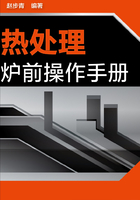
1.4 钢件在真空中的加热
真正的真空是不存在的。可以说,真空也是一种气氛,事实上,比大气压小的空间习惯上统称为真空。将工件置于正常大气压以下的负压空间加热和保温,称为真空加热。负压的程度用真空度Torr(1Torr≈1mmHg=1.33322×102Pa)或Pa来表示,根据真空度的高低,将其划分为4个等级:
低真空——105~102Pa;
中真空——102~10-1Pa;
高真空——10-1~10-5Pa;
超高真空——小于10-5Pa。
目前真空炉的真空度大多为103~10-4Pa。工件在真空炉中加热时,在真空装置中除残存的空气外,还有很多气体来源,如工件内放出的气体、装置内壁吸附的气体、炉衬材料内放出的气体以及向装置内渗漏的气体,所以必须用真空泵进行排气,以保证所要求的真空度。
真空度越高,气体的压力越低,炉内气体分子数量越少,杂质量也就越少。如果把相对杂质量全部看成是水蒸气,则真空度与相对露点的关系如表1-17所示。
表1-17 真空度与相对露点的关系

从表中数据可知,1Pa真空气氛下的相对露点低于-60℃,即相当于99.999%的高纯氮气或氩气。若使用惰性气体作金属保护加热气体,则将杂质含量降低到这一纯度时,必须经过昂贵而又复杂的精制过程,而1Pa的真空度是很容易实现的。另外,在采用普通保护的无氧化加热中,所控制的露点一般在-30~-60℃范围内,与其相对应的真空度为13~1Pa。这一真空度是极易达到的,通过对比可以看出,真空加热比可控气氛加热具有明显的优越性。
1.4.1 真空热处理技术特点
钢铁制品在真空炉中加热时,除可避免氧化烧损,得到光亮的表面质量外,还有脱脂、除气、表面氧化物分解以及合金元素蒸发等效应。
(1)加热速度缓慢 在真空中气体分子稀薄,气体分子的平均自由能随着压力的下降显著增加,工件的加热将主要依靠辐射传热的方式进行。由于对流传热作用很小,靠近发热体一侧的工件升温速度比较快,因此,在工件的装炉方式与炉型结构配制上应尽量避免“背影”部分,或适当延长加热保温时间,以保证加热均匀些。
在真空中的加热速度比在盐浴炉中加热慢得多,初步估算约6:1。特别是在炉温600℃以下加热,辐射传热作用很弱,在极稀薄的气氛中加热,依靠对流传热需要很长时间,而且不易均匀。因此,在真空炉中回火往往需要充入惰性气体,并进行强制循环,鉴于此,有些单位用真空淬火,硝盐回火或空气炉回火。
有人曾对GCr15钢试样在不同介质中的加热速度进行测定,试样心部加热到850℃所需要的时间分别是:盐浴炉8min,空气炉35min,真空炉50min,亦即工件在真空炉中的透热时间为盐浴炉的6倍,空气炉的1.5倍。
(2)氧化作用被抑制 为了实现无氧化加热的光亮淬火,可以选择可控气氛,但对于工模钢来说,在高温加热的情况下,在一般的可控气氛中完全保持中性状态是很困难的。尽管采用高纯度的惰性气体和低露点的可控气氛可以达到上述要求,但成本昂贵,不宜采用。而采用真空加热,因氧化气氛的含量极低,可使钢避免氧化和脱碳。在一定的温度下,金属(M)与其氧化物(MxO)间存在下列反应:
若炉内氧的分解压力低于氧化物的分解压力,则反应向左进行,也就意味着不发生氧化作用。实践证明,只要炉内氧的分解压达到10-1~10-3Pa,工具钢可以免遭氧化之灾,实现光亮淬火。
(3)表面净化 金属的氧化物在普通加热时发生氧化,即(M代表金属)。普通加热时氧的分压(pO2)总是大于氧化物的平衡分解压,而在真空状态下,pO2可以小于氧化物的平衡分解压,使氧化物发生分解,即
。生成的氧气由真空泵抽出,氧化物(氧化皮)中的氧不断被排除,即得到光亮的表面。各种氧化物的平衡分解压如图1-32所示。

