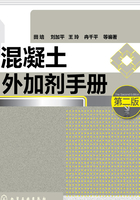
3.2 高效减水剂
高效减水剂是一种新型的化学外加剂,其化学性能有别于普通减水剂,在正常掺量时具有比普通减水剂更高的减水率,没有严重的缓凝及引气量过多的问题,高效减水剂也称超塑化剂、超流化剂、高范围减水剂等
目前我国高效减水剂的品种较多,主要品种有萘系高效减水剂、蜜胺高效减水剂、氨基磺酸盐系减水剂、脂肪高效减水剂等,下面对各种高效减水剂分别予以介绍。
3.2.1 萘系高效减水剂
萘系高效减水剂是以萘及萘系同系物为原料,经浓硫酸磺化、水解、甲醛缩合,用氢氧化钠或部分氢氧化钠和石灰水中和,经干燥而成的产品。
① 英文名称 sulfonated naphthalene formaldehyde (SNF)condensate, superplastcizers, super flowing admixture;high Range water-reducing admixture
② 结构式 如图3-18所示。

图3-18 萘系高效减水剂分子结构示意图(n=6~13)
③ 分子量 由于缩合度不一样,分子量为也不同。
3.2.1.1 生产所用主要原料及检测方法
(1)工业萘
萘的分子式为C10H8,分子量为128。生产实践表明:用工业萘含量高的原料,生产的产品性能较好,引气较小。目前我国大多数外加剂企业采用工业萘为原料,用精萘的较少。精萘有利于产品质量稳定。萘由煤焦油蒸馏提取,固体工业萘为白色,允许带微红或微黄色的片状或粉状结晶。液体工业萘颜色不作规定。萘在80℃时熔化,218℃时沸腾,不溶于水而易于升华,有特殊气味。
① 工业萘的技术指标应符合表3-15规定。
表3-15 工业萘的技术指标

② 试验方法:
a.结晶点按GB 3069.2《萘结晶点的测定方法》进行;
b.不挥发物按GB 6701《萘不挥发物的测定方法》进行;
c.灰分按GB 3069.1《萘灰分的测定方法》规定进行。
(2)硫酸
① 硫酸是生产萘系减水剂的原料之一。一般应用浓度应大于98%浓硫酸,其为无色或淡黄色透明的液体,密度为1.84g/cm3,分子式为H2SO4,分子量为98。
② 浓硫酸性能指标应符合表3-16的要求。
表3-16 浓硫酸性能指标

③ 硫酸含量的测定、发烟硫酸中游离三氧化硫含量、工业硫酸灰分,铁含量,砷含量、铅含量、透明度,色度的测定均按GB 11198有关规定进行。
(3)工业甲醛溶液
工业甲醛浓度为35%~37%,无色透明液体,有刺激性气味,15℃时密度为1.10g/cm3,分子式为CH2O,分子量为30。
① 技术要求 外观:清晰无悬浮物液体,低温时允许白色浑浊,工业甲醛溶液应符合表3-17的要求。
表3-17 甲醛的技术要求

② 检测方法 工业甲醛溶液的色度按GB 3143规定进行,铁的含量按GB 3049规定进行,甲醛和甲醇含量及酸度、灰分按GB 9009规定进行。
(4)氢氧化钠
工业用氢氧化钠有液体和固体两种。固体产品应先配制成浓度为30%~40%的液体后再使用。
外观:工业用固体氢氧化钠主体为白色,有光泽,允许微带颜色。工业用固体氢氧化钠应符合表3-18的要求。
表3-18 工业用固体氢氧化钠 单位: %

从表3-18可以看出,用不同方法生产的氢氧化钠,其中氯化钠含量有较大差异,水银法生产的氢氧化钠中氯化钠含量最低,隔膜法生产的氢氧化钠中氯化钠含量最高。根据对外加剂中氯离子的要求,可选用不同方法、不同等级的氢氧化钠。
工业用液体氢氧化钠应符合表3-19的要求。
表3-19 工业用液体氢氧化钠 单位: %

注:1.二氧化硅、汞含量为型式检验项目。
2.本标准数据处理采用修约值比较法。
a.工业用氢氧化钠中氢氧化钠的含量的测定。 按GB 4348.1和GB 11213.1进行,其中GB 11213.1为仲裁法。
b.工业用氢氧化钠中碳酸钠的测定。 按GB 7698和GB 4348.1进行,其中GB 7698为仲裁法。
c.工业用氢氧化钠中铁含量的测定。 按GB 4348.3进行。
d.工业用氢氧化钠中硅含量的测定。 按GB 11213.4进行。
e.工业用氢氧化钠钙镁总含量的测定(络合滴定法)。 按GB 209.4.6进行。
f.工业用氢氧化钠中汞含量的测定。 按GB 209.4.7进行。
3.2.1.2 生产工艺流程
萘系减水剂制备工艺流程简图如图3-19所示,但是在工艺设备布置上还有所不同,一般按其布置可分为平面和立体布置两种。在工艺设备上采用平面布置,物料在不同工艺设备间利用蒸汽压送(或压缩空气)或泵来输送,这种布置的特点是厂房高度较低,建筑安装较快,缺点是物料的传输需要压送或泵送,操作较麻烦,有时也容易出现一些事故。设备采用立体布置,是将不同的工艺设备布置在不同层高的平面上,物料在不同工艺设备之间传输,可以自上而下的自流输送,这种布置方式在厂房高度较高时适用,但生产时操作较方便,避免了物料传输过程中压送或泵送,自动化生产企业采用此种布置的较多。

图3-19 萘系减水剂生产工艺流程简图
在熔萘方面采用的方式也不一样,有的企业将固体萘经计量后直接加入磺化釜,经加热熔化,再加酸磺化;有的企业将固体萘直接加入专用熔萘釜,将熔化了萘计量后再加入磺化釜磺化,磺化结束后,放入缩合釜水解,然后加入甲醛缩合。在缩合工艺上,目前采用的有两种工艺:一是常压缩合;二是带压缩合。常压缩合的缩合时间较长,为4.5~6h,带压缩合在温度较高的条件下进行,反应较快,缩合时间较短,为2~3h。目前多数企业采用的是常压缩合,少数企业采用带压缩合。缩合过程中,加甲醛的方式也有所不同:一种是将甲醛在规定时间内缓慢滴加方法;另一种是将甲醛分次加入,缓慢滴加方式较易于控制生产。在中和工艺上,根据企业对产品控制,一种是生产低浓产品,中和时全部用烧碱中和,这样生产出的产品为萘磺酸钠甲醛缩合物和硫酸钠的混合物,其中硫酸钠的含量在15%~25%之间;另一种是中和的方法,先加入部分烧碱,将溶液的pH值控制在1~2之间,再加石灰水中和,这样石灰水中的氢氧化钙与过剩的硫酸反应生产硫酸钙,由于硫酸钙的溶解度较小,沉淀析出,可以采用板框压滤机或卧式螺旋沉降离心机过滤,除去硫酸钙,最终产品中硫酸钠的含量较低,一般小于5%,产品称为高浓产品。目前市场上有的厂家将硫酸钠含量控制在10%以内,这类产品一般称为中浓产品。目前常用的干燥方式有两种:一种是喷雾干燥;另一种是离心干燥。喷雾干燥系统,设备费用较低,设备维修简单。离心干燥系统设备费用较贵,设备维修费较贵。建厂时采用什么工艺布置,除根据工厂规模和技术要求外,经技术分析对比后确定。
3.2.1.3 萘系减水剂生产的主要设备
萘系减水剂由于生产工艺设备布置方式不同,所采用的设备略有不同(表3-20)。
表3-20 萘系减水剂生产的主要设备

