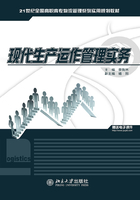
第4章 统计质量控制
学习目标
(1)学生应掌握统计过程控制的含义,了解统计过程控制的作用和特点。
(2)掌握控制图构造的基本原理,熟悉统计控制状态的基本概念。
(3)掌握常规统计控制图作用、类型和制作方法。
(4)理解过程能力的含义。
(5)理解抽样检验的概念,并能熟练应用。
工作任务描述
通过对本章知识框架的学习,学生应了解统计过程控制的基础知识,熟悉统计过程控制的发展演化过程,掌握统计过程控制的基本原理和方法。熟悉统计控制图的原理,掌握控制图的制作方法。理解过程控制的概念,能够进行过程能力分析。理解抽样检验的基本概念,并能够熟练应用。
本章任务
(1)理解统计过程控制的概念和理念,熟悉统计过程控制的方法和工具。
(2)按照过程控制的目的,对过程能力进行分析,并能对过程进行控制。
(3)掌握抽样检验的相关方法,并能熟练运用。
工作任务实施
统计质量控制工作的一般步骤如下:
(1)建立控制标准。
(2)确定控制对象。
(3)实施监控。
(4)利用控制图进行判别。若不正常,及时启动异常处理程序;若正常,则进行下一步。
(5)维持生产过程。
(6)进行过程能力分析。
(7)根据分析结果,对过程能力进行改善。
统计质量控制主要是指应用统计分析技术对生产过程进行实时监控,科学地区分出生产过程中产品质量的随机波动与异常波动,从而对生产过程的异常趋势提出预警,以便生产管理人员及时采取措施,消除异常,恢复过程的稳定,从而达到提高和控制质量的目的。图4.1给出了统计质量控制流程图。

图4.1 统计质量控制流程图
4.1 统计过程控制
从20世纪30年代休哈特提出统计质量控制原理到现在,已有70多年历史。戴明和朱兰在20世纪40年代和50年代发展了这些原理,并在实践中得到了证明,获得了极大的成功。尤其在80年代以后,随着西方工业社会意识到品质复兴的必要性,在戴明思想的主导下,统计过程控制的推广应用已经是现代化工业生产的代名词之一。
4.1.1 统计过程控制的概念
统计过程控制(Statistical Process Control, SPC)是一种借助数理统计方法,对过程中的各个阶段进行评估和监察,建立并保持过程处于可接受的并且稳定的水平,从而保证产品与服务质量的一种过程质量管理工具。
它通过对检测数据的收集,对生产过程进行分析评价,及时发现系统性因素出现的征兆,引发预防措施消除其影响,防止批量不良,并能评估决策者所采取的改进措施的有效性,以使质量得到持续的改善,使过程维持在仅受随机性因素影响的受控状态,以达到“事前预防”的效果,从而有效控制生产过程、不断改进品质。
统计过程控制着重从以下3个方面对过程进行改进:
(1)过程能力的稳定维持。
(2)过程能力的分析与改善。
(3)阻挡不良品的进入、流出。
4.1.2 统计过程控制的发展背景
20世纪20年代,美国贝尔电话实验室成立了两个研究质量的课题组,一个是由休哈特博士领导的过程控制组;另一个为道奇领导的产品控制组。其后休哈特提出了过程控制理论和具体的工具,道奇则提出了抽样检验理论。
统计过程控制技术的出现标志着质量管理从被动的事后检验把关阶段,发展到事前预防为主的现代质量管理时代。
统计过程控制提出后,在欧洲和美国的企业中得到广泛的采用,第二次世界大战后,经济遭受严重破坏的日本在企业中全面推行统计质量控制,经过30年的努力,日本跃居世界质量与效率的领先地位,目前,统计质量控制技术在全球范围内的制造企业中已得到推崇和普及运用。图4.3给出了SPC的发展简史。