图1-32 各种氧化物的平衡分解压
在实际生产中,尽管炉内氧的分解压比金属氧化物的分解压要高得多,却仍然能很好地去除氧化物而得到光净的表面,所以有人认为,这种现象可能是由于在高温和真空下,金属氧化物转变为蒸发压高的不稳定的氧化物而升华,从而使表面净化。也有人认为,由于真空炉内石墨纤维加热元件的蒸发和一些油蒸气的混入,使真空室内存在着一定数量的碳原子,它们将与残存气体中的氧作用,使实际的氧分压大大降低,以致炉内气体变成还原性而使表面净化。
工件表面的油脂在真空下加热可以分解成氢、二氧化碳和水蒸气,并在抽气过程中排出,这种现象称为脱脂。无论是脱去氧化皮还是脱脂,都使得工件表面得以净化。洁净的工件表面不仅美观,而且对提高耐磨性和疲劳强度都有益处。
(4)脱气作用 在常压下溶入金属的气体,如氢、氧、氮等,在负压时从金属内部向表面扩散而逸出,这种现象称为脱气。根据热力学原理,H2、O2和N2等双原子气体在金属中的溶解度S与其分压p的平方根成正比,即:(K为常数)。
由此可见,在真空下随气体分压的降低,气体在金属中的溶解度将减少,也就是说,真空度越高,脱气效果越好。脱气过程是:
①金属中的气体向表面扩散;
②气体从金属表面逸出;
③气体不断被抽出排除。
表面气体向外逸出时在工件表面形成的浓度梯度是气体不断由内向外排出的主要原因。根据扩散系数与温度间所呈的指数关系,升温温度扩散系数(D)显著增加,从而使脱气速度大为加速。扩散系数受温度的影响极大,在相同的真空度下,提高温度就能提高脱气效果。
真空加热时,氢气的脱气效果最为明显,因为氢在钢中易扩散。而氧、氮与氢相比,在钢中的扩散比较困难,一般在900℃以上才能进行。
(5)合金元素的蒸发 在真空中加热时,当炉内的压力比钢中的某些合金元素的蒸发压低时,这些合金元素会从金属的表面逸出,称为脱元现象。在钢中的各种合金元素中,以Mn、Cr的蒸气压最高,真空中加热时,它们最容易挥发。铬在真空中不同温度下的蒸发见图1-33,各种金属在不同温度下的蒸气压见图1-34。从图1-34可以看出,温度越高,合金元素的蒸发压越高,因此,在一定的真空度下就越容易蒸发。合金元素在钢表面蒸发的结果,使钢件表面的物理化学性质发生了变化,以致影响工件的质量,严重时还使工件之间或工件与料筐之间互相黏结。金属蒸发物附着或沉积在炉内结构上,会影响炉子的电气绝缘性能,甚至会引起短路。

图1-33 铬在真空中不同温度下的蒸发

图1-34 各种金属在不同温度下的蒸气压
1atm=101325Pa,下同
为了避免这类现象的发生,必须根据具体情况适当控制炉内的真空度,或先抽成高真空度,随后通入高纯度的惰性气体(或氮),将真空度降低,从而防止钢中元素的蒸发。
在确定真空度时要兼顾两方面的因素:要防止氧化脱碳所需的最小真空度和为避免合金元素蒸发所允许的最大真空度。
真空加热时的注意事项有以下几个方面。
①为达到工具的无氧化加热,加热温度越高,所需的真空度越低。真空回火时的真空度要比淬火时的真空度高,才能得到光亮的金属表面。
②对高铬、高锰合金钢,在850℃以上加热,工作真空度在13.3Pa即可实现无氧化加热,真空度无需太高,以减少合金元素的蒸发。
③在高温高真空条件下加热,加热温度高于1250℃、真空度在1.3×10-2Pa以上时,某些绝缘材料的还原作用(如SiO2还原成Si)有破坏绝缘性能的危险,应当予以注意。
真空炉加热有两个最显著的特征:一是空载时升温速度快,二是工件的加热速度慢。由于真空炉加热室的保温层采用重量轻、隔热性能好、热容量小的隔热材料,如石墨毡或经抛光的多层钼片、不锈钢钢板材料,通常,真空炉功率损耗仅为1/4~1/3。真空炉空载时升温的速度相当快,从室温全功率升温到1320℃,一般约需30min。
工件在真空炉中加热时,加热速率低,升温时间长,尤其是在低温预热阶段(<700℃),工件表面与炉膛温差大。工件尺寸越大,温度滞后就越显著。
1.4.2 真空热处理加热工艺参数的设定
真空热处理比盐浴加热工艺系数要复杂些,制订热处理工艺时应考虑全面,几个主要的工艺参数应确定好。
1.4.2.1 真空度
真空热处理时,工作真空度要根据所处理的工件材料和加热温度来选择,首先要满足无氧化加热所需的工作真空度,再综合考虑表面光亮度、除气和合金元素蒸发等因素,常用工具钢推荐的真空度见表1-18。
表1-18 常用工具钢在真空热处理时推荐的真空度

