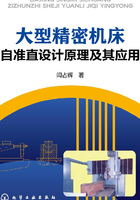
1.2 机床热变形国内外研究现状
机床热变形问题从20世纪30年代开始研究。为适应不断提高制造精度的要求,热变形对机床精度的影响日益引起人们的重视,20世纪30年代至40年代以从改变机床机械结构出发减小机床热变形,从此开始从试验的角度,分析机床热变形产生的原因,逐步形成了有关精密机床热变形的基本知识。但受当时试验条件的限制,研究工作进展十分有限,还不能达到定量分析和准确试验研究的程度。近几十年来,在国内外,研究人员着重针对机械结构热问题产生的机理、机床热变形检测与分析、机床接触面热效应等对机床热变形的影响开展系统的研究,逐步找到了影响机床热变形的因素,并从实际应用的角度寻求解决途径。
1.2.1 机床热变形机理及热变形数学模型
20世纪60年代,H.Fisher同G.Spur共同研究了机床热来源与机械精度之间的数学模型,其基本结论是:机床热变形产生主要在于机床运动时产生的热量传播后,会产生非均匀的温度场,进而机床不同位置的变形大小不一,从而导致机床固定件的位置相对原来位置的移动,最终引起零件加工精度不稳定。20世纪70年代,国外知名研究人员垣野义昭发现,当加工零件时,引起机床热变形的热源不少,详细划分见图1-1。在图1-2中,作者从热变形的来源来阐述机床热变形的影响过程:机械零部件和加工工件都有一定的热容量,温度变化,导致热容量变化,同时热容量的传递具有时间滞后效应,机床热变形是随着材料的变化、不同的温度区间及其他环境等随时间逐渐变化的。

