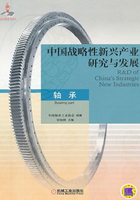
3.3 世界轴承技术水平
轴承的整体技术水平,在近30年来取得了令人瞩目的进步。高精度、高转速、高可靠性、长寿命、免维护保养以及标准化、单元化、通用化已成为轴承的基本技术标志。在轴承基础技术进步、通用产品的结构改进、专用轴承单元化和陶瓷轴承的开发等方面取得的成效最为显著。
3.3.1 基础理论水平
轴承基础理论主要是指与轴承寿命、额定载荷和极限转速等有关的理论。
百余年来轴承寿命理论的研究经历了四个阶段:第一阶段是1945年以前的Stribeck的载荷分布理论,第二阶段是1945~1960年间伦得伯格(Lundberg)和帕尔格恩(Palmgren)轴承疲劳失效理论,第三阶段是1960~1980年间的寿命修正理论,第四阶段是1980~1998年间以Ioanndes和哈里斯(Harris)为代表的新寿命理论。
1962年,国际标准化组织(ISO)将经典的L-P公式作为轴承额定动载荷与寿命计算方法标准列入ISO/R281中。近年来,由于材料技术、加工技术、润滑技术的进步和使用条件的精确化,使轴承寿命有了较大提高,ISO适时地给出了含有可靠性、材料、运转条件和性能等修正系数的寿命计算公式。20世纪80年代以来,哈里斯等学者在大量试验的基础上提出接触疲劳极限的新理论,将寿命理论又向前推进了一步,使轴承寿命计算方法不断完善。
允许轴承发生相当于万分之一滚动体直径的永久变形,一直是ISO额定静载荷标准的基础。最新的额定静载荷理论的贡献是给出了对应于这个永久变形的各类轴承的最大滚动体接触应力。
对于轴承极限转速的研究也取得了新进展。当前世界上较有影响的轴承公司,如瑞典的SKF,德国的INA、FAG,以及日本的NTN等公司,对极限转速的定义、限定范围与使用条件都作出了较科学的规定,使极限转速的研究更加深入。
3.3.2 设计技术水平
传统的轴承设计就其应用的理论和方法而言,多采用静力学和拟静力学设计方法。近50年来,轴承设计理论有了很大发展,先后提出和应用了有限差分法、有限元法、动力学及拟动力学、弹性流体动力润滑理论,有力地促进了轴承产品设计和应用技术的研究与发展。与此相适应,电子计算机辅助设计(CAD)已在各国轴承设计计算中得到广泛应用,从而把轴承设计计算推向了一个新阶段。
量大面广的通用轴承产品的结构一直围绕着提高轴承载荷,延长使用寿命,增加强度与刚性,减少摩擦磨损,降低噪声,减小体积,减轻质量,采用新材料及免除维护保养作为不懈努力的目标。经过近30年的努力,国外通用轴承已全部实现了更新换代,形成了新一代的加强型产品。通用轴承内部结构的改进,主要通过减小套圈壁厚,加大滚动体直径与长度,采用对数母线凸度滚子,改变保持架结构与参数,改变引导方式,增加轴承内密封及改善挡边接触来实现。
3.3.3 轴承产品技术水平
当今国外轴承产品的发展具有五个显著特征:一是坚持产品的“三化”方向,以最少的品种满足不同产业的多样化需求,并有利于产品规模化生产;二是产品向轻量化、功能组件化、单元化及智能化发展,以满足主机产品更新换代的要求;三是产品向高速度、高精度、高可靠性、低摩擦、低振动及低噪声方向发展;四是采用和发展了计算机辅助设计(CAD)、计算机辅助制造(CAM)以及计算机集成制造系统/信息管理系统(CIMS/IMS)技术;五是在轴承产品上采用现代高新技术,如新钢种、新型工程陶瓷材料、表面改性技术及新的设计结构等,以发展轴承可靠性技术。
上述五个特征具体表现在以下几个方面:
(1)技术标准 国际标准化组织滚动轴承第四委员会(ISO/TC4)现颁布正式轴承标准65项、技术报告8项,世界各国都等同、等效采用国际标准,确保轴承“三化”水平。
(2)轴承精度 国外在20世纪80年代就提出了“集中装配设计”的概念,即通过轴承在设计和工艺阶段的相关公差设计,使之控制在一定的公差范围内,经过最少组别的选配,就可实现批量化集中装配,装配后的轴承游隙、装配高等均完全符合标准要求。经检测发现国外名牌产品的精度一致性较好,基本集中在公差带的某一范围内,且离散度较小。如国外精密机床主轴轴承的轴向、径向跳动在0.5μm以下,薄板轧机工作辊轴承可保证工作辊径向摆动量在板厚的3%以下,日本NMB公司研制成功的硬磁盘驱动器高精度小型整体球轴承的重复精度在0.1μm以下。
