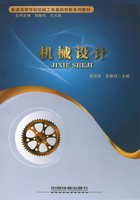
2.2 疲劳强度的基本理论
在变应力作用下,零件的应力即使低于材料的屈服极限,也可能会在经受一定应力循环周期后突然断裂,且断裂时没有明显的宏观塑性变形,这种破坏形式称为疲劳失效。在变应力下工作的零件,疲劳断裂是主要的失效形式之一,据统计,疲劳断裂占零件断裂的80%以上。疲劳失效的机理与静应力作用下的强度失效有本质上的差别,计算方法也明显不同。
2.2.1 变应力的类型
变应力可能由变载荷或静载荷产生,其类型可分为稳定循环变应力和非稳定循环变应力两大类。
1.稳定循环变应力
稳定循环变应力可分为非对称循环变应力、脉动循环变应力和对称循环变应力等3种基本类型,如图2-1所示。

图2-1 稳定循环变应力类型
当变应力的最大应力为σmax,最小应力为σmin时,其平均应力σm和应力幅σa分别为

最小应力与最大应力之比称为变应力的循环特性r,即

变应力特性可用σmax、σmin、σm、σa、r等5个参数中的任意两个来描述。几种典型稳定循环变应力的循环特性和应力特点如表2-1所示。
表2-1 几种典型稳定循环变应力的循环特性和应力特点

2.非稳定循环变应力
非稳定循环变应力可分为规律性非稳定循环变应力和随机性非稳定循环变应力两种,如图2-2所示。

图2-2 非稳定循环变应力
2.2.2 疲劳失效的特点
大量实践结果表明,疲劳失效具有以下特点:
(1)疲劳失效时,零件内部的工作应力值远低于材料的抗拉强度σB,甚至远低于材料的屈服强度σS。
(2)疲劳的失效过程一般要经历裂纹萌生、裂纹扩展和断裂三个阶段,如图2-3所示。
表面无缺陷的金属材料,在变应力作用下零件表面应力较大处的材料会发生剪切滑移,从而产生初始裂纹,形成裂纹源。随着应力循环次数的增加,裂纹沿尖端逐渐扩展,零件的截面面积逐渐减小。当截面面积小到某一临界值时造成零件静应力强度不足,就会突然发生脆性断裂。
零件表面的加工痕迹、划伤、腐蚀小坑以及材料中的夹渣、微孔、晶界等都有可能产生初始裂纹。零件的圆角、凹槽、缺口等造成的应力集中也会促使表面裂纹的产生和发展。
(3)疲劳断裂截面由光滑的疲劳发展区和粗糙的脆性断裂区组成。图2-4为旋转弯曲条件下的疲劳断裂截面示意图。由于变应力的作用。裂纹在扩展过程中,周期性压紧和分开,使裂纹两表面受到不断摩擦和挤压作用,形成了断口表面的光滑区。粗糙的脆性断裂区是由于剩余的截面静应力强度不足造成的,剩余截面的大小与所受载荷有关,载荷大,粗糙表面也大。

图2-3 疲劳失效的三个阶段

图2-4 旋转弯曲的疲劳断裂截面
2.2.3 疲劳曲线
疲劳曲线是用一批标准试件进行疲劳实验得到的。以规定的循环特性r的变应力施加于标准试件,经过N次循环后不发生疲劳破坏时的最大应力称为疲劳极限应力σrN或τrN。表示循环次数N与疲劳极限应力σrN或τrN之间的关系曲线,称为疲劳曲线(σ-N或τ-N曲线)。典型的疲劳曲线如图2-5所示,图2-5(a)是以普通坐标表示的疲劳曲线,图2-5(b)是以双对数坐标表示的疲劳曲线。由图2-5(b)可见,疲劳曲线可分成两个区域:N<N0为有限寿命区;N≥N0为无限寿命区,N0为循环基数。若按循环次数的高低可分为低周循环区和高周循环区,即N<103(104)次时为低周循环区,N≥103(104)次时为高周循环区。
1.有限寿命区
在低周循环区内,疲劳极限较高,接近屈服极限,且疲劳极限几乎与循环次数的变化无关,称为低周循环疲劳。例如飞机起落架、炮筒和压力容器等的疲劳属于低周循环疲劳。但对绝大多数通用零件来说,当其承受变应力作用时的应力循环次数一般都大于104,所以本章不讨论低周循环疲劳问题。
在高周循环区内,当103(104)≤N<N0时,疲劳极限随循环次数的增加而降低,这是有限寿命疲劳强度设计中应用最多的区段。
2.无限寿命区
当N≥N0时,疲劳曲线为水平线,对应N0点的极限应力σr称为持久疲劳极限,对称循环时用σ-1表示,脉动循环时用σ0表示。
所谓“无限”寿命,是指零件承受的变应力水平低于或等于材料的持久疲劳极限σr,工作应力总循环次数可大于循环基数N0,并不是永远不会产生破坏。
大多数钢的疲劳曲线类似图2-5(b),但有色金属和高强度合金钢的疲劳曲线没有明显的水平部分(即没有无限寿命区),如图2-5(c)所示。

