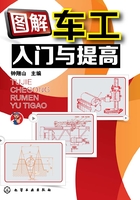
2.3 机制工艺基础与夹具
为保证零件的加工质量,在切削加工前,必须针对所加工零件的结构以及具体的技术要求,确定加工工艺方案,制定相应的工艺规程,此外,在车削加工中,对于一些难以保证车削要求的零件还往往需要设计夹具,以便使工件相对刀具有一个正确的位置,从而使相应的精度能得到保证,相应的车削操作也能方便地完成。因此,对生产操作人员来讲,了解一些基本的机械制造工艺与夹具知识也是很有必要的。
2.3.1 机械加工精度
零件经机械加工后的实际尺寸,表面形状、表面相互位置等几何参数符合于其理想的几何参数的程度称为机械加工精度。两者不符合的程度称为加工误差。加工误差越小,加工精度越高。
(1)零件的加工精度
①尺寸精度。尺寸精度是指加工后零件的实际尺寸与理想尺寸的符合程度。理想尺寸是指零件图上所注尺寸的平均值,即所注尺寸的公差带中心值。尺寸精度用标准公差等级表示,分为20级。
②形状精度。加工后零件表面实际测得的形状和理想形状的符合程度。理想形状是指几何意义上的绝对正确的圆柱面、圆锥面、平面、球面、螺旋面及其他成形表面。形状精度等级用形状公差等级表示,分为12级。
③位置精度。它是加工后零件有关表面相互之间的实际位置和理想位置的符合程度。理想位置是指几何意义上的绝对的平行、垂直、同轴和绝对准确的角度关系等。位置精度用位置公差等级表示,分为12级。
零件表面的尺寸、形状、位置精度有其内在联系,形状误差应限制在位置公差内,位置公差要限制在尺寸公差内。一般尺寸精度要求高,其形状、位置精度要求也高。
(2)获得尺寸精度的方法
①试切法。试切法就是通过试切→测量→调整→再试切的反复过程来获得尺寸精度的方法。它的生产效率低,同时要求操作者有较高的技术水平,常用于单件及小批生产中。
②定尺寸刀具法。加工表面的尺寸由刀具的相应尺寸保证的一种加工方法,如钻孔、铰孔、拉孔、攻螺纹、套螺纹等。这种方法控制尺寸十分方便,生产率高,加工精度稳定。加工精度主要由刀具精度决定。
③调整法。它是按工件规定的尺寸预先调整机床、夹具、刀具与工件的相对位置,再进行加工的一种方法。工件尺寸是在加工过程中自动获得的,其加工精度主要取决于调整精度。它广泛应用于各类自动机、半自动机和自动线上,适用于成批及大量生产。
④自动控制法。这种方法是用测量装置、进给装置和控制系统组成一个自动加工的循环过程,使加工过程中的测量、补偿调整和切削等一系列工作自动完成。图2-32(a)为磨削法兰肩部平面时,用百分表自动控制尺寸h的方法。图2-32(b)是磨外圆时控制轴径的方法。

图2-32 自动控制加工法
1—磨用夹具;2—工件;3—百分表座;4,7—百分表;5,10—硬质合金支点;6—触头;8—弹簧支架;9—工件
(3)获得零件几何形状精度的方法
零件的几何形状精度主要由机床精度或刀具精度来保证。如车圆柱类零件时,其圆度及圆柱度等几何形状精度主要取决于主轴的回转精度、导轨精度及主轴回转轴线与导轨之间的相对位置精度。
(4)获得零件的相互位置精度的方法
零件的相互位置精度,主要由机床精度、夹具精度和工件的装夹精度来保证。如在车床上车工件端面时,其端面与轴心线的垂直度决定于横向溜板送进方向与主轴轴心线的垂直度。
(5)产生加工误差的原因及消减方法
①原理误差。加工时,由于采用了近似的加工运动或近似的刀具轮廓而产生的误差,称为原理误差。如用成形铣刀加工锥齿轮、用近似的刀具形状加工模数相同而齿数不等的齿轮将产生齿形误差。
②装夹误差。工件在装夹过程中产生的误差称为装夹误差。它是定位误差和夹紧误差之和。
a.定位误差。定位误差是工件在夹具中定位时,其被加工表面的工序基准在加工方向尺寸上的位置不定性而引起的一项工艺误差。定位误差与定位方法有关,包括定位基准与工序基准不重合引起的基准不重合误差和定位基准制造不准确引起的基准位移误差。计算方法为:
ΔD=Δy+ΔB
位移误差与基准不重合误差分别为:
Δy=(Th+TS+Xmin)/2
ΔB=Td/2
式中 Th——工件孔的制造公差,mm;
TS——心轴的制造公差,mm;
Td——工序基准所在的外圆柱面的直径公差,mm。
例如某工件的A、B外圆直径分别为mm及
mm,它们的同轴度公差值为0.07mm,按图2-33所示的加工精度及装夹方法进行加工,则可计算出其定位误差为:

