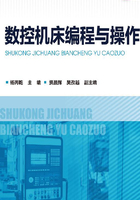
1.3 数控系统简介
数控系统(Numerical Control System)是数字控制系统的简称。它能根据计算机中存储的控制程序,实现机械设备的动作控制。
1.3.1 数控系统概述
(1)数控系统的组成
数控系统的种类繁多,形式各异,组成结构上也各有特点。然而无论哪种系统,它们的基本原理和构成是十分相似的。一般整个数控系统由三大部分组成,即控制系统、伺服系统和位置测量系统。
控制系统是一个具有输入输出功能的专用计算机系统,对加工程序进行插补运算,发出控制指令给伺服驱动系统;测量系统检测运动部件的具体运动位置、速度,并反馈到控制系统和伺服驱动系统,来修正控制指令;伺服驱动系统将来自控制系统的控制指令和测量系统的反馈信息进行比较和控制调节,控制脉冲宽度调制(Pulse Width Modulation,PWM)电流驱动伺服电动机,由伺服电动机驱动运动部件按要求运动。这三部分有机结合,就组成了完整的闭环控制数控系统。
(2)数控系统的硬件结构
控制系统硬件应具有人机交互功能,具有包括现场总线接口输入输出能力的专用计算机。伺服驱动系统主要包括伺服驱动装置和电动机。位置测量系统主要是采用长光栅或圆光栅的增量式位移编码器。
从硬件结构看,数控系统到目前为止可分为两个阶段共六代,第一阶段为数值逻辑控制阶段,其特征是不具有CPU,依靠数值逻辑实现数控所需的数值计算和逻辑控制,包括第一代是电子管数控系统,第二代是晶体管数控系统,第三代是集成电路数控系统;第二个阶段为计算机控制阶段,其特征是直接引入计算机控制,依靠软件计算完成数控的主要功能,包括第四代是小型计算机数控系统,第五代是微型计算机数控系统,第六代是PC数控系统。
从20世纪90年代开始,计算机应用普及推广,PC构架下计算机CPU及外围存储、显示、通信技术的高速进步,制造成本的大幅降低,导致PC构架数控系统日趋成为主流的数控系统结构体系。PC数控系统的发展,形成了“NC+PC”过渡型结构,即保留传统NC硬件结构,仅将PC作为人机接口(Human Machine Interface,HMI)。代表性的产品包括FANUC的160i、180i、310i,SIEMENS的840D等。还有一类是将数控功能集中用运动控制卡的形式实现,通过增扩NC控制板卡,如基于数字信号处理(Digital Signal Processing,DSP)的运动控制卡等,来发展PC数控系统。典型代表有美国DELTA TAU公司用多轴运动控制器(Programmable Multi-Axes Controller,PMAC)构造的PMAC-NC系统。另一种更加革命性的结构是全部采用PC平台的软硬件资源,仅增加伺服驱动及I/O设备通信所必需的现场总线接口,从而实现非常简洁的硬件体系结构。
(3)数控系统的软件结构
1)输入数据处理程序
它接收输入的零件加工程序,将标准代码表示的加工指令和数据进行译码、数据处理,并按规定的格式存放。有的系统还要进行补偿计算,或为插补运算和速度控制等进行预计算。通常,输入数据处理程序包括输入、译码和数据处理三项内容。
2)插补计算程序
CNC系统根据工件加工程序中提供的数据,如曲线的种类、起点、终点、既定速度等进行中间输出点的插值密化运算。上述密化计算不仅要严格遵循给定轨迹要求,还要符合机械系统平稳运动加减速的要求。根据运算结果,分别向各坐标轴发出形成进给运动的位置指令。这个过程称为插补运算。计算得到进给运动的位置指令通过CNC内或伺服系统内的位置闭环、速度环、电流环控制调节,输出电流驱动电动机带动工作台或刀具作相应的运动,完成程序规定的加工任务。
CNC系统是一边进行插补运算,一边进行加工,是一种典型的实时控制方式。
3)管理程序
管理程序负责对数据输入、数据处理、插补运算等为加工过程服务的各种程序进行调度管理。管理程序还要对面板命令、时钟信号、故障信号等引起的中断进行处理。在PC化的硬件结构下,管理程序通常在实时操作系统的支持下实现。
