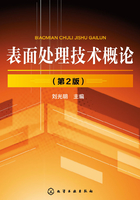
2.1 电镀的基本原理
2.1.1 电镀的基本过程
电镀的基本过程(以镀镍为例)是将零件浸在金属盐的(如NiSO4)溶液中作为阴极,金属板作为阳极,接通电源后,在零件表面就会沉积出金属镀层。

图2-1 电镀基本过程示意图
图2-1为电镀过程的示意图。例如在硫酸镍电镀溶液中镀镍时,在阴极上发生镍离子得电子还原为镍金属的反应,这是主要的电极反应,其反应式为
(2-1)
另外,镀液中的氢离子也会在阴极表面发生还原为氢的副反应
(2-2)
析氢副反应可能会引起电镀零件的氢脆,造成电镀效率降低等不良后果。
在镍阳极上发生金属镍失去电子变为镍离子的氧化反应
(2-3)
有时还有可能发生如下的副反应
(2-4)
在电镀过程中,电极反应是电流通过电极/溶液界面的必要条件,正因为如此,阴极上的还原沉积过程由以下几个过程构成。
①溶液中的金属离子(如水化金属离子或络合离子)通过电迁移、对流、扩散等形式到达阴极表面附近;
②金属离子在还原之前在阴极附近或表面发生化学转化;
③金属离子从阴极表面得到电子还原成金属原子;
④金属原子沿表面扩散到达生长点进入晶格生长,或与其他离子相遇形成晶核长大成晶体。
在形成金属晶体时又分两个步骤进行:结晶核的生成和长大。晶核的形成速度和成长速度决定所得到镀层晶粒的粗细。
电结晶是一个有电子参与的化学反应过程,需要有一定的外电场的作用。在平衡电位下,金属离子的还原和金属原子的氧化速度相等,金属镀层的晶核不可能形成。只有在阴极极化条件下,即比平衡电位更负的情况下才能生成金属镀层的晶核。所以说,为了产生金属晶核,需要一定的过电位。电结晶过程中的过电位与一般结晶过程中的过饱和度所起的作用相当。而且过电位的绝对值越大,金属晶核越容易形成,越容易得到细小的晶粒。
不是所有的金属离子都能从水溶液中沉积出来,如果在阴极上氢离子还原为氢的副反应占主要地位,则金属离子难以在阴极上析出。根据实验,金属离子自水溶液中电沉积的可能性,可从元素周期表中得出一定的规律,如表2-1所示。
表2-1 金属自水溶液中电沉积的可能性

由表2-1可知,能够从水溶液中电沉积的金属主要分布在铬分族以右的第4、5、6周期中,大约有30种。铬分族本身的Mo及W需要在其他元素的诱导下发生沉积。必须指出,这种分界不是绝对的,如电镀合金,或在有机溶剂及熔融盐中沉积金属,就会出现不同的结果。
2.1.2 电镀电源
前面已经说过,所谓的电镀是在电流的作用下,溶液中的金属离子在阴极还原并沉积在阴极表面的过程。所以,在基体表面制备电镀层就必须具备能够提供电流的电源设备。
用直流电向电镀槽供电时,多数工厂使用低压直流发电机和各种整流器。大多数的电镀设备都使用电压为6~12V的不同功率的电源。只有铝及其合金在阳极氧化时需要电压为60~120V的直流电源。电镀槽电流的供给也是多样的,当必须使电流密度保持一定的范围时,最好用单独的电源向镀槽供电,也可以用一个电源向几个镀槽供电。
直流发电机具有使用可靠、输出电压稳定、直流波形平滑,可提供大电流,维修方便等优点,但因其耗能较大、噪声高,使用受到限制,许多电镀厂家已经不再使用。
应用在电镀上的整流器有硅整流器、可控硅整流器等。整流器应具有转换率高、调节方便、维护简单,噪声小、无机械磨损等特点,并可直接安装在镀槽旁,节约了导电金属材料。
随着电镀技术的发展,先后出现了许多特种电镀技术。这些电镀技术都需要有专门的电镀电源,这些电源有些是在传统的电源上做一些改进,有些是具有新的特点的电源,比如脉冲电源、电刷镀电源等。