图1-1 导致机床产生热变形的热源

图1-2 机床热变形的机理
20世纪70年代,日本东京大学佐田登志夫教授和助手吉田良在他们的研究工作中首次提出“热刚度”一词,并论述了热变形与热刚度之间的关系,提出机床结构变形不是单一因素的影响,其对加工精度影响具有综合性和复杂性。从此,人们在研究机床变形时,常常将静变形(静刚度)、振动幅值(动刚度)和热变形(热刚度)统一起来,综合分析和研究机床静刚度、动刚度和热刚度对机床精度和对工件加工精度的影响。
20世纪末以来,国内外研究人员大都针对机床热变形产生原因,从机床热变形敏感部位温度变化与热变形量之间耦合关系建立可靠性模型开展研究。1999年,韩国学者Won Soo Yun从高精密数控车床伺服进给装置丝杠、螺母与滚动体摩擦引起的机床热变形,对数控机床用丝杠和基础件导轨建立各自的数学模型。在加工工件时,一般不容易检测丝杠-滚动体-螺母滚动处的每一点的温度,一般常简化处理丝杠-螺母,建立简化后的热传导数学方程,然后再通过系数进行误差补偿,进而得到丝杠-滚动体-螺母温度场实时分布,最后综合利用神经网络、遗传算法或小波变换等数据处理方法求出热变形的大小。对于相对简单的滑动摩擦,摩擦副之间摩擦引起热变化,导致温度场重新分布及引起的热变形可采用FEA方法求得,摩擦副之间的边界条件可通过测量摩擦副敏感点的温度值获得,最后通过试验验证所建立的模型是否正确。1999年,国外研究人员M.H.Attia采用频域反向求解法,初步得到热源对机床敏感件施加的热能,即在离线情况下,通过理论公式推导出作用在机床敏感件的热量q(τ)与热源附近两点温差Δt(τ)之间的传递函数Δt(s),通过公式Q(τ)=L-1[G-1(s)·Δt(s)]求得机床热源在单位时间间隔内的放热。此外,M.Weck和L.Zangs、E.R.Mcclure、Y.Yoshida 和F.Honda等也在机床热变形与温度分布的关系方面做了大量的研究工作。
1996年,欧盟为保持自身在科学技术和制造业的霸主地位,组织知名大学和大型企业,如比利时鲁文大学、德国阿亨工业大学、DOIMAK数控磨床公司、西班牙ZAYER数控铣床公司、西班牙工业研究中心和意大利三坐标测量机公司等单位研究数控设备热影响的基础理论和变形规律,并从实际应用角度探求减少或消除热变形的途径。他们研究的主要成果如下。
① 数控机床热影响与机床局部点的温度变化相关,特别与机床整体的温度动态时变相关。
② 对于机床温度变化引起的机床热变形,可采用非线性回归方程、小波变换及神经网络等建模方法建立模型。
③ 目前,减小机床热变形的有效方法主要包括:设计有利于消除或减小热变形的机械结构,隔离产生热的热源,热平衡发热元件和在线检测温度与变形补偿。
④ 三坐标测量机所处环境对三坐标测量机等精密检测设备的精度影响极大;三坐标测量机的台面结构、导轨形式对设备热变形的影响也很大。
国内从20世纪60年开始研究机床热误差,浙江大学、上海机床厂和北京机床研究所等高校、企业和研究机构最早在机床热变形研究方面做了很多工作。浙江大学梁允奇教授是我国较早开展机床热变形基本理论问题研究的学者之一,1982年他主持出版的高校统编教材《机械制造中的传热与热变形基础》是国内率先全面、系统地论述机床热变形的资料,书中详细论述了有关热变形的基本概念、热源及热传导、热与热变形等基本理论和方法,做了大量基础性工作,为后来进一步研究机床热变形问题提供了很好的借鉴。清华大学项伟宏等研究了TH6350卧式镗铣高速加工中心主轴热行为,通过相关与非相关分析,目的是筛选出影响很小的参变量,同时建立多因素非线性回归分析模型,计算出加工中心主轴热变形。非线性回归分析计算值与加工中心主轴热变形实际测量值对比分析得出,所建立的多因素非线性回归分析模型与加工中心主轴热变形实际测量值基本一致。
就如何保持数控机床热变形抗变换性(鲁棒性),上海交通大学杨建国等提出了一种针对鲁棒性机床热变形建模方法,它借鉴了传统建模方法,所开发的温度采集系统,能减小或消除白噪声对模型参数的影响,保证基于新建模型开发的温度采集系统干扰最小。
目前机床热变形数学模型可分为经验模型和数值模型。基于经验模型建立的数学模型主要是:通过实验分析法和多变量线性或非线性回归法建立数控机床敏感点的温度,及其对应点的热变形值,并建立自变量和因变量之间的关系表达式。数值模型建立方法主要采用小波分析、神经网络分析法、FEA法建立机床温度场与热误差之间的表达式。经验模型的缺点是温度测量点数量有限,温度传感器的数量合理值和位置的选择难以优化;数值模型由于分析方法复杂,可能导致计算时间长,采用FEA法存在边界条件不易确定,不易在在线补偿机床热变形中实际应用。加拿大学者M.H.Attia提出的GMM法(Generalized Modelling Methodology)具有数值计算效率高、数值模拟精度准等优点,是研究机床热变形理论和应用的一种新方法。
1.2.2 机床热变形测试
(1)机床温度场测试仪器
检测数控机床热变形区域温度的仪器可分为接触式和非接触式两种类型。接触式测温仪器主要包括半导体点温计、热敏电阻、热电偶、贴附式温度计和棒状温度计;非接触式测温仪器主要包括红外线热像仪和点式热像计。
棒式温度计的原理是玻璃管内液体热胀冷缩。一般有水银温度计和酒精温度计两种。可用于机床循环油、冷却液及周围环境温度的测试。贴附式温度计是将一块导热性能好的金属块套在棒状温度计的液体泡的一端,主要用于测量机床表面的温度。
上述两种温度测量仪器使用方便,其测量精度可达0.2℃,主要用于测量固定测量点的温度。
由NiO、MnO2等粉末按一定比例烧结而成的热敏电阻,依据电阻大小随着温度的升高而下降的特性设计。热敏电阻测温灵敏度高,可以达到0.002℃左右。在实际检测物体温度时,在热敏元件的外部需要布置保护层,这样就降低了它的测量精度。所以,它主要用于粗略测量数控机床敏感部位的温度。
热电偶温度计基于热电偶材料的热电效应制成。常用的热电偶材料为铜-康铜、铜-铁、铝-铬、白金-铂铑等。用热电偶测量温度灵敏度高,使用方便,在国内外机床测试中广泛采用,其测量精度可达0.05℃。
红外线热像仪接收发热体发出的红外线热量,经内部处理后显示物体的温度。吉林大学热工实验室购买的日本航空株式会社生产的TVS-2000型红外线热像仪,其温度测量范围达-40~2000℃,2000℃时的测量精度可达±0.4℃,该仪器具有连续监测整台机床的温度变化的功能。采用热像仪拍摄的热像图,可以清楚、全面地看到所监测部位的温度分布情况和各点温度大小,目前红外线热像仪的精度可达0.05℃。图1-3为西安交通大学赵汝嘉教授使用瑞士生产的AGA780SW远红外热像仪,测量ZOO3/1007三坐标测量机龙门框架温度场分布情况拍摄的图片。