在选择真空度时应注意以下几点。
①加热温度≥1000℃的高合金工模钢工件,在加热到900℃以前,应先抽高真空,以达到脱气的效果,随后充入高纯氮气,在一定的分压下继续升温至奥氏体化温度。
②凡加热温度在900℃以下的低合金工具钢,真空度越高,脱气效果越好,最好低于0.1Pa。
③真空度高低对钢的表面光亮度有直接的影响。在不影响合金元素挥发的前提下,真空度越高,则炉气中残存的氧和水蒸气的含量越少,工件不易产生氧化,表面的光亮度也越好。
④一般黑色金属在10-1Pa进行淬火加热,相当于在1×10-6以上纯度的惰性气氛中加热的保护气氛效果,工件表面不会氧化。
⑤工件在充入氮气和氢气的混合气氛中进行加热时,如充至133Pa[φ(N2)50%+φ(H2)50%,此时的氢气分压为66.5Pa,是安全的],其保护效果比10-2~10-3Pa的真空还好。这种方法对高铬钢、高速钢等材料的高温退火尤为适用。
⑥一般在10-3~133Pa的真空范围内,真空炉的温度均匀性可维持在±5℃,随着分压的上升,温度的均匀性会下降。因此,应合理选择回充分压,既保证金属元素不蒸发,又能保持炉温均匀。
1.4.2.2 预热和加热温度
真空加热是以辐射传热为主,在700℃以下的辐射效率很低,工件的温度滞后于炉膛的温度。所以真空加热需通过多段预热来减少工件温度的滞后,特别是对形状复杂的大尺寸工件,进行多段预热尤为重要。预热工艺见表1-19。淬火加热温度一般取盐浴处理温度的中下限。
表1-19 真空淬火加热预热温度

1.4.2.3 真空加热时间的确定
真空加热时的升温特性曲线见图1-35。在周期作业的真空炉中,影响加热时间的因素比较多,如炉膛结构尺寸、装炉量、工件形状和尺寸、加热温度、加热速度以及预热工艺等。一般都通过试验方法得出一个经验公式。

图1-35 真空加热时的升温特性曲线
根据炉温和被加热工件表面与心部的温度曲线(见图1-36)可知,在周期作业真空炉中,总的加热时间
t总=t升+t均+t保

图1-36 真空加热炉温和被加热工件表面与心部的温度
式中 t升——工件加热时,炉膛到达工艺温度指示所需的时间;
t均——透烧工件的均热时间,可按经验公式t保=α'D估算(α'为系数,见表1-20,D为有效厚度);
表1-20 真空加热透热系数α'的确定

注:如没有预热直接加热时,透热系数α'应增大15%~20%。
t保——合金元素在奥氏体中充分溶解的时间。
t保取决于钢的成分、原始组织及特殊工艺的要求等。碳钢到温并均匀化后,就基本上完成了奥氏体的转变,在该温度下仅需停留几分钟甚至零保温也可淬火(加热温度需取中上限)。合金钢,特别是高合金钢则需一定的保温时间(30min左右)。真空回火加热需要充分的保温,一般需1h即可使碳化物充分析出。
为了提高真空热处理的生产效率,克服真空炉在低温预热阶段升温速度慢的缺点,目前,国内外真空炉多数带有对流的加热装置,使生产周期缩短1/3~1/2。
1.4.2.4 真空淬火冷却介质
按照淬火工件的形状、尺寸、技术要求和材质确定冷却工艺时,首先应了解该钢在连续冷却条件下的过冷奥氏体分解曲线,根据所要求的淬火冷速,选择合适的冷却方式。常用的有油冷和气冷。
(1)真空油淬 真空淬火油应具有如下特性:饱和蒸气低,即低压下挥发少,要求蒸气压低于10-2~10-4Pa,以确保真空度在10~10-1Pa的条件下,真空淬火油不会发生明显的挥发;不污染真空系统,不影响真空效果;临界压强(即得到与大气压下有相当淬火冷却能力的最低气压)低,随着气压的降低,冷却能力变化不大,而在真空下仍有一定的冷却速度;化学稳定性好,使用寿命长;杂质与残炭少,酸值低;淬火后表面美观光洁;淬火后工件的硬度和盐浴淬火相当。
目前,世界上已研制和生产了多种精制的适用于真空淬火的油品,如美国海斯公司的H1油、H2油,日本初光工具公司的HV1油、HV2油,前苏联的BM1-4油等。1979年,我国研制成功并投入生产的ZZ-1型、ZZ-2型真空油具有冷却能力高、饱和气压低、热稳定好、对工件无腐蚀的特性,适用于工具钢真空淬火。ZZ-1、ZZ-2和H1、H2真空淬火油的特性指标见表1-21、表1-22。
表1-21 国产真空淬火油技术指标