2.1.3 电镀电极
(1)阳极
电镀时发生氧化反应的电极为阳极。它有不溶性阳极和可溶性阳极之分。不溶性阳极的作用是导电和控制电流在阴极表面的分布;可溶性阳极除了有这两种作用外,还具有向镀液中补充放电金属离子的作用。后者在向镀液补充金属离子时,最好是阳极上溶解入溶液的金属离子的价数与阴极上消耗掉的相同,一般都采用与镀层金属相同的块体金属做可溶性阳极。如酸性镀锡时,阴极上消耗掉的是Sn2+,要求阳极上溶解入溶液的也是Sn2+;在碱性镀锡时,阴极上消耗掉的是Sn4+,要求阳极上溶解入溶液的也是Sn4+。同时还希望阳极上溶解入溶液中的金属离子的量与阴极上消耗掉的基本相同,以保持主盐浓度在电镀过程中的稳定。
阳极的纯度、形状及它在溶液中的悬挂位置和它在电镀时的表面状态等对电镀层质量都有影响。
(2)阴极
在电镀过程中的阴极为欲镀零件。电镀过程是发生在金属与电镀液相接触的界面上的电化学反应过程。要想使反应过程能够在金属表面顺利进行,必须保证镀液与制品基体表面接触良好,也就是说基体表面不允许有任何油污、锈或氧化皮,同时基体表面还应力求平整光滑,这样才能使镀液很好地浸润基体表面,才能使镀层与基体表面结合牢固。由于金属制品的材料种类很多,其原始表面状态也是各式各样的。因此,必须根据具体情况,在电镀前正确地选择与安排预处理工序及操作顺序。金属制品镀前常用的预处理工艺可以分为以下几类。
①机械处理 主要用于对粗糙表面进行机械整平,清除表面一些明显的缺陷。包括磨光、机械抛光、滚光、喷砂等。
磨光是利用粘有金刚砂或氧化铝等磨料的磨轮在高速旋转下以10~30m/s的速度磨削金属表面,除去表面的划痕、毛刺、焊缝、砂眼、氧化皮、腐蚀痕和锈斑等宏观缺陷,提高表面的平整程度。根据要求,一般需选取磨料粒度逐渐减小的几次磨光。磨光轮按照其本身材料的不同可以分为硬轮和软轮两类。如零件表面硬、形状简单或要求轮廓清晰时用硬轮(如毡轮)。表面软、形状复杂的则宜用软轮(如布轮)。
抛光是用抛光轮和抛光膏或抛光液对零件表面进一步轻微磨削以降低粗糙度。抛光轮转速较磨光轮更快。抛光轮分为非缝合式、缝合式和风冷布轮。一般形状复杂或最后精抛光的零件用非缝合式;形状简单用缝合式;大型平面、大圆管零件用风冷布轮。
滚光是零件与磨削介质(磨料和滚光液)在滚筒内低速旋转而滚磨出光的过程,常用于小零件的成批处理。滚筒多为多边桶形。滚光液为酸或碱中加入适量乳化剂、缓蚀剂等。常用磨料有钉子头、石英砂、皮革角、铁砂、贝壳、浮石和陶瓷片等。
喷砂是用净化的压缩空气将砂流喷向金属制件表面,在高速砂流强力的撞击下打掉其表面污垢物的过程。喷砂是为了除掉金属零件表面的毛刺、氧化皮、旧油漆层以及铸件表面上的熔渣等杂质。工业生产上进行喷砂主要是手工操作和半自动化操作。常用的喷砂机有吸入式和压力式。吸入式设备简单,但效率低,适用于小零件。压力式喷砂用于大中型零件的大批量生产,适用性广、效率高。国内广泛使用的空气压力喷砂室,适用于各种形状复杂的中小型零件。国内应用最多的砂料是石英砂(二氧化硅)。它虽然容易粉化,但不污染零件。采用铝矾土(氧化铝)喷砂,因其不易粉化,劳动条件好,砂料还可以循环使用。人造金刚砂因价格过于昂贵而较少使用。
②化学处理 包括除油与浸蚀。其过程是在适当的溶液中,利用零件表面与溶液接触时所发生的各种化学反应,除去零件表面的油污、锈及氧化皮。