3.2.1.4 生产操作
萘系减水剂生产操作步骤简述如下。
① 将经过计量的工业萘加入反应釜中,密闭反应釜,加热使萘熔化,温度达90~100℃时,启动反应釜搅拌桨。
② 当温度升至规定温度时,滴加或分次加入计量的硫酸,加完酸后,将温度控制在160~165℃,保温2~3h。
③ 从反应釜内取样,测定磺化物的总酸度,当总酸度符合要求时,开始降温。
④ 当温度降低120℃时,加入经过规定量的水进行水解,搅拌0.5h。
⑤ 检测水解后的总酸度,当总酸度符合要求时,继续降低温度到90~100℃。
⑥ 在规定时间内将经计量的甲醛滴加或分次加入反应釜,将物料温度控制在规定的温度范围内,保温若干小时。
⑦ 缩合完毕,将物料放至中和釜,加碱或加碱和石灰水中和,控制中和物的pH值在7~9范围内。
⑧ 若生产高浓产品时,应将中和物过滤,除去硫酸钙,经浓缩和干燥(若生产液体产品可以不浓缩和干缩)。
3.2.1.5 生产控制要求
(1)磺化反应
磺化反应是浓硫酸作用于萘,其磺酸根SO2OH取代萘分子中的氢原子,反应结果生成萘磺酸。
磺化反应控制的好坏,直接影响β-萘磺酸的含量,对缩合后的产品质量影响较大。影响反应的因素主要有磺化温度、磺化时间、硫酸浓度及杂质等。
① 萘与硫酸的用量比 萘与硫酸的摩尔比一般控制在1∶(1.2~1.6)之间。为了提高转化率,使反应体系中的萘充分反应,硫酸应是过量的。
② 磺化温度 在磺化反应中,温度不仅影响反应速率,更主要的是影响反应产物。萘的磺化是一个复杂过程,极易生成异构体。高效减水剂生产所需的是β-萘磺酸,该产物在160~165℃磺化时生成效率最高。反应温度与β-萘磺酸转化率的关系见表3-21。若温度过高,则硫酸的氧化性增加,萘核多处被磺化或形成硫砜。
表3-21 反应温度与β-萘磺酸转化率的关系

因此,在磺化反应中,先将萘投入反应釜,加热熔化,升温到适当温度后再加入浓硫酸,最终将物料温度控制在160~165℃。
③ 磺化时间 加完硫酸后,应在160~165℃恒温1.5~2.5h,时间短磺化不充分,磺化时间过长会影响产量。萘磺化时的同分异构化如图3-20所示。

图3-20 萘磺化时的同分异构化
④ 提高磺化反应效果的措施
当反应平衡时有如下关系:
式中 Ke——平衡常数,在一定的反应条件和一定的温度下是常数;
[N]——原料萘的原始浓度,mol/L;
[H2SO4]——原始硫酸的原始浓度,mol/L;
[β-NS]——产物β-萘磺酸的浓度,mol/L;
[H2O]——产物水的浓度,mol/L。
由上式可知,由于在一定温度下Ke是常数,故提高[β-NS]有两种方法。
a.提高[H2SO4] 在[N]保持一定的条件下,若要提高[β-NS],则只有相应提高[H2SO4]。提高[H2SO4]的方法有:
ⓐ 增加酸的浓度,最好用发烟硫酸,则加同样的酸量,可使[H2SO4]提高;
ⓑ 增加用酸量,同样浓度的酸,用量大,则[H2SO4]也提高。
上述方法中以ⓐ为好,ⓑ虽也可行,但废酸多,中和时NaOH用量大,产品中Na2SO4含量高。
b.减少[H2O] 在[N]和[H2SO4]保持一定的条件下,若要提高[β-NS],则只有相应减少[H2O]。减小[H2O]的方法有:
ⓐ 在反应混合物中加入无水硫酸钠,使游离水变成结构水,减小[H2O]。
ⓑ 用低沸点有机或萘蒸气将水汽带走。这些方法都比较昂贵、费事。采用98%硫酸,适当增加酸量的方法达到提高[β-NS]的目的。
(2)水解反应
① 水解目的 在磺化反应时,除生成β-萘磺酸时,还生成一部分α-萘磺酸,为了有利于下一步的缩聚反应,将反应物降温至120℃左右,此时β-萘磺酸稳定,α-萘磺酸而易水解。
② 水解用水量 水解用水量,可以根据水解前后的总酸度的高低通过计算来确定,也可以根据实践经验确定。
水解时加水量多对水解反应有利,但加水量多给缩聚反应带来不利影响。
③ 水解总酸度 水解时,控制其总酸度在26%~30%,水解总酸度低,加水量大,降低反应物浓度;水解总酸度高,缩合时物料黏度大,不利于反应进行。
④ 水解时间 一般加水搅拌半小时左右。
3.2.1.6 缩合反应
萘磺酸水解后接着降温到90~100℃,滴加甲醛缩合,其反应方程如下。
缩合反应是减水剂生产过程中的重要反应,也是时间较长的一个工序。技术关键是使反应尽可能彻底,得到较长链的缩合物;同时反应时间尽可能短,以便缩短生产周期。
影响缩合反应的因素很多,主要有配比、加水量、酸度、反应时间及反应温度。
(1)甲醛用量 甲醛用量大,利于得到多核分子,提高产品质量,但缩合时间要加长,以使反应完全。由于磺化反应的副反应,萘不会全部磺化为β-萘磺酸,故在密封较好、控制严格的生产条件下,甲醛用量可适当减少。甲醛用量一般与萘的摩尔比为1∶(0.95~1.0)。具体用量根据试验结果确定。
(2)缩合温度 缩合温度一般在100~110℃。在有压力时选择较高的温度,温度较高时,反应速率随之加快,可以较快地趋向于平衡;有利于高聚合物的形成。但因缩合反应为逐步反应,如温度过高,反应过快,则有可能发生“爆聚”,生成大量短链分子,不易获得均一分布的多核分子,所以在稍低温度下,延长恒温时间,有可能得到分布均一的多核产物。
(3)缩合酸度 硫酸是萘磺酸缩合的催化剂,具有酸度低时反应物料较稀薄等优点,但产品的分散性较差。酸度高有利于缩合反应的进行。但酸度过高,缩合反应不易控制,有时会引起“爆聚”,一般酸度应控制26%~30%之间。
(4)常压与带压缩合 因为常压下缩合反应速率慢、时间长,温度不能超过110℃;采用带压缩合,则反应可达较高温度,反应时间较短。
(5)缩合反应时间 采用常压缩合时,一般反应时间为4~5h,时间过短反应不完全,过长又使生产周期延长,成本增高,产率降低。带压缩合,反应时间为2.0~2.5h。
(6)中和 缩合物中的磺酸和剩余的硫酸用烧碱、石灰水等物料中和,其可转化为对应的钠盐、铵盐、钾盐、锂盐,钙盐,但常转化为钠盐。过量的硫酸也可转化为钠盐。生产减水剂时常用这两种中和方法。
3.2.1.7 生产中有关问题的处理
(1)磺化终点不到
磺化终点可检验磺化反应是否完全,检验方法:①测酸度;②看磺化物水溶液是否有油状物,如酸度符合要求,又无油状物,则反应是完全的,否者是不完全的。原因有:
① 加酸量不足,必须补加酸,再进行磺化;
② 反应温度低,必须提高反应温度到160~165℃,延长保温时间;
③ 保温时间不够,延长保温时间。
(2)缩合过程中溢锅或喷料
常压缩合时,若升温缓慢,温度不超过100℃,不会发生釜内物料喷溢事故,反之则会发生喷料事故,特别是带压缩合更易发生。
发生喷料原因有:
① 加甲醛时温度过高,一般控制在90~100℃;
② 水解后的酸度过高,一般控制在26%~30%;
③ 升温过急,处理方法是立即向反应釜夹套加入冷却水,必要时用冷水浇淋反应釜盖,如果温度和压力仍激烈上升时,则可开启放料阀门立即放出部分物料,否则会造成严重后果;
④ 加甲醛速率过快,应缓慢滴加,一般控制在2.5~3.0h。
总之,缩合反应激烈,一定要小心谨慎。
(3)防止物料的固化
在缩合过程中,会出现物料突然变稠,致使搅拌困难,甚至停止,而使物料固化在反应釜内,需要人工清理,有时还会造成搅拌器和反应釜损坏。避免的方法是:
① 水解后酸度不能过高;
② 加甲醛速率不能过快,一定要缓慢滴加。
如反应过程中发现物料变稠、搅拌困难时,需要加入一定量的热水,将物料稀解。
3.2.1.8 主要原料消耗指标
由于各企业采用的配比不同,原材料消耗是有所差异的,萘系减水剂主要原料消耗见表3-22。
表3-22 萘系减水剂主要原料消耗

