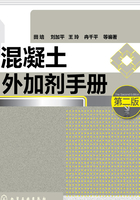
第3章 混凝土外加剂品种、性能和生产技术
3.1 高性能减水剂
聚羧酸系高性能减水剂是一种新型的减水剂,国外20世纪80年代开始研发,我国20世纪末开始研发,它具有比萘系减水剂更高的减水率和更好的坍落度保持性能,并具有一定的引气性和较低的混凝土收缩。目前我国开发的高性能减水剂以聚羧酸盐为主。
3.1.1 定义及分类
(1)定义及名称
根据行业标准JG/T 223—2007《聚羧酸系高性能减水剂》的规定,聚羧酸系高性能减水剂(polycarboxylates high performance water-reducing admixture)是由含有羧基的不饱和单体和其他单体共聚而成,使混凝土在减水、保坍、增塑、减缩及环保等方面具有优良性能的系列减水剂。
(2)按照分子结构分类
1982年日本公开了第一个聚羧酸减水剂的专利,随后聚羧酸系减水剂就逐步成为日本和欧美等发达国家及地区化学外加剂的研究热点,中国也在20世纪90年代末开始开展该领域的研究,并于2001年左右开始实现产业化和工程应用。从目前国内外发表的研究论文和公开的专利来看,聚羧酸系高性能减水剂的基本结构是线型多支链的梳形共聚物,主链上主要含有羧基、磺酸基、羟基、氨基等极性基团,侧链是不同类型的亲水性聚氧乙烯(PEO)链段。根据主侧链接枝方式的不同可以分为如下几类。
① 酯型聚羧酸高性能减水剂 该类聚合物以甲基丙烯酸、丙烯酸、马来酸酐、烯基磺酸盐等为分子主链,PEO侧链以酯键()和主链相连[图3-1(a)、(b)]。

图3-1 酯型聚羧酸系高性能减水剂分子结构示意图
② 醚型聚羧酸高性能减水剂 该类聚合物以丙烯酸、马来酸酐等为分子主链,PEO侧链以醚键(—O—)和主链相连(图3-2)。

图3-2 醚型聚羧酸系高性能减水剂分子结构示意图
③ 酰胺/酰亚胺型聚羧酸高性能减水剂 该类聚合物以丙烯酸为分子主链,PEO侧链以酰胺键或酰亚胺键相连(图3-3)。

图3-3 酰胺/酰亚胺型聚羧酸系高性能减水剂分子结构示意图
④ 混杂型聚羧酸高性能减水剂 此外还可能出现PEO侧链以酯键、醚键、酰胺键或酰亚胺键等两种或多种混杂桥接方式和主链相连。
(3)按使用功能分类
随着人们对梳形接枝共聚物分子结构、性能关系和作用机理的深入研究,发现梳形共聚物外加剂除可以赋予新拌混凝土高初始流动性和高工作性保持外,还可以采用现代分子裁剪技术赋予硬化混凝土低收缩、超早强甚至满足水化控制的要求等多种功能,这为化学家和材料研究者们的创新提供了广阔的空间。因而聚羧酸系高性能减水剂按照其功能又可分为高减水型、保坍型、减缩型、早强型等。高减水型主要强调分散、减水功能,最高减水率可达50%以上;保坍型又称缓释型,重点强调保坍功能而部分牺牲减水功能,主要是运用共聚物分子内或者分子间的酯基、酰氨基或其他非亲水性基团在水泥水化提供的强碱性环境下缓慢释放出吸附基团,徐徐发挥其减水、分散作用,从而实现优异的混凝土流动性保持功能,克服了传统缓凝保坍措施增大混凝土泌水、降低早期强度的缺陷;减缩型指聚羧酸减水剂除在混凝土新拌阶段具有一定的减水功能外,还赋予了其降低混凝土收缩的功能;早强型聚羧酸减水剂是指通过改变共聚物分子结构来加快水泥早期水化,实现超早强,避免添加传统无机盐造成降低后期强度以及劣化混凝土耐久性能的缺陷。
3.1.2 生产所用主要原材料及其检测方法
3.1.2.1 甲氧基聚醚(MPEG)
聚羧酸减水剂生产厂家如果采用先酯化后共聚的工艺路线,则甲氧基聚醚(MPEG)是其最主要的原材料。一般每生产1t聚羧酸外加剂(以20%浓度计)需要消耗MPEG0.12~0.18t,所采用的主要分子量规格有M-600、M-750、M-1000、M-1200、M-2000、M-5000。MPEG质量的好坏直接关系到所合成的产品的最终减水和保坍性能。通常MPEG生产是以乙二醇单甲醚为起始剂,在催化剂的条件下同环氧乙烷(或部分环氧丙烷)加成生成低分子量的甲氧基聚醚,然后根据不同分子量需求加成不同的环氧乙烷量(或部分环氧丙烷),从而制备出不同分子量规格的甲氧基聚醚。MPEG作为生产聚羧酸系高性能减水剂的主要原材料,对其性能指标有如下要求。
(1)分子量大小及分布
MPEG的分子量大小及分布主要受到设备、生产工艺和控制手段以及催化剂的影响。分子量大小直接影响产品的分散性能。通常来说,侧链聚醚分子量低,则共聚物保坍性能好;分子量高则分散性能优异。当然聚醚分子量分布并不是越窄越好,也不是越宽越好,不同的聚羧酸生产厂家由于采用的合成工艺和路线不同,因此对MPEG分子量大小及分布要求也不同。每个厂家的工艺比较固定,有些是转让的配方,有些是自己开发的技术,一般原材料比较固定,如果改变原材料供应商,而仍然采用原来的工艺,很可能生产出不合格的产品,当然这并不能说明采用的原材料质量不合格,只是其分子量大小及分布和原来厂家不同,从而影响了产品的最终性能。如果适当调整酯化或共聚的配方,则也完全可以生产出合格的产品。
(2)严格控制聚乙二醇含量小于1%
MPEG生产过程中由于起始剂、催化剂或环氧乙烷的含水率不同,水与环氧乙烷加成生成了聚乙二醇副产物,副反应式如式(3-1)。当然聚乙二醇副产物也可能是由于制备过程中聚醚发生断链副反应产生的。在利用酯化反应制备大单体时,由于不饱和酸过量,聚乙二醇的两个羟基与—COOH反应,形成两端均含有双键的酯化物,在共聚反应制备聚羧酸系高性能减水剂时起交联剂的作用,产品容易产生凝胶,减水率和保坍能力大幅度下降。如果聚乙二醇含量太高,很可能在第一步酯化反应时就会出现凝胶。因此生产聚醚时对原材料进行脱水处理是很有必要的。
(3-1)
(3)控制pH=6~7
酯化反应制备大单体时,一般都要采用不饱和酸,如果在制备聚醚工艺中残留大量的碱性催化剂,则在酯化反应中碱性催化剂会中和不饱和酸,影响酯化效果。当然如果采用过量的醋酸中和,也会对酯化产生不利的影响。
(4)严格禁止采用双氧水脱色处理
在其他行业应用的聚醚,一般对颜色要求比较高,因此过去很多厂家采用双氧水脱色处理,但是在外加剂行业,聚醚要首先和不饱和酸酯化,原材料中如果残留有双氧水,则双氧水起到引发剂的作用,导致不饱和酸在酯化过程中发生聚合。
3.1.2.2 聚醚大单体
近年来,随着聚羧酸减水剂的发展,所用的原材料也越来越丰富,除酯化法生产所需要的MPEG外,还出现了烯丙基聚醚(APEG)、甲基丁烯基聚醚(TPEG)、甲基烯丙基聚醚(HPEG)等相关聚醚大单体。这一类聚醚大单体有别于MPEG,其不需要经过酯化过程,可直接与不饱和羧酸进行共聚,经过一步工艺即可制备得到聚羧酸减水剂,生产效率大大提高。
聚醚大单体的化学结构式如式(3-2)所示,其一端为不饱和双键;另一端为聚氧化乙烯/氧化丙烯醚链段。其中,双键提供了聚合活性,能与其他含双键的单体进行共聚,而聚醚链段提供了亲水性和空间位阻作用,从而有效保证聚羧酸减水剂的水溶性和分散性。其中,APEG由于自身的衰减链转移特征,具有自阻聚效应,因而共聚活性较其他两种聚醚大单体弱,转化率较低,共聚后聚合物的分子量相对较小。TPEG和HPEG由于甲基的供电子效应,提高了双键的共聚活性,使得其共聚能力和转化率相对较高,效能明显优于APEG。
(3-2)
式中,R为H、CH3;X为连接基团,如—CH2—、—CH2CH2—等;m、n为氧化乙烯或氧化丙烯的重复单元数。
目前市售的聚醚大单体分子量主要以2000~2400为主,这主要是聚醚生产厂家的习惯,一开始将分子量定为2400左右,大规模生产应用后,不便再对其进行调整。其实聚醚大单体的分子量可以是1000、2000、3000等,不同的分子量用于聚羧酸减水剂生产时,需要适当地调整配方,仍然可以得到性能较好的减水剂,并不局限于一种分子量。分子量的检测同MPEG一样,均可以采用羟值的测定来计算分子量,同时目前也可以采用高效凝胶色谱(GPC)来进行测试。另外,不同厂家聚醚大单体的分子量分布也有所不同,其对于减水剂性能的影响,目前未见详细的报道。
最值得关注的一点是聚醚大单体的双键保留率,即双键含量。由于聚醚大单体是在高温条件下由环氧乙烷与不饱和醇起始剂加成而得的,经过长时间的高温反应,势必会造成末端双键的破坏。一旦双键被破坏,聚醚大单体便完全丧失了聚合活性,成为无用的副产物,不能参与后续的共聚反应。因此,双键保留率对于聚醚大单体的应用性能显得尤为重要。不同厂家由于其生产工艺的差别,也会造成聚醚大单体双键保留率的差异,选择双键保留率较高的产品,才能更有效地发挥聚醚大单体的性能。双键保留率的检测方法主要有两种:一种是通过乙酸汞来测定不饱和度;另一种是通过一氯化碘来测其碘值,然后再通过与理论值计算得到双键保留率。两种方法各有优缺点,乙酸汞方法测试比较直接,不用溶剂,但乙酸汞为剧毒品,购买和操作相对烦琐,要求较高;碘值的方法试剂相对容易购买和操作,但需要使用大量有机溶剂。因此可以根据实际情况进行选择。
聚醚大单体的含水量、pH值和聚乙二醇含量对于其性能的影响远没有MPEG严重,因为一般生产聚羧酸减水剂时,聚醚大单体都直接溶解到水中进行共聚反应,有的厂家为了下游客户使用的方便性,也采取直接将聚醚大单体配成水溶液,减少了聚醚溶解的过程。但是聚醚的含水量和pH值还是会对聚醚的其他检测指标造成影响,导致检测的误差。聚乙二醇含量虽然对生产过程不产生影响,由于不参与聚合反应,如果含量偏高,原材料的有效利用率则降低,也造成了原材料的浪费。
3.1.2.3 不饱和酸
合成聚羧酸系减水剂的另外一类主要原材料为不饱和酸,包括马来酸酐、马来酸、丙烯酸、甲基丙烯酸或这些不饱和酸的盐或酯,此外还有可能采用丙烯酰胺、丙烯磺酸钠或甲基丙烯磺酸钠等不饱和单体。这些单体为石油化工常见化学品,已基本具有较为全面的检测方法,有的已有相关标准可供参考。
聚羧酸系减水剂主要原材料、主要控制指标及检测方法见表3-1。
表3-1 聚羧酸系高效减水剂主要原材料、主要控制指标及其检测方法