图1-3 ZOO3/1007三坐标测量机龙门框架温度场分布
(2)机床热变形测量仪器
机床热变形测量仪器有接触式和非接触式两种。接触式热变形测量仪主要有电感测微仪、千分表和水准仪。非接触式热变形测量仪主要有激光干涉仪、电涡流传感器、气动测微仪、电容式传感器和全息照相装置等。激光干涉仪(laser interferometer)的测量精度高达0.01μm,目前国内外已广泛使用激光干涉仪测量机床热变形。
1.2.3 接触面热阻对机床热变形影响的研究
机械设备零部件之间,无论是固定接触面和滑动接触面,它们的接触刚度大小不一,零部件接触面的热阻大,零部件接触面区域的热变形显著。20世纪70年代,加拿大M.H.Attia教授最先分析接触面与机床热变形之间的关系,在机械工程领域知名杂志《Annals of the CIRP》上发表了题为“On the role of fixed joints in thermal deformation of machine tool structure”一文,在文中引出“接触面”的概念,研究了接触面实际状态的基本情况,及其如何影响热变形,而机械零部件接触面的热变形又通过接触面处形成的热应力,反过来影响接触面的形态。图1-4为接触面处于普通接触状态(不完全接触),接触面热变形与接触热应力相互作用的过程。20世纪70年代,M.H.Attia又提出了接触面的非线性热变形状态,研究了材料的线性、非线性与接触面几何形状的非线性而产生的热-材料-机械-应力-变形之间的闭环相互作用,创建了接触面非线性热变形基本理论。20世纪90年代,浙江大学居冰峰教授等针对接触面传热过程影响因素多、模型难以准确建立和求解复杂的特点,对TKA1969落地镗铣床模型主轴箱与立柱接触区域结构的热接触行为进行FEA混合法分析,为研究接触面的热变形提供了一种新思路和新方法。

图1-4 接触面闭环相互作用示意图
1.2.4 减小机床热变形的途径
(1)改变机床零部件结构形式及材料
① 改进机床零部件设计结构 改进机床结构是减小机床热变形的最基本方法。研究人员通过多年的基本理论研究和试验分析,发现了在机床零部件热变形过程中,因机床主轴箱主轴相对于基准面的位置差异,会产生不同的热变形。图1-5中,Fy为切削力的大小和作用方向,当主轴相对于主轴箱产生热变形时,图1-5(a)中主轴箱主轴在水平方向的热变形远小于图1-5(b)中主轴箱主轴在水平方向的热变形。

