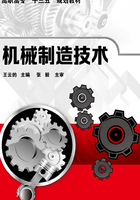
第3章 金属切削机床概述
3.1 车床
3.1.1 CA6140型普通车床的组成
1.车削加工工艺范围
车削是机械加工中最基本、应用最广泛的一种加工方法,主要用于加工各种回转表面,如内外圆柱表面、内外圆锥表面、成形回转面和回转体的端面等。通常,车削的主运动由工件随主轴旋转来实现,进给运动由刀架的纵、横向移动来完成。车床使用的刀具为各种车刀,也可用钻头、扩孔钻、铰刀、镗刀进行孔加工,用丝锥、板牙加工内外螺纹表面。由于大多数机器零件都具有回转表面,车床的工艺范围又较广,因此,车削加工的应用极为广泛。如图3-1所示是卧式车床所能加工的典型表面。

图3-1 卧式车床的典型加工
2.车床的分类
在所有车床类机床中,卧式车床和立式车床(如图3-2所示)应用最广。此外,还有转塔车床、马鞍车床、单轴自动车床和半自动车床、仿形车床、数控车床及各种大批量生产中使用的专用车床等。
如图3-2(a)所示为单柱立式车床,图3-2(b)所示为双柱立式车床,它们与卧式车床的不同之处是主轴竖立,工件安装在由主轴带动旋转的工作台2上,横梁5上装有垂直刀架4,可作上下左右移动。立式车床适合用于加工直径大而长度短的重型盘类零件。

图3-2 立式车床
1—底座;2—工作台;3—立柱;4—垂直刀架;5—横梁 6—垂直刀架进给箱;7—侧刀架;8—侧刀架进给箱;9—顶梁

图3-3 转塔车床
1—主轴箱;2—前刀架;3—六角刀架;4—床身;5—溜板箱;6—进给箱
转塔车床(如图3-3所示)有一个可旋转换位的六角刀架3,以替代卧式车床的尾座,在六角刀架上可同时安装钻头、铰刀和板牙等各种切削刀具,这些刀具通常是按工件的加工顺序安装的,因此,在一个零件的加工过程中,只要使六角刀架依次转位,便可迅速更换刀具。此外,六角刀架上的刀具与方刀架上的刀具可同时进行加工。
3. CA6140型卧式车床的组成部件
普通车床应用最多,所占比例较大,代表型号CA6140 。车床的加工工艺范围很广,它适用于加工各种轴类、套筒类和盘类零件上的回转表面,如:内圆柱面、圆锥面、环槽及成形回转表面、端面及各种常用螺纹,还可以进行钻孔、扩孔、铰孔和滚花等工艺。最大的特点是通用性强,价格低廉,加工范围广泛,但生产率低,操作工人劳动强度高,适用于单件小批生产。如图3-4所示为CA6140型卧式车床的外形图,其主要组成部件及其功用如下。

图3-4 CA6140型卧式车床
1—主轴箱;2—床鞍;3—中滑板;4—回转盘;5—方刀架;6—小滑板;7—尾座;8—床身;9—右床腿;10—光杠;11—丝杠;12—溜板箱;13—左床腿;14—进给箱;15—挂轮架;16—操纵手柄
(1)CA6140车床的布局及主要技术性能 由于卧式车床主要加工轴类和直径不大的盘套类零件,所以采用卧式布局,其主要性能:
床身上最大工件回转直径 400mm
最大工件长度 750mm;1000mm;1500mm;2000mm
刀架上最大工件回转直径 210mm
主轴转速 正转 24级 10~1400r/min
反转 12级 4~1580r/min
进给量 纵向 64级 0.028~6.33mm/r