3.2.1.9 萘系减水剂性能
(1)物理性能
① 外观 液体——棕色至深棕色;粉状——淡黄色至棕色。
② pH值 7~9。
③ NaSO4 低浓度<25%;中浓度<10%;高浓度<5%。
④ 氯离子含量 与中和时所用碱的质量有关,一般氯离含量<1.0%。
⑤ 总碱量 一般低浓度<16%;高浓度<12%。
⑥ 表面张力 65~70mN/m。
(2)性能指标 萘系减水剂的性能指标见表3-23。
表3-23 萘系减水剂的性能指标

(3)萘系减水剂掺量对不同品种水泥浆体流动度的影响 试验选用了基准水泥PI42.5、PS32.5水泥、PP32.5和PO3.25水泥。水泥净浆的水灰比均为0.29,试验结果见表3-24。
表3-24 水泥净浆流动度与萘系减水剂掺量关系

试验结果表明,随着萘系减水剂掺量的增加,各种水泥的净浆流动度均有不同程度的提高。但火山灰水泥,在同等掺量的情况下水泥净浆的流动度低于其他水泥。当掺量在0.5%~0.75%时,水泥净浆的流动度增长较快。
(4)减水剂对水泥水化热影响
试验按标准规定方法进行,试验结果列于表3-25和图3-21。
表3-25 水泥水化热试验结果

注:1cal=4.18J。

图3-21 水泥水化曲线
1~3—表3-25中序号1~3
试验结果:PO42.5水泥掺萘系减水剂后,水泥水化热有所降低,放热峰出现时间延迟,有利于浇灌大体积混凝土工程。另外,掺萘系减水剂后,掺减水剂者较不减水剂者水化热降低更多。
(5)对混凝土性能的影响
① 对新拌混凝土性能的影响
a.对含气量和泌水率的影响 混凝土配合比为1∶2.3∶3.77,水泥用量310kg/m3,试验结果见3-26。由表3-26可见,对于上述各种水泥,掺入萘系减水剂,混凝土含气量略有增加,泌水率下降。
表3-26 萘系减水剂对混凝土含气量和泌水率的影响

注:水泥为基准水泥。
b.萘系减水剂对混凝土拌和物凝结时间的影响 采用贯入阻力法测定混凝土拌和物筛出砂浆的硬化速率,来确定混凝土的凝结时间。初凝贯入阻力为3.5MPa,终凝贯入阻力为28MPa。试验结果见表3-27。
试验结果表明,掺入萘系减水剂后,混凝土凝结时间虽稍有变化,但变化幅度并不大。在施工上不会有什么不利影响,可以和未掺加外加剂的混凝土一样作业,无需特殊要求。
c.掺萘系减水剂对混凝土拌和物的坍落度损失影响 在混凝土中掺入萘系减水剂,可以明显改善混凝土和拌和物的和易性,但对混凝土的坍落度损失也带来影响,一般来说,掺入萘系减水剂后,混凝土早期坍落度损失增大,试验结果见表3-27和图3-22。
表3-27 萘系减水剂混凝土拌和物凝结时间和坍落度的影响


图3-22 掺萘系减水剂混凝土坍落度损失
② 对硬化混凝土性能的影响
a.抗压强度 萘系高效减水剂掺量与减水率的关系见表3-28。
表3-28 萘系高效减水剂掺量与减水率的关系

b.对其他性能的影响 试验表明,掺入萘系减水剂的混凝土,在混凝土坍落度基本相同时,劈裂强度有所提高,混凝土弹性模量有所增大,收缩也有所增加。
(6)萘系高效减水剂的主要用途
① 萘系减水剂 作为一种主要的减水剂品种,它可作为各种复合减水剂的组分,根据对复合外加剂的要求,其在各种复合外加剂中的用量是不同的。
② 配制流动性混凝土 长期以来工程界所期望的目标是在保持水灰比相同时,可制备一种实际上可安全自流平的混凝土,在浇筑过程中或浇筑之后,混凝土不泌水,不离析和不降低强度。使用高砂率、高水泥用量和普通减水剂可部分达到目的,但有一定的局限性,混凝土的坍落度最高只能达到18cm左右。
选用初始坍落度为7.5cm的基准混凝土,掺入适量的高效减水剂,可以拌制坍落度超过20cm的流动混凝土,它与普通混凝土的根本区别在于:既能保持凝聚性,又极易流动而成自流平。
③ 配制减水高强混凝土 减水高强混凝土主要用于下列几个方面。
a.在预制构件生产中,利用其早强性能,有利提前脱模和剪断钢筋。大量试验表明,利用高效减水剂适当减水,减水混凝土与基准混凝土的强度相同时,减水混凝土3d就能达到基准混凝土的7d强度,减水混凝土7d就能达到基准混凝土的28d强度,这对提高劳动率,加速模板周转,增加产量非常有利。
b.可以生产C100的混凝土构件,并且可减少构件的损失。
c.用低水灰比配制大坍落度混凝土,更便于浇筑。
④ 生产降低水泥用量的混凝土 在相同的强度要求下,保持和易性和水灰比不变,由于高效减水剂的作用,促进了混凝土强度增长,每立方米混凝土的水泥用量随高效减水剂掺量的增加而减少。
3.2.2 蒽系减水剂
3.2.2.1 合成原理
蒽系减水剂以蒽油、甲醛、浓硫酸及液碱为主要原材料,其合成主要经历磺化反应、水解反应、缩合反应和中和反应。
(1)磺化反应
蒽易磺化,磺化反应极为复杂。蒽环上有α、β、γ位之分,如下图所示。γ位由于位阻效应,一般较难进行反应;α位电子云密度较大,比较容易磺化,磺化物也比较容易水解;而β位电子云密度小,较难磺化,磺化物也较难水解,所以发生磺化取代反应时,因反应条件不同就可形成α-蒽磺酸、β-蒽磺酸和蒽二磺酸等产物。由于蒽磺酸和甲醛的缩合是一个亲电缩合反应,而磺酸基是一个吸电子基团,会降低蒽环的反应活性。相比之下,α-蒽磺酸和蒽二磺酸等更易降低蒽环的反应活性,不利于缩合反应的进行。所以必须严格控制磺化反应,使其能得到较高比例的β-蒽磺酸,以使缩合反应较易进行,其磺化反应式如下:
(2)水解反应
水解反应主要是除去α-蒽磺酸和蒽二磺酸,否则会使缩合反应受影响,最终影响产品质量。水解温度控制在110~120℃,反应可进行得较完全。水解补水量应使补水后的物料酸度能够满足缩合要求,既不会因补水过多、酸度过低而导致缩合反应难以进行,但也不能因水解补水过少,缩合物料酸度过高,使缩合反应太快而难以控制,甚至出现物料溢锅和固化现象,水解反应式如图3-23所示。

