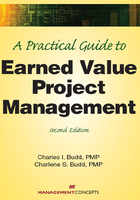
CHAPTER 3 Earned Value Metrics
Our first discussion point is the metrics. Even if you do not plan a full-blown earned value management system implementation, you must understand this most important part of the system.
Earned value metrics play an increasingly important role because project management is now recognized as a desirable professional skill. Many organizations require project management applicants to be certified by a recognized professional organization. To acquire any professional project proficiency designation, such as the Project Management Institute’s Project Management Professional certification, you will have to master certain metrics.
PRIMARY METRICS
There are four primary EV metrics. The names given first in the following paragraphs are more popular in industry and are becoming more universally adopted. The second names are those originally used, which are most often the primary references in government documents.
Total Value (TV) or Budget at Completion (BAC)
The first EV measure, total value or budget at completion, is prepared in the planning stage before the project is begun. Total value more accurately should be called total cost or total budget, but we’ll use the term “value.” TV is developed by examining all the work to be accomplished on the project and the estimated cost of each portion of work. The budget and the project schedule then become the baseline against which the project progress is measured. Remember that this metric is established before work is begun. Having all required information prior to beginning work sometimes is referred to as a “full kit” concept.
As work on the project progresses, EVMS requires periodic status reports. At each status point, three periodic measures are used to report the project status and to derive other report metrics. The first two are budgeted costs, and the last one is actual costs. Another distinction is that the first metric represents scheduled work, and the last two are for completed work. They are:
The budgeted cost (planned value) for the work scheduled to have been completed
The budgeted cost for the work actually completed (earned)
The actual cost of the work actually completed (performed).
Planned Value (PV) or Budgeted Cost of Work Scheduled (BCWS)
At each status reporting date, the portion of the project’s planned value or BAC corresponding to the elapsed time from the beginning of the project to the status date details both the work that should have been completed and the costs that should have been incurred. The U.S. Department of Defense calls this subset of BAC the budgeted cost of work scheduled; others refer to it as planned value. BCWS or PV is the dollar value of the work that was scheduled for completion by this point in the project’s schedule.
Earned Value or Budgeted Cost of Work Performed (BCWP)
This periodic measurement shows the original estimated costs for work actually completed. This can be the most confusing of the basic measures because it uses both an actual measurement and a budget measurement. It is a measure of the work actually performed during the status period, but at its planned (budgeted) amount—not its actual cost. Both EV and PV typically represent cumulative-to-date values, but this additional label is seldom used.
Actual Cost (AC) or Actual Cost of Work Performed (ACWP)
The actual costs incurred from the beginning of the project represent the third periodic measure. Note that costs incurred (direct or indirect costs used on the project) are not necessarily the same as costs paid in cash. Like the other two basic periodic status measures, this is usually a cumulative amount.
Again, the terminology can be confusing. We would prefer to use the term actual value to maintain the “value” terminology, but although we might point out occasional inconsistencies in term definitions, in this book we use those that are more generally accepted in industry.
Reporting and Comparison Metrics
We have presented the four basic measurements as TV or BAC, PV or BCWS, EV or BCWP, and AC or ACWP. Other major reporting metrics that are derived from these basic measures are cost and schedule variances, their related ratios, and future performance estimates. The variances are designed to illustrate the difference between planned and actual project performance; the ratios are relative metrics that can be compared across projects.
The cost variance (CV) is the difference between the budgeted cost of work actually performed (EV) and the actual cost of that work (AC). The formula for the cost variance is EV – AC or BCWP – ACWP.
The CV’s related ratio is the cost performance index (CPI). The formula is EV / AC or BCWP / ACWP. The schedule variance (SV) is the difference between the budgeted cost of the work actually completed (EV) and the budgeted cost of work scheduled for completion (PV). The formula for schedule variance is EV – PV or BCWP – BCWS. The SV’s related ratio is the schedule performance index (SPI). The formula is EV / PV or BCWP / BCWS.
The formulas are designed so that a positive amount represents favorable performance, and a negative amount signals unfavorable performance.