横向 64级 0.014~3.16mm/r
车削螺纹范围 米制螺纹 44种 P=1~192mm
英制螺纹 20种 α=2~24牙/in
模数螺纹 39种 m=0.25~48mm
径节螺纹 37种 DP=1~96牙/in
主电机功率 7.5kW
(2)车床的主要组成部件 CA6140卧式车床主要由主轴箱、进给箱、溜板箱、床鞍、尾座、床身、中滑板、小滑板、回转盘、方刀架、左右床腿、光杠、丝杠、挂轮架、操纵手柄等部分构成。
①主轴箱 主轴箱1(又称为床头箱或主变速箱)固定在床身8的左端。其内装有主轴和变速、换向机构,由电动机经变速机构带动主轴旋转,实现主运动,并获得所需转速及转向。主轴前端可安装三爪自定心卡盘、四爪单动卡盘等夹具,用以装夹工件。
②床鞍 床鞍2(又称为大拖板)位于床身8的中部,并可带动中滑板3、回转盘4、小滑板6和方刀架5沿床身上的导轨作纵向进给运动。
③溜板箱 溜板箱12固定在床鞍2的底部,可带动方刀架5一起作纵向运动。溜板箱的功用是将进给箱14传来的运动传递给方刀架,使方刀架实现纵向进给、横向进给、快速移动或车螺纹。在溜板箱上装有各种操纵手柄及按钮,可以方便地选择纵、横机动进给运动的接通、断开及变向。溜板箱内设有连锁装置,可以避免光杠10和丝杠11同时转动。
④进给箱 进给箱14固定在床身8的左前侧。进给箱是进给运动传动链中主要的传动比变换装置,它的功用是改变被加工螺纹的导程或机动进给的进给量。
⑤方刀架 方刀架5用来夹持车刀,并使其作纵向、横向或斜向移动。方刀架安装在小滑板6上,用来夹持车刀;小滑板装在回转盘4上,可沿回转盘上导轨作短距离移动;回转盘可带动方刀架5在中滑板3上顺时针或逆时针转动一定的角度;中滑板可在床鞍2(大拖板)的横向导轨上面作垂直于床身的横向移动;床鞍可沿床身的导轨作纵向移动。
⑥尾座 尾座7安装于床身8的尾座导轨上。其上的套筒可安装顶尖,以便支承较长工件的一端;也可装夹钻头、铰刀等孔加工刀具,对工件进行加工,此时可摇动手轮使套筒轴向移动,以实现纵向进给。尾座可沿床身顶面的一组导轨(尾座导轨)作纵向调整移动,然后夹紧在所需要的位置上,以适应加工不同长度工件的需要。尾座还可以相对其底座沿横向调整位置,以车削较长且锥度较小的外圆锥面。
⑦床身 床身8固定在左床腿13和右床腿9上。床身是车床的基本支承件。车床的各个主要部件均安装于床身上,并保持各部件间具有准确的相对位置。
⑧丝杠 丝杠用于车螺纹加工,将进给箱的运动传给溜板箱。
⑨光杠 光杠用于一般的车削加工,进给时将进给箱的运动传给溜板箱。
3.1.2 CA6140型卧式车床的传动系统分析
CA6140型卧式车床的传动系统由主运动传动链、车螺纹运动传动链、纵向进给运动传动链、横向进给运动传动链、刀架的快速空行程传动链组成。
传动系统的结构如图3-5所示。

图3-5 CA6140型卧式车床的传动系统图
主运动传动链的两端件是主电动机与主轴,它的功能是把动力源的运动及动力传给主轴,并满足卧式车床主轴开、停、变速和换向的要求。
(1)两端件 电动机—主轴。