图3-23 蒽磺酸水解反应式
(3)缩合反应
缩合反应是合成高效减水剂的关键反应。β-蒽磺酸与甲醛在酸作催化剂的条件下可发生缩合反应。催化剂的作用是将甲醛转化成反应性强的阳离子,即:CH2O+H3O+ CH2OH++H2O,然后这个阳离子再与β-蒽磺酸化合物反应。反应式如下:
(4)中和反应
采用液碱和石灰乳两步中和,得到聚亚甲基蒽磺酸盐,以降低产品中的硫酸钠含量,提高产品性能。中和时要控制好加碱速率,并调节好pH值。中和反应式如下:
3.2.2.2 蒽系减水剂的合成工艺
蒽系减水剂的生产工艺如下,
① 将计量好的蒽油投入反应釜中,升温至120~130℃开始搅拌,按配比以细流方式加入95%~98%的浓硫酸,同时启动水膜除尘装置吸收反应产生的酸性气体。
② 于135~140℃恒温磺化反应2h,取样测磺化酸度,根据酸度值计算水解补水量,在110~120℃水解30min。
③ 降温至80℃以下,以较慢的速率滴加甲醛,整个滴加时间不宜少于60min。在加甲醛的过程中若发现物料升温较快,应及时向釜内夹套通冷水降温。
④ 加完甲醛后,于80~85℃缩合反应3~4h,物料黏度很大时,应及时向釜内补少量水调节。
⑤ 将缩合好的物料放入中和槽中,先加液碱,再加石灰乳中和物料pH值至7~9,再将物料过滤除去硫酸钙沉淀。水剂物料可调节至一定含量制成水剂成品使用,也可干燥成粉剂成品,粉剂成品为深褐色。
合成工艺流程示意图如图3-24。

图3-24 合成工艺流程示意图
3.2.2.3 性能及应用技术
蒽系减水剂的主要成分为聚亚甲基蒽磺酸钠。磺酸盐类物质易溶解于水,溶解后均有离解作用,生成带有负电荷的有机阴离子及无机阳离子(Na+、Ca2+),因此它属于阴离子表面活性剂。离解后的阴离子两端性质不同,具有两亲性,即分子一端具有极性很强的亲水基团(磺酸基,—S),有较强的亲水性;另一端为有机烷链,属于憎水基团,随着烷链的加长,蒽系减水剂在水中的溶解度将变差。
蒽系减水剂分子有机链中的蒽环借助于分子间的引力和水泥颗粒作用,被平铺地吸附于水泥颗粒的表面,而作为一种聚合物电解质,其水溶液是一种亲液溶胶,亲液溶胶达到一定的浓度就形成网络结构。这种聚合物电解质的最基本特性是随着pH值的增加,溶液黏度成千百倍地增加,即由流动性变为凝胶状。当水泥颗粒吸附足够的减水剂后,借助于—S和水分子氢键缔合作用,再加上水分子之间的氢键缔合,便在水泥表面形成了一层溶胶膜。普通水泥本身是一种碱性较强的物质,当蒽系减水剂随水加入水泥中之后,由于这种碱性的作用,使网络结构的蒽系减水剂溶胶膜有结构黏性,因而形成的溶胶膜具有较强的稳定性,极大地减少了水泥颗粒间互相结合的可能性,阻碍了水泥颗粒的凝聚,形成更加稳定的分散体系。这样,只需很少量的水就易将水泥拌和均匀,从而达到减水目的。
蒽油和工业萘都为炼焦工业的副产品,蒽油原料供大于求,工业萘则供不应求,且蒽油的价格只有工业萘的30%左右。因此,蒽系减水剂作为一种非萘系高效减水剂,具有原料来源有保证、生产成本较低廉的特点。同时,生产过程采用水膜除尘装置吸收酸气,操作时无环境污染,适于规模生产。蒽系减水剂产品的减水、早强、增强效果明显。
3.2.3 氨基磺酸盐系减水剂
3.2.3.1 物理性能
氨基磺酸盐系减水剂是以对氨基苯磺酸钠、苯酚、甲醛为主要原料,在一定温度条件下经反应缩合而成的一种外加剂。
① 别名 氨基磺酸盐系减水剂,也被称为单环芳烃型高效减水剂。
② 英文名称 amino-aryl-sulphonate phenol formaldehyde condensate。
③ 分子结构 氨基磺酸盐系减水剂为氨基苯磺酸-苯酚-甲醛的缩合物。主链中苯酚和对氨基苯磺酸钠由亚甲基交替连接而成,在主链单环上接有—SO3H、—OH、—NH2和—COOH的亲水性官能团、烷基、烷氧基等取代基,结构式如图3-25所示。

图3-25 氨基磺酸盐分子结构
3.2.3.2 生产用的主要原料及控制指标
生产中所用的主要原材料及控制指标表3-29。
表3-29 生产中所用的主要原材料及控制指标