图2-33 定位误差计算实例
由于加工时以A圆的下母线为工序基准,而定位基准是B圆中心线,属基准不重合误差。误差为垂直方向上A圆下母线与B圆中心线距离的变动量,包括A、B圆的同轴度误差δ及A圆下母线到A圆中心线的变动量。
ΔB=TSA/2+δ=0.05+0.07=0.12mm
B圆在90°的V形架上定位,其中心线在垂直方向的变动量为基准位移误差:
因此 ΔD=ΔB+Δy=0.12+0.0707=0.1907mm
此定位误差超过了尺寸精度公差,无法达到加工要求。
b.夹紧误差。结构薄弱的工件,在夹紧力的作用下会产生很大的弹性变形,在变形状态下形成的加工表面,当松开夹紧、变形消失后将产生很大的形状误差,如图2-34所示。

图2-34 夹紧变形
c.消减定位误差和夹紧误差的方法。消减定位误差和夹紧误差的方法主要有以下两方面。
(a)正确选择工件的定位基准,尽可能选用工序基准(工艺文件上用以标定加工表面位置的基准)为定位基准。图2-33的加工实例,如果采用图2-35的方法进行装夹,则ΔB为零,且Δy可以忽略不计,故ΔD为零,可大幅度地降低其误差。如必须在基准不重合的情况下加工,一定要计算定位误差,判断能否加工。

图2-35 基准相符加工
(b)采用宽卡爪或在工件与卡爪之间衬一开口圆形衬套可减小夹紧变形,如图2-36所示。

图2-36 减小夹紧变形
③机床误差
a.机床主轴误差。它是由机床主轴支承轴颈的误差、滚动轴承制造及磨损造成的误差组成的。主轴回转时将出现径向圆跳动及轴向窜动。径向圆跳动使车、磨后的外圆及镗出的孔产生圆度误差;轴向窜动会使车削后的平面产生平面度误差。因此,主轴误差会造成加工零件的形状误差、表面波动和表面粗糙度值大。
消减机床主轴误差,可采用更换滚动轴承、调整轴承间隙、换用高精度静压轴承的方法。在外圆磨床上用前、后固定顶尖装夹工件,使主轴仅起带动作用,是避免主轴误差的常用方法。
b.导轨误差。导轨误差是导轨副实际运动方向与理论运动方向的差值。它包括在水平面及垂直面内的直线度误差和在垂直平面内前后导轨的平行度误差(扭曲度)。导轨误差会造成加工表面的形状与位置误差。如车床、外圆磨床的纵向导轨在水平面内的直线度误差,将使工件外圆产生母线的直线度误差[图2-37(a)];卧式镗床的纵向导轨在水平面内的直线度误差,当工作台进给镗孔时,孔的中心线会产生直线度误差[图2-37(b)]。

图2-37 导轨直线度误差的影响
1—导轨;2—工件;3—工作台
为减小加工误差,需经常对导轨进行检查及测量。及时调整床身的安装垫铁,修刮磨损的导轨,以保持其必需的精度。
c.机床主轴、导轨等位置关系误差。该类误差将使加工表面产生形状与位置误差。如车床床身纵向导轨与主轴在水平面内存在平行度误差,会使加工后的外圆出现锥形;立式铣床主轴与工作台的纵向导轨不垂直,铣削平面时将出现下凹度,如图2-38所示。

