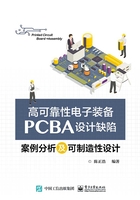
前 言
在产品全生命周期中,设计对产品的性能、质量和成本控制起着关键的作用。一般情况下,设计费用约占产品总成本的8%,却决定了产品总成本的大约80%,而约80%的设计差错要到制造使用过程中才能发现。
业内人士公认的“十倍定律”表明,如果在概念设计阶段发现并改正一个错误所需费用为1,那么改正同一个错误,在详细设计阶段所需费用为10,而在生产制造阶段所需费用为100,并直接导致制造周期的延长。
随着科学技术的飞速发展,现代电子产品的构造和功能越来越复杂,在保证产品性能、质量要求的前提下,如何降低制造成本和缩短产品的生产周期,是市场竞争的关键。
产品生产中的质量问题大部分是由设计所造成的;实行可制造性设计,把问题尽可能消灭在设计阶段是提高产品设计质量的根本措施。
美国HP公司统计表明:产品总成本60%取决于产品的最初设计,75%的制造成本取决于设计说明和设计规范,70%~80%的生产缺陷是由于设计原因造成的。
我国航天部门统计表明:一个航天型号产品的质量问题80%出在电装焊接上,而造成电装焊接质量问题的主要原因是电路设计缺乏可制造性。
中国电子科技集团(中国电科)统计表明:电子产品的质量问题75%出在电装焊接上,而造成电装焊接质量问题的主要原因是电路设计缺乏可制造性。
如果一个企业没有可制造性理念,不建立可制造性设计文化,也就根本谈不上成果转换,谈不上产业化、规模化!
我们的很多产品,尤其是军工电子产品,往往以数量代替质量,以反复延长研制生产周期的方法来取得质量,这种状况与企业做大做强,做国内卓越、国际一流的目标是背道而驰的。
可制造性设计(Design For Manufacture,DFM)与可靠性设计(Design For Reliability,DFR)、可组装性设计(Design For Assembly,DFA)同属卓越设计(Design For X,DFX)的核心内容,它与集成产品开发(Integrated Product Development,IPD)里的共享基础模块(Common Building Block,CBB)都属于并行工程理念;DFM主要研究产品本身的物理设计与制造系统各部分之间的关系,并把它用于产品设计中,以便将整个制造系统融合在一起进行总体优化。
通过这种方法可以降低成本、缩短产品投入市场的时间、提高产品质量、提高产品的可制造性、缩短生产时间、提高工作效率。
DFM不仅是使用一套规则(包括设计规则和工艺规则)对设计进行可制造性审查,还是通过产品研究开发、生产制造和售后服务的全系统工艺控制流程,向设计提供共享基础模块(CBB),以及把设计和工艺结合起来、把工艺和工艺过程控制结合起来的系统工程。
这里的设计包括产品设计、开发过程设计和系统设计。在产品设计时,不但要考虑功能和性能要求,而且要同时考虑与产品整个生命周期各阶段相关的因素,包括可制造性、高效性和经济性等。
笔者在中国电科第10研究所和中国电科从事军用电子装备电子装联技术/SMT研究半个多世纪,20世纪60年代初开始参与航空、航天、通信、侦察、识别等军事领域电子系统工程及设备全方位、全过程电子装联工艺工作,1979年开始任航天外测安全系统某产品整机负责人,1986年该整机获“国家科技进步特等奖”,2001年创新性地提出“电路可制造性设计技术”,2003年该技术成为企业标准,“十五”期间任总装先进制造技术项目负责人,多次荣获所级科研成果一等奖。
本书的基础是《电路可制造性设计》,该资料于2005年由四川省电子学会SMT专委会首次作为电子装联技术培训教材使用,之后历经多次修改和补充,作为电科内部和航天、航空、兵器等军工集团,以及国防科工局和相关协会、学术团体与培训机构的培训教材,深受好评,并作为“航天电子产品设计工艺性”的主要参考书之一。
2008年,在以中国工程院院士童志鹏为总编,程辉明为主编,中国电科相关研究所总工程师、副总工程师为副主编的《先进电子制造技术(第二版)——信息化武器装备的能工巧匠》一书中,把“电路可制造性设计”列为先进电子制造技术。
本书的主要内容已列入中国电科承担的国防科工局“印制电路板焊接工艺质量控制”研究课题主要成果“印制电路板焊接工艺质量控制”,并作为中国电科内部文件下发所属各研究所实施。
当前电子制造业界还没有一本系统介绍电子装备电子装联可制造性设计的书籍;本书和计划中的《高可靠电子整机可制造性设计(DFM)及装联工艺技术》这两本书的出版,将着力从设计源头解决电子产品可靠性和质量问题,与众多电子装联技术书籍形成良好的互补。
本书在编撰过程中学习、参考和引用了一些专业技术书籍、内部文件及标准里的资料和图片,在此表示衷心的感谢。
陈正浩
2018年12月于成都