3.1.3 聚羧酸系高性能减水剂的制备方法及其优缺点
近年来国内各种类型的聚羧酸系高性能减水剂生产企业如雨后春笋般层出不穷,由于技术来源不同,到目前为止,国内有关的聚羧酸系高性能减水剂生产企业产生了不同的生产方式,从目前所报道的文献来看,聚羧酸系高效减水剂的生产方法大体上有如下几种。
3.1.3.1 酯型聚羧酸系高性能减水剂的制备方法
(1)先酯化后聚合
先将不饱和羧酸单体(通常是丙烯酸或甲基丙烯酸单体)与MPEG进行酯化反应,在聚醚上引入活性双键,酯化成分子量为200~5000甚至10000的活性大单体,然后由大单体与各种不饱和单体共聚物而得,其反应示意图如图3-4所示,当然聚合完毕后还需要加碱进行中和反应。

图3-4 先酯化后聚合反应示意图(L指其他共聚单体)
此方法的优点是各官能团的摩尔比可任意调节,分子设计具有多样性。但也有缺点,一是功能性大单体的合成难度大,MPEG分子量越大,酯化率越低;二是(甲基)丙烯酸聚合活性较大,极易发生聚合,所以在酯化反应时,必然要加入阻聚剂。此时若阻聚剂含量过小,则在酯化过程中就会发生聚合,生产报废。若阻聚剂用量过大,在酯化过程中起到了阻聚作用,但过量的阻聚剂会影响之后的共聚反应,使得之后的分子量难以控制。该方法工艺比较复杂,操作控制有一定的难度。但这是目前国内技术实力雄厚、生产能力较强、生产规模较大的企业采用的主要合成路线。
(2)先聚合后酯化
第一步将一种或几种不饱和羧酸单体在溶液中均聚或共聚成聚合物,分子量由几千至几万不等,第二步由该聚合物与MPEG在催化剂作用下发生缩合反应,从而在高分子主链上引入聚醚侧链,其反应示意图如图3-5所示。