图2-38 机床导轨、主轴相互位置精度的影响
1—工件;2—导轨
d.机床传动误差。机床传动误差是刀具与工件速比关系误差。传动机构的制造误差、装配间隙及磨损,将破坏正确的运动关系。如车螺纹时,工件每转一转,床鞍不能准确地移动一个导程,会产生螺距误差。
提高传动机构的精度,缩短传动链的长度,减小装配间隙,可减小因传动机构而造成的加工误差。
④夹具误差
a.夹具各元件的位置误差。夹具的定位元件、对刀元件、刀具引导装置、分度机构、夹具体的加工与装配所造成的误差,将直接影响工件的加工精度。为保证零件的加工精度,一般将夹具的制造公差定为相应尺寸公差的1/3~1/5。
b.夹具磨损造成的误差。夹具在使用一定时间后,因与工件及刀具摩擦而磨损,使加工时产生误差。因此,应定期检查夹具的精度及磨损情况,及时修理及更换磨损的夹具。
⑤刀具误差。刀具的制造误差、装夹误差及磨损会造成加工误差。用定尺寸刀具加工时,刀具的尺寸误差将直接反映在工件的加工尺寸上。如铰刀直径过大,则铰孔后的孔径也过大,此时应将铰刀直径研小。成形刀具的误差直接造成加工表面的形状误差,如普通螺纹车刀的刀尖角不是60°时,则螺纹的牙型角便产生误差。
刀具在使用过程中会磨损,并随切削路程增加而增大。磨损后刀具尺寸的变化直接影响工件的加工尺寸,如车削外圆时,工件的直径将随刀具的磨损而增大。因此,加工中应及时刃磨、更换刀具。
⑥工艺系统变形误差
a.工艺系统的受力变形。工艺系统在切削力、传动力、重力、惯性力等外力作用下,产生变形,破坏了刀具与工件间的正确位置,造成加工误差。其变形的大小与工艺系统的刚度有关。
工艺系统刚度不足造成的误差有:工艺系统刚度在不同加工位置上的差别较大时造成的形状误差;毛坯余量或材料硬度不均引起切削力变化造成的加工误差;切削力变化造成加工尺寸变化。此外,刀具的锐、钝变化及断续切削都会因切削力变化使工件的加工尺寸造成较大的误差。
减少工件受力变形误差的措施包括:零件分粗、精阶段进行加工;减少刀具、工件的悬伸长或进行有效的支承以提高其刚度,减小变形及振动;改变刀具角度及加工方法,以减小产生变形的切削力;调整机床,提高刚度。
b.工艺系统受热变形误差。切削加工时,切削热及机床传动部分发出的热量,使工艺系统产生不均匀的温升而变形,改变了已调整好的刀具与工件的相互位置,产生加工误差。热变形主要包括:工件受热变形,即在切削过程中,工件受切削热的影响而产生的热变形;刀具受热变形,刀具体积较小,温升快、温度高,短时间内会产生很大的伸长量,然后变形不再增加;机床受热变形,机床结构不对称及不均匀受热,会使其产生不对称的热变形。
减少热变形误差的措施有:减轻热源的影响,切削时,浇注充分的切削液,可减小工件及刀具的温升及热变形;进行空运转或局部加热,保持工艺系统热平衡;在恒温室中进行精密加工,减少环境温度的变化对工艺系统的影响;探索温度变化与加工误差之间的规律,用预修正法进行加工。
⑦工件残余应力引起的误差。工件材料的制造和机械加工过程中会产生很大的热应力。热加工应力超过材料强度时,工件产生裂纹甚至断裂。因此,残余应力是在没有外力作用的情况下,存在于构件内部的应力。存在残余应力的工件处于不稳定状态,具有恢复到无应力状态的倾向,直到此应力消失。工件在材料残余应力的消失过程中,会逐渐地改变形状,丧失其原有的加工精度。具有残余应力的毛坯及半成品,经切削后原有的平衡状态被破坏,内应力重新分布,使工件产生明显的变形。减小工件的残余应力的措施有以下几种。
a.铸、锻、焊接件进行回火后退火,零件淬火后回火。
b.粗、精加工间应间隔一定时间,松开后施加较小的夹紧力。
c.改善结构,使壁厚均匀,减小毛坯的残余应力。
⑧测量误差。测量时,由量具本身的误差及测量方法造成的误差称测量误差。减少测量误差,要选用精度及最小分度值与工件加工精度相适应的量具。测量方法要正确并正确读数;避免因工件与量具热膨胀系数不同而造成误差。精密零件应在恒温室中进行测量。要定期检查量具并注意维护保养。
(6)工艺尺寸链及其计算
在机械加工过程中,互相联系的尺寸按一定顺序首尾相接,排列成的尺寸封闭图就是尺寸链。在加工过程中的有关尺寸形成的尺寸链,称为工艺尺寸链。
①尺寸链的组成。一个尺寸链由组成环、封闭环组成。
a.链环。尺寸链图中的每一个尺寸都称为链环。
b.封闭环。尺寸链中,最终被间接保证尺寸的那个环称为封闭环,代号为A∑。一个尺寸链中只有一个封闭环。
c.组成环。尺寸链中,能人为地控制或直接获得的尺寸的环,称为组成环。组成环按它对封闭环的影响,又可分为增环与减环。组成环中,某组成环增大而其他组成环不变,使封闭环随之增大,则此组成环为增环,记为;某组成环增大而其他组成环不变,使封闭环随之减少,此组成环为减环,记为
。
②尺寸链的基本计算。尺寸链的基本计算公式为:
式中 A∑——封闭环的基本尺寸,mm;
A∑max——封闭环的最大极限尺寸,mm;
——各增环的基本尺寸,mm;
A∑min——封闭环的最小极限尺寸,mm;
——各减环的基本尺寸,mm;
——各增环的最大极限尺寸,mm;
——各增环的最小极限尺寸,mm;
——各减环的最大极限尺寸,mm;
——各减环的最小极限尺寸,mm;
m——增环的环数;
n——减环的环数;
T∑——封闭环的公差,mm;
——各增环的公差,mm;
——各减环的公差,mm;
Ti——各组成环的公差,mm。
③计算实例。如图2-39所示的零件,工件平面1和平面3已经加工,平面2待加工,尺寸A及其公差可按以下方法求解。

