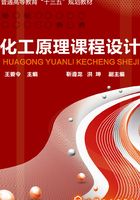
2.4 典型化工单元的自控流程
2.4.1 流体输送设备的自动控制
(1)离心泵的自动控制方案
离心泵流量控制的目的是要将泵的排出流量恒定于某一给定的数值上。流量控制在化工厂中是常见的,例如,进入化学反应器的原料量需要维持恒定,精馏塔的进料量或回流量需要维持恒定等。
离心泵的流量控制大体有控制泵出口阀开度、控制泵的转速和控制泵的出口旁路三种方法。
①控制泵出口阀门开度 通过控制泵出口阀门开度来控制流量的方法如图2-23所示。当干扰作用使被控变量(流量)发生变化偏离给定值时,控制器发出控制信号,阀门动作,控制结果将使流量回到给定值。

图2-23 离心泵的出口阀门开度调节流量
采用该方案时,要注意控制阀一般应该装在泵的出口管线上,而不应该装在泵的吸入管线上。控制泵出口阀门开度的方案简单可行,是应用最为广泛的方案。但是,此方案总的机械效率较低,特别是控制阀开度较小时,阀上压降较大,对于大功率的泵,损耗的功率就相当大,因此是不经济的。
②控制泵的转速 改变泵的转速调节流量是指当泵的转速改变时,泵的流量特性曲线发生了改变,从而达到调节流量的目的。
此方案节约能量,机械效率较高,但驱动机械及其调速设施投资较高,一般只适用于较大功率的机泵。
③控制泵的出口旁路 旁路调节是将泵的部分排出量重新送回到吸入管路,用改变旁路阀开度的方法来控制泵的实际排出量,如图2-24所示。

图2-24 离心泵的旁路调节流量
(2)往复泵的自动控制方案
①改变原动机的转速 这种方案适用于以蒸汽机或汽轮机作原动机的场合,此时,可借助于改变蒸汽流量的方法方便地控制转速,如图2-25所示。当用电动机作原动机时,由于调速机构复杂,较少采用。

图2-25 改变原动机转速的控制方案
②改变旁路阀开度 如图2-26所示,用改变旁路阀开度的方法来控制实际排出量。

图2-26 改变旁路阀开度的控制方案
③改变冲程 计量泵常用改变冲程来进行流量控制。冲程的调整可在停泵时进行,也有在运转状态下进行的。
往复泵的出口管道上不允许安装控制阀,这是因为往复泵活塞往复一次,总有一定体积的流体排出,当在出口管线上节流时,压头会大幅度增加。改变出口管路阻力既达不到控制流量的目的,又极易破坏泵体。
(3)真空泵的自动控制方案
使用真空泵时,可采用吸入支管调节和吸入管阻力调节的方案来控制真空系统的真空度,如图2-27所示。当用蒸汽喷射泵抽真空时,真空度还可用调节蒸汽量的方法来控制,如图2-28所示。

图2-27 真空泵流量控制方案(一)

图2-28 真空泵流量控制方案(二)
(4)离心压缩机的自动控制方案
离心压缩机常用的流量调节方法有入口流量调节旁路阀,改变进口导向叶片的角度和改变压缩机的转速等。
改变转速法是一种最为节能的方法。由于调节转速有一定的限度,因此需要设置放空设施。压缩机的进口压力调节一般可采用在压缩机进口前设置一缓冲罐,从出口端引出一部分介质返回缓冲罐以调节缓冲罐的压力,如图2-29所示。

图2-29 压缩机进口压力调节原理图
2.4.2 传热设备的自动控制
在化工生产过程中,传热设备的种类很多,主要有换热器、蒸汽加热器、再沸器、冷凝器和加热炉等。由于传热的目的不同,被控变量也不完全一样。在多数情况下,被控变量是温度,本节仅讨论温度为被控变量时的各种控制方案。
(1)两侧均无相变化的换热器控制方案
当换热器两侧流体均无相变时,可以通过改变换热器的热负荷来保证工艺介质温度在换热器出口处恒定的给定值上。控制方案的实施可采用调节载热体的流量、调节载热体旁路流量、调节被加热流体自身流量及调节被加热流体自身流量的旁路几种方法来实现。
①控制载热体流量 图2-30是利用控制载热体的流量来稳定被加热介质出口温度的控制方案。此方案适用于载热体流量的变化对温度影响敏感的场合。若载热体的压力不稳定,可另设稳压系统,或者采用以温度为主变量、流量为副变量的串级控制系统,如图2-31所示。

图2-30 改变载热体的流量控制温度

图2-31 换热器串级控制系统
②控制载热体旁路 当载热体是工艺流体,其流量不允许变动时,可采用图2-32所示的控制方案。该方法采用三通控制阀来改变进入换热器的载热体流量及其旁路流量的比例,这样既可控制进入换热器的载热体流量,又可保证载热体总流量不受影响。

