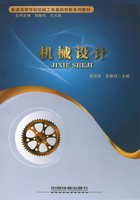
1.5 机械结构设计
结构设计是机械设计的重要环节,它包括总体结构和零部件结构设计。
1.5.1 结构设计的重要性
机械结构设计是机械设计的重要组成部分,它的重要性体现在以下几个方面:
(1)结构是实现机械功能的载体,没有结构就没有机械。用户使用机械是使用它的功能,而机械的功能是通过它的结构实现的。设计师的任务就是设计出具有预期功能的机械结构。
(2)机械制造的对象是机械结构。设计阶段对机械结构的性能和成本有决定性的作用。
(3)机械结构是设计计算的基础和计算结果的体现。进行机械设计要作大量的分析、计算和试验,其目的是把结构设计得更好。设计计算和结构设计常要反复、交叉进行。如设计机械传动装置,首先根据电动机转速和工作机转速,计算传动装置的传动比。然后选择传动装置的类型(如齿轮、蜗杆传动、带传动等),选定以后,计算传动装置的主要参数,画出传动装置草图后,根据齿轮、轴承、轴的尺寸,计算轴承、轴的尺寸,画出传动装置的装配图和零件图。
由此可以看出,结构设计在机械设计中占有重要地位。
1.5.2 机械结构设计的准则
机械结构设计的主要目标是实现产品的规定功能、延长寿命、制造方便、降低成本。结构设计必须遵守明确、简单和安全可靠的基本原则。为了实现这三个原则,设计结构要考虑使用者、制造者、经济性和节能减排等各方面的要求。
为了使初学机械设计者迅速掌握机械结构设计的思路和方法,把这些知识总结成《机械结构设计准则与实例》,以便于学习和掌握。下面对此作一些扼要的介绍,并举出一些实例。
1.考虑满足使用要求的设计准则
确定设计任务必须经过仔细全面的调查研究和分析(参见案例分析1-1),慎重确定机器的主要参数,简化机器的动作要求,避免原理性错误,正确选择原动机,注意使用条件、生产条件和国家的有关规定等准则。
在研究使用要求时,不但要注意要求什么,还要注意不要求什么,仔细分析设计要求,寻找解决问题的途径。例如,一个电子器件制造用的工作台,要求在平面内x、y轴两个方向能够移动和在水平面内转动。按一般经验,如机床,要求做成三层的工作台,满足三个运动要求。但是,仔细研究设计对象的使用要求以后发现,在x、y轴方向的移动只要求各移动±3mm,在平面中的转动只要求±3°,而且受力很小。根据这些要求的特点,设计者设计了一个单层工作台,如图1-2所示。转动螺旋3实现x轴方向移动,同步转动螺旋4、5实现y轴方向移动,以不同速度转动螺旋4、5可以实现工作台转动。
这一设计根据使用要求的特点,创造性地设计了一种新的结构。
2.考虑机械装置承载能力、寿命、精度的设计准则
(1)提高强度和刚度的设计准则。包括减小机械零件受力,减小机械零件的应力,提高零件的强度,减小变形,正确选择材料等准则。如图1-3所示,压力容器的密封盖用螺栓固定,图1-3(a)所示的结构螺栓受力很大;图1-3(b)所示的结构,容器内压力有助于密封盖压紧,螺栓受力很小。
(2)提高精度的设计准则。包括误差合理配置,消除空回,误差均化,误差传递,误差补偿,符合阿贝原理等准则。例如:图1-4所示为精密螺旋加工机床的校正尺补偿机构。对于精密螺纹磨床,由于进给丝杠的误差,会引起被加工螺旋的螺距误差。这一误差可以用补偿的方法消除。做法是利用精密测量装置,测得螺旋机构的误差以后,制造一个图1-4所示的校正尺。在加工时,丝杠转动带动螺母左右移动,导杆的触头沿校正尺的边缘滑动,其上缘的曲线使导杆转动一个很小的角度,螺母也随之转动。由于这一附加的转动,使螺母多走一点,或少走一点,如果校正尺的曲线设计合理,则可以完全补偿丝杠螺距误差引起的加工误差,从而提高了机床的加工精度。