图2-39 工艺尺寸链的计算
根据零件的工序图要求,可画出如图2-39(b)所示的尺寸链图,已知组成环A1、A2,则:

故A∑最大为60.2mm,最短为59.9mm。
2.3.2 工件的定位
在切削加工中,要使工件的各个加工表面的尺寸、形状及位置精度符合规定要求,必须使工件在机床或夹具中占有一个确定的位置。使工件在机床上或夹具中占有正确位置的过程称为定位。工件的定位可以通过找正实现,也可以由工件上的定位表面与夹具的定位元件接触来实现。
(1)工件的定位原理
工件的定位是通过六点定位原理来实现的。
①六点定位原理。物体在空间的任何运动,都可以分解为相互垂直的空间直角坐标系中的六种运动。其中三个是沿三个坐标轴的平行移动,分别以、
及
表示;另三个是绕三个坐标轴的旋转运动,分别以
、
及
表示,如图2-40所示。这六种运动的可能性,称为物体的六个自由度。

图2-40 物体的六个自由度
在夹具中适当地布置六个支承,使工件与六个支承接触,就可限制工件的六个自由度,使工件的位置完全确定。这种采用布置恰当的六个支承点来限制工件六个自由度的方法,称为“六点定位”,如图2-41所示。

图2-41 六点定位原理
在图2-41中,xoy坐标平面上的三个支承点限制了工件的、
及
三个自由度;yoz坐标平面的两个支承点限制了
及
两个自由度;xoz坐标平面上的一个支承点限制了
一个自由度。这种必须使定位元件所相当的支承点数目刚好等于六个,且按3:2:1的数目分布在三个相互垂直的坐标平面上的定位方法称为六点定则,或称为六点定位原理。
②六点定位的应用
a.完全定位。工件在夹具中定位时,如果夹具中的六个支承点恰好限制了工件的六个自由度,使工件在夹具中占有完全确定的位置,这种定位方式称为“完全定位”,简称“全定位”,参见图2-41。
b.不完全定位。定位元件的支承点完全限制了按加工工艺要求需要限制的自由度数目,但却少于六个自由度。
如图2-42所示为阶梯面零件,需要在铣床上铣阶梯面。

图2-42 阶梯面零件图
由于其底面和左侧面为高度和宽度方向的定位基准,阶梯槽是前后贯通的,故只需限制五个自由度(底面三个支承点,侧面两个支承点),装夹定位如图2-43所示。

图2-43 工件在夹具中的定位
又如在平面磨床上磨平面,如图2-44所示,要求保证工件的厚度尺寸H及平行度δa,只需限制、
、
三个自由度即可。

图2-44 工件在磁力工作台上磨平面
以上说明,并非任何工件在夹具中一定要完全定位,只要满足加工工艺要求,限制的自由度少于六个也是合理的,且可简化夹具的结构。
c.欠定位。工件定位时,定位元件所能限制的自由度数,少于按加工工艺要求所需要限制的自由度数,称为欠定位。欠定位不能保证加工精度要求,不允许在欠定位情况下进行加工。
如图2-45(a)所示的零件,需在铣床上铣不通槽。如果端面没有定位点C[见图2-45(b)],铣不通槽时,其槽的长度尺寸不能确定,因此,不能满足加工工艺要求,这就是欠定位。

