部件动作的动力由成形机床提供,而现代大型复杂模具往往需要配备独立的动力系统,才能完成诸如多向抽芯、电动脱模、多料注射模具旋转等复杂动作,加之许多大型模具还同时配备有加热冷却控制系统,因此,这类模具本身就是一台(套)完整的制造装备。
(1)金属板材冲模结构 落料模结构如图1-15所示。弯曲模结构如图1-16所示。拉深模结构如图1-17所示。级进模结构如图1-18所示。

图1-15 落料模结构
1—模柄 2—卸料螺钉 3—上模座 4—内六角螺钉 5—弹簧 6—导套7—导柱 8—挡料销 9—下模座 10—托板 11—推杆 12—推件块13—凹模 14—卸料板 15—凸模 16—凸模固定板 17—垫板 18、19—圆柱销

图1-16 弯曲模结构
1—模柄 2—打杆 3—上模座 4—内六角螺钉 5—导套 6—导柱 7—挡料销 8—下模座9—推杆 10、12—推件块 11—凹模 13—凸模 14—凸模固定板 15、16—圆柱销

图1-17 拉深模结构
1—模柄 2—卸料螺钉 3—上模座 4—内六角螺钉 5—导套6—弹簧 7—导柱 8—挡料销 9—下模座 10—推杆 11—推件块12—凹模 13—卸料板 14—凸模 15—凸模固定板 16、17—圆柱销

图1-18 级进模结构
1—上模座 2—卸料螺钉 3—冲导正孔凸模 4—冲预孔凸模 5—切口凸模 6—垫板7—导正销 8—压印凸模 9—冲孔凸模 10—凸模固定板 11—橡胶弹性体 12—垫板13—落料凸模 14—弹性卸料板 15—导套 16—导柱 17—内六角螺钉 18—落料凹模19—凹模固定板 20—冲孔凹模 21—螺塞 22—弹簧 23—抬料销 24—压印凹模25—凹模镶件 26—垫板 27—下模座
(2)塑料注射模结构 塑料注射模结构如图1-19所示。

图1-19 塑料注射模结构
1—定模座板 2—型腔板 3—带肩导柱 4—带头导套 5—型芯固定板 6—支承板 7—垫块8—复位杆 9—动模座板 10—推杆固定板 11—推板 12—限位钉 13、14—型芯 15—推管16—推板导套 17—推板导柱 18—限位块 19—侧型芯滑块 20—楔紧块 21—斜导柱22—浇口套 23—定位圈
(3)塑料挤出模结构 塑料挤出模结构如图1-20所示。

图1-20 塑料挤出模结构
a)模头 b)定型模
(4)塑料吹塑模结构 塑料吹塑模结构如图1-21所示。

图1-21 塑料吹塑模结构
1—颈部镶件 2—冷却通道 3—型腔 4—分型面 5—底部镶件 6—导柱
(5)塑料发泡模结构 塑料发泡模结构如图1-22所示。

图1-22 塑料发泡模结构
1—上蒸汽室盖板 2—上蒸汽室 3—蒸汽密封垫 4—上模型腔板 5—型芯 6—蒸汽孔7—侧型腔板 8—下模型腔板 9—下蒸汽室 10—下蒸汽室盖板 11—进料管 12—料塞
(6)压铸模结构 压铸模结构如图1-23所示。

图1-23 压铸模结构
a)纵向剖视图 b)横向剖视图
1—动模座板 2—推板限位块 3—垫块 4—动模套板 5—滑块限位块 6—滑块导板7—滑块 8—楔紧块 9—定模套板 10—斜导柱 11—活动型芯 12—定模块 13—镶件14—型腔 15—浇口 16—横流道 17—直浇道 18—浇口套 19—冷却环 20—导流块21—动模块 22—推杆固定板 23—推板 24—推杆 25—点冷却器 26—限位钉 27—推板导套28—推板导柱 29—型芯 30—动模排气板 31—定模排气板 32—挤压销 33—挤压销套34—隔板 35—导柱 36—锁扣 37—导套 38—复位杆 39—支承柱 40—推板连接杆
(7)粉末冶金模结构 粉末冶金模结构如图1-24所示。

图1-24 粉末冶金结构

图1-24 粉末冶金结构(续)
a)压制模 b)浮动压制模 c)干袋冷等静压模 d)粉末挤压模
(8)拉制模结构 整体式拉制模如图1-25所示。组合式拉制模结构如图1-26所示。

图1-25 整体式拉制模
1—润滑角 2—压缩角 3—入口区 4—润滑区 5—压缩区 6—定径区 7—减压区8—出口区 9—减压角 10—出口区长度 11—减压区长度 12—定径区长度13—压缩区长度 14—润滑区长度 15—入口区长度

图1-26 组合式拉制模结构
a)硬质合金组合式拉制模 b)金刚石组合式拉制模
(9)挤压模结构 通用反挤压模结构如图1-27所示。型材挤压分流模结构如图1-28所示。

图1-27 通用反挤压模结构
1—下模座 2—导柱 3—凹模固定圈 4—导套 5—上模座 6--凸模座7—凸模固定圈 8—垫块 9—凸模定位圈 10—凸模 11—凹模12—预应力圈 13—卸料板 14—垫板 15—凹模定位圈 16—推杆

图1-28 型材挤压分流模结构
1—芯模 2—分流模凹模 3—分流桥 4—分流孔 5—焊合室
1.1.4 典型模具
(1)冲模 如图1-29至图1-34所示。

图1-29 汽车侧围自动线模具

图1-30 电机铁心多工位级进模

图1-31 电子插接器级进冲模

图1-32 空调器翅片冲模

图1-33 结构件多工位级进模

图1-34 安装在压力机上的精冲模具和典型的精冲件
(2)塑料模具 如图1-35至图1-44所示。

图1-35 汽车保险杠注射模具

图1-36 PET瓶坯注射模具

图1-37 车灯注射模

图1-38 双色注射模

图1-39 双色注射模浇口

图1-40 塑料管件注射模具

图1-41 液体瓶吹塑模

图1-42 大型容器吹塑模

图1-43 集成电路塑封模具

图1-44 塑料片材挤出模具
(3)压铸模 如图1-45所示。

图1-45 汽车大型壳体类压铸件三维设计造型与实物模具
(4)锻造模具 如图1-46、图1-47所示。

图1-46 发动机曲轴锻模

图1-47 发动机连杆锻模
(5)橡胶轮胎模 如图1-48和图1-49所示。

图1-48 汽车子午线轮胎活络模

图1-49 巨型工程胎模具
(6)铝型材挤压模 如图1-50所示。

图1-50 铝型材挤压模