4)诊断程序
诊断程序的功能是在程序运行中及时发现系统的故障,并指出故障的类型。也可以在运行前或故障发生后,检查系统各主要部件(CPU、存储器、接口、开关、伺服系统等)的功能是否正常,并指出发生故障的部位。
(4)数控系统选型
数控系统的功能适用性,对于数控机床的设计选型无疑是重要的限制性因索。以下因素在选择数控系统时是必须考虑的重要因素。
1)驱动能力
不同的数控系统供应商,伺服系统的功率范围和配套电动机范围是不同的。首先应该从可匹配的电动机类型,功率范围来初步筛选。特别是要注意数控机床方案中是否包括力矩电动机、直线电动机、电主轴属于同步电主轴还是异步电主轴,上述电动机的额定电流需求和过载电流需求,电主轴的最高转速需求等。
2)全闭环需求与双驱需求
数控机床,特别是大型、重型数控机床,大多数都有全闭环和双驱需求。在全闭环控制方案中,要在距离编码光栅、绝对值式光栅、普通增量光栅间进行选择,同时数控系统也要支持相应的反馈信号接入。双驱动可以解决大型、重型机床由于刚性不足造成的双导轨副运动不同步误差。根据机床刚性情况,可以选择主从方式,即一边为主,一边跟随。这种方法控制十分简单;或选择交叉耦合,即动态跟踪双边的运动跟随误差,从而动态调整,但其参数调节较为复杂。
3)运动轴数与联动控制需求
数控车床属于2轴机床,加工中心有3、4、5轴之分。运动轴的数量直接影响机床的加工工艺范围;机床各轴是否需要联动控制,相应选择数控系统功能也不同。比如针对五面箱体类加工,通常不需要实时传输协议(Real-time Transport Protocol,RTP)和实时传输控制协议(RTP Control Protocol,RTCP)。同时针对5轴功能可能涉及数控系统供货商在出口许可证、售后服务、技术支持等方面的问题也必须认真考虑。
4)生产系统需求
数控系统网络化支持是生产系统集成的必要条件。对于要纳入自动化生产系统的数控机床,必须明确数控系统具有相应的接入解决方案,从采用低级的可编程控制器(Programmable Logic Controller,PLC)输入输出点直接接入,到采用高级的对象连接与嵌入(Object Linking and Embedding,OLE)内置服务器,依照OPC(OLE for Process Control)标准向用户开放数控系统内部数据。此外面向自动化生产系统,在线工件检测和刀具检测也是必须支持的功能。
1.3.2 常用数控系统
(1)FANUC数控系统
1)FANUC数控系统的特点
日本FANUC公司的数控系统具有高质量、高性能、全功能等特点,适用于各种机床和生产机械,在市场上的占有率远远超过其他的数控系统,其特点主要体现在以下几个方面。
①系统在设计中大量采用模块化结构。这种结构易于拆装,各个控制板高度集成,使可靠性有很大提高,而且便于维修、更换。
②具有很强的抵抗恶劣环境影响的能力。其工作环境温度为0~45℃,相对湿度达到75%。
③有较完善的保护措施。FANUC对自身的系统采用比较好的保护电路。
④FANUC系统所配置的系统软件具有比较齐全的基本功能和选项功能。对于一般的机床来说,基本功能完全能满足使用要求。
⑤提供大量丰富的PMC(Programmable Machine Controller)信号和PMC功能指令。这些丰富的信号和编程指令便于用户编制机床侧PMC控制程序,而且增加了编程的灵活性。
⑥具有很强的DNC功能。系统提供串行RS-232C传输接口,使通用计算机PC和机床之间的数据传输能方便、可靠地进行,从而实现高速的DNC操作。
⑦提供丰富的维修报警和诊断功能。FANUC维修手册为用户提供了大量的报警信息,并且以不同的类别进行分类。
2)FANUC数控系统的产品系列
FANUC系统早期有5系列和6系列系统,1984年之后,在6系统基础上研制出10/11/12系列,同时成功研制出具有数字伺服功能的0系列,而后又相继研发出15、16、18、21以及i系列等。而应用最广的是FANUC 0系列数控系统。FANUC数控系统的主要产品系列应用情况如下:
①高可靠性的Power Mate 0系列。用于控制2轴的小型车床,取代步进电动机的伺服系统;可配画面清晰、操作方便,中文显示的CRT/MDI,也可配性价比高的DPL/MDI。
②普及型CNC 0-D系列。其中0-TD用于车床,0-MD用于铣床及小型加工中心,0-GCD用于圆柱磨床,0-GSD用于平面磨床,0-PD用于冲床。
③全功能型的0-C系列。其中0-TC用于通用车床、自动车床,0-MC用于加工中心、铣床和钻床,0-GCC用于内、外圆磨床,0-GSC用于平面磨床,0-TTC用于双刀架4轴车床。
④高性价比的0i系列。该系列具有整体软件功能包,高速、高精度加工,并具有网络功能。0i-MB/MA用于4轴4联动的加工中心和铣床;0i-TB/TA用于4轴2联动车床;0i-Mate MA用于3轴3联动铣床;0i-Mate TA用于2轴2联动车床。
⑤具有网络功能的超小型、超薄型CNC 16i/18i/21i系列。控制单元与LCD集成于一体,具有网络功能和超高速串行数据通信。其中FS16i-MB的插补、位置检测和伺服控制以纳米为单位。16i最大可控8轴6联动;18i最大可控6轴4联动;21i最大可控4轴4联动。
除此之外,CNC 16/18/160/180系列可以满足机床的个性化定制。
(2)SIEMENS数控系统
西门子数控系统是西门子集团旗下自动化与驱动集团的产品,西门子数控系统SINUMERIK发展了很多代。目前在广泛使用的主要有802、810、840等几种类型。
1)SINUMERIK 802D
具有免维护性能的SINUMERIK 802D,其核心部件PCU(面板控制单元)将CNC、PLC、人机界面和通信等功能集成于一体。可靠性高、易于安装。
SINUMERIK 802D可控制4个进给轴和一个数字或模拟主轴。通过生产现场总线PROFIBUS将驱动器、输入输出模块连接起来。
模块化的驱动装置SIMODRIVE 611Ue配套1FK6系列伺服电动机,为机床提供了全数字化的动力。
通过视窗化的调试工具软件,可以便捷地设置驱动参数,并对驱动器的控制参数进行动态优化。
SINUMERIK 802D集成了内置PLC系统,对机床进行逻辑控制。采用标准的PLC的编程语言Micro/WIN进行控制逻辑设计。并且随机提供标准的PLC子程序库和实例程序,简化了制造厂设计过程,缩短了设计周期。
2)SINUMERIK 810D
在数字化控制领域中,SINUMERIK 810D第一次将CNC和驱动控制集成在一块板子上。快速的循环处理能力,使其在模块加工中独显威力。
SINUMERIK 810D NC软件选件的一系列突出优势可以帮助人们在竞争中脱颖而出。例如提前预测功能,可以在集成控制系统上实现快速控制。
另一个例子是坐标变换功能。固定点停止可以用来卡紧工件或定义简单参考点。模拟量控制控制模拟信号输出;刀具管理也是另一种功能强大的管理软件选件。
样条插补功能(A,B,C样条)用来产生平滑过渡;压缩功能用来压缩NC记录;多项式插补功能可以提高810D/810DE运行速度。
温度补偿功能保证数控系统在这种高技术、高速度运行状态下保持正常温度。
此外,系统还提供钻、铣、车等加工循环。
3)SINUMERIK 840D
SINUMERIK 840D数字NC系统用于各种复杂加工,它在复杂的系统平台上,通过系统设定而适于各种控制技术。
840D与SIMODRIVE 611数字驱动系统和SIMATIC7可编程控制器一起,构成全数字控制系统,它适于各种复杂加工任务的控制,具有优于其他系统的动态品质和控制精度。
(3)华中数控系统
华中“世纪星”系列数控系统以其质量好,性价比高,新产品开发周期短,系统维护方便,配套能力强,开放性好和便于用户二次开发及集成等优点,现已派生出了10多种系列30多个特种数控系统产品,广泛用于车、铣、加工中心、车铣复合、磨、锻、齿轮、仿形、激光加工、纺织机械、玻璃机械、医疗机械等设备,满足用户对低价格、高性能、简单、可靠数控系统的要求。