图3-5 先聚合后酯化反应示意图(L指其他共聚单体)
Y=NH2或OH;X=O或NH
该合成方法的优点是工艺简单,所有反应在一个反应釜中完成,且操作方便,成本低,但也存在很多问题。首先,难以找到一种合适的溶剂作为聚合反应的介质。如以水为溶剂,酯化反应本身是一个可逆平衡反应,反应本身要生成水,大量水的存在不利于反应的进行。采用有机溶剂尽管能解决上述问题,但同时也抹杀了该方法的最大优点——成本低,同时,不可避免地会对环境造成污染,也不符合可持续发展的要求。其次,在第一步合成低分子聚羧酸时一般要采用油溶性引发剂,甚至还要加入硫醇类链转移剂,这类物质不但有毒,而且有很大的刺激性气味,会对环境造成污染。最后,在酯化过程中,羧酸类低聚物和端羟基聚氧乙烯基醚都是聚合物,比较黏稠,反应活性很低,很难提高其酯化效率。而且聚羧酸和聚醚的相容性不好,酯化实际操作困难;另外随着酯化的不断进行,水分不断蒸出,会出现相分离。
因此,目前国内还没有发现采用此工艺路线生产聚羧酸系高效减水剂。
(3)原位聚合与接枝
该方法主要是为了克服先聚合后酯化工艺的缺点而开发的,此方法在主链聚合的同时引入侧链。聚醚作为羧酸类不饱和单体的反应介质,克服了聚羧酸与聚醚相容性不好的问题,其反应示意图如图3-6所示。T.Shawl等人把丙烯酸单体、链转移剂、引发剂的混合液逐步滴加到装有分子量为2000的甲氧基聚乙二醇的水溶液,在60℃反应45min,然后升温到120℃,用N2鼓动反应物,不断除去水分(约50min),加入催化剂升温到165℃,反应1h进一步反应接枝得到成品。这种方法虽然可以控制聚合物的分子量,但主链一般也只能选择含—COOH基团的单体,否则很难接枝,且这种接枝反应是一个可逆平衡反应,反应前体系中已有大量的水存在,其接枝度不会很高且难以控制。此外聚合反应一般要采用有毒的油溶性引发剂和强刺激味的硫醇类链转移剂,对环境造成了一定的污染。当然这种方法工艺简单,生产成本较低,缺点是分子设计比较困难。

图3-6 原位聚合与接枝反应示意图(L指其他共聚单体)
Y=NH2或OH;X=O或NH
因此,目前国内还没有发现采用此工艺路线生产聚羧酸系高效减水剂。
3.1.3.2 醚型聚羧酸系高性能减水剂的制备方法
近年来,国内聚醚生产厂家逐渐开发出多种不饱和醚类聚醚大单体,市场上大量使用的有乙烯基聚氧乙烯醚、烯丙基聚氧乙烯醚、甲基烯丙基聚氧乙烯醚、甲基丁烯基聚氧乙烯醚等。这些醚类大单体与上述酯类大单体相比具有质量稳定、合成简单、贮存稳定性好的优点,尤其是能大大简化聚羧酸系高性能减水剂的生产过程。醚型聚羧酸系高性能减水剂主要通过不饱和醚类聚醚大单体与不饱和羧酸类单体在引发剂和链转移剂存在的条件下发生自由基共聚而制备(图3-7)。

图3-7 醚型聚羧酸系高性能减水剂聚合反应示意图(L指其他共聚单体)
无论聚羧酸系高性能减水剂采用何种合成工艺,一般自由基共聚反应都会采用如下三种工艺来控制其分子量大小及分布,不同的控制工艺其合成的共聚物的分散和保坍性能也有一定的差距。
① 连续滴加法 往聚合反应釜中加入一定的反应介质,升温。将大分子单体、共聚单体配成混合溶液,同时配制引发剂溶液,在一定的时间内将单体溶液和引发剂溶液分开,同时往反应釜中滴加。
② 一次投料法 将全部单体及全部溶剂、引发剂一次性加入反应瓶中,然后升温聚合。
③ 种子聚合法 将部分单体、部分溶剂和少量引发剂加入反应釜中,升温开始聚合,然后继续将剩余单体溶液和引发剂溶液连续滴加入反应釜中。
3.1.4 聚羧酸系高性能减水剂的生产工艺
3.1.4.1 生产工艺流程图
以制备工艺较为复杂的酯型聚羧酸系高性能减水剂生产工艺为例,其主要的生产过程可以分为酯化、共聚合、中和三个步骤,其生产工艺流程示意图如图3-8所示。

图3-8 聚羧酸系高效减水剂生产流程示意图
详细操作方法可以描述如下。
① 用水反复冲洗装有温度计、搅拌装置、滴定装置和油水分离器的反应釜,并烘干。依次将烷基聚醚、不饱和酸类单体、阻聚剂、催化剂、携水剂加入反应釜中,升温到回流状态进行酯化反应制备大分子单体,酯化反应至终点时,从油水分离器底部的出口接收反应生成的水分,然后减压蒸馏回收溶剂,有机溶剂可多次回收使用。
② 将酯化混合料加水降温,并加入其他共聚单体,配制成单体混合溶液,在一定的时间内往聚合釜中滴加单体混合液,同时分开滴加引发剂溶液(必要时加入链转移剂),滴加完毕后,保温反应4~6h。
③ 降温至40℃以下加入计算量的碱溶液进行中和,调节pH=6~9,得到聚羧酸系高性能减水剂溶液。
醚型聚羧酸系高性能减水剂的生产工艺则更为简单,只涉及如图3-9所示的共聚合和中和单元操作。

图3-9 聚羧酸系高效减水剂生产关键设备图
1—反应釜;2—高位槽;3—冷凝器;4—油水分离器
3.1.4.2 生产关键设备图
酯型聚羧酸系高性能减水剂生产设备主要是酯化设备,如图3-9(a)所示,酯化设备中最关键的部分是搅拌桨叶片型式和油水分离器的分离效果。另外一个关键设备是聚合反应釜,如图3-9(b)所示,其中最关键的部分是搅拌桨的搅拌效率,共聚反应必须充分搅拌,有利于单体混合均匀和散热,从而有利于共聚物的分子量分布均匀。
3.1.4.3 操作控制关键点
酯型聚羧酸系高性能减水剂生产工艺中最重要的工艺是酯化和聚合两个反应过程。
(1)酯化过程
羧酸与醇生成酯的反应是在酸催化下进行的。在一般情况下,羧酸与伯醇或仲醇的酯化反应,羧酸发生酰氧键断裂,其反应过程如图3-10所示。

图3-10 酯化反应原理示意图
酯化反应是一个化学平衡过程,即羧酸与聚醚的酯化反应速率与酯的水解速率相等,此时反应物与生成物的浓度都不再发生变化。根据平衡原理,增加反应物的浓度、减少生成物的浓度有利于酯化产物的生成,在实际生产中可以增加羧酸的浓度和及时移走反应生成的水分有利于酯的生成。在酯化反应中,存在着一系列可逆的平衡反应步骤。步骤②是酯化反应的控制步骤,而步骤④是酯水解的控制步骤。这一反应是SN2反应,经过加成-消除过程。采用同位素标记醇的办法可证实酯化反应中所生成的水是来自于羧酸的羟基和醇的氢。醇作为亲核试剂对羧基的羰基进行亲核攻击,在质子酸存在时,羰基碳更为缺电子而有利于醇与它发生亲核加成。因此酯化反应最关键的控制点为酯化温度、酯化时间和酯化生成水。因此操作人员必须严格控制搅拌速率和反应温度,尽可能提高回流速率,以回流管不冲料为宜。操作人员从反应釜温度计上读出各段温度,做好记录。
(2)聚合过程
共聚合反应是决定分子结构和分子量大小及分布的关键反应,聚合酸度、单体浓度、反应温度、引发剂和链转移剂用量、引发剂和单体的滴加方式与滴加速率是控制共聚物分子量大小及分布的关键因素。在原材料配比固定的情况下,共聚物分子量大小及分布则是控制共聚物分散性能和保坍性能的最关键因素。因此操作人员严格控制聚合酸度、单体浓度、聚合反应温度和物料滴加速率,并从反应釜温度计上读出各反应段温度,做好详细的操作记录。
此外,聚合反应结束后,必须对共聚物进行中和,中和工艺中,操作人员要控制好加碱前温度,最好控制在40℃以下加碱溶液中和,碱液缓慢滴加为宜。最终物料的pH值一般控制在6~9,如果共聚物酸性太强,不但贮存稳定性不好,而且会对金属贮罐具有腐蚀性。如果共聚物呈强碱性,则酯键会发生降解,侧链断链,共聚物性能变坏。
酯型聚羧酸系高性能减水剂生产主要控制点见表3-2。
表3-2 酯型聚羧酸系高效减水剂生产主要控制点