图2-45 工件在夹具中安装铣不通槽
d.过定位。定位元件所相当的支承点数多于所能限制的自由度数,即工件上有某一自由度被两个或两个以上支承点重复限制的定位,称为过定位,也称重复定位。
图2-46(a)所示的装夹方法中,较长的心轴对内孔定位消除了、
及
、
四个自由度,夹具平面P对工件大端面定位,消除
、
及
三个自由度,
和
被心轴和平面P重复限制,故是过定位。

图2-46 工件的过定位及改进方法
由于工件与定位元件都存在误差,无法使工件的定位表面同时与两个进行重复定位的定位元件接触,如果强行夹紧,工件与定位元件将产生变形,甚至损坏。
图2-46(b)及图2-46(c)是改进后的定位方法。图2-46(b)采用短圆柱、大平面定位。短圆柱仅限制、
两个自由度,避免了过定位。图2-46(c)采用长圆柱、小平面定位,小平面仅限制
一个自由度,避免了过定位。这两种都是正确的定位方法,其中图2-46(b)主要保证加工表面与大端面的位置精度;图2-46(c)主要保证加工表面与内孔的位置精度。
(2)常用的定位方法及定位元件
①平面定位。工件以平面作定位基准,是常见的定位方式,如加工箱体、机座、平板、盘类零件时,常以平面定位。
当工件以一个平面为定位基准时,一般不以一个完整的大平面作为定位元件的工作接触表面,常用三个支承钉或两三个支承板作定位元件。
a.支承钉。支承钉主要用于毛坯平面定位。如图2-47(a)、图2-47(b)所示分别为球头钉及尖头钉,可减小与工件接触面;图2-47(c)为网纹顶面支承钉,能增大与工件的摩擦力;图2-47(d)、图2-47(e)为可调支承钉。当各批毛坯尺寸及形状变化很大时,可调节其高度,调节后用螺母锁紧。

图2-47 支承钉
b.支承板。支承板主要用于已加工过的大、中型工件的定位基准。它有A型和B型两种结构,如图2-48所示。其中B型接触面积小,有碎屑时不易影响定位精度。

图2-48 支承板
②圆柱孔定位。利用工件上的圆柱孔作定位基准,也是常见的定位方式之一,根据所定位圆柱孔长短的不同,又可分为长圆柱孔定位及短圆柱孔定位两种。
a.长圆柱孔定位。长圆柱孔定位是用相对于直径有一定长度的孔定位,是能限制工件4个自由度的定位方法。定位元件有刚性心轴与自动定心心轴两大类。其中:刚性心轴与工件孔的配合,可采用过盈配合、间隙配合或小锥度心轴。
当工件定位孔的精度很高,且要求定位精度很高时,可采用具有较小过盈量的过盈配合。心轴的结构如图2-49(a)所示。它由导向部分盘起引导作用,使工件能迅速套上心轴。

图2-49 刚性心轴
图2-49(b)所示为间隙配合心轴结构,以心轴轴肩端面作小平面定位,工件由螺母作轴向夹紧。心轴直径与工件孔一般采用H7/e7、H7/f6或H7/g5的配合。间隙配合使装卸工件比较方便,但也形成了工件的定位误差。
图2-49(c)所示为小锥度心轴。其锥度C=1/5000~1/1000,工件套入心轴需要大端压入一小段距离,以产生部分过盈,提高定位精度。小锥度心轴消除了间隙,并且能方便地装卸工件。
图2-50所示为自动定心心轴。该心轴的两端Ⅰ—Ⅰ、Ⅱ—Ⅱ截面处都有三块一组的滑块,旋动螺母,由于斜面A与B的作用,两组滑块同时向外撑紧内孔,使孔得到自动定心。

图2-50 自动定心心轴
b.短圆柱孔定位。短圆柱孔定位是定位孔与定位元件的接触长度较短的一种定位方法。它一般需要与其他定位方法同时使用。其定位元件是短定位销及短圆柱,如图2-51所示。

图2-51 短圆柱孔定位
③外圆柱面定位。工件以外圆柱面定位,可分长、短圆柱表面定位。定位方法有以下几种。
a.自动定心定位。三爪自定心卡盘、弹簧夹头及双V形架自动定心装置都属于这种定位。这种定位方法一般用于长圆柱表面定位,如图2-52所示。