In addition, there are two forecasting metrics: an estimate to complete the remainder of the project (ETC) and an estimate at completion (EAC). These can be more easily explained after a look at an analogy to the standard cost system and some example calculations of ratios.
An emerging practice in EV uses an additional measurement called earned schedule (ES), which is presented in Part VII.
ANALOGY TO THE STANDARD COST SYSTEM
A perfect analogy to EV analysis is found in a standard cost system. If you have ever taken a management accounting class, you probably were exposed to the bar or triangle approach to calculating variances in a standard cost system. This triangle approach also can be applied to compute EV variances, as shown in Figure 3.1.
CALCULATION OF RATIOS
The cost and schedule variances are absolute amounts that are influenced by the size of the project and thus are difficult to compare with performance on other projects. Converting the variances into schedule and cost ratios standardizes them.
FIGURE 3.1 Standard Cost System and EV Triangle Approaches
The SPI is the result of dividing the EV (at the top of the EV triangle illustrated in Figure 3.1) by the PV (bottom right of the EV portion of Figure 3.1); the CPI is the result of dividing the EV by the AC. The SPI and CPI are relative measures, and they enable comparisons across projects. Further, these two indices, or ratios, are included in formulas used to produce a host of other metrics that provide estimates of total cost at completion. They also are used in an index ratio that measures the additional effort required to complete the project, which can be used to compare performance on many different projects.
The SPI, therefore, shows schedule completion (the EV) on the measurement date relative to planned completion by that date. A ratio of 1 indicates that EV and PV are identical. An amount greater than 1 indicates a favorable performance; an amount less than 1 indicates unfavorable performance.
The CPI indicates the cost performance that should have been achieved for the project portion completed—the EV relative to the costs actually incurred as of the status date. A ratio greater than 1 indicates favorable performance (compared with the baseline budget), while a ratio less than 1 means that actual costs are higher than were expected for the work completed.
In an EV system, we never make any comparisons across the bottom of the triangle—ACWP and BCWS (actual cost and planned value). Although computing this variance makes sense in certain environments, such as in standard cost systems where the standard costs applied during the period are computed for work actually completed, it is uninformative and can be misleading for projects. This total variance merely indicates that actual costs do not equal the amounts budgeted as of the time elapsed since the project started, and it is meaningless without knowing how much of the project’s work has been completed.
Forecasting Metrics
So far we have seen from the standard cost triangle how the EV can be compared against the PV and the AC to calculate the project’s performance variances and the related performance indices. We can now use the CPI (and the SPI) to predict the project’s remaining cost and its total revised cost.
The two predictive metrics are called the estimate to complete (ETC) and the estimate at completion (EAC). And, as you might have expected, a ratio also can be calculated for the ETC, and it is called the to-complete performance index (TCI). Generally, only the CPI is used to calculate the ETC, but a more realistic number could include the SPI by multiplying the two together. The formulas for ETC, EAC, and TCI are:
sometimes modified to show the impact of SPI as well: . To differentiate this ratio from the more common version shown just above, this ratio is often called the critical ratio.
Estimate at Completion (EAC) = Actual Cost + Estimate to Complete, or AC + ETC.
Now let’s see how these formulas work, using a simple example.
Calculations Example
A status is taken at the end of week 2 for a 12-week project. The total planned budget for the project is $120,000 for work that is evenly spread over 12 weeks. The project staff has completed work that was scheduled to have been completed by halfway through the middle of week 2. Actual costs incurred to date on this project total $16,000. Figure 3.2 shows the tasks and costs involved.
FIGURE 3.2 A 12-Week Project
To-Complete: Calculations that consider only the CPI provide the most optimistic estimates:
Alternative to Complete: Calculations that take into account both the CPI and the SPI provide more pessimistic estimates:
EAC = $16,000 + $149,333 = $165,333 ($45,333 more than the original estimate to complete)
USING THE MEASUREMENTS
Calculations and measurements can be used in many different ways and accomplish a variety of objectives. Remember, however, that calculating the metrics is only a small part of managing an EVMS project.
