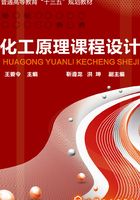
3.1 概述
精馏过程是利用各组分挥发度的差异,借助于“回流”技术,使混合液多次连续进行部分汽化和部分冷凝的过程。实现精馏操作的主体设备是精馏塔。
精馏塔是石油工业、化学工业等生产领域当中最重要的设备之一。它可使两相流体之间进行充分的接触,达到相际间传质和传热的目的。精馏塔性能的好坏,关乎整个装置系统的产品质量、产量和单位产品能耗指标。塔设备在炼油装置中的投资费用占整个工艺设备投资费用的一半左右,在化工行业中占25%左右。因此,塔设备的设计和研究,受到炼油、化工及轻化工等行业的高度重视。
随着石油工业、化学工业及其他工业的发展,众多研究者研制出了许多结构新颖的塔设备内件。为了便于研究和比较,人们也从不同的角度对塔设备进行分类。例如,按操作压力分为加压塔、常压塔和减压塔;按单元操作分为精馏塔、吸收塔、解吸塔、干燥塔、反应塔和萃取塔等。但是最常用的分类方式是按塔设备的内部结构分为板式塔和填料塔两大类。精馏操作既可以采用板式塔,也可以采用填料塔。在塔设备内部,气相靠压差作用自下而上流动,而液相则靠自身的重力作用自上而下流动,汽液两相做逆流流动。两相之间进行充分接触,其接触界面由塔内塔板或填料提供。前者称为板式塔,后者称为填料塔。
早在1813年Cellier首次提出泡罩塔结构至今,板式塔已广泛应用于工业生产,是使用量最大、应用范围最广的汽液传质设备。板式塔为逐级接触式的汽液传质设备,两相的组分浓度沿塔高呈阶梯式变化。
板式塔结构形式多种多样,依据塔板上汽液两相接触元件的不同,可分为泡罩塔、筛板塔、浮阀塔等结构形式。随着炼油工业、化学工业的迅速发展,相继出现了大批结构新颖的高效新型塔板,如浮动喷射塔板、穿流式波纹塔板和新型垂直筛板等。表3-1给出了各种板式塔型所占比例。
表3-1 板式塔型使用比例

3.1.1 泡罩塔
泡罩塔是工业上最早使用的板式塔,自Cellier提出泡罩塔板结构以来,它在工业上的应用已有近两百年的历史。近数十年来由于塔设备的更新发展,不少新型的塔板结构取代了泡罩塔,但在许多场合仍然使用。泡罩塔盘的主要结构包括泡罩、升气管、溢流管和降液管。泡罩塔盘结构如图3-2所示。

图3-2 泡罩塔盘结构示意图
泡罩安装在升气管的顶部。泡罩的种类很多,目前应用最为广泛的是圆形泡罩,常用的泡罩已经标准化。泡罩尺寸有Φ80mm、Φ100mm、Φ150mm三种,可根据塔径的大小选择。泡罩的下部周边开有许多齿缝,齿缝一般有三角形、矩形或梯形。泡罩在塔板上呈正三角形排列。
在泡罩塔的操作过程中,塔盘上的汽液接触状况是液体由上层塔盘通过降液管流入下层塔盘,然后横向流过塔盘上布置泡罩的区域,溢流堰保持板上有一定厚度的液层,上升气体通过齿缝进入液层时,与塔板上的液层进行汽液接触形成鼓泡层和泡沫层,从而达到汽液相传质、传热的目的。升气管的顶部应略高于泡罩齿缝的上沿,以阻止液体从升气管流下。
泡罩塔的优点是操作弹性大,在负荷变化范围较大时仍能保持较高的分离效率,无泄漏,不易堵塞,能适应多种介质,液气比的范围大。其缺点是塔板结构复杂,造价高,维修麻烦,压降大。
3.1.2 筛板塔
筛板塔也是很早出现的一种板式塔,其塔盘结构如图3-3所示。