图2-52 外圆柱面的自动定心
b.定位套定位。如图2-53(a)为短圆柱定位;图2-53(b)为长圆柱表面定位。

图2-53 定位套定位
1—工件;2—定位套
c.V形架定位。工件以V形架作定位元件,不仅安装方便,且对中性好。不论定位基准如何,均可保证工件定位基准线(轴线)落在两斜面的对称平面上,即x轴方向定位误差为零。但当圆柱直径大小有变化时,在z轴方向有定位误差。其定位情况如图2-54所示。

图2-54 圆柱体在V形架中定位
V形架有长、短之分,短V形架仅限制2个自由度;长V形架可限制4个自由度。为减小工件与V形架的接触面积,可将长V形架做成两个短V形架。
④锥孔定位。锥孔定位有长锥孔与短锥孔定位。长锥孔一般采用锥度心轴定位,可限制5个自由度。锥度较小时,工件不再作轴向定位,不夹紧就可进行切削力较小的加工。锥度较大的工件应进行轴向夹紧[图2-55(a)]。如果工件的定位表面是外圆锥面,可采用定位套定位[图2-55(b)]。

图2-55 长锥孔、轴定位
锥孔定位时,工件与心轴间无间隙,且能自动定心,具有很高的定心精度。
⑤几种定位方法的组合定位
a.两面一销定位。两面一销定位是一种完全定位,定位情况如图2-56所示。工件底面作三点定位,右侧面作两点定位,削边销仅限制向自由度。

图2-56 两面一销定位
b.一面两销定位。定位情况如图2-57所示。图中工件大平面限制3个自由度,短圆柱销限制2个自由度。削边销限制绕圆柱销1转动的自由度。削边销既可保证定位精度,又可补偿两定位销的销距误差。

图2-57 一面两销定位
1—圆柱销;2—削边销
c.平面、短V形架及削边销定位。这种定位如图2-58所示。工件的大端面限制3个自由度;短V形架作两点定位,削边销限制绕轴线转动的自由度。

图2-58 平面、短V形架及削边销定位
2.3.3 工件的夹紧
工件在夹具上正确定位后,还必须通过夹紧装置来固定工件,使其保持正确的位置,当切削加工时,不使零件因切削力的作用而产生位移,从而保证零件的加工质量。
由于加工零件外形结构、生产批量、技术要求不同,因此,所用的夹紧装置也有所不同。夹紧装置分类的方法较多,按夹紧力的来源不同,可分为手动夹紧装置(力源来自人力)、气压夹紧装置(力源来自气动压力)、液压夹紧装置(力源来自液压)、电力(力源来自电磁、电动机等动力装置)夹紧装置等;按传递夹紧力机构形式的不同,可分为螺旋夹紧、杠杆夹紧、斜楔夹紧、螺旋压边夹紧等。
(1)夹紧装置的基本要求
①保证加工精度,即夹紧时不能破坏工件的定位准确,并使工件在加工过程中不产生振动和工件的受压面积最小。
②手动夹紧机构要有自锁作用,即原始作用力消除后,工件仍能保持夹紧状态而不会松开。
③夹紧机构操作时安全省力、迅速方便,以减轻工人劳动强度,缩短辅助时间,提高生产效率。
④结构简单、紧凑,并具有足够的刚度。
(2)常用夹紧装置的结构
①斜楔夹紧机构。图2-59为斜楔夹紧机构,它由螺杆1、楔块2、铰链压板3、弹簧4和夹具体5组成。当转动螺杆时,推动楔块向前移动,铰链压板转动而夹紧工件。

图2-59 斜楔夹紧机构
1—螺杆;2—楔块;3—铰链压板;4—弹簧;5—夹具体
②螺钉夹紧机构。螺钉夹紧机构如图2-60所示。它通过旋转螺钉直接压在工件上,螺钉前端的圆柱部分通常淬硬。为了防止拧紧螺钉时其头部压伤工件表面,常制成压块与螺钉浮动连接。压块结构见图2-61。

图2-60 螺钉夹紧机构
1—手柄;2—套;3—夹具;4—工件;5—压块

图2-61 压块结构
③螺母夹紧机构。当工件以孔定位时,常用螺母夹紧。该机构具有增力大,自锁性好的特点,很适合于手动夹紧。它夹紧缓慢,在快速机动夹紧中应用很少,常见结构如图2-62所示。