醚型聚羧酸系高性能减水剂的生产关键控制点只涉及表3-2的共聚工艺。
3.1.4.4 原材料大致消耗
生产酯型聚羧酸系高效减水剂最主要的原材料是MPEG和不饱和酸,醚型聚羧酸系高性能减水剂最主要的原材料是不饱和大分子单体和不饱和酸。具有不同功能的聚羧酸外加剂的化学结构不同,原材料的消耗也不相同。但无论采用何种合成工艺,聚醚类单体都占了绝大部分的重量,基本上要占聚羧酸外加剂总重量的60%~90%,甚至会达到95%以上,因此聚醚类单体的质量好坏是生产聚羧酸系减水剂质量好坏的决定性因素。当然不饱和酸也是不可缺少的主要原材料,不饱和酸的含量以及其中的阻聚剂种类和含量是影响酯化和聚合的关键因素。聚羧酸系高性能减水剂主要原材料大致消耗定额见表3-3。
表3-3 聚羧酸系高效减水剂主要原材料大致消耗定额(以20%有效浓度计算) 单位:kg/t

3.1.5 常规聚羧酸系高性能减水剂性能特点
3.1.5.1 聚羧酸系高性能减水剂分散作用机理
聚羧酸系高性能减水剂是由一定长度的活性聚醚大单体与含有羧酸、磺酸等官能团的不饱和单体共聚而成的梳形接枝共聚物分散剂,其分散作用机理如图3-11。主链上的羧酸、磺酸等极性基团提供吸附点,长聚醚侧链提供空间位阻效应,从而赋予共聚物良好的分散性能。

图3-11 聚羧酸系高性能减水剂分散作用机理
3.1.5.2 主要性能特点
与掺萘系等第二代高效减水剂的混凝土性能相比,掺聚羧酸系高性能减水剂的混凝土具有显著的性能特点。从聚羧酸和萘系外加剂总体性能比较来看,见表3-4。聚羧酸外加剂掺量低、减水率高、保坍性能好、增强效果好,而且能有效降低混凝土的干燥收缩。另外,梳形接枝共聚物分子结构可变性大,可以根据用户不同的性能要求,设计不同功能的产品,满足不同的工程需要。部分性能特点已被许多检验结果和工程实践所证实,有些还需要进一步研究。
表3-4 聚羧酸和萘系外加剂总体性能比较

(1)掺量低、减水率高
按固体掺量计,聚羧酸系高性能减水剂的常用掺量为胶凝材料重量的0.2%左右(0.15%~0.25%),为萘系一般常用掺量的1/3左右。目前国内外的产品按照GB 8076—2008测定减水率,一般均在25%~30%之间;在接近极限掺量0.5%左右时,其减水率可达45%以上。根据最新国外报道,目前的聚羧酸系高性能减水剂的减水率最高可达到60%。与萘系相比,减水率大幅度提高,掺量大幅度降低。并且带入混凝土中的有害成分大幅度减少,单方混凝土成本明显低于萘系高效减水剂,从而最大限度地降低水泥用量,提高混凝土强度和改善混凝土耐久性。
(2)新拌混凝土流动性保持性好、坍落度损失小
尽管混凝土拌和物流动性保持性能好是聚羧酸系高性能减水剂的显著特点之一,但由于我国水泥种类繁多,水泥和集料质量地区差异很大,所以聚羧酸系高性能减水剂仍然存在对水泥矿物组成、水泥细度、石膏形态和掺量、外加剂添加量和添加方法、配合比、用水量以及混凝土拌和工艺的适应性问题。许多对比试验和工程实践证明:在同样原材料条件下,掺聚羧酸系高性能减水剂混凝土拌和物的流动性和流动保持性能要明显好于萘系减水剂。当然对于某些适应性不好的水泥品种,仍然可以通过复配缓凝剂或聚羧酸系保坍组分,甚至可以通过调整分子结构来加以解决。
(3)增强效果好
按照GB 8076—2008检测了国内外11种聚羧酸减水剂产品的抗压强度比,与掺萘系减水剂的混凝土相比,掺聚羧酸外加剂的混凝土各龄期的抗压强度比均有大幅度提高。以28d抗压强度比为例:掺萘系减水剂的混凝土28d抗压强度比一般都在130%左右,而掺聚羧酸外加剂的混凝土抗压强度比在150%左右。并且在掺加了粉煤灰、矿渣等矿物掺合料后,其增强效果更佳。另外,由于聚羧酸分子结构的多变性,可以通过分子结构设计开发出超早强型聚羧酸外加剂,其强度性能与基准相比,12h抗压强度比达400%,1d混凝土抗压强度可达到28d强度的40%~60%以上。
(4)新拌混凝土和易性好
掺聚羧酸高性能减水剂的混凝土抗泌水、抗离析性能好,泵送阻力小,便于输送;混凝土表面无泌水线、无大气泡、色差小,特别适合于外观质量要求高的混凝土。
(5)收缩率低。
掺聚羧酸高性能减水剂的混凝土体积的稳定性与掺萘系减水剂相比有较大的提高。按照GB 8076—2008检测了国内外11种聚羧酸减水剂产品的28d收缩率比。11种样品中掺聚羧酸减水剂的混凝土收缩率的平均值为102%,最低收缩率为91%。而对于掺萘系减水剂的混凝土,国家标准规定28d收缩率不大于135%。很显然聚羧酸高性能减水剂有利于混凝土耐久性的提高。如果从原材料和工艺方面进行优化,再接枝上适当比例的减缩组分,可以开发出具有减缩功能的聚羧酸高效减水剂,其减缩、抗裂效果甚至可以和减缩剂相当,但掺量仅为减缩剂的10%左右。
(6)总碱量低
国内外11种聚羧酸减水剂产品的总碱量平均值为1.35%,最低值仅为0.19%,与萘系等第二代高效减水剂相比,单方混凝土中带入的总碱量仅为数十克,大大降低了外加剂引入混凝土中碱含量,从而最大程度上避免发生碱-集料反应的可能性,提高了混凝土的耐久性。
(7)环境友好
聚羧酸系高性能减水剂合成生产过程中不使用甲醛和其他任何有害原材料,生产和长期使用过程中对人体无健康危害,对环境不造成任何污染。而萘系等第二代高效减水剂是一类对环境污染较大的化工合成材料,并且其污染是持续性的,在生产和使用过程中均存在,无法克服。在缩合中仍残余有甲醛,在配制成混凝土后产品中残留的甲醛和萘等有害物质会从混凝土中缓慢逸出,对环境造成污染。
(8)不含氯离子聚羧酸系高性能减水剂不含氯离子,对钢筋无腐蚀性
3.1.5.3 外加剂推荐掺量及掺量影响
通常来说,聚羧酸系高性能减水剂(20%有效含量计)常用掺量为水泥重量的0.7%~1.3%,配制超高强混凝土时,掺量可提高到1.5%~1.8%,在混凝土配合比固定的情况下,增大聚羧酸外加剂的掺量,坍落度保持能力明显增强,但减水率提高很小,掺量过高甚至会出现严重的离析、泌水现象;此外随掺量的增加,混凝土凝结时间会延长。当掺量太低,如固体掺量≤0.1%时,新拌混凝土坍落度保持能力会下降。
3.1.5.4 掺量对新拌混凝土性能的影响
不同掺量的聚羧酸系高性能减水剂对新拌混凝土性能的影响见表3-5。采用GB 8076—2008标准,以基准混凝土在坍落度为21cm±1cm为基准,加水量则以控制坍落度为21cm±1cm为准。
表3-5 不同掺量的聚羧酸系高性能减水剂对新拌混凝土性能的影响
(配合比按GB 8076—2008标准,外加剂以有效固体量计)