表1-22 美国海斯公司真空淬火油技术指标

普通淬火油的特性指标随液面压强的下降有明显的变化:如特性温度降低,特性时间延长;沸腾阶段出现在更低的温度区间;在800~400℃范围的冷却时间比大气压下显著延长等。因而钢在低气压下油的冷却能力下降了,而在低温区却具有较高的冷却速度。真空淬火油的冷却强度随液面上气体压强的下降而降低的强度就小得多,这是由于在大气压以下一个较为宽广的压强区间内,蒸汽膜阶段能迅速结束,因而蒸汽膜对冷却过程的影响减弱。
由于真空加热的工件具有良好的表面状态,因而钢在真空淬火油中冷却可以获得与常规工艺相同的硬度。从原理上讲,真空淬火时维持液面压力为临界压强即可获得接近于大气压下的冷速。除此之外,提高气压还可以提高油的蒸发和凝结温度,因而可以避免因油本身的瞬时升温造成的挥发损失和对设备的污染。工艺上常采用向冷却室充填纯氮气至40~73kPa的操作,实践证明,对于某些低淬透性钢,若将气压增至大气压以上,将可能获得更高的冷速。这是由于蒸汽膜进一步变薄了,缩短了传热慢的蒸汽膜阶段。增压油淬进一步发展为油淬气冷淬火,这就为提高大型及精密工模具的淬火效果、减少变形提供了多种选择的可能性。
为了满足冷却能力的需要,真空淬火需要有足够的油量,一般按工件总重:油重为(1:10)~(1:15)计。
真空淬火油的品质,如酸值、残炭、水分、离子量都可能使工件严重着色,有时它们对工件光亮度的影响远大于对真空度的影响,使用过程中需定期分析黏度、闪点、冷却性能和水分。视检测结果适时更换或补充新油,并在使用中严格防止混入其他品牌的油品和水分。当真空油中水的质量分数达到0.03%时,就足以使工件表面变暗。当油中水的质量分数达到0.3%时,油的冷却特性将发生变化:低温区的冷却速度变大,因而易使形状复杂的工件淬裂。在液压压力降低时,含水的油面将发生沸腾,从而严重地破坏了真空。为此,新油在第一次使用前需进行调制,每次停炉后还应保持炉子的真空度,以防止空气和水分再次溶入。
为能迅速地调节油温趋于均匀,淬油池中应设搅拌装置以加强油的循环和对流。静止的油冷却速度为0.25~0.30℃/s,激烈搅拌的油为0.8~1.10℃/s。这是由于搅拌可加速破坏蒸汽膜和对流传热效果。若油的搅拌不够强烈,则易使尺寸大、结构复杂的工件和长杆件等出现软点和软带,若油的搅拌过于强烈,也会使淬火件产生较大的变形。控制工件入油后的开始搅拌时间,调节搅拌的激烈程度以及实现断续搅拌可以减少变形和软点。
应该关注真空油淬时高温瞬时的表面渗碳现象,高速钢经过真空油淬后将在工件表面层出现一个由残留奥氏体和碳化物组成的白亮层。分析认为,这与钢在油中冷却的高温阶段(1200~900℃)的瞬时渗碳有关。一般的解释是:由C、H、O组成的有机化合物——真空淬火油,在与活性的高速钢表面接触时,将形成一层薄而致密的、包围着工件的油蒸气外套,其中的CH4、CO将发生分解并析出浓度大和传播特性较高的具有活性的碳,可瞬时渗入钢中。高速钢M2于1.33Pa、1200℃下加热后油淬所得的瞬时渗层可达35~50μm,X射线显微分析证明,距表面10μm内是耐蚀性高的白层,其碳浓度可达1.50%~1.70%,从表面至50μm以下,C逐步降至其基体含量(0.80%~0.90%)。
真空油淬是目前广泛应用的一种工模具热处理工艺,使用中应注意以下几点。
①真空油淬时,如油面压强很低,接近油的沸腾状态,会使冷却能力下降,达不到预期的淬硬效果。因而,必须在真空加热后工件入油前后向炉内充填惰性气体,使淬面形成一定的压强,才能达到淬硬和光亮的淬火效果。实验指出,对不同淬透性的钢应选取不同的油面压强。淬火时还应注意淬火室充气与淬火件入油的先后顺序,对于淬透性差的钢种应采用先充气后入油的方式淬火,对于淬透性较好的钢种可采用先入油后充气的方式淬火。