The Challenge of Meeting All Targets
Striving to be successful, project managers want to look good on both cost and schedule metrics simultaneously. Textbooks and EV implementation research usually warn that a cost variance and a schedule variance should never be “netted” together. One source specifically cautions that “[a] poor cost variance combined with a good schedule variance does not mean that everything is all right” (Humphreys 2002, 675).
Because meeting the schedule may be critical to the customer—meaning we must meet SPI targets—project teams may be encouraged to spend as much time as necessary to meet SPI targets. At the same time, meeting cost targets is probably critical to the company responsible for completing the project. Therefore, project teams also are pressured to spend as few hours as necessary to meet CPI targets. Project managers are expected to expend the necessary resources to meet SPI targets while at the same time feeling strong pressure to use as few resources as necessary to meet CPI targets.
This conflict between the two metrics typically leads to alternating compromises, as shown in the abbreviated cause-effect diagram of an EV system (Figure 3.3).
W. Edwards Deming (Deming 1993, 101–103) emphasized the importance of distinguishing between two kinds of variation: common cause variation (variation within the capability of a system to repeatedly produce results—a system in control) and special cause variation (variation beyond the capability of a system to repeatedly produce results, usually variation with causes outside the system—an out-of-control situation). Attempting to “fix” common cause variation worsens the results by overcorrecting an in-control process to an out-of-control state. The same concept applies to projects. That is, responding to small variances by making frequent project adjustments very likely will result in decreased project performance.
FIGURE 3.3 Cause-Effect Diagram
Obviously, there are possible tradeoffs between CPI and SPI. For example, to improve poor schedule performance, additional costs (e.g., overtime, acquisition of additional resources) might be incurred. Another scenario is that the schedule might be put on hold until prior resource commitments have been fulfilled, thereby reducing the need for additional costs but resulting in schedule slippage. The attempt to keep both measures on track instead of making appropriate decisions to complete the project frequently results in conflicted behavior.
Attempting to remain on schedule, as reflected in SPI, and stay within budget, as reflected in CPI, means that project managers will try to make both metrics look better by constantly adjusting behavior to garner better performance on each metric. Because of a tradeoff effect, focus on an unfavorable SPI (or CPI) naturally makes the CPI (or SPI) metric worse. The conflict between spending as few hours as possible and spending as many resources as necessary means that attempting to improve both SPI and CPI simultaneously practically ensures that neither metric will improve.
Neither metric improves because the actions intended to make each metric look better mean that shortcuts and temporary patches may quickly cause other problems. These activities make remaining project tasks even more difficult, and a downward spiral ultimately and inevitably results in failure to meet any of the targets.
Information and Motivation
We must have measurements to communicate progress, but an ideal indicator of performance may be especially difficult to find. Arrow (1971, 278) showed that all measures of performance are not equally easy to measure. Thus, performance metrics adopted by organizations are constrained by practicality and cost. It should not be surprising that not all critical dimensions of project performance are measured and reported.
One Size Does Not Fit All
Robert Austin (1996, 216) partitions measurement into two categories: motivational measurements, which are explicitly intended to affect behavior, and informational measurements, which are used primarily for the information they convey. He maintains that informational measurements should be used to improve decisions and should not be used to effect behavioral changes.
EV metrics provide information to project owners, but they may inadvertently affect the behavior of project team members attempting to perform to those metrics. In fact, it is as true today as when described by Flamholtz (1979, 71–84) that accounting measurements are simultaneously intended to facilitate multiple functions, including accountability, performance evaluation, and motivation, and to provide information for decision-making. This “one size fits all” objective of internal managerial accounting information must be questioned, just as many analysts recently have questioned the appropriateness of one financial report for external users.
Managers who have made decisions on the basis of their impact on the next quarter’s results or annual report rather than the long-term health of the organization for all stakeholders have been severely criticized and punished by the market. Analogously, making project decisions on the basis of an imperfect measurement system that does not measure all critical dimensions of project performance is detrimental to ongoing project process improvement, possibly to project completion, and certainly to project success.