图3-3 筛板塔盘上汽液接触状况示意图
20世纪50年代以前,工业上采用的板式塔大多数是泡罩塔,筛板塔则被认为操作范围过于狭窄,长期不受重视。随着石油化学工业的发展,生产规模逐渐扩大,泡罩塔在结构、成本方面的缺陷成为一个突出问题。此后,研究人员对筛板塔做了大量工业规模的研究,逐渐掌握了筛板塔的性能,并形成了较完善的设计方法。与泡罩塔相比,筛板塔结构相对简单,投资成本较低,生产能力提高20%左右,并且只要设计合理,筛板塔可以得到不低于泡罩塔的操作范围。
筛板上开有许多均匀分布的小孔,孔径一般为3~8mm,筛孔在塔板上呈正三角形分布。国内外众多研究机构均研究过大孔径筛板,有用19mm、25mm,甚至有用50mm孔径的筛板,这种筛板能防止筛孔的堵塞,能适应更广泛的物系,还可以考虑使用非金属制造筛板。
与泡罩塔的操作类似,液体从上一层塔板经降液管流下,横向流过塔板,然后流入下一层塔板;气体经筛孔分散成小股气流,自下而上鼓泡通过塔板上的液层,汽液两相间进行密切接触,从而进行传质和传热。正常操作状态下,经过筛孔上升的气流应能阻止液体经筛孔向下泄漏。
溢流堰能够使筛板上维持一定厚度的液层。近几十年来,为了更好地发挥筛板塔结构简单的优点,有人对无溢流筛板进行了研究,取得了可观的成果。只是由于没有溢流,设计自由度小,要求设计方法更加可靠。为了消除普通筛板的气体死区,有人研制了林德筛板,这种筛板在塔板上开有蒸汽导向孔,并在液流入口处使塔板翘起,制造有利于鼓泡的条件,该类型塔板特别适用于真空精馏。为了克服普通筛板因液流路径较长,泡沫层较高的缺点,有人提出了多降液管筛板,以适应高液体负荷的操作状况。该类型的塔板在同一个筛板上布置几个降液管,缩短了液流路径,增大了液体处理量,增加了塔板的有效面积。
近年来,随着计算机及数值计算的发展,计算流体力学为研究塔板上的两相流体传质与传热微观机理及流场分布情况虚拟可视化提供了有力的工具,从而避免了大量的塔板流场实际测量工作。
3.1.3 浮阀塔
浮阀塔是在泡罩塔和筛板塔的基础上发展起来的,它吸收了两种塔板的优点。浮阀塔板是在塔盘上开许多阀孔,每个阀孔安置一个能上、下浮动的阀件。阀腿与定距片限制了阀件所能上升与下降的空间距离。由于浮阀塔板的气体流通面积能随气体负荷变动自动调节,因而操作负荷范围较大,具有良好的操作弹性和较高的塔板效率。
与泡罩塔的操作类似,通过阀孔上升的气体,流经阀片与塔板间隙沿水平方向进入液层,这种接触方式汽液接触时间较长,雾沫夹带少。浮阀的开度随着气体流量的变化而变化,在气体流量小时,开度较小,气体仍能以足够的气速通过缝隙鼓泡,避免过多的泄漏;在气体流量大时,阀片上浮,开度增大,使气速不至于过大。有数据表明,浮阀塔在接近于阀全开时的操作状态下传质、传热效果最好。
浮阀塔有诸多优点:首先,它的处理能力大,浮阀在塔盘上可以布置得更加紧凑,其处理能力相对于泡罩塔可提高20%~40%;其次,由于浮阀可以随着气量的变化而升降,操作弹性较大;另外,由于气体以水平方向吹入液层,汽液接触状况良好,塔板效率高。其缺点是处理易结焦、高黏度的流体时,阀片易与塔板黏结,在操作过程中有时会发生阀片脱落或卡死等现象,使塔板效率或操作弹性下降。
阀片的结构形式很多,国内常用的有F1型、V4型和T型等,其结构如图3-4所示。

图3-4 几种浮阀结构图
由于浮阀塔具有处理能力大,操作弹性大及塔板效率高等优点,有关浮阀塔板的研究是目前新型塔板研究与开发的主要方向。近年来开发的新型浮阀有导向筛孔浮阀、单侧浮动整流浮阀、斜喷浮阀、船形浮阀、十字旋阀、方形浮阀、椭圆形浮阀、微分固定浮阀板等,它们显著的优点是具有明显的流体导向作用,使操作弹性与塔板效率得到更进一步的提高。
常用的三种塔的典型性能比较见表3-2中。
表3-2 常用的三种塔的典型性能比较

3.1.4 舌形塔及浮动舌形塔
舌形塔是喷射型塔,自20世纪60年代开始应用于工业生产,其结构如图3-5所示。

图3-5 舌形塔板结构图
它是在塔板上开有许多舌形孔,向塔板液流出口侧张开。舌片与板片成一定角度,以20°左右为宜。舌片尺寸有50mm×50mm和25mm×25mm两种。一般推荐使用25mm×25mm的舌片。舌孔呈正三角形排列。塔板液流出口侧不留溢流堰,只保留降液管。要求降液管截面积设计得比一般的塔板大些,以便有效地将夹带的液沫分离出来。
当操作气速较低时,液体从舌孔直接漏下,随着气速的提高,液漏停止。当气速升至20~30m/s时,汽液接触从鼓泡状态逐渐发展为喷射状态。若气速过高,可能造成液泛。
舌形塔的优点是生产能力大,塔板压降低,传质传热效率高;缺点是操作弹性小,被气体喷射的液体在通过降液管时,会夹带气泡到下一层塔板,降低塔板效率。
浮动舌形塔与舌形塔相比,其舌片可上下浮动,它综合了浮阀塔及固定舌形塔的结构特点,因此,既有舌形塔的大处理量、低压降等优点,又有浮阀塔的操作弹性大、效率高等优点。特别适用于热敏性物系的减压分离过程。其结构如图3-6所示。

图3-6 浮动舌形塔盘结构示意图