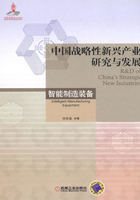
第2章 我国智能制造装备产业发展分析
2.1 产业发展概况
制造业是国家创新能力的重要战场,是支撑国家经济和社会发展的重要基础产业。我国制造业经过十几年的发展,总体规模和水平得到了大幅提升,综合实力不断增强。在技术创新方面,我国制造产业历经了模仿创新、集成创新、引进消化吸收再创新等多个阶段,总体的创新能力得到了明显增强,正在由跟随式创新向引领式创新转型,为进一步提升我国创新能力,政府及相关部门不断加大对科技创新的支持力度。截至2014年,我国全社会科研经费投入达13312亿元,占GDP比重的2.09%,是2008年科研经费投入总额4616亿元的2.88倍,经费投入总额位居世界第三,投入强度在新兴发展国家中居于领先地位。在制造产业方面,随着以信息技术为代表的高新技术的发展和应用,制造业不断引入新的技术,逐渐呈现向高端制造发展的特点,也促进了为高端制造提供装备支撑的智能制造装备产业的快速发展。
依托国家重大科技专项和国家重点工程专项的实施,我国制造业装备的智能化水平不断提升,以智能测控装置、高档数控机床与基础制造装备、自动化成套生产线为代表的智能制造关键技术与装备产业发展迅速,一批国家急需、长期依赖进口、受制于国外的智能制造装备实现突破。如精密、高速加工中心;重型数控镗铣床;总线、高速高精运动控制;插补、多轴联动等关键技术。一大批重点高校、机床集团公司和用户单位在国家相关科技项目的支持下联合攻关,在智能制造关键技术与装备领域取得重要突破。华中科技大学突破国外技术封锁,自主研发了用于加工航空发动机压气机盘的智能双面车床,其主要技术指标达到或超过国外同类产品。武汉重型机床集团公司和华中科技大学联合研制了七轴五联动车铣复合机床,打破国外技术垄断。华中科技大学联合华工激光工程有限责任公司、神龙汽车有限公司、湖北中航精机科技有限公司、凌云工业股份有限公司等多家企业,潜心技术攻关和市场耕耘,研发了汽车车身激光焊接、不等厚板拼焊、激光非穿透紧密切割等一系列生产线,突破国外公司的技术垄断,在汽车制造激光加工高端装备生产中实现了国产自主化。由沈阳机床(集团)有限责任公司、天津大学、成都飞机工业(集团)有限责任公司承担,国产首台用于复杂钛合金航空结构件加工的五轴联动加工中心研制成功,其中,“S”试件切削工艺技术研究获重大突破。由齐重数控装备股份有限公司承担,我国自主知识产权的、全功能、高精度数控重型曲轴铣车复合加工机床研制成功,一次装卡即可完成大型船用低速柴油机组合曲轴的主轴颈、法兰和曲拐颈的半精加工和精加工。由齐齐哈尔二机床(集团)有限责任公司、南京航空航天大学、清华大学、航天材料及工艺研究所联合研制的大型复合材料构件铺带机,主要适用于大型筒形复合材料构件的成形,能够突破手工成形、效率和质量保障难度大的瓶颈,实现筒形复合材料构件自动化高速成形,批量化生产。由中国第一重型机械集团公司牵头承担的“大型高质量铸件的材料冶炼与成形控制技术”课题,主要围绕能源、冶金、数控机床等重大装备大型铸件和大型特大型钢锭的生产工艺,研究大型铸件的成形控制、材料冶炼、成分优化技术和用于大型锻件的钢锭冶炼等技术。大型关键件模锻工艺技术课题重点围绕大型航空模锻件热模锻近净成形技术,结合正在建设的800MN大型模锻压机,开发出航空复杂精密锻件的近净成形新技术,解决了大型模锻工艺基础共性技术和关键技术问题。截至2012年,我国智能制造装备产业主营业务收入约11052.9亿元,产业产值约为5100亿元,已提前完成《“十二五”智能制造装备产业发展规划》中所要求的“到2015年我国智能制造装备产业销售收入预计将超过1万亿元,年均增长率超过25%,工业增加值率达到35%”的目标。
我国智能制造装备产业已形成了一批具有国际竞争力的龙头企业。如在机床工业领域的沈阳机床、大连机床两大集团,其年销售收入均超过百亿元,位居世界机床产业前10强。在智能控制系统领域的上海新华控制技术集团、浙大中控、北京和利时和山东鲁能控制等,均是具有自主知识产权的DCS生产厂商。在仪器仪表领域:重庆川仪、京仪集团、天瑞仪器、聚光科技、威尔泰等龙头企业具有很高的影响力。在工业机器人领域:新松机器人、哈尔滨博实自动化设备、海尔哈工大机器人、安川首钢机器人、上海ABB工程、上海发那科机器人、库卡机器人(上海)等在机器人产业舞台占有重要位置。在工程机械领域:三一重工、中联重科、徐工集团、柳工集团、中国龙工等10家企业位居全球工程机械前50强排名榜单,此外,还有瓦轴集团、沈鼓集团等一批各具特色的智能制造装备企业。
目前,我国智能制造装备产业虽然已经具备一定的规模和影响力,但是从质量与产业化水平来看,中国智能制造还处于初级发展阶段。相比在20世纪70年代制造技术已经成熟的发达国家,中国在智能制造的关键技术和基础工艺方面还有待提升,智能制造装备产业能力、应用范围、服务质量等与发达国家相比,仍存在较大差距。比如在关键零部件、智能仪表和控制系统等基础零部件上,研发能力及配套能力薄弱,很大程度上仍然依赖于国外进口;没有形成完整的自主知识产权技术体系,多数出口产品是贴牌生产,拥有自主品牌的不足20%;80%的集成电路芯片制造装备、40%的大型石化装备、70%的汽车制造关键设备及先进集约化农业装备仍依靠进口。德勤与中国机械工业联合会2013年调研200家制造企业所发布的首份中国智造现状及前景报告显示,我国企业的智能化水平参差不齐,仅有10%左右的大企业智能制造水平较高,尚有90%的企业智能化程度未成熟;仅16%的企业进入智能制造应用阶段,大部分仍处于研发阶段;从智能制造的经济效益来看,52%的企业智能制造收入贡献率低于10%,60%的企业智能制造利润贡献低于10%,而智能化升级成本过高是导致90%的中小企业智能制造实现程度较低的根本原因,其中缺乏融资渠道影响最大。德勤的调研显示,年收入小于5亿元的企业中,50%的企业在智能化升级过程中采用自有资金,25%为政府补贴,银行贷款和资本市场融资各占11%。而企业收入规模大于50亿元的企业,其智能化升级资金来源中自有资金占67%,银行贷款占比25%。整体而言,中小微型企业的银行贷款比例低于大中型企业,占企业数量绝大多数的中小企业只能依靠自有资金进行智能化改造。
另一方面,智能制造水平较低也意味着迫切需要夯实基础,加快推动智能制造创新发展。据国家发改委宏观研究院报道,全国已有多个地方相继出台相关的政策和产业规划、申报智能制造试点示范和专项项目,包括北京、上海、广东、浙江、江苏、湖北、天津、安徽、山东、河南、四川、黑龙江等省市。此外,机械科学研究总院联合航天科技、中科院沈阳自动化研究所等国内知名产学研单位共计23家机构联合发起成立“中国智能制造产业技术创新战略联盟”。在2015年5月19日印发的《中国制造2025》中也将智能制造纳入了五大重点工程,首批30家企业为示范试点。