试验结果表明,当外加剂掺量为水泥的0.15%时,就具有20%的减水率,其减水率超过目前市场上一般萘系高效减水剂的水平,掺量大于水泥用量的0.30%时,减水率可以达到30%。当外加剂掺量增加时,减水率增加,但增加幅度不是很大,而坍落度保持能力更趋稳定,新拌混凝土无论1h的坍落度或扩展度都增大,但当掺量太高时,混凝土会有一定的泌水。当掺量大于水泥用量的0.15%时,无论是坍落度或扩展度都不损失。实际应用中,如果胶材增加,实际减水率会增大,尤其是在有矿物掺合料时,流动性能比掺萘系减水剂改变更为明显。
3.1.5.5 掺量对硬化混凝土性能的影响
(1)抗压强度
不同掺量聚羧酸系高性能减水剂掺量对混凝土的抗压强度的影响见表3-6。
表3-6 不同掺量聚羧酸系高性能减水剂掺量对混凝土抗压强度的影响(配合比按GB 8076—2008标准)

注:表格中除基准混凝土的抗压强度值外,其余各栏中的数据,斜线前面的数值表示混凝土的抗压强度,斜线后面的数值表示该混凝土的抗压强度与基准混凝土的抗压强度的比值
试验结果表明,聚羧酸系高性能减水剂具有很好的增强效果。掺加聚羧酸系高性能减水剂,使混凝土抗压强度得到迅速增加,尤其是其早期强度,在掺量为水泥重量的0.15%时,3d的抗压强度增加可达190%以上,其他掺量情况下,抗压强度增加幅度也达到了200%以上。同时,不同龄期的混凝土抗压强度的增加幅度也是非常明显的,根据试验结果,3d的抗压强度提高80%~150%,7d的抗压强度提高50%~150%,28d的抗压强度可增加50%~100%,90d的抗压强度可增加50%~150%,可见,掺聚羧酸系高性能减水剂的混凝土抗压强度不仅具有相当高的早期强度,其后期强度也有大幅度提高,且不断稳定增长。这样的增长幅度在目前大量使用的混凝土外加剂中也是相当突出的。
另外,在一定的范围内,随着聚羧酸系高性能减水剂掺量的增加,其增强效果越明显。对比试验结果还可以看到,混凝土强度随超塑化剂掺量的增加而增加,尤其在低掺量范围内增加的幅度较大,随着掺量的增加,增加的幅度减慢,当掺量增加到水泥用量的0.25%时,强度不再继续增加,反而略有下降,这可能与混凝土含气量上升有关。
采用GB 8076—2008检测了不同厂家生产的聚羧酸外加剂与掺传统萘系减水剂的混凝土抗压强度的比较,见表3-7。从表3-7可见,聚羧酸外加剂增强效果比较明显,掺加了该外加剂后,混凝土无论早期强度或中后期强度增长都比较明显,这对配制高强高性能混凝土是十分有利的。
表3-7 GB 8076—2008方法测定的抗压强度及其抗压强度比

(2)其他力学性能
同时采用GB 8076—2008检测了不同厂家生产的聚羧酸外加剂与掺传统萘系减水剂的其他力学性能,见表3-8。从表3-8可见,掺聚羧酸系高性能减水剂的混凝土抗压强度、抗拉强度、抗折强度以及静压弹模与掺萘系减水剂的基本相当,并没有不利的影响。
表3-8 GB 8076—2008方法测定的其他物理性能和力学性能

在实际工程应用中,从使用效果和经济效益两个方面考虑,应选用合适的掺量。对于聚羧酸系高性能减水剂,一般掺量为胶材总重量的0.12%~0.3%,同时研究结果表明,如果混凝土配合比中有大量的矿物掺合料,则掺量可以提高到0.4%。
(3)收缩性能
江苏省建筑科学研究院对比研究了掺聚羧酸类外加剂和萘系减水剂的混凝土干燥收缩和净浆的自收缩,试验结果如图3-12所示。图3-12(a)的试验结果表明,与萘系高效减水剂增加混凝土干燥收缩不同,掺聚羧酸类外加剂的混凝土的干缩率低于基准混凝土,在通常掺量下(水泥的0.2%)掺聚羧酸类混凝土60d干缩率较掺萘系减水剂的低了约40%。图3-12(b)的试验结果表明,对于低水胶比的水泥浆体,掺聚羧酸减水剂后其自收缩率要明显低于掺萘系减水剂,在相同配比下90d的自收缩约降低30%,因此聚羧酸类减水剂在配制高抗裂性高性能混凝土方面较传统减水剂具有明显的优势。

图3-12 不同种类的外加剂对混凝土收缩性能的影响
3.1.6 其他功能型聚羧酸系高性能减水剂
3.1.6.1 减缩型聚羧酸系高性能减水剂
新型的减缩剂(shrinkage reducing agent)能有效降低混凝土的收缩,但其掺量较高(胶凝材料重量的2%~3%),大幅增加成本,而且本身并不具有减水功能,难以在量大、面广的中低强度混凝土中大力推广。新型聚羧酸系高性能减水剂具有良好的分散、保坍和增强功能,在一定程度上降低混凝土的干燥收缩,但降低幅度尚远远不够。聚羧酸系高性能减水剂的非离子型聚醚侧链占共聚物总重量的80%~90%,其结构与有机减缩剂具有极大的相似性,而减水剂只需在混凝土塑性阶段发挥作用,因此如果采用现代分子裁剪技术能充分利用聚醚侧链发挥其在混凝土硬化阶段的作用,有望提升聚羧酸减水剂的减缩功能。
(1)减水剂分子构建
聚羧酸系减水剂与萘系等第二代减水剂相比最大的特点是分子结构可设计性强,在丙烯酸链节单元中接枝长链聚醚,一方面可以提供分散性能;另一方面可以降低混凝土的干燥收缩。在马来酸酐链节上接枝功能性减缩组分(SRA),可以有效降低混凝土早期的收缩。同时在共聚体系中引入聚醚大单体,一方面提供空间位阻;另一方面可有效改善混凝土的后期收缩,见图3-13。