图2-5 典型的疲劳曲线
3.疲劳曲线方程
一般情况下,疲劳强度的设计问题,主要根据图2-5(b)中AB段曲线进行。AB段的曲线方程为

式中 m——随材料和应力状态而定的指数,如钢材弯曲疲劳时m=9,钢材线接触疲劳时m=6;
C——试验常数。
若已知循环基数N0和持久疲劳极限σr,则N次循环的疲劳极限为


式中 kN——寿命系数。
应当注意,材料的持久疲劳极限σr是在N=N0时求得的,当N>N0时应取N=N0计算。各种金属材料的N0大致为106~25×107,但通常材料的疲劳极限是在107(也有定为106或5×106)循环次数下试验得来的,所以计算kN时取N0=107。对于硬度低于350HBW的钢,若N>107,取N=N0=107,kN=1;硬度高于350HBW的钢,若N>25×107,取N=25×107。对于有色金属也规定当N>25×107时,取N=25×107。
2.2.4 疲劳极限应力图
即使是相同的循环次数,若循环特性r不同,材料的疲劳极限也不相同。循环特性r对疲劳极限的影响可用以σa-σm为坐标系的疲劳极限应力图来表示。根据实验数据,塑性材料的疲劳极限应力图近似呈抛物线分布,低塑性和脆性材料的疲劳极限应力图呈直线状,如图2-6所示。图2-6中横坐标σm为平均应力,纵坐标σa为应力幅,A(0,σ-1)为对称循环点,B(σ0/2,σ0/2)为脉动循环点,C(σB,0)为静强度极限点。

图2-6 疲劳极限应力图
实际应用中,为便于计算,常对塑性材料疲劳极限应力图进行简化。常用的一种简化疲劳极限应力图如图2-7所示。在横坐标σm上取S(σS,0)点,由S作135°斜线与AB连线的延长线交于E,得折线ABES。在AE线段上任一点D(σrm,σra)的极限应力为
σr=σrm+σra (2-8)
式中 σr——循环特性r时的疲劳极限;
σrm、σra——分别为循环特性r时的极限平均应力和极限应力幅。
因ES为屈服极限曲线,若D在ES线段上,则其极限应力均为
σr=σrm+σra=σS (2-9)
零件的工作应力点(σm,σa)处于折线ABES以内时,其最大应力既不超过疲劳极限,也不超过屈服极限,ABEO区域称为疲劳安全区,ESO区域称为塑性安全区,而在折线以外为疲劳和塑性失效区。

图2-7 塑性材料简化疲劳极限应力图
由图2-7中的A(0,σ-1)和B(σ0/2,σ0/2)两点可求得AE疲劳极限方程为

由图2-7可知ψσ的几何意义为ψσ=tanθ。可以理解为利用ψσ将平均应力(静应力)化为当量的对称循环应力。
σ-1=OA=OG+GA=OG+DGtan(∠ADG)=σra+ψσσrm
同理,可得到切应力的疲劳极限方程为

其中ψσ、ψτ是将平均应力折合为应力幅的等效系数,其大小表示材料对循环不对称性的敏感程度。试验结果表明,ψσ、ψτ的近似取值范围为:对于碳钢,ψσ=0.1~0.2,ψτ=0.05~0.1;对于合金钢,ψσ=0.2~0.3,ψτ=0.1~0.15。
设图2-7中OE连线与横坐标夹角为αE(αE取决于材料的性质),如果在折线ABES上任意一点D对应有α角,则当α≥αE时,极限应力为疲劳极限,容易发生疲劳断裂;当α≤αE时,极限应力为屈服极限,容易发生塑性变形。
低塑性和脆性材料的疲劳极限应力图如图2-6(b)所示,采用上述类似方法可求得其疲劳极限方程为