图2-32 载热体旁路控制温度方案
③控制被加热流体自身流量 如图2-33所示,当工艺介质的流量允许变化时,可采用将控制阀安装在被加热流体进入换热器管道上的控制方案。

图2-33 用被加热流体自身流量控制温度
④控制被加热流体自身流量的旁路 当被加热流体的总流量不允许变化,且换热器的传热面积有余量时,可将一小部分被加热流体由旁路直接流到出口处,使冷热物料混合来控制温度,如图2-34所示。如果换热器的被加热介质流量较小时,采用此方案则不太经济。

图2-34 用介质旁路控制温度
(2)载热体进行冷凝的加热器自动控制
利用蒸汽冷凝的加热器,不同于两侧均无相变化的传热过程。蒸汽在整个冷凝过程中温度保持不变,直到蒸汽将所有冷凝潜热释放完毕为止,若还需继续换热,凝液才进一步降温。因此这种传热过程分两段进行,先冷凝后降温。当以被加热介质的出口温度为被控变量时,常采用控制进入的蒸汽流量和改变换热器的有效传热面积的控制方案。
①控制蒸汽流量 当蒸汽压力稳定时,常采用如图2-35所示的控制方案。通过改变加热蒸汽量来稳定被加热介质的出口温度。当阀前蒸汽压力有波动时,可对蒸汽总管加设压力控制,或者采用温度与流量(或压力)的串级控制。

图2-35 用蒸汽流量控制温度
此方案简单易行,控制迅速,但需要较大的蒸汽阀门,传热量变化比较剧烈,影响均匀传热。
②控制换热器的有效换热面积 如图2-36所示,将控制阀安装在冷凝液管道上。如果被加热物料温度高于给定值,说明传热量过大,可将冷凝液控制阀关小,冷凝液就会积聚起来,减少了有效的蒸汽冷凝面积,使传热量减少,工艺介质出口温度就会降低。反之,可开大冷凝液控制阀,增大传热面积,使传热量增大。

图2-36 用凝液排出量控制温度
此方案调节通道长,控制比较迟钝,且需要较大的传热面积裕量,但变化缓和,可防止局部过热。
(3)冷却剂进行汽化的冷却器自动控制
当用水或空气作为冷却剂不能满足冷却温度的要求时,需要用液氨、乙烯、丙烯等其他冷却剂。这些液体冷却剂在冷却器中由液体汽化为气体时带走大量潜热,从而使另一种物料得到冷却。
以液氨为例,下面介绍几种控制方案。
①控制冷却剂的流量 如图2-37所示,通过改变液氨的进入量来控制介质的出口温度。但要注意,此方案不以液位为控制变量,液位过高会造成蒸发空间不足,引起氨压缩机的操作事故。所以这种控制方案往往带有上限液位报警,或采用温度-液位自动选择性控制。

图2-37 用冷却剂流量控制温度
②温度与液位的串级控制 如图2-38所示,被控变量仍然是液氨流量,但以液位作为副变量,以温度作为主变量构成串级控制系统。这种方案可以限制液位的上限,保证足够的蒸发空间。

图2-38 温度-液位串级控制
③控制汽化压力 由于氨的汽化温度与压力有关,所以可将控制阀装在气氨出口管道上,阀门开度改变时,引起氨冷器内的汽化压力改变,相应的汽化温度也改变了,如图2-39所示。

图2-39 用汽化压力控制温度
2.4.3 精馏塔的自动控制
在精馏操作中,被控变量多,可选用的操纵变量也多,所以控制方案繁多。本节只选择具有代表性的、常见的以压力、温度及进料量为控制变量的控制方案。
(1)塔顶压力控制
①常压精馏塔 对于精馏操作压力恒定要求不高的情况,常压精馏不需要压力调节系统,仅需要在蒸馏设备上设置一个通大气的管道来平衡压力,使之维持在大气压力。
②真空精馏塔
a.改变不凝性气体的抽吸量,如图2-40所示。

图2-40 改变不凝气抽吸量控制塔压
b.改变旁路吸收空气或惰性气体量。在回流罐至真空泵的吸入管上,连接一根通大气或某种惰性气体旁路,并在该旁路上安装一调节阀,通过改变经旁路管吸入的空气量或惰性气体量,即可控制塔的真空度,如图2-41所示。