图2-62 螺母夹紧机构
1—螺母;2—工件;3—垫圈
④螺旋压板夹紧机构。螺旋压板夹紧机构是螺旋机构与压板及其他机构组合成的复合式夹紧机构。图2-63(a)、(b)、(c)的螺旋压紧位于中间,螺母下用球面垫圈,压板尾部的支柱顶端也作成球面,以便在夹紧过程中作少量偏转。图2-63(d)是“L”形压板,结构紧凑,但夹紧力小。图2-63(e)是可调高度压板,它适应性广,图2-63(f)的螺旋压紧机构,在夹紧过程中作少量偏转及高度调整。

图2-63 螺旋压板夹紧机构
⑤偏心夹紧机构。偏心夹紧机构是利用转动中心与几何中心偏移的圆盘或轴作为夹紧元件进行夹紧的。常用的偏心结构有带手柄的偏心轮[图2-64(a)、(b)],偏心凸轮[图2-64(c)、(d)]和偏心轴[图2-64(e)、(f)、(g)]。

图2-64 常用偏心夹紧机构
1—手柄;2—偏心轮;3—轴;4—槽块;5—压板;6—拉杆
2.3.4 车床典型夹具
车床夹具的种类较多,根据其通用化程度的不同,可分为通用夹具及专用夹具、组合夹具三种,表2-2给出了车床夹具的分类及特点。
表2-2 车床夹具的分类及特点

(1)通用夹具
通用夹具通常由具有互换性、耐磨性的机床附件构成,其尺寸、规格已形成系列及标准,通用性好,能用于不同形状、不同规格的各类零件的加工。
常用的通用夹具类型有:顶尖、卡头、卡盘、心轴、拨盘、花盘等,各类型的结构及使用特点如下。
①顶尖。顶尖一般与卡头拨盘配合使用,顶尖与工件上的中心孔定位,卡头夹住工件的一端,拨盘与机床主轴连接,并通过拨杆带动卡头和工件转动。常用顶尖的类型如下。
a.固定顶尖。固定顶尖一般固定在机床上,工件的中心孔与顶尖接触并相对转动,其形式与结构参数如图2-65所示。

图2-65 固定顶尖的形式与结构参数
b.回转顶尖。回转顶尖具有转动功能,其结构形式如图2-66所示。

图2-66 回转顶尖
c.内拨顶尖。内拨顶尖的外锥面上开有沟槽与工件上的内锥面接触精度高,其结构形式如图2-67所示。

图2-67 内拨顶尖
d.夹持式内拨顶尖。夹持式内拨顶尖是削边的圆柱柄,锥面同内拨顶尖,其结构形式如图2-68所示。

图2-68 夹持式内拨顶尖
e.外拨顶尖。外拨顶尖的内锥面上开有槽,与工件的外锥面接触,其结构形式如图2-69所示。

图2-69 外拨顶尖
②卡头。卡头用来夹紧工件,在拨盘或拨杆的带动下使工件旋转,其类型主要有鸡心卡头、卡环、夹板和快换卡头。
a.鸡心卡头。鸡心卡头夹紧工件的形式和结构参数如图2-70所示。

图2-70 鸡心卡头
b.卡环。卡环夹紧工件的形式和结构参数如图2-71所示。

图2-71 卡环
c.夹板。夹紧工件的形式和结构参数如图2-72所示。

图2-72 夹板
③拨盘。拨盘的结构参数如图2-73所示。

图2-73 拨盘
④卡盘。常用的卡盘主要有三爪卡盘和四爪卡盘。图2-74给出了三爪自定心卡盘的结构和工作原理。使用时,用扳手通过方孔1转动小锥齿轮2时,就带动大锥齿轮3转动,大锥齿轮3的背面有端面螺纹4,如图2-74(b)所示,与三个卡爪上的端面螺纹相啮合,带动三个卡爪5同时沿径向作向心或离心移动,实现工件的定心和夹紧。

图2-74 三爪自定心卡盘
1—方孔;2—小锥齿轮;3—大锥齿轮;4—端面螺纹;5—卡爪
四爪单动卡盘也称四爪卡盘,卡盘上有四个卡爪,每个卡爪都单独由一个螺杆来移动。每个卡爪1上的螺纹与螺杆2啮合,实现单卡爪独立移动,如图2-75所示。