3.2.3.3 生产工艺
(1)氨基磺酸盐生产工艺
氨基磺酸盐减水剂生产工艺流程如图3-26所示。

图3-26 氨基磺酸盐减水剂生产工艺流程
首先使磺化单体——对氨基苯磺酸钠与苯酚在反应釜中溶解,然后缓慢加入甲醛进行缩合反应,缩合反应结束后降温,恒温搅拌,加碱溶液进行中和,然后出料制得成品。制备时,单体、苯酚和甲醛不能同时投放,应在偏酸性条件下进行缩合反应,然后在碱性条件下进行分子重排反应,最终产品的pH值要大于等于10.5,缩合生产所用的摩尔比、缩合温度以及酸度等因素均会影响产品质量,应通过试验研究找出最佳值,才能合成优质的产品。
① 苯酚与甲醛的加成反应 苯酚与甲醛加成反应时,发生羟甲基化反应,其反应式如下。
如果甲醛足够多,甲醛会继续进攻一羟甲基苯酚的另一个邻位,生成二羟甲基苯酚,其反应式如下。
影响苯酚羟甲基化的主要因素如下。
a.反应介质的酸碱度 pH值过高,甲醛会发生坎尼扎罗副反应。
b.反应时间 时间短,转化率低,羟甲基化不完全。
c.投料比例 两种物质的摩尔比将影响生成物的分子结构。
② 对氨基苯磺酸钠与甲醛的加成反应 反应式如下。
如果甲醛量足够多,甲醛会继续进攻一羟甲基对氨基苯磺酸钠的氨基的另一个邻位,生成二羟甲基对氨基苯磺酸钠,其反应式如下:
③ 缩聚反应 缩聚反应发生在羟甲基苯酚与羟甲基对氨基苯磺酸钠之间,生成大分子聚合物,其主要结构式表示如下:
氨基磺酸系高效减水剂分子结构中含有多种极性基团,分子极性较强。产品浓度为35%左右时为棕红色液体。
(2)生产控制要领
① 氨基苯磺酸钠与苯酚的配比。
② 甲醛用量对分散性能的影响。甲醛在三元共聚中起桥梁连接作用,甲醛的加入量对产品性能有重要的影响。
③ 反应体系的酸碱度对产品分散性能的影响。pH值控制在7.5~8.5时为最佳。
④ 反应温度对产品分散性能的影响。一般反应温度控制在75℃左右,水泥浆体的初始流动性好及经时损失小。
⑤ 反应时间对产品分散性能的影响。通常将反应时间控制在3~5h。
3.2.3.4 原材料大致消耗
(对氨基苯磺酸钠+苯酚)∶甲醛约为1∶(2~2.5)(摩尔比),原材料的吨耗见表3-30。
表3-30 氨基磺酸系高效减水剂原材料吨耗

3.2.3.5 氨基磺酸系高效减水剂主要性能特点
(1)氨基磺酸系高效减水剂(氨基磺酸盐)的表面性能特征
混凝土减水剂大多数是表面活性剂,其表面性能不仅影响其减水效果,而且能揭示其减水作用机理,故而引起众多学者的关注和兴趣。华南理工大学的蒋新元等采用对比的方法较为系统地研究了氨基磺酸系高效减水剂(简称氨基磺酸盐)与萘磺酸盐甲醛缩合物高效减水剂(简称萘系)的表面性能特征与差异。
① 氨基磺酸盐的表面张力 配制不同浓度的减水剂试样溶液,用70545型表面张力仪采用拉膜法测表面张力,试验结果如图3-27所示。由图可知,两种高效减水剂溶液的表面张力都随着溶液浓度的增大而减小,但减小的幅度都很小。

图3-27 表面张力与减水剂浓度的关系
② 氨基磺酸盐的起泡性能 起泡性能是表面活性剂的一个重要性质,其内涵包括起泡力和泡沫稳定性。起泡力是指泡沫形成难易程度和产生泡沫量的多少;泡沫稳定性是指产生泡沫的持久性,即消泡的难易程度。试验测定了一定浓度氨基磺酸盐和萘系溶液的起始泡沫高度及5min后泡沫高度,以分别表示其起泡和泡沫稳定性,测试结果见表3-31,氨基磺酸盐和萘系两者起泡能力与泡沫稳定性均较差,可以认为两者均属于非引气型高效减水剂。
表3-31 氨基磺酸盐与萘系的起泡性能

③ 氨基磺酸盐在水泥颗粒表面的吸附量 由氨基磺酸盐与萘系两种高效减水剂在水泥颗粒表面吸附量的试验结果可见,在低浓度下,两种高效减水剂的吸附量均随着减水剂浓度的增大而明显增加,萘系更为明显。当浓度大于2.5g/L时,吸附量则随着减水剂浓度的增大而缓慢增加,达到饱和吸附量,氨基磺酸盐的饱和吸附量比萘系的要小,如图3-28所示。

图3-28 减水剂在水泥颗粒表面的吸附曲线
上述研究结果表明,氨基磺酸盐属于非引气型的高效减水剂。
(2)氨基磺酸系高效减水剂(氨基磺酸盐)的分散性能特征
根据有关科技人员的研究,氨基磺酸系高效减水剂(简称氨基磺酸盐)的分散性能特征主要表现在如下几方面。
① 氨基磺酸盐的减水分散效果 在水灰比为0.28时,不同掺量氨基磺酸盐和萘系的水泥净浆流动度及水泥净浆流动度随时间变化关系的试验结果分别如图3-29和图3-30所示。

图3-29 减水剂的掺量对水泥净浆流动度的影响

图3-30 水泥净浆流动度随时间的变化
由图3-29可知,当减水剂的掺量增大时,水泥净浆均基本不能流动,掺量超过0.2%后,掺氨基磺酸盐的水泥净浆流动度远大于掺萘系的水泥净浆流动度;当掺量为0.5%时,掺氨基磺酸盐的水泥净浆流动度高达280mm,而掺萘系的净浆流动度只有166mm。
由图3-30可知,掺入萘系的水泥净浆经过90min后流动度从208mm降到64mm,水泥浆体几乎不能流动,流动度完全损失;而掺入氨基磺酸盐的水泥净浆流动度在60min内反而有所增加,120min后才从220mm降到208mm,相对流动度损失率仅为7.7%,远小于萘系。说明氨基磺酸盐高效减水剂具有良好的分散性能及较长时间防止流动度损失的能力。
② 氨基磺酸盐对水泥颗粒表面ζ电位的影响 不同浓度氨基磺酸盐和萘系的水泥悬浮体系的ζ电位的测试结果如图3-31所示,由图可知,加入氨基磺酸盐和萘系后,随着减水剂浓度的增大,ζ电位由正变负且绝对值增大,当浓度增大到一定值时,ζ电位增加缓慢。未水化的水泥颗粒表面的ζ电位在10mV左右,而掺加氨基磺酸盐和萘系后水泥颗粒表面的ζ电位分别为-20~-10mV和-40~20mV。故掺入高效减水剂后,水泥粒子间排斥力相应大大增加,从而使水泥净浆流动度大大增加。

图3-31 水泥颗粒表面ζ电位与减水剂浓度的关系
③ 氨基磺酸盐对水泥颗粒表面ζ电位稳定性的影响 掺氨基磺酸盐和萘系的水泥悬浮体系的ζ电位随时间变化规律的试验结果如图3-32所示,由图可知,虽然掺萘系的水泥颗粒表面起始ζ电位很高,但是随时间的推移,ζ电位下降很快,掺氨基磺酸盐的水泥颗粒表面ζ电位起始要比掺萘系的小,但是随时间的变化较小,所以掺氨基磺酸盐的水泥净浆流动度经时损失要比掺萘系的小;水泥颗粒表面ζ电位与减水剂浓度的关系如图3-32所示。通过上述研究结果,表明氨基磺酸系高效减水剂是一类高性能减水剂。