(2)计算位移 所谓计算位移,是指传动链首末传动件之间相对运动量的对应关系。CA6140型卧式车床的主运动传动链是一条外联系传动链,电动机与主轴各自转动时运动量的关系为各自的转速,即:主电动机—主轴1450(r/min)—n(r/min)。
(3)传动路线表达式 主运动由主电动机(7.5kW,1450r/min)经V带传动Ⅰ轴而输入主轴箱。轴Ⅰ上安装有双向多片式摩擦离合器M1,以控制主轴的启动、停转及旋转方向。M1左边摩擦片结合时,空套的z51、z56双联齿轮与Ⅰ轴一起转动,通过两对齿轮副56/38、51/43带动Ⅱ轴实现主轴正转。右边摩擦片结合时,由齿轮z50与Ⅰ轴一起转动,齿轮z50通过Ⅶ轴的中间齿轮z34带动Ⅱ轴上的齿轮z30实现主轴反转。当两边摩擦片都脱开时,则Ⅰ轴空转,此时主轴静止不动。Ⅱ轴的运动通过Ⅱ—Ⅲ轴之间的3对齿轮副39/41、22/58、30/50带动Ⅲ轴。Ⅲ轴的运动可由两种传动路线至主轴,当主轴Ⅵ轴的滑移齿轮z50处于左边位置时,轴Ⅲ的运动直接由齿轮z63传至与主轴用花键连接的滑移齿轮z50,从而带动主轴以高速旋转;当主轴Ⅵ轴的滑移齿轮z50右移,脱开与轴Ⅲ上齿轮z63的啮合,并通过其内齿轮与主轴上齿轮z58左端齿轮啮合(即M2结合)时,轴Ⅲ的运动经轴Ⅲ—Ⅳ间及轴Ⅳ—Ⅴ间两组双联滑移齿轮变速装置传至轴Ⅴ,再经齿轮副26/58使主轴获得中、低转速。其传动路线表达式为:
(4)主轴转速级数 由传动系统图和传动路线表达式可以看出,主轴正转时,适用各滑动齿轮轴向位置的各种不同组合,主轴共可获得Z=2×3×(1+2×2)=30级转速,轴Ⅲ—Ⅴ间的4种传动比为:u1=(50/50)×(51/50)≈1,u3=(20/80)×(51/50)≈1/4,u2=(50/50)×(20/80)=1/4,u4=(20/80)×(20/80)=1/16。由于u2≈u3,所以主轴实际上获得的转速级数为:Z=2×3×[1+(2×2-1)]=24级。同理,反转时:Z'=1×3×[1+(2×2-1)]=12级。
(5)运动平衡式 主轴的转速可按下列运动平衡式计算:
n主=1450×(130/230)×(1-ε)uⅠ—ⅡuⅡ—ⅢuⅢ—Ⅵ
最低转速:
nmin=1450×(130/230)×(1-0.02)×(51/43)×(22/58)×(20/80)×(20/80)×(26/58)
≈10(r/min)
最高转速:
nmax=1450×(130/230)×(1-0.02)×(56/38)×(39/41)×(63/50)=1418(r/min)
式中 n主——主轴转数,r/min;
ε——V带传动的滑动系数,近似取ε=0.02;
uⅠ—Ⅱ、uⅡ—Ⅲ、uⅢ—Ⅵ——轴Ⅰ—Ⅱ、Ⅱ—Ⅲ、Ⅲ—Ⅵ间的传动比。
主轴各级转速的数值,可根据主运动传动所经过的传动件的运动参数(如带轮直径、齿轮齿数等)列出运动平衡式来求出。图3-6所示为CA6140型卧式车床主运动的转速图。

图3-6 CA6140型卧式车床主运动的转速图
3.1.3 车削螺纹传动链
CA6140型卧式车床可车削米制、模数制、英制和径节制4种标准螺纹,另外还可加工大导程螺纹、非标准螺纹及较精密螺纹。
3.1.4 车削米制螺纹