图2-75 四爪单动卡盘
1—卡爪;2—螺杆;3—卡盘体
根据车床主轴结构不同,三爪自定心卡盘或四爪单动卡盘一般通过带锥柄的法兰盘或带内锥孔的法兰盘与车床主轴的连接。
带锥柄的法兰盘的结构如图2-76所示,它的锥柄与主轴前端内锥孔配合实现定位,并通过贯穿主轴孔的拉杆1拉紧法兰盘,通过圆锥面间的摩擦力,将主轴上的运动和动力传递给法兰盘。

图2-76 带锥柄的法兰盘
1—拉杆;2—主轴;3—法兰盘;4—定心圆柱面
带内锥孔的法兰盘的结构如图2-77所示,它的内锥孔与主轴的外圆锥面配合实现定位,法兰盘用螺钉紧固在主轴前端的法兰上,通过端面间的摩擦力,将主轴上的运动和动力传递给法兰盘。

图2-77 带锥孔的法兰盘
1—主轴;2—法兰盘
(2)专用夹具
专用夹具是针对某特定零件的某道加工工序,为保证其加工质量而有针对性设计的夹具,一般只能用于该零件的加工,常见的类型有:角铁式车床夹具和花盘式车床夹具等。
当零件被加工表面的旋转轴线与定位支承表面不垂直时,夹具的定位支承面与安装平面就不平行,两面具有一定的夹角,即构成角铁形状。角铁式车床夹具多用于加工壳体、多通管接头和复杂的交角表面等。图2-78所示角铁式车床夹具,零件定位基准为一平面,被加工表面的轴线对基准面是平行的。

图2-78 角铁式车床夹具
1—削边定位销;2—圆柱定位销;3—轴向定程基面;4—夹具体;5—压板;6—工件;7—导向套;8—平衡铁
当加工表面与主要定位基准面要求相互垂直的复杂工件,可以装夹在花盘式车床夹具上加工,花盘式车床夹具主要适用于盘、环、套类和壳体类零件的加工;图2-79给出了利用圆盘式车床夹具装夹连杆的加工示意图。

图2-79 花盘式车床夹具装夹连杆
1—连杆;2—圆形压板;3—压板;4—V形架;5—花盘
(3)组合夹具
组合夹具是利用一套预先制造好的,不同形状,不同规格,具有互换性、耐磨性的标准元件和组合件,根据工件的不同加工要求,采用组合的方式,拼装而成的各种专用夹具。主要适用于产品变化较大的生产,如新产品试制,单件小批量生产和临时性突击任务等。
①组合夹具的元件。一套组合夹具主要由基础元件、支承元件、定位元件、导向元件、压紧元件、紧固元件、其他元件及组合件八大元件所组成。
a.基础元件。基础件包括方形、圆形基础板和基础角铁(图2-80),它是组合夹具的底座,相当于专用夹具的夹具体。

图2-80 基础元件
b.支承元件。支承元件主要作为不同高度和各种定位的支承面,和基础件共同组成夹具体。它包括方形、角度支承、角铁、菱形板、V形架等,如图2-81所示。

图2-81 支承元件
c.定位元件。它用来确定各元件之间或元件与元件之间的相对位置,以保证夹具的组装精度。包括定位键、定位销、定位盘及各类定位支座、定位支承等,如图2-82所示。

图2-82 定位元件
d.导向元件。它包括各种结构形式和规格尺寸的模板、导向套及导向支承等,如图2-83所示,主要起引导刀具的作用。

图2-83 导向元件
e.压紧元件。它是指各种形状和尺寸的压板,如图2-84所示。其作用是压紧工件,保持工件定位后的正确位置,使之在外力作用下不会变动。

图2-84 压紧元件
f.紧固元件。紧固元件包括各种螺栓、螺钉、螺母和垫圈,如图2-85所示。

图2-85 紧固元件
g.其他元件。包括连接板、回转压板、浮动块、各种支承钉、支承帽,如图2-86所示。

图2-86 其他元件
h.组合件。组合件是由几个元件组成的单独部件,在使用过程中,以独立部件参与组装。它用途广,结构合理,使用方便,与基础件、支承件并列成为组合夹具的一种重要元件,如图2-87所示。

图2-87 组合件
②组合夹具的组装
a.熟悉零件图、工艺和技术要求,特别是对本工序所要求达到的技术要求要了解透彻。
b.确定组装方案,选择定位元件、夹紧元件,初步确定夹具的结构方案。
c.试装。在有了初步设想后,进行试装,并在试装中不断地修改和完善组装方案。
d.连接、调整和固定各元件,安装后检验。