图3-32 掺不同减水剂的水泥颗粒表面ζ电位与时间的关系
(3)氨基磺酸系高效减水剂(氨基磺酸盐)优良性能主要表现氨基磺酸系高效减水剂(简称氨基磺酸盐)是继萘系、三聚氰胺系高效减水剂之后,新近开发的新型高效减水剂,它克服了萘系、三聚氰胺系高效减水剂在低水灰比下流动性差、坍落度损失大等弊病。
采用对比实验,比较氨基磺酸盐与萘系高效减水剂的减水分散作用,其结果如下。
① 掺量对水泥净浆流动度的影响 如图3-33所示,为水灰比0.38时不同掺量氨基磺酸盐和萘系的水泥净浆流动度的试验结果。由此可知,当减水剂的掺量增大时,水泥净浆流动度也增大,掺氨基磺酸盐的水泥净浆流动度明显大于掺萘系者,在掺量为0.1%时,前者净浆流动度为220mm,而后者为190mm;当掺量增至0.5%时,前者高达330mm,而后者只有290mm。由此可见,氨基磺酸盐是一种具有高流动性作用的高效减水剂。

图3-33 减水剂的掺量对水泥净浆流动度的影响
② 掺量对水泥净浆减水率的影响 在保持水泥净浆流动度相同时,测定两种减水剂的水泥净浆减水率,其结果如图3-34所示。两种减水剂的减水率均随掺量的增加而增大;在相同掺量下,氨基磺酸盐的减水率明显高于萘系。掺量为0.5%时,前者减水率高达24%,而后者只有10.5%,当掺量大于0.5%时,氨基磺酸盐减水率增加缓慢,故其适宜的掺量在0.5%左右。

图3-34 减水剂的掺量对水泥净浆减水率的影响
③ 水灰比对水泥净浆流动度的影响 低水灰比是保证混凝土高性能的关键因素,因此在低掺量条件下,既能满足混凝土性能要求,又能实现低水灰比,是衡量减水剂性能优良的重要指标。在掺量为0.5%、相同净浆流动度条件下,掺氨基磺酸盐的水灰比要比掺萘系的低很多。水灰比低至0.19%时,掺氨基磺酸盐的水泥净浆仍具备200mm的流动度,而掺萘系的已不能流动,如图3-35所示。表明氨基磺酸盐的掺入,可以保证混凝土在低水灰比时仍能保持良好的工作性。

图3-35 水灰比对水泥净浆流动度的影响
3.2.3.6 氨基磺酸盐对混凝土性能的影响
(1)对混凝土坍落度损失的影响
表3-32为掺氨基磺酸盐和萘系混凝土坍落度经时损失值的试验结果。在两种常用掺量条件下,掺氨基磺酸盐混凝土的坍落度在60min内几乎没有变化,而在120min后仅分别降低2.5cm和2.0cm,说明氨基磺酸盐可有效控制混凝土坍落度经时损失。
表3-32 掺氨基磺酸盐和萘系混凝土坍落度经时损失值的试验结果

注:混凝土配合比为水泥∶砂∶碎石=1∶2.27∶3.58,水泥用量为325kg/m3。
(2)氨基磺酸盐对水泥与混凝土的缓凝作用强
试验测定了两种减水剂在0.5%掺量条件下,水泥净浆与混凝土的凝结时间,并分别与基准水泥和混凝土的凝结时间进行了对比。由表3-33可知,掺萘系的水泥初凝时间和基准差不多,而终凝时间延长1h左右;而掺氨基磺酸盐者初凝、终凝时间分别为400min和875min。
表3-33 氨基磺酸盐和萘系对水泥凝结时间的影响

由表3-34数据可知,掺萘系混凝土初凝时间和基准差不多,而终凝时间略有提前;掺氨基磺酸盐者初凝、终凝时间分别为590min和920min,说明氨基磺酸盐是缓凝性能很强的高效减水剂。
表3-34 氨基磺酸盐和萘系对混凝土凝结时间的影响

注:混凝土配合比同表3-27掺氨基磺酸盐和萘系混凝土的坍落度经时损失值。
(3)氨基磺酸盐对硬化混凝土性能的影响
抗压强度是混凝土最重要的力学性能之一。表3-35列出了基准混凝土、掺量为0.5%时氨基磺酸盐和萘系混凝土3d、7d、28d龄期的抗压强度及抗压强度试验结果,由表中数据可见,掺高效减水剂是提高混凝土强度的有效措施。而氨基磺酸盐对混凝土减水作用更强,对强度提高更明显。
表3-35 氨基磺酸盐和萘系对混凝土的减水增强效果

注:混凝土配合比同表3-32氨基磺酸盐和萘系混凝土的坍落度经时损失值。
3.2.4 脂肪族羟基磺酸盐系减水剂
3.2.4.1 物理性能
脂肪族羟基磺酸盐系减水剂是以羰基化合物为主要原料,经缩合得到的一种脂肪族高分子聚合物。
别名:脂肪族羟基磺酸盐系减水剂称为磺化丙酮甲醛树脂,又称为酮醛缩合物。
英文名称:aliphatic hydroxy sulphonate condensate。
分子结构:脂肪族高效减水剂的结构特点是憎水基主链为脂肪族的烃类,而亲水基主要为—SO3H、—COOH、—OH等,结构式如下:
3.2.4.2 生产所用主要原材料及其控制指标
生产所用主要原材料及其控制指标见表3-36。
表3-36 生产所用主要原材料及其控制指标

3.2.4.3 脂肪族羟基磺酸盐系减水剂生产工艺
脂肪族减水剂生产工艺流程如图3-36所示。

图3-36 脂肪族减水剂生产工艺流程
(1)生产工艺流程简述
① 先将计量好的甲醛加入RA釜,再接着加入一定量的亚硫酸氢钠,用甲醛溶解亚硫酸氢钠,待充分溶解后,可以通过观察釜里有无硬块状物质来判断。
② 在约30℃加入计量好的丙酮,使其反应,注意控温(一般情况下加丙酮期间温度会持续在30~35℃,最高不超过40℃),加丙酮时间约为30min,加完后反应约30min。
③ 反应均匀后得到磺化产物PA。
④ 然后往RB釜里加入计量的水,接着投放焦亚硫酸钠,待其搅拌溶解后,加入片碱(用水事先溶解片碱),在此过程中注意控温,由于加碱过程为放热反应,温度会上升,控温≤60℃。
⑤ 反应均匀后得到磺化产物PB。
⑥ 在PA料温为30℃、PB料温为60℃时,将PA慢慢地加入PB中,注意控温≤90℃,并观察物料颜色变化,料色由乳白色变为红棕色时,即为变色反应。
⑦ 在95~100℃缩合保温2~3h,降温到40~50℃即得成品。
成品为红棕色液体,有一定黏性,固含量为35%~40%;本品与萘系高效减水剂、缓凝组分复配使用具有良好的控制混凝土坍落度损失的效果,推荐掺量为1.5%。
(2)操作要领
① 严格按照生产流程顺序依次投料。
② 亚硫酸氢钠呈块状,投料前必须将其粉碎成直径≤5cm的小块,以免对磺化产物的质量产生严重影响(目的是使亚硫酸氢钠完全溶解)。
(3)控制要领
① 由于丙酮具有一定的危险性,所以要缓慢加入,切忌急躁。
② 加片碱前,应事先用水溶解,注意控温≤60℃(原因是放热反应,温升较快)。
③ 缩合保温时间应在2~3h,小于2h,流动性与减水性能均差;大于3h,流动性与减水性能变弱,而且物料过黏,易产生网状絮凝结构,引发交联。
3.2.4.4 原材料大致消耗
甲醛∶亚硫酸氢钠∶丙酮=2∶0.7∶1(摩尔比),原材料消耗见表3-37。
表3-37 脂肪族羟基磺酸盐系减水剂原材料消耗