另外,油面压强对淬火畸变亦有较大的影响。降低油面压强,可使淬火畸变显著减轻。应在保证淬火硬度和淬硬层的前提下,使油面压强尽可能低一些。
一般淬火前的压强应提高到26kPa以上,工艺上常采用向冷却室回充氮气,压强为0.04~0.05MPa(常用40~67kPa,高于67kPa对冷却特性的影响就不显著了)。淬火前压强接近于0.1MPa,可得到高的淬火硬度,充氮气有利于安全操作。
②淬火油槽要满足冷却要求,油槽的容积应比油与工件(包括料筐、料盘)之积大20%~30%。
③保持淬火油的纯洁度,防止老化变质。
④新油第一次使用时需做脱气处理。脱气处理的操作步骤是:将炉门开闭,启动机械真空泵抽真空及开动油槽内的油搅拌器,从观察孔观察油面情况,当油面沸腾并上升且有溢出油槽的趋势时需立即关闭真空阀门,当降压至46550Pa(350Torr)时,关闭真空阀门并保持5min以上,然后打开真空阀门使真空室压强再降至39900Pa(300Torr),仍保持5min以上,按此方式,使真空室中压强逐渐降低下来,在压强降至6650Pa(50Torr)之后,可使压强每次降得少些,直至降到最低压强为止。经此脱气处理后的淬油可以施行淬火。
⑤每次停炉后,还应使炉子保持真空状态(39900Pa,即300Torr以下),防止空气和水分再次溶入。
⑥严格控制淬火油的温度。油槽中还应装设冷却器,油的温升控制在25℃以内,对稳定淬火质量有益。
⑦为防止淬火软点和硬度不均匀,油槽中必须设置搅拌器。
⑧为了确保淬火油操作的安全性,必须制订防爆防燃措施。
(2)真空气淬 从目前国内外工模具真空淬火的情况分析,高压气淬的运用越来越普遍,工艺也越来越成熟。
真空气淬的冷速与气体的种类、气体的压力、流速、炉子的结构及装炉状况有关。可供使用的冷却气体有氩、氮、氦、氢等。它们在100℃时的某些物理特性见表1-23。
表1-23 各种冷却气体的物理特性(100℃)

与相同条件下的空气传热速度相比较,以空气为1,则氮气为0.99,氩气为0.70,氢气为7,氦气为6,见图1-37。

图1-37 氢、氦、氩、氮的相对冷却特性
①淬火气体的种类。在任何压强下,氢都有最大的热传导能力及最大的冷却速度,氢可以应用于装有石墨元件的真空炉,但对含碳量高的钢件,在冷却过程的高温阶段(1050℃以上)有可能造成轻微脱碳,对高强度钢有造成氢脆的危险,因此,人们并不欢迎它。
冷却速度仅次于氢的是惰性气体氦,在空气中氦的含量不足0.0005%,一般在天然气液化过程中制取氦比氮的价格可能高至上百倍,只有在某些特殊场合下必须用氦且经济合理时才用它。
氩的冷却能力比空气低,它在大气中的体积分数为0.93%,用压缩空气使之液化,精馏而来的氩成本较高。所以,只有在必要时作为氮的代用气使用。
氮的资源丰富,成本低,在略低于大气压下进行强制循环,冷却强度可上升约20倍。它是使用安全、冶金损害小的中性气体。氮在200~1200℃的温度范围内,对常用钢材呈惰性状态。
氮气中含氧(0.001%以上)可使高温下的钢轻微氧化、脱碳。因而常规下所用的高纯氮气纯度为99.999%。(相对露点-62℃,相应于真空度1.33Pa)。鉴于高纯氮气价格昂贵,有时在无特殊要求的情况下,可以用普通氮气。工业用氮的纯度一般为99.9%左右(O2含量<0.1%、露点-30℃)。
②提高气体冷却能力的方法。图1-38给出了冷却气体的压力与冷却时间(亦可理解为冷却速度)的关系。