金属制品经过各种加工处理其表面不可避免的粘附一层油污。如机械加工过程中使用的润滑油、半成品在库存期间所涂的防腐油;在磨、抛光过程中沾带的抛光膏和人手上的分泌物等。这些油污包括矿物油、动物油和植物油。按照其化学性质可分为皂化油(能够与碱起皂化反应的油,包括动物油和植物油)和非皂化油(不能与碱起皂化反应,包括矿物油)两大类。根据油污的不同性质,可以选择不同的除油剂。一般来说除油剂是各种化学试剂的混合物,配方比较多,但主要的化学物质大致相同。现在市面上有很多针对不同零件的专用除油剂出售。
③电化学处理 采用通电的方法强化化学除油和浸蚀的过程,处理速度快,效果好。
在含碱的溶液中零件为阳极或阴极,在直流电的作用下清除零件表面油污的过程称为电化学除油。在电解条件下,电极的极化作用使油与溶液界面的表面张力下降;电极上析出的大量氢气泡或氧气泡对油膜具有强烈的剥离作用和机械搅拌作用,加速了除油过程。而且除油液本身的皂化、乳化作用的共同发挥使电化学除油的速度加快,除油效果更彻底。
对浸蚀过程通以电流,利用电解作用除去零件表面的氧化皮和其他腐蚀产物的过程叫电化学浸蚀。电化学浸蚀的优点是浸蚀速度快,浸蚀液消耗小,使用寿命长。缺点是增加设备,对于形状复杂的零件,浸蚀效果差。电化学浸蚀主要用于黑色金属,有色金属很少使用。对于附有厚而致密氧化皮的零件不应该直接进入电解浸蚀液,应先进行化学浸蚀,松动氧化皮后再进行电化学浸蚀。电化学浸蚀可分为阳极浸蚀和阴极浸蚀,可根据被处理零件的性质及表面状况而选择。
④超声波处理 是在超声波场作用下进行的除油或清洗过程。主要用于形状复杂或对表面处理要求极高的零件。
实践证明,电镀生产中出现的质量问题,相当多的并不是由于电镀工艺本身所造成,而是由于工件镀前处理不当或欠佳所致。这样的例子很多,造成了很大的浪费,也耽误了工时。因此,必须严格执行电镀技术规范中对镀前处理的要求。
2.1.4 电镀挂具
挂具的主要作用是固定镀件和传导电流。设计挂具的基本要求是:有良好导电性和化学稳定性;有足够机械强度,保证装夹牢固;装卸方便;非工作部分绝缘处理。
挂具的结构多种多样,既有通用型挂具,也有专用挂具,尤其是对复杂形状的镀件常需专门设计。设计挂具时要考虑镀件形状、大小、设备能力和生产流程。在满足对挂具基本要求的前提下,还应货源广、成本低。通常在外形尺寸上要求挂具顶部距液面不小于50mm,挂具地步距槽底约100~200mm,挂具与挂具之间约20~50mm。
挂具一般由吊钩、提杆、主架、支架和挂钩五部分组成,如图2-2所示。

图2-2 电镀挂具
挂具的吊钩与极棒相连,同时具有承重和导电作用。所以吊钩材料应有足够的机械强度和导电性。吊钩与极棒应有良好的接触。
挂具的非导电部位用绝缘材料包扎或涂覆。要求绝缘材料有化学稳定性、耐热和耐水性。涂层与挂具应结合牢固,涂层坚韧致密。
2.1.5 电镀槽
镀槽是电镀所用的主要工艺槽。常用镀槽的大小、结构和材料等皆有多种类型。镀槽的大小主要由生产能力与操作方便决定。镀槽结构设计既要保证有足够的机械强度,同时要考虑与辅助设备方便而有效的链接。镀槽材料的选用要符合工艺条件及其用途,并且尽可能成本低,适应性广。通常,碱性镀槽的槽体用碳钢板,加热系统用普通钢管。常温碱性镀槽也用钢板内衬聚氯乙烯,以便于碱性氰化物镀液。酸性镀槽可用聚氯乙烯板焊制,或钢板内衬聚氯乙烯板。加热系统可用铅锑合金管。有时热酸性槽也用玻璃钢作槽体。
2.1.6 电镀溶液的组成及其作用
电镀是在电镀液中进行的。不同的镀层金属所使用的电镀溶液的组成多种多样,即便是同一种金属镀层所采用的电镀溶液也可能是差别很大。不管是什么样的电镀液配方都大致由以下几部分组成:主盐、络合剂、导电盐、缓冲剂、阳极去极化剂以及添加剂等,它们各有不同的作用,下面分别介绍。