米制螺纹是应用最广泛的一种螺纹,在车削螺纹时,应满足主轴带动工件旋转一转,刀架带动刀具轴向进给所加工螺纹的一个导程。国家标准规定了米制螺纹的标准导程值,表3-1列出了CA6140型车床能车制的常用米制螺纹标准导程值。
表3-1 CA6140型普通车床米制螺纹导程 mm

从表3-1中可以看出,每一行的导程组成等差数列,行与行之间的导程值成一公比为2的等比数列,在车削米制螺纹的传动链中设置的换置机构应能将标准螺纹加工出来,并且满足传动链尽量简便。
(1)车削米制螺纹
①车削米制螺纹的传动路线 车削米制螺纹时,运动由主轴Ⅵ经齿轮副58/58至轴Ⅸ,再经三星轮换向机构33/33(车左螺纹时经33/25×25/33)传动轴Ⅹ,再经挂轮63/100×100/75传到进给箱中轴XⅢ,进给箱中的离合器M3和M4脱开,M5接合,再经移换机构的齿轮副25/36传到轴ⅪⅤ,由轴ⅪⅤ和ⅩⅤ间的基本变速组uj、移换机构的齿轮副25/36×36/25将运动传到轴ⅩⅥ,再经增倍变速组ub传至轴ⅩⅧ,最后经齿式离合器M5,传动丝杠ⅩⅨ,经溜板箱带动刀架纵向运动,完成米制螺纹的加工。其传动路线表达如下:
②车削米制螺纹的运动平衡式 由传动系统图和传动路线表达式,可以列出车削米制螺纹的运动平衡式:
式中 uj、ub——基本变速组传动比和增倍变速组传动比。
将上式化简可得:
P=7ujub
进给箱中的基本变速组uj为双轴滑移齿轮变速机构,由轴ⅪⅤ上的8个固定齿轮和轴ⅩⅤ上的四个滑移齿轮组成,每个滑移齿轮可分别与邻近的两个固定齿轮相啮合,共有8种不同的传动比:
不难看出,除了uj1和uj5外,其余的6个传动比组成一个等差数列。改变uj的值,就可以车削出按等差数列排列的导程组。
进给箱中的增倍变速组ub由轴ⅩⅥ—轴ⅩⅧ间的三轴滑移齿轮机构组成,可变换4种不同的传动比:
它们之间依次相差2倍,改变ub的值,可将基本组的传动比成倍地增加或缩小。
把uj、ub的值代入上式,得到8×4=32种导程值,其中符合标准的有20种,见表3-1。可以看出,表中的每一行都是按等差数列排列的,而行与行之间成倍数关系。
③扩大导程传动路线 从表3-1可以看出,此传动路线能加工的最大螺纹导程是12mm。如果需车削导程大于12mm的米制螺纹,应采用扩大导程传动路线。这时,主轴Ⅵ的运动(此时M2接合,主轴处于低速状态)经斜齿轮传动副58/26到轴Ⅴ,背轮机构80/20与80/20或50/50至轴Ⅲ,再经44/44、26/58(轴Ⅸ滑移齿轮z58处于右位与轴Ⅷz 26啮合)传到轴Ⅸ,其传动路线表达式为:
(主轴)Ⅵ—-Ⅸ-(按正常导程传动路线)
从传动路线表达式可知,扩大螺纹导程时,主轴Ⅵ到轴Ⅸ的传动比为:
当主轴转速为40~125r/min时,
当主轴转速为10~32r/min 时,
而正常螺纹导程时,主轴Ⅵ到轴Ⅸ的传动比为:
所以,通过扩大导程传动路线可将正常螺纹导程扩大4倍或16倍。CA6140型车床车削大导程米制螺纹时,最大螺纹导程为Pmax=12×16=192mm。
(2)车削英制螺纹 英制螺纹以每英寸长度上的螺纹扣数α(扣/in)表示,其标准值也按分段等差数列的规律排列。英制螺纹的导程Pα=1/α(in)。由于CA6140型车床的丝杠是米制螺纹,被加工的英制螺纹也应换算成以毫米为单位的相应导程值,即