图1-2 单层多自由度工作台
1—工作台;2—底座;3、4、5—手动调节螺旋

图1-3 减小零件受力

图1-4 螺旋机构校正尺示意图
(3)提高耐磨性的设计准则。包括采用耐磨性高的材料组合,避免有害物质进入摩擦表面之间,加大摩擦面尺寸,正确选择润滑剂并保证有足够的润滑剂在摩擦表面,减少摩擦面之间的相对运动和压力,设置容易更换的易损件,减少磨损的不利影响等准则。如图1-5所示,两个图中由于磨损产生的凸轮与触点接触处的误差同为δ1、δ2,图1-5(a)中滑块的运动误差为Δ1=δ1+δ2,而图1-5(b)中滑块的运动误差为Δ2=δ1-δ2,因此该结构比较合理。
(4)提高耐腐蚀性的设计准则。常见的有避免产生腐蚀的结构,设置容易更换的易腐蚀件等。如图1-6(a)所示,未排放干净的液体会引起腐蚀,应该采用图1-6(b)所示的结构。
3.考虑提高工艺性的设计准则
设计机械零部件的结构,必须考虑结构的工艺性。要求设计者在保证使用功能的前提下,力求所设计的零部件在制造过程中生产率高、材料消耗少、生产成本低、节约能源减少排放。下面举出几个铸造、焊接、热处理、机械加工、装配等工艺性的设计准则。

图1-5 避免磨损产生的误差相互叠加

图1-6 容器内液体必须能够排放干净
(1)对于铸件常常遇到的工艺性设计准则:
①铸造方法与零件性能要求、形状、尺寸和生产批量相适应准则。铸造方法常用的有砂型铸造、金属型铸造、压力铸造、熔模铸造、壳型铸造、离心铸造等,按零件的要求和特点选择适用的铸造方法。
②按规定选择铸件的壁厚、圆角、凸台等尺寸。
③便于制造木模准则。对于砂型铸造,应该使铸件形状对称,表面凹凸尽量减少,避免用活块,内外部形状尽量用平面等,如图1-7所示。
④浇铸和冷却过程中能保证铸件质量准则。铸造零件应该避免水平的大平面[见图1-8(a)],因为在浇铸时由于金属漫流会产生浇铸不足、冷隔等缺陷。在平面上面增加一些肋[见图1-8(b)],使金属流动的通道增加,而且加大了刚度可以减小变形。如果铸造时把大平面放在下面,而且处于倾斜位置浇铸[见图1-8(c)],也可以得到较好效果。
(2)对于焊接零件,应该注意焊接件不可简单模仿铸件,应尽量简化焊接件结构,减少焊接件应力集中,减少焊缝受力,避免焊缝集中,避免焊缝汇集等,如图1-9、图1-10、图1-11所示。

图1-7 肋的合理形状

图1-8 避免铸造大的水平面

图1-9 尽量减少组成焊接件的零件数和焊缝数零件数由9件减少到5件

图1-10 注意提高焊接悬臂梁根部的强度

图1-11 焊缝应远离零件有螺纹部分
(3)对于热处理件,应该注意合理选择热处理方法,考虑材料的淬透深度,避免热处理引起变形和裂纹等,如图1-12所示。
(4)对于机械加工件,应该考虑以下设计准则:减少机械加工工作量,减少手工加工或补充加工,简化被加工面的形状,便于夹持和测量,避免刀具处于不利的工作条件等结构设计准则,如图1-13~图1-17所示。
(5)图1-17(a)中零件1、2靠零件3的凸起圆柱形对中,但两个对中面不能在一次切削中完成,对中较差。图1-17(b)中,零件3的孔在一次加工中作出,零件1、2的圆柱形配合面对中较好。

图1-12 为了避免变形,孔不可距离零件边缘太近

图1-13 不同加工精度表面要分开

图1-14 减少退刀次数

图1-15 凹槽圆角半径R不可太小以提高切削加工效率

图1-16 避免在斜面上钻孔

图1-17 以一次加工得到的孔作为对中基面
(6)对于装配,应该考虑以下设计准则:为避免安装错误,不影响正常工作,应减少安装时的手工操作,自动安装时应使零件容易夹持和运输,避免试车时出现事故,如图1-18~图1-20所示。

图1-18 避免同时装入两个配合面

图1-19 零件安装部位应该有必要的倒角
(7)考虑维修、回用的结构设计准则:尽量用标准件,合理划分部件,易损件应容易拆卸,避免零件在使用中损坏,注意用户的维修水平和条件,考虑维修时修复可能,如图1-21~图1-23所示。

图1-20 采用对称结构简化装配工艺

图1-21 中间的螺纹孔1中可以拧入螺钉,拆卸键方便

图1-22 齿轮传动装置的各轴承座不应分离,应为整体

图1-23 拆下轴承盖时不必拆下底座