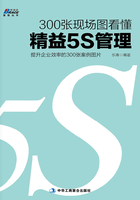
2.如何提高库存周转率

图3-2 物料区改善前
图3-2是没有做5S管理的现场,在这样的现场要找一个东西怎么找?经验丰富的老师傅知道大概在某个位置,新来的员工几乎要崩溃,半天找不到物料。
这样的现场为什么会拉长作业周期?简单举三个例子。
例1:现场的物料没有固定位置存放,不能保证人人都知道每个物料放在哪里。每个人放的位置不一样,每天都花很长时间找物料,这是生产环节的浪费——动作浪费、时间浪费、寻找浪费、无效工作时间浪费。
例2:现场的半成品没有固定位置存放一样会造成浪费。
例3:右图现场空间狭小,进出极其不便,影响生产周期。改善后是什么样的?给大家看世界上最顶尖的企业——丰田的案例。

图3-3 丰田公司物料周转区
图3-3是丰田公司物料周转区,看图中标注的箭头。
箭头1:货位区域明确标识,让员工知道具体位置。放的人知道放在哪里,取的人知道去哪里拿。时间是不是缩短了?成品生产周期是不是提高了?
箭头2:每个周转筐都有编码、品名、型号、数量、厂家、送到哪个工序等信息。丰田的这个标识卡可以直接用扫码机扫码,快速便捷,缩短生产周期。
箭头3:地面货位定位摆放,每类物料固定放在一个位置,谁都知道在这个位置,不需要找,提高了周转率,所以5S管理不仅仅是搞卫生。
丰田几乎是零库存,怎么做到的?
第一,丰田要求供应商的厂址必须距离丰田厂址200公里内。
第二,供应商用的所有报表与丰田的一样。
第三,准时化数量,比如明天丰田要生产985辆汽车,要求方向盘供应商明天几点几分送985个方向盘,要求轮胎供应商明天几点几分送3940个轮胎。
送到公司后怎么办?一般公司是:供应商→质量抽检验收→库房暂存→需求部门领用→车间使用;丰田是:供应商→车间使用,把中间环节全部取消,直接进入生产线进行组装。
怎么控制质量?丰田是最终成品出来后检查,出现问题供应商直接赔偿。丰田要求供应商100%保证品质,当年大野耐一推行这套管理体系时也受到供应商抵触,最后多次与供应商谈判才摸索出这个模式。