车削英制螺纹时,对传动路线作如下变动,首先,改变传动链中部分传动副的传动比,使其包含特殊因子25.4;其次,将基本组两轴的主、被动关系对调,以便使分母为等差级数。其余部分的传动路线与车削米制螺纹时相同。其运动平衡式为:
将Pα=25.4/α代入上式得
变换uj、ub的值,就可得到各种标准的英制螺纹。
(3)车削模数螺纹 模数螺纹主要用在米制蜗杆中,模数螺纹螺距P=πm,P也是分段等差数列。所以模数螺纹的导程为:
Pm=kπm
式中 Pm——模数螺纹的导程,mm;
k——螺纹的头数;
m——螺纹模数。
模数螺纹的标准模数m也是分段等差数列。车削时的传动路线与车削米制螺纹的传动路线基本相同。由于模数螺纹的螺距中含有π因子,因此车削模数螺纹时所用的挂轮与车削米制螺纹时不同,需用来引入常数π,其运动平衡式为
上式中,将运动平衡方程式整理后得:
变换uj、ub的值,就可得到各种不同模数的螺纹。
(4)车削径节螺纹 径节螺纹主要用于同英制蜗轮相配合,即为英制蜗杆,其标准参数为径节,用DP表示,其定义为:对于英制蜗轮,将其总齿数折算到每一英寸分度圆直径上所得的齿数值,称为径节。根据径节的定义可得蜗轮齿距为:
式中 z——蜗轮的齿数;
D——蜗轮的分度圆直径,in。
只有英制蜗杆的轴向齿距PDP与蜗轮齿距π/DP相等才能正确啮合,而径节制螺纹的导程为英制蜗杆的轴向齿距为:
标准径节的数列也是分段等差数列。径节螺纹的导程排列的规律与英制螺纹相同,只是含有特殊因子25.4π。车削径节螺纹时,可采用英制螺纹的传动路线,但挂轮需换为,其运动平衡式为:
上式中 ,将运动平衡方程式整理后得:
变换uj、ub的值,可得常用的24种螺纹径节。
(5)车削非标准螺纹和精密螺纹 所谓非标准螺纹是指利用上述传动路线无法得到的螺纹。这时需将进给箱中的齿式离合器M1、M4和M5全部啮合,被加工螺纹的导程LⅠ依靠调整挂轮的传动比μ传来实现。其运动平衡式为:
所以,挂轮的换置公式为
适当地选择挂轮a、b、c及d的齿数,就可车出所需要的非标准螺纹。同时,由于螺纹传动链不再经过进给箱中任何齿轮传动,减少了传动件制造和装配误差对被加工螺纹导程的影响,若选择高精度的齿轮作挂轮,则可加工精密螺纹。
(6)机动进给运动传动链 进给运动传动链的首末端件分别为主轴和刀架。但与车螺纹传动链不同,它为一条外联系传动链。由主轴至进给箱ⅩⅦ轴的传动路线与车螺纹相同,其后运动经齿轮副28/56及联轴器传至光杠(ⅩⅢ轴),再由光杠经溜板箱中的传动机构,分别传至齿轮条机构(纵进给)和丝杠螺母机构(横进给),使刀架作纵向或横向机动进给。其传动路线表达式如下:
①纵向机动进给传动链 CA6140型车床纵向机动进给量有64种。当运动由主轴经正常导程的米制螺纹传动路线时,可获得正常进给量。这时的运动平衡式为:
将上式化简可得:
f纵=0.711ujub
通过变换uj、ub的值,可得到32种正常进给量(范围为0.08~1.22mm/r),其余32种进给量可分别通过英制螺纹传动路线和扩大导程传动路线得到。
②横向机动进给传动链 由传动系统图分析可知,当横向机动进给与纵向进给的传动路线一致时,所得到的横向进给量是纵向进给量的一半,横向与纵向进给量的种数相同,都为64种。