(1)主盐
能够在阴极上沉积出所要求的镀层金属的盐称为主盐,如电镀镍时的硫酸镍、电镀铜时的硫酸铜等。根据主盐性质的不同,可以将电镀液分为简单盐电镀溶液和络合物电镀溶液两大类。
简单盐电镀溶液中主要金属离子以简单离子形式存在(如Cu2+、Ni2+、Zn2+等),其溶液都是酸性的。在络合物电镀溶液中,因含有络合剂,主要金属离子以络离子形式存在(如[Cu(CN)3]2-、[Zn(CN)4]2-、[Ag(CN)2]-等),其溶液多数是碱性的,也有酸性的。
(2)导电盐
能提高溶液的电导率,而对放电金属离子不起络合作用的物质。这类物质包括酸、碱和盐,由于它们的主要作用是用来提高溶液的导电性,习惯上通称为导电盐。如酸性镀铜溶液中的H2SO4,氯化物镀锌溶液中的KCl、NaCl及氰化物镀铜溶液中的NaOH和Na2CO3等。
(3)络合剂
在溶液中能与金属离子生成络合离子的物质称为络合剂。如氰化物镀液中的NaCN或KCN,焦磷酸盐镀液中的K4P2O7或Na4P2O7等。
(4)缓冲剂
缓冲剂是用来稳定溶液的pH值,特别是阴极表面附近的pH值。缓冲剂一般是弱酸或弱酸的酸式盐,如镀镍溶液中的H3BO3和焦磷酸盐镀液中的Na2HPO4等。
任何一种缓冲剂都只能在一定的范围内具有好的缓冲作用,超过这一范围其缓冲作用将不明显或者完全没有缓冲作用,而且还必须有足够的量才能起到稳定溶液pH值的作用。缓冲剂可以减缓阴极表面因析氢而造成的局部pH值的升高,并能将其控制在最佳值范围内,所以对提高阴极极化有一定作用,也有利于提高镀液的分散能力和镀层质量。
(5)稳定剂
稳定剂主要用来防止镀液中主盐水解或金属离子的氧化,保持溶液的稳定。如酸性镀锡和镀铜溶液中的硫酸、酸性镀锡溶液中的抗氧化剂等。
(6)阳极活化剂
在电镀过程中能够消除或降低阳极极化的物质,它可以促进阳极正常溶解,提高阳极电流密度。如镀镍溶液中的氯化物,氰化镀铜溶液中的酒石酸盐等。
(7)添加剂
是指那些在镀液中含量很低,但对镀液和镀层性能却有着显著影响的物质。近年来添加剂的发展速度很快.在电镀生产中占的地位越来越重要,种类越来越多,而且越来越多地使用复合添加剂来代替单一添加剂。按照它们在电镀溶液中所起的作用,大致可分为如下几类。
①光亮剂 它的加入可以使镀层光亮。如镀镍中的糖精及1,4-丁炔二醇;氯化物镀锌中的苄叉丙酮等。当在镀液中含有几种光亮剂或将几种物质配制成复合光亮剂时,常根据光亮剂的基团及其在镀液中的作用、性能和对镀层的影响等,又将它们分为初级光亮剂、次级光亮剂、载体光亮剂和辅助光亮剂等。
②整平剂 具有使镀层将基体表面细微不平处填平作用的物质。如镀镍溶液中的香豆素,酸性光亮镀铜溶液中的四氢噻唑硫酮、甲基紫等。
③润湿剂 它们的主要作用是降低溶液与阴极间的界面张力,使氢气泡容易脱离阴极表面,从而防止镀层产生针孔。这类物质多为表面活性剂,其添加量很少,对镀液和镀层的其他性能没有明显的影响,如镀镍溶液中的十二烷基硫酸钠。
④应力消除剂 能够降低镀层内应力,提高镀层韧性的物质。如碱性镀锌溶液中的香豆素等。
⑤镀层细化剂 它是能使镀层结晶细化并具有光泽的添加剂。如碱性镀锌溶液中的DE及DPE等添加剂。
⑥抑雾剂 这是一类表面活性剂,具有发泡作用。在气体或机械搅拌的作用下,可以在液面生成一层较厚的稳定的泡沫以抑制气体析出时带出的酸雾、碱雾或溶液的飞沫。选择原则是应对镀液和镀层的其他性能无害,而本身在溶液中相当稳定。抑雾剂的加入量一般都很小,过多会造成泡沫外溢或爆鸣,如果选择或使用不当则会在镀层上造成气流痕、针孔等。
