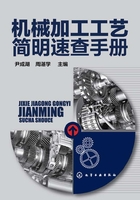
2.2 机械加工表面质量
机器零件的破坏,如磨损、疲劳断裂,一般都是从表面层开始的,这说明零件的表面质量对机器使用性能、使用寿命和产品质量有很大的影响,了解和掌握在机械加工中各种工艺因素对表面质量影响的规律,应用这些规律控制加工过程,达到保证和提高零件的表面加工质量。
2.2.1 表面加工质量的概念
零件的机械加工表面质量包括:加工表面的微观几何形状误差和表面层材料性能两个方面的质量。
(1)加工表面的几何形状误差
加工表面的微观几何形状误差包括表面粗糙度、波度、纹理方向和伤痕。
①表面粗糙度 表面粗糙度是加工表面的微观几何形状误差。其波长与波高的比值一般小于50。表面粗糙度高度参数按我国现行标准采用轮廓算术平均偏差Ra(μm)和微观不平度高度Rz(μm)评定。
②波度 波度是介于加工精度(宏观几何形状误差)和表面粗糙度(微观几何形状误差)之间的周期性几何形状误差,包括波长Lo与波高Hb两个主要参数。
波长与波高的比值在50~1000范围内的几何形状误差称为波度。它主要是加工过程中工艺系统的振动引起的。当波长与波高的比值大于1000时,称为宏观几何形状误差。例如,平面度误差、圆度误差、圆柱度误差等,它属于加工精度范畴。表面粗糙度、波度与宏观几何形状误差之间的相互关系如图2.2所示。

图2.2 零件加工的表面粗糙度与波度
③纹理方向 纹理方向是指表面刀纹的方向。它取决于表面形成过程所采用的机械加工方法。
④伤痕 伤痕是在加工表面的某些位置上出现的缺陷,例如砂眼、气孔、划痕、裂纹等。
(2)表面层金属材料性能方面的质量
表面层金属材料性能方面的质量,指机械加工后,零件一定深度表面层的物理力学性能等方面的质量与基体相比发生了变化,故又称加工变质层。它包括表面层金属的加工硬化、残余应力以及金相组织的变化。
①表面层金属的加工硬化 机械加工过程中表面层金属产生强烈的塑性变形,使晶格扭曲、畸变,晶粒间产生剪切滑移,晶粒被拉长,这些都会使工件已加工表面表层金属的硬度高于基体材料的硬度,这种现象称为加工硬化。加工硬化通常以表面层金属硬度H(GPa)、硬化层深度hc及硬化程度N表示。hc是已加工表面至未硬化处的垂直距离,单位为μm;N是已加工表面显微硬度H的增加值对原始基体材料的显微硬度H0比值的百分数,即

一般机械加工中,硬化层深度可达0.05~0.20mm。 若采用滚压加工,硬化层可达几毫米。
②表面层金属的残余应力 机械加工过程中由于切削力、切削热等因素的作用,在工件表面层材料中产生的内应力称为表面层残余应力。在铸、锻、焊、热处理等加工过程产生的内应力与这里介绍的表面残余应力的区别在于前者是在这个工件上平衡的应力,它的重新分布会引起工件变形;后者则是在加工表面材料中平衡的应力,它的重新分布不会引起工件变形,但它对机器零件表面质量有重要影响。
③表面层金相组织变化 机械加工过程中,在工件的加工区域温度会急剧升高,当温度升高到超过工件材料金相变化的临界点时就会发生金相组织变化。例如磨削淬火钢件时,常会出现回火烧伤、退火烧伤等金相组织的变化,将严重影响零件的使用性能。
2.2.2 影响机械加工表面粗糙度的因素及改善措施
(1)影响切削加工表面粗糙度的因素及改善措施(表2.4)
表2.4 影响切削加工表面粗糙度的因素及改善措施

(2)改善表面粗糙度的措施(表2.5)
表2.5 改善表面粗糙度的措施

(3)影响磨削表面粗糙度的因素及改善措施(表2.6)
表2.6 影响磨削表面粗糙度的因素及改善措施

2.2.3 典型表面粗糙度与加工精度和配合性质的关系
(1)轴的表面粗糙度与加工精度和配合的关系(表2.7)

(2)孔的表面粗糙度与加工精度和配合的关系(表2.8)

(3)动连接接合表面的粗糙度(表2.9)
表2.9 动连接①接合表面的粗糙度Ra μm

①动连接——密贴着移动的连接或两个表面彼此有相对位移的连接,当它们有相对移动和变位时,这种连接对部件和零件间的相互位置精度有要求。
(4)静连接接合表面的粗糙度(表2.10)
表2.10 静连接①接合表面的粗糙度

①静连接——用紧固件将零件的密贴面彼此接合在一起的连接。它要求装好的零件和部件具有一定的相互位置精度。
(5)丝杠传动接合表面的粗糙度(表2.11)
表2.11 丝杠传动接合表面的粗糙度

(6)螺纹连接的工作表面粗糙度(表2.12)
表2.12 螺纹连接的工作表面粗糙度Ra μm

2.2.4 加工硬化
(1)常用加工方法的冷硬程度及硬化层深度(表2.13)
表2.13 常用加工方法的冷硬程度及硬化层深度

①磨削用量大、冷却条件不好时,会发生淬火钢的回火转化,表层金属的显微硬度要降低,回火层的深度有时可达200μm。
(2)影响加工表面硬化的因素(表2.14)
表2.14 影响加工表面硬化的因素


2.2.5 残余应力
残余应力是指在没有外力作用的情况下,在物体内部保持平衡而存留的应力。残余应力有残余压应力(-σ)和残余拉应力(+σ)之分。影响残余应力的因素及减少残余应力的措施见表2.15。
表2.15 影响残余应力的因素及减少残余应力的措施

2.2.6 表面层材料的金相组织变化
加工表面温度超过相变温度时,表层金属的金相组织将会发生相变。切削加工时,切削热大部分被切屑带走,因此影响较小,多数情况下,表层金属的金相组织没有质的变化。磨削加工时,切除单位体积材料所需消耗的能量远大于切削加工。磨削加工所消耗的能量绝大部分要转化为热,磨削热传给工件,使加工表面层金属金相组织发生变化。
磨削淬火钢时,会产生三种不同类型的烧伤:
①回火烧伤 如果磨削区温度超过马氏体转变温度而未超过相变临界温度 (碳钢的相变温度为 723℃ ),这时工件表层金属的金相组织,由原来的马氏体转变为硬度较低的回火组织(索氏体和托氏体),这种烧伤称为回火烧伤。
②淬火烧伤 如果磨削区温度超过了相变温度,在切削液急冷作用下,使表层金属发生二次淬火,硬度高于原来的回火马氏体,里层金属则由于冷却速度慢,出现了硬度比原先回火马氏体低的回火组织,这种烧伤称为淬火烧伤。
③退火烧伤 若工件表层温度超过相变温度,而磨削区又没有冷却液进入,表层金属产生退火组织,硬度急剧下降,称为退火烧伤。
磨削烧伤严重影响零件的使用性能,必须采取措施加以控制。控制磨削烧伤有两个途径;一是尽可能减少磨削热的产生;二是改善冷却条件,尽量减少传入工件的热量。采用硬度稍软的砂轮,适当减小磨削深度和磨削速度,适当增加工件的回转速度和轴向进给量,采用高速冷却方式(如高压大流量冷却、喷雾冷却、内冷却)等措施,都可以降低磨削区温度,防止磨削烧伤。