图1-38 气压对冷却速度的影响
1—0.66m3/s;2—0.566m3/s
从图1-38可以看出,冷却速度随着气压的上升明显提高,但并非气压越高越好。对于尺寸较大,比表面小的工件,在更高的气压下,决定冷却速度的主导因素是钢的内部传热传导,因为这时对流传热加速冷却的效果难以达到中心。此时提高气压对增大冷却速度的作用不十分明显。又考虑到一般的真空炉只在低于大气压时密封效果较好,以及为了节约高纯气体,故真空淬火时的常用压力为0.5×105~0.8×105Pa,最高取0.92×105~0.99×105Pa。有试验表明,对M2钢制成的ф25mm×40mm圆柱体试样,装炉100kg,采用以下处理工艺:850℃×25min、1050℃×15min两次预热,1220℃×40min加热,气淬冷却至550℃,当淬火气体压力为1×105Pa时,冷却需185s,2×105Pa时需55s。即随着气压的增高,冷速加大,冷却时间减少。560℃×1h×2次回火后,硬度为65HRC以上。
此外,加压气体淬火还扩大了高合金工模具气淬的材料品种和尺寸范围,但气压过高时,由于动力和气体消耗呈比例地增长,设备需有严格的防护措施等,经济效益不再有优势。
提高气体的流速也可以提高其冷却速度。例如,静止空气的冷却烈度H=0.008,激烈搅拌的空气H=0.20,这是由于流速增大和气流的紊流程度加大,可使边界层减薄,热阻下降,因而传热系数增大的结果。例如,当气流速度从10.2m/s提高到58m/s时(一般情况下大于25m/s),氮、氢、氦的对流传热系数将提高3倍。
采用合适的装炉量,保持适当的间隔,均匀有序地摆放工件,也可以进一步改善冷却时热交换的条件。
(3)真空硝盐淬火 真空硝盐等温淬火,为很多工模具淬火提供了质量保证。等温淬火可减少畸变,防止开裂,再加上真空脱气效果,使淬火工具的寿命得到提高。如30CrMnSiNi2A钢经真空硝盐等温淬火后,其多次冲击疲劳总寿命比常规盐浴淬火提高1.56~1.92倍。所配制的硝酸钾、亚硝酸钠混合淬火剂在大气压下,没有物态的变化,它的冷却能力与自身温度有密切的关系。在大气压下,硝盐浴的使用温度一般不超过600℃(一般在550℃以下),可是在真空中的情况就不一样了。在真空中硝盐浴的温度越高,其饱和蒸气压越高,蒸发越剧烈。如在133Pa和320℃下的蒸发量为4.673mg/(cm2·h)。NaNO2在320℃开始分解,KNO3在550℃以上急骤分解。分解时将析出杂质和潮气。所以硝盐浴应尽量低温使用,并应在260~280℃或达到工作温度时继续排气,以清除杂质和水汽。加强搅拌可以提高盐浴的冷却能力。如204℃静止的硝盐浴冷却强度为0.5~0.8,激烈搅拌者可达2.25。搅动可以防止淬火件周围介质的局部过热。用氮或氩提高盐浴液面压力和反复充气至大气压以稀释盐槽上方的气氛,可以提高冷却能力并减少盐蒸气对设备的腐蚀。
静止硝盐浴总的冷却能力与油相近。为提高尺寸大、淬透性差的低合金工具钢的淬透能力,真空等温淬火的加热温度一般比常规淬火温度高。在Ms+30℃等温冷却,可以获得较为满意的力学性能和金相组织。在硝盐中的等温时间同高温加热时间。