图3-13 减缩型聚羧酸系高性能减水剂(SRPCA)分子结构示意图
(2)减缩型聚羧酸系高性能减水剂性能检测
根据GB 8076—2008《混凝土外加剂》对减缩型聚羧酸系高性能减水剂不同掺量的减水效果进行了测试,其试结果见表3-9。
表3-9 减缩型聚羧酸系高性能减水剂的性能检测

当减缩型聚羧酸系高性能减水剂掺量为水泥的0.16%时,减水率为18.6%,掺量为0.20%时,减水率达22.3%,其减水率超过目前市场上一般高效减水剂的水平,掺量大于水泥用量的0.30%时,减水率可达25%。减缩型聚羧酸系高性能减水剂具有很好的增强效果,3d的抗压强度提高70%~120%,7d的抗压强度提高到70%~100%,28d的抗压强度可增加60%~80%。
(3)减缩型聚羧酸系高性能减水剂对混凝土收缩的影响(图3-14)

图3-14 减缩型聚羧酸系高性能减水剂对混凝土收缩的影响
水泥基材料的收缩变形行为总体来说主要包括干燥收缩、自收缩、化学减缩、温度下降引起冷缩、塑性收缩以及因碳化而引起的碳化收缩。
凝缩指加水后初凝之前的收缩,一部分源于塑性阶段胶凝材料水化产生的化学减缩。掺减缩型聚羧酸系高性能减水剂(SRPCA)的混凝土凝缩值为5.79×10-4,与萘系相比下降了43%。自干燥收缩则是指在密封的条件下水泥浆初始结构形成以后,由于水泥进一步水化在体系内部形成空孔,引起的内部相对湿度的下降所引起的收缩。掺SRPCA的混凝土早期自干燥收缩值为1.34×10-4,与萘系相比下降了50%以上。掺SRPCA的混凝土后期(60d,测试零点选取加水拌和后48h)自干燥收缩值为0.83×10-4,与萘系相比下降了51.7%。掺SRPCA对减少混凝土干燥收缩效果也十分显著,掺量为0.16%时,28d干燥收缩率与基准相比降低了24%,60d干燥收缩率降低了25.1%;掺量为0.20%时,28d干燥收缩率与基准相比降低了44%,60d干燥收缩率降低了45%,基本上达到了复掺2%减缩剂的减缩效果。
3.1.6.2 超早强型聚羧酸系高性能减水剂
超早强型聚羧酸系高性能减水剂是指兼具早强及减水功能的聚羧酸减水剂。
目前市场上普通聚羧酸系减水剂在一定程度上延缓了水泥的水化,特别是养护温度低时,由于其早期强度发展缓慢,限制了其在寒冷气候下的使用。即便是在常温条件下,混凝土1d抗压强度也仅能达到设计强度的20%~30%,3d抗压强度达到设计强度的40%左右。采用传统无机盐或有机早强剂提高混凝土早期强度,不但其掺量高,降低了混凝土后期强度,而且容易劣化混凝土的耐久性。通过在分子结构中接枝聚醚超长侧链可显著缩短混凝土的凝结时间,提高混凝土1~3d的机械强度,满足日益加速的建筑施工要求。
(1)减水剂分子构建
聚羧酸减水剂在水泥颗粒表面的吸附是发挥分散作用的必要条件,水泥颗粒絮凝结构的破坏有利于水泥水化反应的进行,但吸附在水泥颗粒表面的减水剂的定向排列形成了一道足以隔绝水与水泥颗粒接触的屏障,包覆住水泥颗粒表面的水化活性点,从而延长了混凝土的凝结时间,导致混凝土早期强度降低。超早强型聚羧酸减水剂分子结构中引入超长分子侧链结构,其空间位阻作用强,达到同样分散效果时在水泥颗粒表面吸附的减水剂分子相对减少,水泥水化活性点较少被包覆,混凝土水化速率加快,早期强度显著提高,如图3-15所示。

图3-15 超早强型聚羧酸系高性能减水剂的作用机理示意图
(2)超早强型聚羧酸系高性能减水剂性能检测
根据GB 8076—2008《混凝土外加剂》对超早强型聚羧酸系高性能减水剂不同掺量的减水效果进行了测试,其测试结果见表3-10。
表3-10 超早强型聚羧酸系高性能减水剂的性能检测(试验温度为4℃)

当超早强型聚羧酸系高性能减水剂掺量为水泥的0.16%时,减水率达到23.4%,初凝时间缩短49min,终凝时间缩短74min,1d抗压强度提高110%。掺量提高到0.30%时,减水率达28.6%,凝结时间缩短2h以上,1d抗压强度提高400%。
(3)超早强型聚羧酸系高性能减水剂对混凝土力学性能的影响
温度对水泥水化速率的影响是巨大的,低温条件下水泥的水化十分缓慢,当气温低至-3℃时,水泥的水化反应几乎停止。超早强型聚羧酸系高性能减水剂在不同温度环境下均体现出较好的早强性能,低温环境下早强效果更明显(表3-11~表3-13)。不过,超早强型聚羧酸系高性能减水剂的坍落度损失较大,特别是在高温环境下,所以其主要的应用范围为预制混凝土领域。
表3-11 30℃环境下超早强型聚羧酸系高性能减水剂对混凝土性能的影响

注:混凝土配合比为小野田PⅡ52.5水泥∶水∶砂∶石子=430∶137∶718∶1145。
表3-12 21℃环境下超早强型聚羧酸系高性能减水剂对混凝土性能的影响

注:混凝土配合比为小野田PⅡ52.5水泥∶粉煤灰∶水∶砂∶石子=343∶86∶138∶694∶1190。
表3-13 4℃环境下超早强型聚羧酸系高性能减水剂对混凝土性能的影响

注:混凝土配合比为小野田PⅡ52.5水泥∶粉煤灰∶水∶砂∶石子=343∶86∶138∶694∶1190
3.1.7 聚羧酸系高性能减水剂用途及主要应用范围
聚羧酸系高性能减水剂自20世纪90年代初期开始在工程中应用,2000年后用量呈快速增长的态势,各个国家的应用发展水平和用量不尽相同。目前,聚羧酸系高性能减水剂在日本的应用最为普遍,其预拌混凝土基本上全部使用聚羧酸系高性能减水剂。欧洲近年来的发展比较快速,不仅在欧洲各国的用量占到减水剂用量的40%以上,其聚羧酸系产品也在全世界范围内获得了广泛应用。亚洲各国除日本以外,韩国和中国的研究应用最为广泛,中国不仅从生产总量上在亚洲处于领先位置,而且从市场和应用规模上在全世界也处于前列,2011年我国聚羧酸系高性能减水剂的用量已经达到了240万吨,而且正以超乎想象的速度递增,如图3-16所示。