(3)轴承性能 主要表现在用于航空航天工业配套和高技术所需的专用轴承的高速度、高灵敏度、高可靠性及耐高温、耐低温、耐腐蚀、耐辐射和耐真空度的能力方面,以及通用轴承的转速、温升、振动、噪声和密封等性能方面。
专用轴承中的飞机发动机主轴轴承的速度参数dn值已达到(2.25~2.5)× 106mm·r/min,耐高温能力达250~300℃,寿命达10000h。国外正在研制dn值为3×106mm·r/min的轴承。陀螺仪轴承精度达ABEC9级(P2级),摩擦力矩仅为0.001~0.002mN·m;火箭发动机涡轮泵轴承的耐低温能力达-253℃(液氢)~-183℃(液氧),转速为20000~40000r/min,寿命为7h;原子能反应堆的轴承温度高达650℃;迄今美国已研制出能耐133.3×(10-11~10-13)Pa高真空度的轴承。
通用轴承中机床主轴轴承为适应CNC机床的需求发展很快。如现代数控车床主轴转速可达3500~10000r/min,比普通车床提高了1/3~3倍;对于磨床主轴轴承,SKF公司推出大接触角(60°)的角接触球轴承,国外主要轴承公司已系列化生产,此类轴承与双列向心圆柱滚子轴承组合使用,可显著提高速度性能;法国GAMET公司推出的空心滚子圆锥轴承改善了轴承温升,是现今机床主轴轴承的精品。
工业机器人精密薄壁轴承国外已有在常温环境下,以及高于150℃高温环境下和在腐蚀、辐射、污染工况下使用的各种类型,并正向精密化、小型化和智能化方向发展。
近年来,随着机电产品的发展,一些精密机械和高档家电对轴承的音质控制提出了相当严格的要求。为减轻轴承振动,改善轴承品质,提高轴承的无异音合格率,国外在产品设计、加工工艺、工装设备、洁净度控制、钢球加工及保持架改进等诸方面都取得了有益的经验。如日本NSK的6202“静音”轴承的噪声值仅约为26dB。
除加工工艺外,润滑脂对轴承的振动和噪声也有较大影响。国外一些著名轴承公司均采用轴承专用脂来降低轴承的振动和噪声。如:SKF公司按照不同的温度、转速、载荷等使用条件,以及轴承尺寸大小,来选用不同的轴承专用脂;NSK公司相继开发了AV2、NS7和NSC等低噪声轴承专用脂,较好地控制了噪声,延长了轴承的噪声寿命。目前国外常见的轴承异音在线检测主要有两种方法:一是测量轴承振动的峰值,用峰值因子来判别轴承是否有异音;另一种方法是在测振仪上接示波器,通过示波器上的波形幅值及波的形状来控制。这两种方法都取得了较好的效果。
密封轴承的密封特性是衡量轴承性能的一个重要指标。全世界密封轴承的产量约占轴承总产量的70%,各类通用轴承都有密封轴承系列。20世纪90年代,日本KOYO公司的轻接触密封、SKF公司推出的双唇非接触式橡胶密封、FAG公司的高速主轴轴承密封、INA公司满滚子轴承聚酯密封、Timken公司的通用圆锥滚子轴承密封及FAG公司的轧机轴承密封等,都代表了当代密封轴承技术的最新成果。
(4)轴承寿命和可靠性 国外深沟球轴承的台架试验寿命一般为计算寿命的8倍甚至十几倍以上,可靠度高达98%以上,甚至达99.9%;圆锥滚子轴承的台架试验寿命一般为计算寿命的4~6倍,甚至8倍以上,可靠度达98%以上。一些为重点主机配套的轴承寿命也较长,如铁路货车轴承寿命达150万~200万km,可实现10年无更换;铁路客车轴承,如日本、意大利的高速列车,速度可达350km/h,行驶寿命为150万~300万km,可靠度在800km内可达90%;载重汽车轮毂轴承行驶寿命达25万km;轧机轧辊轴承轧制寿命可达60万~80万t钢等。
(5)轴承单元化 轴承单元化技术方兴未艾。轴承行业为了方便用户的装拆、免除维护和减轻结构件质量,已越来越注重开发轴承单元,比较典型的轴承单元有汽车轮毂轴承单元、自调心汽车离合器轴承单元、汽车水泵轴连轴承单元、带座外球面轴承单元、轧机轴承单元、铁路轴承单元、计算机磁盘驱动器主轴轴承单元、气流纺杯轴承单元及钻铣床高速主轴轴承单元等。
(6)轴承材料 注重开发耐磨损低摩擦材料,如含高碳、铬、钼及镍等成分的新型合金钢材,提高了在高频率交变应力下耐疲劳性能。随着对材料性能要求的不断提高,如纯净度高、夹杂物含量低、均匀度及稳定性好等,发展了真空脱气、炉外精炼及电渣重熔等工艺冶炼技术。随着材料科学的发展,满足特殊用途的非金属材料也相继出现,如陶瓷材料、尼龙材料和树脂材料等。
美国的Timken公司轴承钢的年销售额占总销售额的比例高达32%。此外,日本和德国在耐热钢的研究上也取得了重大进展。