此生产工艺同时采用亚硫酸钠和焦亚硫酸钠,生产工艺较为复杂。目前此类产品,有的企业生产时,只采用亚硫酸钠或焦亚硫酸钠;有的企业在此类产品生产时,改变生产工艺过程,采用无热源生产工艺(即生产时,充分利用反应放热,无再由外部加热),从节能降耗来说,这是一个值得提倡的生产工艺。
3.2.4.5 脂肪族羟基磺酸盐系减水剂的性能
(1)对水泥净浆性能的影响
用脂肪族高效减水剂与萘系高效减水剂、氨基磺酸盐高效减水剂、三聚氰胺系减水剂和聚羧酸系高性能减水剂进行净浆流动度对比试验,检验其减水塑化效果,结果见表3-38。流动指数F=(D2-602)/602,D为水泥净浆扩展直径。水泥为基准水泥,水灰比为0.29,外加剂掺量以水泥质量分数,按固体有效成分计。脂肪族磺酸盐高效减水剂在相同掺量下,流动度高于萘系高效减水剂。
表3-38 掺不同减水剂的水泥净浆流动度

针对出厂水泥温度高的情况,测定了不同水泥温度下净浆流动度情况,结果如图3-37所示。实验采用了京都42.5和新港42.5普通硅酸盐水泥,水泥的温度为22~80℃,W/C=0.35,脂肪族磺酸盐高效减水剂的掺量为水泥重量的0.62%。结果表明,随着温度的升高,京都水泥的流动度从255mm下降到239mm,下降约6%,而新港水泥的流动度从226mm下降到110mm,降低51%。

图3-37 水泥温度对其流动度的影响
(2)对混凝土性能的影响
① 对凝结时间与泌水率的影响 掺加脂肪族磺酸盐高效减水剂的混凝土的凝结时间略有缩短,其初凝、终凝时间分别比空白混凝土提前26min和54min,符合高效减水剂标准中规定的凝结时间要求。由于掺加脂肪族高效减水剂能够大幅度降低水泥浆的黏度,新拌混凝土在水灰比较大时容易出现泌水现象,可以采用适当的黏度调节成分或引气剂复合使用。
② 脂肪族高效减水剂对混凝土性能的影响 按照GB 8076—2008混凝土外加剂试验方法,测定其减水率。由图3-38可见随着脂肪族减水剂掺量的增加,减水率表现出成比例增加的趋势,而且在低掺量下即具有较强的减水分散效果。在混凝土坍落度保持不变的条件下,强度增长明显。3d、7d和28d的强度随脂肪族磺酸盐掺量呈现出线性的增长规律,与减水率随掺量的变化规律相同(图3-38),说明脂肪族磺酸盐高效减水剂具有良好的增强效果。3d、7d及28d强度统计数字如图3-39和图3-40所示,含气量统计如图3-41所示。

图3-38 减水率、抗压强度与掺量的关系

图3-39 3d抗压强度统计结果

图3-40 7d和28d抗压强度统计结果

图3-41 含气量统计结果
③ 脂肪族磺酸盐与萘系高效减水剂的强度与含气量比较 采用同一批水泥,同样的配合比,在控制坍落度相同条件下,试验测定了基准混凝土、掺脂肪族磺酸盐高效减水剂的混凝土和掺萘系高效减水剂的混凝土的含气量与各龄期抗压强度,共进行10批次试验。结果表明,掺脂肪族磺酸盐高效减水剂的混凝土平均含气量(1.85%)低于掺萘系高效减水剂的混凝土平均含气量(2.15%)。掺脂肪族磺酸盐高效减水剂的混凝土3d、7d和28d的强度较基准混凝土分别提高44.4%、35%和28%,分别高于掺萘系高效减水剂的34%、23%和21%。可见脂肪族磺酸盐高效减水剂具有较好的增强效果,引气量低于萘系减水剂。
与萘系高效减水剂相比,脂肪族高效减水剂生产工艺简单,周期短,成本低,性能价格比高,减水分散能力强,不缓凝,引气量低,增强效果好,具有很好的推广应用前景。
3.2.5 三聚氰胺高效减水剂
3.2.5.1 物理性能
三聚氰胺高效减水剂是一种水溶性的高分子聚合物树脂,20世纪60年代初由德国研制,主要用于水泥、石膏和无机胶凝材料添加剂,对水泥有分散减水作用,能大幅提高初期强度,目前在一些国家已得到广泛应用。
别名:三聚氰胺高效减水剂又称为蜜胺系高效减水剂,光亮剂,化学名称为2,4,6-三氨基-1,3,5-三嗪(系统命名法)。
英文名称:sulfonated melamine formaldehyde(SMF) condensate,melment。
分子结构:
3.2.5.2 生产中所用的主要原材料及控制指标
生产中所用的主要原材料及控制指标见表3-39。
表3-39 生产中所用的主要原材料及控制指标

3.2.5.3. 三聚氰胺高效减水剂
三聚氰胺高效减水剂工艺流程如图3-42所示。

图3-42 三聚氰胺高效减水剂工艺流程
由三聚氰胺、甲醛和亚硫酸氢钠按摩尔比1∶3∶1在一定反应条件下缩聚反应而成。由图3-34可知,生产工艺分三个阶段:单体合成,单体磺化,单体缩聚。
(1)单体合成(三羟甲基三聚氰胺)
单体合成是将三聚氰胺和甲醛在碱性介质中进行加成反应,生成三羟甲基三聚氰胺。反应是不可逆的放热反应,反应产物的特性与反应速率和原料的摩尔比及反应条件有关。在酸性条件下将快速生成树脂,产生胶凝化。在中性或碱性介质中,则生成三羟甲基三聚氰胺,因此实际生产时pH值控制在8.5下进行。
(2)单体磺化
三羟甲基三聚氰胺的磺化采用亚硫酸氢钠、亚硫酸钠或焦亚硫酸钠作磺化剂,反应在碱性介质中进行。
(3)单体缩聚
三聚氰胺羟甲基磺酸钠的缩聚反应,介质的pH值起决定作用。反应在弱酸性介质中进行,羟甲基之间缩合成醚键。这样羟甲基三聚氰胺单磺酸钠单体之间以醚键连接成线型的树脂(分子量为3000~30000)。
3.2.5.4 操作要领
① 单体聚合中三聚氰胺和甲醛在碱性介质中进行加成反应。
② 单体磺化应在碱性介质中进行。
③ 单体缩聚应在弱酸性条件下进行。
3.2.5.5 原材料大致料耗
三聚氰胺∶甲醛∶亚硫酸氢钠(或焦亚硫酸钠)=1∶3∶1(摩尔比),原材料消耗见表3-40。
表3-40 三聚氰胺系高效减水剂原材料消耗(固含量为38%)