图3-16 国内聚羧酸系高性能减水剂的用量
聚羧酸系高性能减水剂具有大减水、高保坍、高增强和低收缩等功能,产品对水泥适应性强,掺量低,使用方便,特别适用于配制C30~C100的高流态、高保坍、高强甚至超高强的混凝土工程。从近年来聚羧酸系高性能减水剂的发展和应用特点来看,其应用趋势由过去的重大工程重点部位的应用向一般重大工程、普通工程应用,从高强度等级特殊功能混凝土逐步向普通混凝土中应用发展。目前,几乎所有国家重大、重点工程中,尤其在水利水电、核电、桥梁、高速铁路、超高层建筑等工程用混凝土中已经广泛使用聚羧酸系高性能减水剂。随着聚羧酸系高性能减水剂的制备技术和应用技术的逐渐发展,全国范围内普通商品混凝土的生产中也大量使用了聚羧酸系外加剂。
此外,随着预制混凝土行业对节能减排、劳动力成本以及轻质高强需求日益提高,聚羧酸高性能减水剂产品也已经逐步应用到预制构件生产中。其中,PHC管桩免压蒸生产工艺、PHC管桩泵送施工工艺、C120超高强管桩生产以及盾构施工用混凝土管片的免蒸养生产工艺均对减水剂的减水能力(大于30%)、早强能力(1d抗压强度比大于250%)、保坍能力(1h坍落度损失率小于20%)以及减缩能力(收缩率比小于95%)提出了更高的要求,第二代减水剂产品已不能满足新工艺的需求,所以其在预制构件领域内的市场份额正逐步被聚羧酸系高性能减水剂所取代。
3.1.8 应用技术要点
聚羧酸系减水剂被认为是最新一代的高性能减水剂,人们总是期望其在应用中体现出比传统萘系减水剂更安全、更高效、适应能力更强的优点。然而工程实际使用中总是更多地遇到各种各样的问题,而且有些问题还是使用其他品种减水剂时所从未遇到的,如混凝土拌和料异常干涩、无法卸料,更谈不上泵送浇筑了,或者混凝土拌和料分层严重等。另外,应用萘系减水剂所遇到的技术难题,通过近20年的研究已基本上从理论和实践上得到解决,而应用聚羧酸系减水剂出现的问题正在发生,目前人们正在积极地着手研究和找到正确的解决措施,某些工程遇到的前所未有的问题无疑为聚羧酸系高性能减水剂的安全、高效应用带来一定的阻力。
(1)减水效果对混凝土原材料和配合比的依赖性大
聚羧酸系高性能减水剂被证实在较低掺量条件下就具有良好的减水效果,其减水率比其他类型减水剂大得多。必须注意的是,与其他减水剂相比,聚羧酸系减水剂的减水效果与试验条件的关系更大。
首先,聚羧酸系减水剂的减水效果与混凝土中水泥用量关系很大。曾经采用相同的掺量对同一减水剂进行试验,当基准混凝土用水量分别为330kg/m3、350kg/m3、380kg/m3、420kg/m3时,减水率分别为18%、22%、28%、35%。由于聚羧酸系高性能减水剂和萘系减水剂本身结构及分散作用机理的不同,当添加到混凝土中,表现出来的混凝土状态也大不相同,对其性能的检测方法和标准也应该有所不同,而新型聚羧酸系高性能减水剂与萘系减水剂相比,具有更高的减水率,可达到50%以上。
混凝土中集料的颗粒级配以及砂率对聚羧酸系减水剂的减水效果影响也非常大。试验证明,其他条件都不变,仅砂率在40%~50%之间变化时,同种聚羧酸系减水剂的减水率最大可相差4%。
另外聚羧酸系减水剂与其他减水剂一样,减水率还取决于搅拌工艺,如果采用手工拌和,测得的减水率往往比机械拌和降低2%~4%。
如果混凝土中掺加掺合料,减水效果当然取决于掺合料的品种和掺量。对于大掺量的掺合料混凝土,聚羧酸系高性能减水剂的减水效果更加优于萘系减水剂。
(2)减水、保坍效果对减水剂掺量的依赖性大
大量的试验表明,聚羧酸系高性能减水剂的减水效果对其掺量的依赖性很大,且随着胶凝材料用量的增加,这种依赖性更大。在胶凝材料用量相同的情况下,聚羧酸系高性能减水剂的减水效果与掺量的关系总体来说是随着减水剂掺量增加而增大,但当胶凝材料用量低的情况下,到了一定的掺量后甚至出现随掺量增加,减水效果反而“降低”的现象。这并不是说掺量增加其减水作用下降了,而是因为此时的混凝土出现严重的离析、泌水现象,混凝土拌和物板结,流动性难以用坍落度法反映。
尽管保坍性能性能好是聚羧酸系高性能减水剂的显著特点之一,但保坍总是与聚羧酸外加剂的掺量相关的。在中、低强度等级的混凝土中,聚羧酸外加剂在掺量低的条件下(固体掺量≤0.10%)就能满足用水量和坍落度的要求,但此时新拌混凝土的坍落度保持能力较弱。可以通过复配缓凝剂或聚羧酸系保坍组分,甚至可以通过调整分子结构来加以解决。
(3)配制的混凝土拌和物性能对用水量极为敏感
由于采用聚羧酸系高性能减水剂后混凝土的用水量大幅度降低,单方混凝土的用水量大多在130~165kg,水胶比为0.3~0.4,甚至为0.2。在低用水量的情况下,加水量波动可能导致坍落度变化很大,然而对强度的影响较小,见表3-14。
表3-14 聚羧酸系高性能减水剂对用水量的敏感性