非金属材料用于滚动轴承制造中,主要是陶瓷和塑料。FAG、SKF、KOYO等公司都推出了陶瓷轴承新品种,世界陶瓷轴承年度贸易额超过4亿美元。塑料被广泛用于轴承的保持架,如德国SKF子公司有70%的圆柱滚子轴承和85%的新一代圆锥滚子轴承采用了塑料保持架,FAG公司塑料保持架轴承占其轴承总产量的30%。
3.3.4 工艺及工艺装备水平
轴承是批量生产的精密产品,只有用先进的制造技术和相应的设备,才能保证产品的精度、性能、寿命、可靠性和成本等技术经济指标的实现。在工业发达的国家,对批量较大的标准轴承,通常都采用高效、高精度的自动化设备加工制造,对于批量更大的则组织自动化生产线、自动化车间甚至自动化工厂进行生产。
在热处理技术方面,研究不同钢号不同的金相组织形态,如控制GCr15钢淬火马氏体常为隐晶状和弥散碳化物含量,根据对尺寸稳定性要求控制残留奥氏体含量,根据冲击性能要求进行差异定量控制。设计合理硬度及匹配,套圈、滚动体具有不完全相同的高硬度。为获得长寿命,研究晶粒细化对无氧化热处理工艺过程的要求。采用氮基保护气氛,气氛的纯度高和吸热式、甲醇裂解滴注,过滤式、直生式等,淬火炉腔内碳势氮势平衡可准确控制。为了提高材料的冲击韧性,发展了贝氏体淬火工艺。此外,表面工程技术也得到广泛应用,如激光表面冲击强化、离子注入等。
在机械加工方面,向着高精度、大批量、标准化生产、优质、高效及低耗方向发展,大量采用了复合工序和自动化生产线。在套圈锻造中为提高材料利用率采用精化、半精化工艺和装备,如高速镦锻机、多工位压力机和冷辗机等,以减少切削量并降低后加工工序成本。在保持架加工中采用焊接架、无车边工艺和一次性冲孔技术,提高精度与效率。车削加工采用数控多轴车床高效切削。
磨超加工以高速、高效为发展方向,套圈内表面磨削速度已达60~80m/s,外表面磨削速度达80~120m/s。同时,大力开发磨削-超精研自动化生产线,应用CBN砂轮磨削、自适应磨削、在线测量和故障自动诊断等新技术,并配以轴承自动装配生产线,确保生产率,稳定产品质量。纳米级轴承加工与测量技术已取得进展。
质量检测与控制是轴承制造技术的重要内容,是轴承优良品质的重要保证。目前已能够进行原材料冶金质量的检测,如氧含量、夹杂物等;能够进行热处理质量的定量检测与控制,解决了残留奥氏体定量检测,表面物理、化学及力学性能的定量检测问题。自动化生产线加工过程在线检测的闭环控制系统、高精度的纳米圆度测量技术及误差补偿技术等也发展起来。
相应地,各类检测仪器也相继发展起来。如:用作零件特征测量仪器的圆度仪、轮廓度仪、沟形仪、凸度仪、表面粗糙度仪、内外径仪及高度仪等;用作检测轴承成品整体性能或特征仪器的振动仪、游隙仪、旋转精度仪、摩擦力矩仪、刚度仪、接触角仪及凸出量仪等;用作生产设备或装配线在线测量仪器的主动测量仪、机外检测机、自动游隙仪、自动测振仪及灵活性检测机等。随着IT技术的发展,轴承仪器向着网络化、智能化、虚拟化和纳米化的方向发展,高精度的纳米圆度测量仪、工业CT无损检测技术和激光技术也已在轴承行业中应用。
为了检验轴承的质量(性能、功能的保持性、寿命与可靠性),发展了试验理论、试验技术及装备。早在1939年,韦布尔(Weibull)就提出了轴承的疲劳寿命服从某一概率分布,即著名的韦布尔分布疲劳寿命理论。在此基础上又发展了能很好地解释轴承失效机理和预测寿命的L-P模型。随着轴承钢质量的不断提高,SKF公司改进了L-P模型,考虑了润滑、污染、疲劳极限和轴承当量动载荷之间的复杂关系。为了提高试验效率,缩短试验时间和降低成本,发明了快速强化可靠性试验方法、相似性试验方法等,并开发了各类试验机。检测轴承可靠性、相似性等性能的各类试验机分类如图3-1所示。

图3-1 检测轴承可靠性、相似性等性能的各类试验机分类
3.3.5 技术前沿领域
1.轴承设计
(1)多界面系统动态润滑接触理论
(2)精确定量润滑理论
(3)表层弹塑性接触分析理论
(4)弹塑性流体润滑理论
(5)轴承运动副表面润滑介质分布规律及建模
(6)脂润滑机理
2.轴承制造
(1)组件的控形控性制造
(2)强化层的形成与可控机理研究
(3)磨削过程中磨粒与工件微观作用与可控机理研究
(4)轴承滚道低温供液磨削加工技术
(5)轴承滚道电化学机械光整磨削技术
3.轴承服役
(1)复杂环境下的工况建模
(2)轴承服役性能影响机理(工况、装配、配置等)
(3)轴承状态监测与智能轴承
(4)轴承服役性能在线调整