3.2.5.6 三聚氰胺系高效减水剂对混凝土性能的影响
(1)对新拌混凝土性能的影响
① 减水率 对普通水泥而言,当掺量为水泥质量的1.5%~2.0%时,最大减水率可达到25%。
② 凝结时间 混凝土或砂浆的凝结时间,不论是初凝还是终凝都是以加入量1%的影响为最小。
(2)对硬化混凝土性能的影响
① 强度 三聚氰胺系高效减水剂的减水作用很大,对混凝土强度有很大改善,抗折、抗拉、抗压或弹性模量都有较大的增强效果。
强度的增长率以掺1.0%~2.0%为最大,初期强度,特别是1d强度比基准混凝土要提高2~3倍,远远超过掺2% CaCl2的早强剂的效果,所以三聚氰胺系高效减水剂作为早强剂也是有效的。其强度检验结果见表3-41。
表3-41 不同品种减水剂对混凝土性能的影响

在保持水灰比不变时,超量掺加,即使加入10%,强度降低也是微小的,加入到4%强度还有一定的增长,这一点值得注意。
② 混凝土的水密性 在工作性相同时,掺1%三聚氰胺系高效减水剂,由于水灰比降低,混凝土更加致密,水密性得到改善,一般掺三聚氰胺系高效减水剂混凝土的渗水高度仅为基准混凝土的一半左右。
③ 干缩性能 掺入三聚氰胺系高效减水剂混凝土的收缩与掺木质素磺酸盐减水剂的混凝土相比,其收缩约为掺木质素磺酸盐减水剂的混凝土的一半。
④ 耐热性能 应用于矾土水泥时,提高了其混凝土的耐热性能,加热至200℃时,强度几乎没有变化。
⑤ 其他性能 掺入三聚氰胺系高效减水剂混凝土对钢筋的黏结力、抗冻融性能、抗碳化性能、抗耐磨性能均有所提高。
3.2.5.7 应用
① 用于蒸汽养护混凝土制品时,可大幅度缩短蒸养时间,节省能源。
② 三聚氰胺系高效减水剂用于矾土水泥,在改善工作性和增强效果方面与普通水泥一样,但矾土水泥用于耐热混凝土,可以降低矾土水泥混凝土在300~400℃时的强度损失。
③ 用于清水混凝土,改善其外观,减少混凝土装饰工作量。
④ 用于防水砂浆和混凝土,可以防止由于加入防水剂引起的强度降低,还可增加防水效果。
⑤ 用于彩色砂浆,也可防止由于加入着色剂而降低强度,且可使色彩鲜艳,还可以防止起“白霜”。
⑥ 三聚氰胺系高效减水剂用于石灰砂浆,不但可以增强,而且可改善表面硬度、耐磨和耐热性能。
⑦ 三聚氰胺系高效减水剂与其他外加剂的适应性好,可用于配制多种复合型外加剂,如泵送剂、防冻剂等。
3.2.6 古马隆系高效减水剂
1890年,作为松香的代用品,古马隆——茚树脂(简称古马隆树脂)首先用于大量生产人造树脂,广泛应用于建材工业、涂料工业与橡胶工业。特别20世纪90年代开发利用其作为原料,合成高效减水剂的研究备受人们青睐。它的连锁产品,各类溶剂油、洗油、炭黑油等广泛地应用于涂料、农药、橡胶及炼焦等行业。古马隆树脂高效减水剂属于水溶性树脂磺酸盐(国内有些文献将其划属三聚氰胺类),其合成主要原料有古马隆树脂、硫酸、四氯化碳、甲醛溶液、氢氧化钠。原料古马隆树脂质量对制得的古马隆系减水剂的性能影响很大。
3.2.6.1 古马隆系高效减水剂的合成步骤及工艺流程
(1)磺化
将250g的古马隆树脂粉末溶于400mL四氯化碳中,然后在溶液中加入50mL 98%的硫酸进行磺化。在60℃下,搅拌2h。
(2)聚合
在80℃下,往磺化产物中缓慢滴加36mL 36%的甲醛溶液,搅拌30min后加入100mL水,再保温24h。
(3)中和
在冰浴下,用25%的氢氧化钠溶液调节体系的pH值至中性。在50℃的真空环境下,将混合液浓缩,干燥。其固体产物被研磨成粉末。
(4)古马隆系高效减水剂的工艺流程
古马隆系高效减水剂的合成过程为磺化、聚合、中和、过滤/分液及干燥,其工艺流程如图3-43所示。

图3-43 古马隆系高效减水剂的工艺流程
3.2.6.2 古马隆系减水剂的性能应用技术要点
国内古马隆系减水剂的代表有CRS减水剂(武汉市四新建材助剂厂出品),它是由焦化厂副产品古马隆经磺化而制得。CRS减水剂合适掺量为水泥重量的0.2%~0.75%,最大掺量不得超过1%。当水泥用量不变,掺CRS减水剂混凝土坍落度保持与不掺CRS减水剂混凝土基本相近,减水率能达到15%~20%;混凝土3d强度能提高40%~130%,28d强度能提高20%以上;当坍落度和强度保持与不掺CRS减水剂的混凝土相近时,可节约水泥12%左右。当用水量不变,强度保持与不掺CRS减水剂的混凝土相同时,可使坍落度为3~5cm的混凝土流态化,其他性能如抗拉、抗折、弹性模量、抗渗等性能也有不同程度的改善,无钢筋锈蚀影响。但是,当CRS减水剂的掺量较大时,具有较大缓凝性。
3.2.7 聚苯乙烯磺酸盐减水剂
苯乙烯低聚物是一种重要的化工助剂,它具有优良的电绝缘性能可用作聚氯乙烯的电绝缘性能改进剂;它的带电性好、吸湿性小、不污染感光板、易与炭黑混合,适于作电子照相显相剂;它的分子量低,与颜料的亲和性及一些树脂的相容性能比较好,可作为聚苯乙烯、聚氯乙烯等树脂的颜料分散剂;它还可作为EVA热溶胶及溶液型胶黏剂的增黏剂;作为热熔型涂料及交通标志用涂料的基材。苯乙烯低聚物经过磺化、中和反应得到的苯乙烯低聚物磺酸盐是一种优良的阴离子型高分子表面活性剂——聚苯乙烯磺酸盐减水剂。聚苯乙烯磺酸盐减水剂的合成工艺如图3-44所示。

图3-44 聚苯乙烯磺酸盐减水剂的合成工艺
聚苯乙烯磺酸盐减水剂与市售磺酸盐型减水剂相比,其对水泥净浆流动性的改善效果明显优于市售的萘磺酸甲醛缩合物、甲基萘磺酸甲醛缩合物和磺化蒽油甲醛缩合物等减水剂。
聚苯乙烯磺酸盐减水剂具有一定的引气和轻微的缓凝性,这类减水剂对水泥颗粒的分散作用强,减水率高,掺量小(一般在0.3%左右),其最大的优点是具有一定的保塑性,能有效地控制混凝土拌和物的坍落度经时损失,而对混凝土硬化时间影响不大,具有良好的增强作用,能提高混凝土的抗渗性和抗冻性,因此能提高混凝土的耐久性。对净浆而言,砂浆减水率试验结果与其混凝土比较一致。