Decision Metrics
In any event, there are some clear implications for any organization that implements EVMS. First, the EV metrics that are a source of information for stakeholders must not be the only information used to make project decisions. That means that the EV metrics must not be used to determine how work should proceed. Project decisions must be based on sound project management practices. Project team members must be motivated to complete a project as quickly as possible and at the lowest cost. Decisions must be made using real-time data, not based on historical data or the impact of the decision on data to be reported in the future.
A 1990 study by Beach illustrated that, as early as 15 percent into a project, EV metrics can predict the ultimate completion date and project cost (Fleming and Koppelman 2000, 39). However, EV measures may not track closely with project performance early in the project. Therefore, management may have to be careful not to be too hasty in demanding corrective action if initial reports show unfavorable EV variances. Management must avoid forcing project people into the destructive spiral of chasing improvement on one EV metric at the expense of another.
At the same time, some projects, for any number of reasons, will not deliver the intended results. These projects should be killed early to release resources for more valuable work. Rarely are such failures the fault of the project teams, and cancellation should not reflect unfavorably on individual performance.
Response to Measurements
Finally, organizations must be very aware of the behavioral responses to measurements and be extremely careful in designing performance evaluation systems. If Austin is correct, motivation and information metrics must be separated to minimize dysfunctional worker behavior. Establishing appropriate organization measurements is hard work, and it may require that management not be allowed access to all the detailed information measures that the project staff needs to do its best work. There are no easy answers where performance evaluation is involved.
Management’s not having access to nonaggregate information that workers have might mean that management must place more reliance on the subjective judgment of supervisors and fellow employees.
Now that you have completed this chapter, you are well on your way to understanding the metrics of EVMS. You will have the opportunity to practice your knowledge and ability with the sample problems in the Discussion Questions and Practice Calculations section.
The metrics of EVMS are based on a standard accounting system but have their own nomenclature. The primary measures are:
1.Total value (TV) or budget at completion (BAC) for the project—the original budget prepared at the initiation of the project.
2.Planned value (PV) or budgeted cost of work scheduled (BCWS)—the dollar amount of the work that was planned to be completed by the date of the status report.
3.Earned value (EV) or budgeted cost of work performed (BCWP)— the budgeted dollar amount of the work that has been completed by the date of the status report.
4.Actual cost (AC) or actual cost of work performed (ACWP)—the dollar amount incurred (charged to the project) by the date of the status report.
From these basic metrics, cost and schedule variances can be calculated to indicate project progress. The variances can be converted to ratios and indices to facilitate comparisons across projects. Further calculations then can be used to predict the final cost of the project. There are many challenges in preparing and using measurements. The project manager must be aware of the informational and motivational aspects of using metrics, as well as the potential consequences.
It can be very difficult for project managers to meet both the schedule and cost requirements of the baseline plan, and this conflict can lead to dysfunctional behavior. Although the measurements can provide valuable information to stakeholders, the dark side is that the metrics can be misleading if other good project management techniques are not employed.
DISCUSSION QUESTIONS AND PRACTICE CALCULATIONS Questions
1.Name and describe the three points of the EVMS standard cost triangle.
2.Discuss the strengths and weaknesses of using the EVMS metrics.
Practice Calculations
FIGURE 3.4 Project Plan for Practice Calculations
Use Figure 3.4 to calculate EVMS metrics for the following test problems:
Plan at end of second quarter: Tasks 1, 3, 5, and 6 should be completed; Tasks 2 and 4 should be 96 percent complete; and Task 7 should be 51 percent complete.
Results at end of second quarter: Tasks 1, 3, 5, and 6 have been completed; Task 2 is 50 percent complete; Task 4 has not been started; and Task 7 is 10 percent complete. $137,500 has been charged to the project.
Calculate the following values (assuming that all tasks incur costs uniformly over time):
1.At project initiation, what was the total projected cost of this project (BAC or TV)?
2.On the status date, what is the budgeted cost of work scheduled (BCWS or PV)?
3.What is the actual cost (AC) of this project on the status date?
4.What is the earned value (BCWP or EV) of this project on the status date?
5.Calculate the cost variance (CV) and the cost performance index (CPI).
6.Calculate the schedule variance (SV) and the schedule performance index (SPI).
7.Compute the “optimistic” and “pessimistic” estimate at completion (EAC).