⑦无机添加剂 此类添加剂多数是硫、硒、碲的化合物及一些可与镀层金属共析的其他金属盐。这些金属离子对镀层的性能会有显著的影响,而且这种影响是多方面的。例如在镀镍溶液中加入镉盐可以得到光亮的镀层,在硫酸盐镀锡溶液中加入铅盐可防止镀层长锡须,在镀银或镀金溶液中加入锑或钴盐可以提高镀层的硬度等。但是这些金属的含量必须很低,否则将会使镀层恶化,如发黑、发脆、产生条纹等。
2.1.7 影响镀层质量的因素
作为金属镀层,无论其使用目的和使用场合如何,都应该满足以下要求:镀层致密无孔,厚度均匀一致,镀层与基体结合牢固。
影响镀层质量的主要因素有以下几个方面。
(1)镀前处理质量
镀前处理对镀层质量的重要性在前面的内容已经涉及。镀前处理的每道工序都会对镀层质量产生直接影响。相比其他电镀工序,镀前处理是最容易被忽视的,也是最容易出问题的地方。
(2)电镀溶液的本性
镀液的性质、组成各成分的含量以及附加盐、添加剂的含量都会影响镀层质量。这部分在电镀液的组成部分已经有所介绍。
(3)基体金属的本性
镀层金属与基体金属的结合是否良好,与基体金属的化学性质有密切关系。如果基体金属的电位负于镀层金属的电位,或对易于钝化的基体或中间层,若不采取适当的措施,很难获得结合牢固的镀层。
(4)电镀过程
电流密度、温度和搅拌等因素的影响。
在其他条件不变的情况下,提高阴极电流密度,可以使镀液的阴极极化作用增强,镀层结晶变得细致紧密。如果阴极电流密度过大,超过允许的上限时,常常会出现镀层烧焦的现象,即形成黑色的海绵状镀层。电流密度过低时,阴极极化小,镀层结晶较粗,而且沉积速度慢。
提高镀液的温度,一方面加快了离子的扩散速度,导致浓差极化降低;另一方面,使离子的活性增强,电化学极化降低,阴极反应速度加快,从而使阴极极化降低,镀层结晶变粗。但是,镀液温度的升高使离子的运动速度加快,从而可以弥补由于电流密度过大或主盐浓度偏低所造成的不良影响。温度升高还可以减少镀层的脆性,提高沉积速度。
搅拌能够加速溶液的对流,使扩散层减薄,使阴极附近被消耗了的金属离子得以及时补充,从而降低了浓差极化。在其他条件不变的情况下,搅拌会使镀层结晶变粗。但是,搅拌可以提高允许电流密度的上限,可以在较高的电流密度和较高的电流效率下,获得致密的镀层。搅拌的方式有机械搅拌、压缩空气搅拌等。其中,压缩空气搅拌只适用于那些不受空气中的氧和二氧化碳作用的酸性电解液。
(5)析氢反应
在电镀过程中大多数镀液的阴极反应都伴随着有氢气的析出。在不少情况下析氢对镀层质量有恶劣的影响,主要有针孔或麻点、鼓泡、氢脆等。如当析出的氢气粘附在阴极表面上会产生针孔或麻点,当一部分还原的氢原子渗入基体金属或镀层中,使基体金属或镀层的韧性下降而变脆,叫氢脆。为了消除氢脆的不良影响,应在镀后进行高温除氢处理。
(6)镀后处理
镀后对镀件的清洗、钝化、除氢、抛光、保管等都会继续影响镀层质量。
除了上面所列举的因素外,影响镀层质量的因素还有很多。电镀工艺发展到现在,具体某种因素对镀层质量的影响已经被研究的很充分,相关的研究论文或书籍很多。当然,上面这些因素的影响不是孤立的,改变其中某一个参数很可能引起其他参数的联动变化,需要综合分析,找出内在的联系。有经验的电镀工程师或技工完全可以凭着肉眼观察发现问题出在哪个环节。当然,经验是在丰富的理论知识结合长时间的生产实践中总结出来的。