图2-41 改变旁路吸入空气或惰性气体量控制塔压
③加压精馏塔
a.塔顶气相馏出物不冷凝。该流程很少使用,压力调节阀可设置在塔顶气相管线上,如图2-42所示。

图2-42 塔顶气相馏出物不冷凝的塔压控制
b.塔顶馏出物部分冷凝。通常采用压力调节器调节气相馏出物,气相流量变化对压力影响敏感,效果较好,如图2-43所示。

图2-43 塔顶馏出物部分冷凝的塔压控制
c.塔顶馏出物含微量不凝气体。
ⅰ.调节冷却水流量。调节冷却水量以改变气体在冷凝器中冷凝的速度从而调节塔压,如图2-44所示。该方案操作费用低,调节阀可不考虑介质腐蚀。但塔顶温度过高时,可能使冷凝器水出口温度过高而加速冷凝器的腐蚀和结垢。

图2-44 冷却剂流量控制塔压
ⅱ.热气体旁通法控制塔压。如图2-45所示,此法调节系统滞后小,调节阀尺寸小,便于维修,但冷却水耗量大。

图2-45 热气体旁通法控制塔压
d.塔顶馏出物种含少量不凝性气体。当塔顶气相中不凝性气体含量小于塔顶气相总量的2%时,或在塔的操作中预计只在部分时间里产生不凝性气体时,不能采用将不凝性气体放空的方法控制塔压。这样会把未冷凝下来的产品排放掉。此时可采用如图2-46所示的分程控制方案对塔压进行控制。首先用冷却水调节阀控制塔压,若冷却水阀全开塔压还降不下来时,再打开放空阀,以维持塔压的恒定。

图2-46 分程控制方案控制塔压
e.馏出物中有较多不凝性气体。当塔顶馏出物中含有不凝性气体较多时,塔压控制可以通过改变回流罐的气相排放量来实现,如图2-47所示。

图2-47 改变回流罐的气相排放量控制塔压
该方案适用于进料流量、组分、塔釜加热蒸汽压力波动不大,且塔顶蒸气经冷凝的阻力变化也不大的情况。
(2)精馏塔的温度控制
①精馏段的温度控制 如果采用以精馏段温度作为衡量质量指标的间接变量,而以改变回流量作为控制手段的方案,称为精馏段温控。
如图2-48所示是一种常见的精馏段温度控制方案,其主要控制系统是以精馏段塔板温度为被控变量,而以回流量为操纵变量。

图2-48 精馏段温度控制的控制方案
精馏段温控的主要特点及适用场合如下。
a.由于采用了精馏段温度作为间接质量指标,因此,它能较直接地反映精馏段的产品情况,当塔顶产品纯度要求比塔底严格时,宜采用精馏段温控方案。
b.如果干扰首先进入精馏段,例如,气相进料时,由于进料量的变化首先影响塔顶的成分,所以采用精馏段温控就比较及时。
②提馏段的温度控制 如果采用以提馏段温度作为衡量质量指标的间接变量,而以改变加热量作为控制手段的方案,称为提馏段温控。
图2-49是最常见的一种提馏段温控方案。这种方案控制系统是以提馏段塔板温度为被控变量,加热蒸汽量为操纵变量。

图2-49 提馏段温度控制的控制方案
提馏段温控的主要特点及适用场合如下。
a.由于采用了提馏段温度作为间接质量指标,因此,它能较直接地反映提馏段产品情况;将提馏段温度恒定后,能较好地保证塔底产品的质量,所以,在以塔底采出为主要产品,对塔釜成分要求比馏出液高时,常采用提馏段温控方案。
b.当干扰首先进入提馏段时,例如,在液相进料时,进料量或进料成分的变化首先要影响塔底的成分,采用提馏段温控比较及时,动态过程也比较快。
③精馏塔的温差控制 以上两种方案都是以温度作为被控变量,这在一般的精馏塔中是可行的。但是在精密精馏时,产品纯度要求很高,而且塔顶、塔底产品的沸点差又不大时,应当采用温差控制,以进一步提高产品的质量。
如图2-50所示是双温差控制系统图,双温差控制是分别在精馏段与提馏段上选取温差信号,然后将两个温差信号相减,作为控制器的测量信号。双温差法是一种控制精馏塔进料板附近的组成分布,使其产品质量合格的办法。

图2-50 双温差控制系统图
(3)精馏塔的流量控制
精馏操作中进料量的波动直接影响分离效果,最终影响到产品的质量。然而进料量的波动是难以避免的,多数情况下精馏塔的处理量是由上一工序所决定,为了缓和上、下工序之间的冲突,上一工序可以采用液位均匀调节系统来出料,以使进塔流量的变动不至于过于剧烈。若塔的进料来自一个很大的中间储槽或原料罐,可以设置流量定制调节系统来恒定进料流量。采用的调节方案可根据选用泵的类型决定。
回流量的调节可根据使用的泵的形式决定。采用重力回流时,调节方法如图2-51所示。

图2-51 全凝器的回流量控制