③刀架快速机动移动 刀架的快速移动由装于溜板箱内的快速电动机(0.25kW,2800r/min)带动。快速电动机的运动经齿轮副传至ⅩⅩ轴,再经溜板箱与进给运动相同的传动路线传至刀架,使刀架快速纵移或横移。
当快速电动机带动ⅩⅩ轴快速旋转时,为避免与进给箱传来的慢速进给运动发生干涉,在ⅩⅩ轴上装有单向超越离合器M6,可保证ⅩⅩ轴的工作安全。

图3-7 超越离合器的结构原理
1—空套齿轮;2—星形体;3—滚柱;4—顶销;5—弹簧
单向超越离合器M6的结构原理如图3-7所示。它由空套齿轮1(即溜板箱中的Z56齿轮),星形体2,滚柱3,顶销4和弹簧5组成。当机动进给运动由空套齿轮1传入并逆时针转动时,带动滚柱3挤入楔缝,使星形体随同齿轮1一起转动,再经安全离合器M7带动ⅩⅩ轴转动。当快速运动传入时,星形体由ⅩⅩ轴带动逆时针快速转动时,由于星形体2超越齿轮1转动,使滚柱3退出楔缝,使星形体与齿轮1自动脱开,由进给箱传至齿轮1的运动虽未停机,超越离合器将自动接合,刀架恢复正常的进给运动。
3.1.5 主轴箱
主轴箱主要由主轴部件、传动机构、开停与制动装置、操纵机构及润滑装置等组成。为了便于了解主轴箱内各传动件的传动关系,传动件的结构、形状、装配方式及其支承结构,常采用展开图的形式表示。主轴箱基本上按主轴箱内各传动轴的传动顺序,沿其轴线取剖切面,展开绘制而成,其剖切面的位置如图3-8所示。以下对主轴箱内主要部件的结构、工作原理及调整作简单介绍。
主轴箱展开图及中间轴间隙调整:
主轴上装有3个齿轮,最右边的是空套在主轴上的左旋斜齿轮,其传动较平衡,当离合器M2接合时,此齿轮传动所产生的轴向力指向前轴承,以抵消部分轴向切削力,减小前轴承所承受的轴向力。中间滑移齿轮用花键与主轴相连,该齿轮的图示位置为高速传动。当其处于中间空当位置时,可用手拨动主轴,以便装夹和调整工件;当滑移齿轮移到最右边位置时,其上的内齿与斜齿轮左侧的外齿相啮合,即齿式离合器M2接合,此时获低速传动。最左边的齿轮固定在主轴上,通过它把运动传给进给系统。现以图3-8中的轴Ⅲ为例说明其结构及轴承的调整。花键轴Ⅲ较长,采用了三支承结构,两端为圆锥滚子轴承,中间为深沟球轴承。松开锁紧螺母18,拧动螺钉17,推动压盖19及圆锥滚子轴承的外圈右移,消除了左端轴承间隙,然后轴部件向右移,由于右端圆锥滚子轴承的外圈被箱体的台阶孔所挡,因而又消除了右轴承的间隙。并由此而限定了轴Ⅲ组件在箱体上的轴向位置。共有4个台阶,两端台阶分别安装圆锥滚子轴承,右端的第二个台阶分别串装有齿轮9、10、11及垫圈14,垫圈14为调整环,以限定上述零件在其上的轴向位置。齿轮12右端面紧靠深沟球轴承内圈,左端由轴用弹簧卡圈13定位,从而限定了齿轮12的轴向位置。三联齿轮15可以在轴上滑移,实现3种不同的工作位置。轴向位置不能限定,但必须有可靠而较准确的定位。方法是通过导向轴5上的3个定位槽和在拨叉8上安装的弹簧钢珠,实现三联齿轮3种不同工作位置的定位。松开螺母7,拧动有内六方孔的调节螺钉6可调节弹簧力的大小,以保证定位的可靠性。

图3-8 主轴箱展开图