图1-5 基准面位置对主轴箱主轴热变形的影响
20世纪70年代,日本学者吉田嘉太郎在他的研究成果中引出了“热源对中面”的术语,他指出如果将影响加工精度的零部件设计在热源对中面上,就可减小机械零部件的热影响,提高零部件的加工精度。并且,该学者将这一思路成功地应用在新改造的双立柱龙门式加工中心,双立柱龙门式机床比原先单立柱悬臂式机床前后左右的热误差小很多。以主轴箱主轴对中的左右对称双立柱设计结构,就是利用了热对称设计这一原则。
杭州机床集团有限公司的MB7650型端面磨床热变形,为控制机床主轴轴向热变形量(最大时可达0.08mm左右)引起的工件尺寸超差及精度降低问题,首先改善了机床主轴的润滑条件,另外在壳体1和前主轴2之间设计了一个过渡套筒3,如图1-6所示。壳体1和套筒3只在壳体1的左端接触,右端和孔壁不接触。如果主轴2因轴承发热而向左端热变形时,那么套筒3只能水平向右热伸长,并使整个主轴向右热伸长,自动补偿了主轴向左的伸长量,消除了机床主轴热变形对加工精度的影响。

图1-6 主轴部件的结构改进
1—壳体;2—前主轴;3—套筒
机床主轴速度日益提高,目前工业发达国家生产的高速加工中心主轴最高转速高达100000r/min,主轴轴承的发热及采用新技术研制的新型轴承,是机床研究者最关注的目标,如采用磁力轴承、液体静压轴承和气体静压轴承等新型轴承来减小机床热变形。
② 采用新型机床结构材料 机床基础件所用的金属材料受热后,其变形量与温度、尺寸密切相关,又和材料的热膨胀系数成正比。因此,采用热膨胀性能优越的新型材料是从根本上消除热变形的一个重要途径。
1917年,联邦德国施莱辛格通过研究得出用混凝土制作机床基础件可以明显减小热变形,三十年后,伯林格公司实现批量生产混凝土车床,而且节约了大量钢材。
采用人造花岗岩,又称聚合物混凝土,来制造机床的零部件能得到较好的动态刚度和热刚度,其原因在于人造花岗岩的振动衰减系数大约是铸铁的10倍,热导率仅为铸铁的1/35,而且耐腐蚀、尺寸稳定性好,但韧性差,难承受剧烈冲击。20世纪70年代后,瑞士的乔治·费舍公司、原联邦德国的伯林格公司、德克尔公司以及意大利的诺曼公司等陆续制造了用人造花岗岩生产的机床零部件。其好处是不但可以降低生产成本,而且可以很好地改善机床的动刚度和热刚度。
为了更好地改善高精度机床、坐标测量机的使用性能,近些年人们开始研究采用陶瓷与结晶玻璃等复合材料加工成机床基础件。例如,日本东京精密公司潜心研制了一台小型机床,它的床身、导轨、立柱、横梁和工作台等都用结晶玻璃制造。结晶玻璃的热变形很小,铸铁的热膨胀系数约是结晶玻璃的100倍。
20世纪80年代开始,北京机床研究所、上海机床厂等先后从事新型机床结构材料的研究。例如,上海机床厂和同济大学合作,研制成功了钢筋混凝土床身。同济大学还与北京第二机床厂合作,系统地研究了人造花岗岩材料的性能和在机床设计与制造中的应用,按所研制的材料配方,设计制造的人造花岗岩在较宽的工作温度、工作频率范围内具有高强度、大阻尼、耐腐蚀、较短的固化时间等优点,其蠕变、热变形和收缩等均能满足工作要求,当时已经达到日本和德国同类产品的最好水平。使用上述配方研制成功的M1420外圆磨床,突破了国内外只能用人造花岗岩材料设计、制作机床支承件的惯例。
(2)采用热流控制技术控制机床热变形
机床基础件热源产生部位较多,热源产生的热量常常以不同的传导方式传入零部件,引起非均匀的温度分布,造成机床热误差。减小或消除热源的不利影响,控制热流动是减小机床热误差最常采用的方法。
① 强制冷却控制温升 采用冷却技术,使机床工作过程中由于摩擦或热源传播的热量转移到非敏感部位,是减小机床热变形的重要途径之一。
日本研究者垣野义昭发现坐标镗床加工时,机床工作台与主轴中心之间发生较大的位移,通过采用模拟方法对机床内部热源进行强制冷却的方法试验,结果如图1-7所示。不采用冷却措施时,机床运转6h后,经测量,主轴中心与工作台之间发生了190μm的热位移,而且还有继续增加热位移的趋势;采用强制冷却措施后,主轴中心与工作台之间热误差减小到15μm,而且热平衡时间控制在2h以内。再如,美国加利福尼亚大学提出并试验了一种新的强制冷却控制温升方法——喷油冷却。图1-8为对超精密加工工艺系统从外部进行喷油雾冷却的原理。它把已经处于恒温的冷却油,用速度为150L/min、以雾状喷在用密封罩封闭起来的整个系统。油的温度严格控制在(20±0.6)℃。它的热导率是859.85W/(m·K)。喷油的温度与工艺系统的温度差为0.5℃。采用这种措施,不但克服了超精密加工工艺系统内空气对流和热辐射的影响,并且冷却面积也增大了,整个工艺系统能够一直处于恒温状态,采用这种措施保证了由于环境温度变化引起的加工误差减小到1/10。