正因为用水量对坍落度作用敏感,在测试掺聚羧酸系高性能减水剂混凝土的坍落度损失时,由于地板、工具、蒸发等引起的失水以及砂子含水率的波动更容易造成误差,尤其是在低坍落度或水胶比低的情况下更为明显。
(4)与其他类型减水剂的存在相容性问题,无叠加的作用效果
很多搅拌站反映,过去配制混凝土时,可随意更换泵送剂品种,不会出现混凝土拌和物性能与实验室结果相差很悬殊的现象,更不会出现混凝土拌和物性状的突变。自从搅拌站开始使用聚羧酸系高性能减水剂后,就经常出现一些令人费解的问题,有时加水量已经很大,但混凝土仍然很干涩,有时混凝土拌和物的坍落度损失比掺加普通泵送剂的混凝土还快,混凝土拌和物根本无法卸料,甚至取样测定的混凝土试件强度更是低得无法让人相信。
大量试验和工程应用表明,传统的木质素磺酸钙(钠)、萘磺酸盐甲醛缩合物、多环芳烃磺酸盐甲醛缩合物、三聚氰胺甲醛缩合物以及氨基磺酸盐甲醛缩合物等减水剂,完全可以相互复合掺加,以满足不同工程的特殊配制要求,或获得更好的经济性。这些减水剂复配使用都能达到叠加的使用效果,且这些减水剂的溶液都可以互溶。聚羧酸系高性能减水剂与其他品种的减水剂复合使用却得不到叠加的效果,且聚羧酸系外加剂溶液与其他类型减水剂溶液的互溶性本身就很差。目前的实践和研究证明,聚羧酸系高性能减水剂能与木质素磺酸盐减水剂复配使用。此外也有人研究认为可以与脂肪族高效减水剂、三聚氰胺系减水剂复合使用,不同的研究有时得到的结论不尽相同。掺加聚羧酸系减水剂的混凝土遇到极少量的萘系减水剂或者是它们的复配产品,都可能会出现流动性变差、用水量增加、流动性损失严重、混凝土拌和物十分干涩甚至难以卸料等现象,其最终的强度、耐久性将受到影响。
因此聚羧酸系高性能减水剂不应与萘系和氨基磺酸盐高效减水剂复合或混合使用,与其他种类减水剂复合或混合时,应经试验验证,满足设计和施工要求方可使用。掺用过其他类型减水剂的混凝土搅拌机和运输罐车、泵车等设备,应清洗干净,方可搅拌和运输掺聚羧酸系高性能减水剂的混凝土。
(5)与其他改性组分存在相容性问题
目前关于减水剂的复配改性技术措施,基本上都是建立在木质素磺酸盐系、萘系等传统减水剂改性措施的基础之上。由于聚羧酸系高性能减水剂的分子结构和作用机理与传统外加剂截然不同,如果完全照搬过去传统减水剂的应用经验,不但用处不大,有时甚至起到了相反的效果。如与萘系复配的羟基酸和多糖类缓凝剂就不能很好地解决聚羧酸外加剂的高温缓凝难题,柠檬酸钠也不适合用于聚羧酸系高性能减水剂的缓凝,它不仅起不到缓凝作用,反而有可能促凝。再者,许多品种的消泡剂、引气剂、增稠剂也不适合于聚羧酸系高性能减水剂。因此聚羧酸系外加剂与其他改性组分配合使用时,应提前配制样品,考察其溶液均匀性和稳定性,再考虑其混凝土性能。
(6)减水和保坍受环境温度的影响大
与传统减水剂相比,聚羧酸系高性能减水剂的减水和保坍性能受温度影响更大。固定配方和工艺的聚羧酸系高性能减水剂如果在夏天具有优异的流动性保持能力,到了冬季,混凝土会出现明显的坍落度反增长,有时甚至从初始7cm,1h后会达到20cm以上,而且掺量与夏季相比也会增加5%~10%;相反,固定配方和工艺的聚羧酸系高性能减水剂如果在冬季坍落度保持满足施工要求,则到了夏天,新拌混凝土坍落度损失会明显加快(图3-17)。当然不同分子结构的聚羧酸减水剂具有不同的温度敏感性。因此解决温度敏感性问题必须针对冬、夏季不同气温,调控其分子结构,从而改变共聚物的吸附行为。

图3-17 聚羧酸系高性能减水剂的温度敏感性
(7)搅拌方式和时间对聚羧酸系外加剂含气量影响大
江苏省建筑科学研究院研究了新旧搅拌机和搅拌时间对聚羧酸系外加剂含气量的影响规律。新搅拌机的效率高,C30混凝土含气量增加了2%~3%,C40混凝土含气量增加了5%以上,而采用化学接枝消泡剂的技术途径,则含气量只增加了0.6%。当搅拌时间由3min变成2min后,C30混凝土的含气量下降了1%~2.2%,含气量越高,降低越明显。
(8)含泥量的敏感性
与传统萘系等高效减水剂相比,聚羧酸系高性能减水剂对砂石集料中黏土(尤其是蒙脱土)更敏感,因此极大地制约了其在混凝土中的推广和应用:一方面,黏土矿物对聚羧酸系高性能减水剂有强烈的吸附作用,减少了用于分散水泥的聚羧酸分子数量,降低了减水性能增大了流动度损失;另一方面,由于黏土矿物较高的比表面积,能吸附较多的水分,减少了浆体中自由水的量,这就导致了混凝土流动性降低,黏度变大。另外,黏土矿物的层状结构,使离子和水分很容易进入其结构中。
(9)产品质量稳定性问题
① 聚羧酸系高性能减水剂母液质量稳定性问题 由于不同企业生产时对原材料选择及技术路线不同,其聚羧酸系高性能减水剂产品的颜色不尽相同,有的深,有的浅,有的偏红,有的偏黄,这种颜色差异是正常的,不会影响产品性能,此外,其聚羧酸系高性能减水剂产品的气味也不尽相同,有的基本无味,有的则有较强烈的刺激性气味,主要可能是聚合过程中单体聚合不完全,成品中还存在着未聚合的单体,这些单体的存在,除产生环保问题以外,也有可能影响混凝土的性能,因此生产厂家应采取措施减少未聚合的单体,消除气味。
② 复配后的聚羧酸系高性能减水剂质量稳定性问题 当加入消泡剂、引气剂或缓凝、早强、防冻等组分时,一些复配的聚羧酸减水剂产品会呈现浑浊、变色、分散不良的现象,有的聚羧酸减水剂加入葡萄糖酸钠等缓凝组分后,在一定的温湿度条件下就会有霉点、异味,甚至长毛的现象发生,可以加入一定的防腐剂、杀菌剂适当缓解上述现象。因此,为了避免外加剂组分不均匀而影响混凝土的质量和稳定性,使用前最好进行均化处理。
③ 聚羧酸高性能减水剂贮存问题 在聚羧酸系高性能减水剂的生产和贮存时,应避免与铁质材料长期接触。由于聚羧酸系高性能减水剂产品呈弱酸性,而且聚合过程中加入了引发剂,与铁质材料长期接触会发生缓慢反应,造成聚羧酸的分子量发生变化,因此聚羧酸系高性能减水剂在运输、贮存时应采用洁净的塑料、玻璃钢或不锈钢等容器,不宜采用铁质容器。高温季节,聚羧酸系高性能减水剂应置于阴凉处,防止暴晒;低温季节,应对聚羧酸系高性能减水剂采取防冻措施。
(10)聚羧酸系高性能减水剂检测与应用脱节
按照目前的标准体系,判断减水剂产品是否合格,是以基准水泥为基础来判断的。而外加剂的准确效能主要取决以下几个因素:水泥种类、掺合料的种类与其性能、粗细集料的性能及其所含的杂质、混凝土配合比和混凝土拌和物的搅拌形式、搅拌时间、混凝土温度以及环境条件等。
这就产生了一个很大的矛盾:按国家标准检验合格的产品,不一定能用到实际工程中,而实际用于工程中的产品则很可能不能满足有关国家标准要求并很可能被判为不合格产品。这类矛盾在现场实际抽检时往往会出现,甚至会引起所谓的质量事故。这类矛盾由来已久,只是由于聚羧酸系高性能减水剂的低掺量、高敏感性,使得这个矛盾更加突出。
由于聚羧酸系高性能减水剂的高效能和低掺量导致其对原材料和环境条件的敏感性大大增加,所以,该类产品的现场技术支持就显得非常重要。对施工方而言:由于不同企业聚羧酸减水剂生产原材料的选择、配方、合成工艺、助剂、质量控制、复配技术等的差异,所生产的聚羧酸高性能减水剂产品性能、质量及稳定性不尽相同,因此,产品售后服务对施工方尤为重要。
此外,某些水泥品种的净浆流动度试验结果与其混凝土相关性较差,有时甚至出现截然相反的试验结果。因此,只做净浆试验是不够的,还应进一步做混凝土试验加以确认。