1—带轮;2—花键套筒;3—法兰;4—箱体;5—导向轴;6—调节螺钉;7—螺母;8—拨叉;9~12—齿轮;13—弹簧卡圈;14—垫圈;15—三联齿轮;16—轴承盖;17—螺钉;18—锁紧螺母;19—压盖
3.1.6 双向式多片摩擦离合器结构
如图3-9所示,摩擦离合器由内摩擦片3、外摩擦片2、压块8和螺母9、销子5和推拉杆7等组成,离合器左右两部分的结构是相同的。图3-9表示的是左离合器结构,内摩擦片3的孔是花键孔,装在轴Ⅰ的花键上,随轴Ⅰ旋转,其外径略小于双联空套齿轮1套筒的内孔,不能直接传动齿轮1。外摩擦片2的孔是圆孔,其孔径略大于花键轴的外径,其外圆上有4个凸起,嵌在空套齿轮1套筒的4个缺口中,所以齿轮1随外摩擦片一起旋转,内外摩擦片相间安装。当推拉杆7通过销子5向左推动压块8时,将内外摩擦片压紧。轴Ⅰ的转矩由内摩擦片1通过内外摩擦片之间的摩擦力传给外摩擦片2,再由外摩擦片2传动齿轮1,使主轴正转。同理,当压块8向右压时,主轴反转。压块8处于中间位置时,左右内外摩擦片无压力作用,离合器脱开,主轴停转。摩擦离合器不但实现主轴的正反转和停止,并且在接通主运动链时还能起过载保护作用。当机床过载时,摩擦片打滑,避免损坏机床部件。摩擦片传递转矩大小在摩擦片数量一定的情况下取决于摩擦片之间压紧力的大小,其压紧力的大小是根据额定转矩调整的。当摩擦片磨损后,压紧力减小,这时可进行调整,其调整方法是用工具将防松的弹簧销4压进压块8的孔内,旋转螺母9,使螺母9相对压块8转动,螺母9相对压块8产生轴向左移,直到能可靠压紧摩擦片,松开弹簧销4,并使其重新卡入螺母9的缺口中,防止其松动。

图3-9 双向式多片摩擦离合器
1—双联空套齿轮;2—外摩擦片;3—内摩擦片;4—弹簧销;5—销子;6—羊角形摆块(元宝销);7—推拉杆;8—压块;9—螺母;10,11—止推片;12—销轴;13—滑套;14—空套齿轮;a,b—回油孔
3.1.7 溜板箱
溜板箱的作用是将丝杠和光杠传来的旋转运动变为刀架进给运动,控制刀架运动的接通、断开和换向。溜板箱是由接通、断开和转换纵、横向进给运动的操纵机构,接通丝杠传动的开合螺母机构,保证机床工作安全的互锁机构,保证机床工作安全的过载保护机构和实现刀架快慢速自动转换的超越离合器等几部分组成的。下面将介绍主要机构的机构、工作原理及有关调整。
3.1.8 安全离合器的结构
安全离合器是防止进给机构过载或发生偶然事故时机床部件的保护装置。在刀架机动进给过程中,如进给抗力过大或刀架移动受到阻碍时,安全离合器能自动断开轴的运动,如图3-10所示,安全离合器由端面带螺旋齿爪的4和10两半部分组成,左半部4用平键9与超越离合器的星形体5连接,右半部10与轴用花键连接。正常工作情况下,通过弹簧3的作用,使离合器左右两半部经常处于啮合状态,以传递由超越离合器星形体5传来的运动和转矩,并经花键传给轴。此时,安全离合器螺旋齿面上产生的轴向分力,由弹簧3平衡。当进给抗力过大或刀架移动受到阻碍时,通过安全离合器齿爪传递的转矩及产生的轴向分力将增大,当轴向分力大于弹簧3的作用力时,离合器的右半部10将压缩弹簧3而向右滑移,与左半部4脱开接合,安全离合器打滑,从而断开架的机动进给。过载现象排除后,弹簧3又将安全离合器自动接合,恢复正常的机动进给;调整螺母7,通过轴承内孔中的拉杆11及圆柱销2调整弹簧座12的轴向位置,可以改变弹簧3的压缩量,以调整安全离合器所传递的转矩大小。