图1-7 冷却与热位移的关系

图1-8 喷油冷却原理
1—机床;2—工件;3—玻璃罩;4—加热器;5—传感器;6—冷却水温度控制系统;7—油温控制系统;8—开关;9—热交换器;10—过滤器;11—泵;12—气垫
② 设置人工热源控制机床热变形 热源是导致热误差的来源,但也可作为机床热变形控制的手段。例如,把人工热源设计在机床外或机床内的理想位置,通过改变理想位置热源产生的热量,平衡机床热误差,是一种方便可行的方法。该方法的优点是热平衡时间变短,热误差平衡性稳定等,已在数控机床开发中得到应用。如英国的600家集团(Group-600)生产的数控铣床,美国莫尔(Moore)公司生产的坐标磨床,以及瑞士豪塞(Hauser)厂生产的2A3型坐标镗床,均采用系统控制方法调节设置的平衡热误差热源。如图1-9所示,设置在机床主轴箱的温度检测元件a和机床立柱内的温度检测元件c组成一个回路,设置在机床工作台内进给机构的温度检测元件d和机床立柱上的温度检测元件b也构成一个回路。依据上述回路输入、输出关系式,对控制系统中的发热装置和冷却装置的整个电路进行控制,通过平衡热变形,以实现控制工作台相对主轴箱主轴的位置。当控制系统设置的温度比机床主轴箱温度低时,接通冷却器开关;反之,则接通加热器开关。

图1-9 通过加热补偿热变形
1—主轴箱;2—主轴;3—立柱;4—工作台;5—底座;6—风扇;7—加热器;8—进给机构
③ 采用热管技术控制机床热变形 目前,为控制机床各部位的温度变化,常常采用比较直观、简单易行的强制冷却方法,但是当数控机床中流动的润滑油和冷却液不断循环过程中,时刻产生热能,可采用低温热交换的方法冷却润滑油和水冷、油冷和空气等冷却剂,如此不断循环,这样即避免了润滑液和冷却液变成“持续不断的热源”。在机床工作过程中,如果某些敏感位置的热能难以用前述方法减小或消除;或者即使能够减小或消除,但会造成机床结构复杂或明显增加成本,或需添加额外装置,此时可研究是否适合采用“热管”。
热管技术是1963年美国Los Alamos国家实验室的George Grover发明的,热管作为新型传热元件,利用了热传导与相变过程。其特点为结构简单、导热性好、温度场分布均匀,在生产实践中得到很好的应用。近年来,它作为一类技术成熟的热量传导和温度控制产品,在精密制造领域中得到很好地应用。热管工作的基本原理如下。热管一般由端盖、管壳、吸液芯组成,使用时,必须先将热管内抽成真空,呈负压状态,然后再充以一定量的传热流体,保证吸附在热管内表面的吸液芯毛细多孔材料中填充全部液体,并确认密封。热管的一侧为加热部位,另一侧为冷却部位,依据实际需要,可在热管两段中间布置绝热部位。当热管的一侧加热、温度升高时,毛细多孔材料中的流体蒸发、汽化,蒸发的气体在微小的压差下运动到另一侧,放出热量后凝结成流体,流体再沿多孔材料在毛细力的作用下流回蒸发段。如此往复循环,实现了热量由热管的一侧传至另一侧。热管在完成热能传递的过程中,一般包括以下六个互相联系的主要步骤:热能从源头通过热管管壁和填充工作流体的吸液芯传递到液、汽分离界面;流体在蒸发侧内的液、汽分离界面上蒸发;蒸汽腔内的蒸汽从蒸发侧流到冷凝侧;蒸汽在冷凝侧内的汽、液分离界面上凝结;热量从汽、液分离界面通过吸液芯、液体和管壁传给冷源;在吸液芯内由于毛细作用使冷凝后的工作液体回流到蒸发侧。其工作原理如图1-10所示。

图1-10 热管工作原理
20世纪80年代,H.Sugishita在设计新型加工中心时将热管放置在混凝土制作的立柱和主轴箱中,如图1-11所示,由于混凝土的热导率远远小于铸铁的热导率,产生的热量不易散出,因此在混凝土制作的立柱和主轴箱内部聚集着很多热量。在立柱和主轴箱上安装了热管以后,可使立柱和主轴箱内部产生的热量快速散发出去,具有较好的热特性。

图1-11 使用热管的加工中心示意图
受热管技术的启发,浙江大学陈子辰教授根据物体相变时温度不变而有热量传递的原理,研究了在机床中使用恒温结构件来控制机床立柱的温度场,达到控制热误差的目的。其原理是采用相变材料,利用其潜热特性,把机床立柱内材料相变过程中吸收或放出一定的热能传递出去,而温度却保持恒定的特点。如果结构件表面的温度大于相变材料的相变温度,热量便传到相变材料,产生固-液相变,这时它就吸收相变热能,而结构件温度仍然是相变温度或变化较小;当零部件表面温度小于相变材料的相变温度,热量便传到零部件,产生液-固相变,此时它就放出热能,而零部件温度保持不变或变化较小。试验时选用的材料为芒硝(主要成分是Na2SO4·10H2O),并添加一定比例的核剂硼砂和一定比例的颗粒状铝粉,试验表明,其相变温度一般为20℃左右。选择合适的相变材料,并将其应用在机床零部件的温度控制中,可以取得较好的机床零部件热变形控制效果。只要选择好合适的相变材料,应用在适宜的温度环境中,就能很好地发挥相变材料的作用。
④ 控制环境温度 精密设备周围环境温度变化对其影响较大,机械加工中的三坐标测量机、精密机床和超精密加工机床受环境温度的影响必须控制。图1-12为日本东京农工大学工学部西胁信彦教授等建立的设备环境温度变化引起机床立柱热变形的几何模型,结合实际情况,假定机床立柱的底面和内腔不与周围环境发生热传导,外表面与周围环境发生热交换,其自然对流系数为13W/(m2·K),图1-13是机床立柱前后表面的温度变化情况,图1-14为立柱前面、后面伸缩和立柱倾斜结果。