3.1.9 超越离合器的结构
超越离合器的作用是实现同一轴运动的快、慢速自动转换。如图3-10中A—A剖面图所示,超越离合器由齿轮6(它作为离合器的外壳)、星形体5、3个滚柱8、顶销13和弹簧14组成。当刀架机动工作进给时,空套齿轮6为主动逆时针方向旋转,在弹簧14及顶销13的作用下,使滚柱8挤向楔缝,并依靠滚柱8与齿轮6内孔孔壁间的摩擦力带动星形体5随同齿轮6一起转动,再经安全离合器M7带动轴转动,实现机动进给。当快速电动机启动时,运动由齿轮副13/29传至轴ⅩⅩ,则星形体5由轴带动作逆时针方向的快速旋转,此时,在滚柱8与齿轮6及星形体5之间的摩擦力和惯性力的作用下,使滚柱8退缩,顶销移向楔缝的大端,从而脱开齿轮6与星形体5(即轴)间的传动联系,齿轮6并不再为轴ⅩⅩ传递运动,轴ⅩⅩ是由快速电动机带动作快速转动,刀架实现快速运动。当快速电动机停止转动时,在弹簧及顶销和摩擦力的作用下,使滚柱8又瞬间嵌入楔缝,并楔紧于齿轮6和星形体5之间,刀架立即恢复正常的工作进给运动。由此可见,超越离合器M6可实现轴快、慢速运动的自动转换。

图3-10 安全离合器和超越离合器的结构
1—蜗杆;2—圆柱销;3,14—弹簧;4—M7左半部;5—星形体;6—齿轮;7—螺母;8—滚柱;9—平键;10—M7右半部;11—拉杆;12—弹簧座;13—顶销
3.1.10 方刀架的结构
如图3-11所示,方刀架安装在小滑板上,用小滑板的圆柱凸台D定心。方刀架可转动间隔为90°的4个位置,使装在它四侧的4把车刀依次进入工作位置。每次转位后,定位销8插入刀架滑板上的定位孔中进行定位。方刀架每次转位过程中的松夹、拔销、转位、定位以及夹紧等动作,都由手柄16操纵。逆时针转动手柄16,使其从轴6顶端的螺纹向上退松,刀架体10便被松开。同时,手柄通过内花键套筒13(用骑缝螺钉与手柄连接)带动花键套筒15转动,花键套筒15的下端的端面齿与凸轮5上的端面齿啮合,因而凸轮也被带动着逆时针转动。凸轮转动时,先由其上的斜面a将定位销8从定位孔中拔出,接着凸轮的垂直侧面b与安装在刀架体中的固定销18相碰,于是带动刀架体10一起转动,钢球3从定位孔中滑出。当刀架转至所需位置时,钢球3在弹簧2作用下,进入另一定位孔中进行预定位。然后反向转动手柄16,同时凸轮5也被带动一起反转。当凸轮在斜面a退离定位销8的勾形尾部时,在弹簧的作用下,定位销8插入新的定位孔,使刀架实现精确定位。刀架被定位后,凸轮的另一垂直侧面c与固定销18相碰,凸轮便被固定销18挡住不再转动。于是,凸轮与花键套筒间的断面齿离合器便开始打滑,直至手柄16继续转动到夹紧刀架为止。修磨垫片12的厚度,可调整手柄16在夹紧方刀架后的正确位置。

图3-11 方刀架结构
1—小溜板;2,7,14—弹簧;3—钢球;4—定位套;5—凸轮;6—轴;8—定位销;9—定位套;10—刀架体;11—刀架上盖;12—垫片;13—内花键套筒;15—花键套筒;16—手柄;17—调节螺钉;18—固定销