图1-12 立柱的数值计算模型

图1-13 立柱的前面、后面温度随室温的变化
1—环境温度;2—立柱前面温度;3—立柱后面温度

图1-14 立柱的热变形
1—立柱倾斜;2—前面伸缩;3—后面伸缩
为消除环境温度周期性变化对机床加工精度的影响,常常将机床安置在恒温车间或恒温室中。沃茨教授将三坐标测量机放置在恒温工作室中,恒温工作室的温度通过空调调节,将温度变化控制在±0.1℃范围内。并且,要求操作者在恒温工作室外操作机床,以消除人体体温等因素对机床精度的影响。
(3)热变形补偿
采用热管方法控制机床热变形需要复杂的附加机构,采用空气调节器控制环境温度存在运行成本高、需要额外的空间等缺陷。为更好地消除数控机床的热变形,随着计算机技术和控制技术的发展,德国和日本等国家,从20世纪70年代开始研究利用数控机床数控装置的控制功能,通过在线检测与闭环控制的方法,实现机床热变形的在线测量与实时补偿。20世纪80年代,德国柏林工业大学U.Heise以机床热变形的在线测量与实时补偿为主要内容完成了他的博士学位论文。1984年,日本学者小岛辉一利用一台高精度数控机床进行试验,通过测量、分析、反馈、补偿等环节实现了热变形的自动补偿。通过安置在机床主轴箱上的自动检测系统,检测主轴前后方向的热变形量,再通过数控装置反馈,计算补偿量并实时补偿。热变形实时补偿的特点是直接测量或间隔计算出热误差,目前已经成为一种主要的解决机床热误差方法,由于存在对检测装置的精度要求高、安装复杂、数学模型难以准确建立、鲁棒性差等,目前难以在普通工作环境下推广应用。
德国阿亨工业大学M.Weck教授在《Annals of the CIRP》发表了“Reduction and compensation of thermal errors in machine tools”一文,全面深入总结了数控机床热位移实时补偿的研究情况。在文中,作者将热位移补偿分为间接热位移补偿和直接热位移补偿。间接热位移补偿是指利用有关热变形基本理论构建温度-热误差量数学模型,然后得到机床所确定温度测量点的热变形大小,最后利用数控机床配备的数控装置或外加辅助控制装置完成热误差的检测与修正。直接热位移补偿就是直接测量出某些点的位置变化量,进而推断机床热误差变化量,最后利用补偿手段修正误差值。
在国内,2012年上海交通大学王维利用几何与热的复合误差综合建模方法,采用激光干涉仪完成了数控机床进给系统定位误差的检测,分析了环境温度对数控机床进给精度的影响。由于现场工况的不确定性,采用将各种误差分离的方法,用分段的线性函数拟合,然后根据影响因子加权处理,建立了高精度的温度-热变形数学模型,其中温度传感器采用测量精度为0.05℃的NiCr-Ni热电偶,采用LabVIEW 的数控机床综合误差补偿系统进行数据采集和处理。图1-15是热变形在线补偿原理图。该装置补偿的工作原理是:通过传感器对机床温度进行在线测量,CNC 上的控制程序定时采集机床温度,经A/D转换后,通过接口板输入CNC系统。通过对采集的数据进行处理,并利用温度-热变形数学模型计算,计算出机床的热变形量,从而判断是否需要发出补偿脉冲信号。若需要发出,则该信号经接口板输入CNC系统,CNC系统按照补偿信号发出补偿进给量,伺服电机就精确地完成机床热变形引起的误差补偿。

图1-15 数控机床热变形在线补偿原理图
上海交通大学杨建国等开发的机床热变形补偿系统框图如图1-16所示。热误差补偿系统主要由四个温度传感器、配有桥接电路的调整板、A/D板及车削加工中心控制系统等组成。首先利用布置在车削加工中心的四个温度传感器实时采集机床敏感部件的温度大小,然后经调整板将电阻信号转换为电压信号并放大,经A/D板进入车削加工中心的控制装置,控制装置根据热误差建模方法计算出补偿量,对进给刀架的进给运动实行实时控制,实现修正热变形误差量。补偿前后对比表明,工件尺寸误差一般可缩小到原来的1/3,热误差补偿效果明显,零件加工精度得到提高。

图1-16 热变形补偿系统框图
齿轮绿色成形加工工艺不再使用切削油,是发展的重要方向,但干式滚切工艺将导致更为严重的机床热变形,影响齿轮加工精度。作者利用某高速干切滚齿机床,采用基于齐次坐标变换原理建模高速干切滚齿机床的热变形误差,推导出热位移公式,并通过热变形试验进行了应用验证。
2012年,同济大学张曙教授发表了“机床热变形:机理、测量和控制——机床产品创新与设计”一文,综合论述了近年来有关机床热变形机理、测量和控制的最新研究成果。
一年四季环境温度的周期性变化是影响精密机床几何精度不可避免的客观因素,通过改变机床设计思想实现机床精度的保持性,以吉林省机电研究设计院采用自准直原理研制的新型自准直导轨磨床最具代表性,它在不增设任何补偿控制装置的条件下,利用床身自重自动补偿由环境温度变化引起的床身导轨在垂直平面内的热变形,这一原理和设计方法具有实用价值。