图4.2 SPC发展简史
4.1.3 统计质量控制的数理统计基础
1.数据的类型
1)计量值数据
测量结果的数据可以是连续的,也可以是不连续的数据,如长度、重量、电流和温度等。
2)计数值数据
不能连续取值的,只能以个数计算的数为计数值数据,如不合格品数、缺陷数等。
2.总体和样本
把所研究的对象的全体称为全及总体,也叫做母体,或简称为总体。
通常全及总体的单位数用N来表示,样本单位数称为样本容量,用n来表示。相对于N来说,n则是个很小的数。它可以是总体的几十分之一乃至几万分之一。
3.数据的特征值
数据特征值是数据分布趋势的一种度量。数据特征值可以分为两类。
集中度:平均值、中位数、众数等。
离散度:极差、平均偏差、均方根偏差、标准偏差等。
1)表示数据集中趋势的特征值
(1)频数。计算各个值反复出现的次数,称为频数。
(2)算术平均值。如果产品质量有n个测量数据xi(i=1,2, …, n),平均值为:。
如果测量数据按大小分组,则平均值为:。
(3)中位数。数据按大小顺序排列,排在中间的那个数称为中位数。用Me表示。当数据总数为奇数时,最中间的数就是;当数据总数为偶数时,中位数为中间两个数据的平均值。
(4)众数。众数是一组测量数据中出现次数(频数)最多的那个数值,一般用M0表示。
2)表示数据离散度的特征值
(1)极差。极差是一组测量数据中的最大值和最小值之差。通常用于表示不分组数据的离散度,用符号R表示。
R=xmax-xmin
(2)平均差。将每个数据减去平均值,并把它们的差值的绝对值相加再除以测量数据的总个数,即得到平均差,用AD表示。
当数据没有分组时:。
当数据为分组数据时:(注:f为各组对应的频数)。
(3)标准差。标准差是各数据偏离平均数的距离的平均数,它是离差平方和平均后的方根,用σ表示。标准差是方差的算术平方根。标准差能反映一个数据集的离散程度。平均数相同的,标准差未必相同。
当数据没有分组时:。
当数据为分组数据时:。
用标准差作为度量,通过直接比较两组数据的标准差的大小就可看出两组数据离散程度的大小。
4.最常见的概率分布
连续随机变量最重要的分布——正态分布,表达形式为

式中,μ为总体的算术平均值;σ为总体的标准偏差。
如果令Z=(x-μ)/σ,那么可以得到正态密度函数标准化形式为

图4.3 μ与σ间的关系
4.1.4 统计过程控制图
控制图于1924年由美国贝尔电话研究室的休哈特创立,后来由戴明博士在美国和日本广为推行。由于它操作简单、效果明显、便于掌握,因此逐渐成为质量管理的重要工具。
控制图是画有控制界限的一种图表,其基本形式如图4.4所示。

图4.4 控制图的一般图示
假定产品的质量标准为μ,如果只在往随机性原因影响,不发生系统性偏差,则随机抽取一件产品。其质量特征x应该满足
xi~N(μ, σ 2), i=1,2, …, n
根据正态分布原理:μ-3σ≤xi≤μ+3σ的概率为99.73%,这就是说,如果生产过程是正常进行的,不存在系统性原因影响,那么产品质量的观察值超出[μ-3σ, μ+3σ]范围的可能性不到1%,是一个小概率事件。小概率事件由于发生的可能性较小,通常在少数试验中是不可能出现的,一旦出现了,就有理由认为生产过程有系统性原因在起作用。据此,可以确定出控制图的管理界线,其中,质量标准μ为中心线(CL);μ+3σ为控制上限(UCL);μ-3σ为控制下限(LCL)。
控制图是用来区分质量波动是由偶然因素还是系统因素引起的,从而判明过程是否处于统计控制状态的一种工具。使用控制图时,将特征统计量的一系列观察值依次标在图上。若这些点全部落在上、下控制限内,而且点的排列没有什么缺陷(如同侧链、周期、靠近控制限等),则判断过程处于统计控制状态;否则认为过程异常,须查明原因,加以消除。
为控制过程处于稳定状态,人们希望能及时掌握并控制总体的分布情况,即控制总体的参数μ和σ。但μ和σ总体的值,只有等到全部零件加工出来以后才能知道,另外,一些产品经过测量就不能用了(如保险丝的熔断时间、零件的抗拉极限、小孔表面的光洁度检查等),因此,在生产过程中直接控制总体的μ和σ值往往是不可能的。解决这一问题的办法是从总体中抽取样本,根据样本的检查结果,运用统计量来推断总体的分布状态,进而判断过程是否处于稳定状态。
控制图的作用和价值:第一,过程控制,计量值控制图可以用来查明过程中心的变化或过程变异,进而采取纠正措施,以保持或恢复过程的稳定性;第二,过程能力分析,若过程处于稳定状态,可用控制图中的数据估计过程能力;第三,测量系统分析,结合反映测量系统固有变异的控制限,显示测量系统是否有查明过程或产品的变异的能力,用于监控测量过程;第四,因果分析,通过控制图形态与过程事件间的相关性,有助于判断并查明变异的根本性原因,并策划有效的纠正措施;第五,持续改进,可用于监控并识别过程变差,以及可减少变差的原因。
为有效地使用和解释控制图以及了解过程变差来源,科学地抽取过程样本是重要的关键。一般采用整群抽样的办法,这样做的目的是要保证组内仅有偶然原因的影响,而不会存在异常原因的影响,而异常原因的影响应体现在组与组之间的差异上。短期过程因不能提供足够的数据,故难以建立适宜的控制限,在这种情况下不宜建立和使用控制图。应用控制图会出现两种错误。第Ⅰ类错误(弃真):将正常判为不正常,即过程未发生变化时判为发生了变化;第Ⅱ类错误(纳伪):将不正常判为正常,即过程已发生变化时而判为未发生变化。孤立地看,哪种错误都可以避免。加宽控制限,可使犯第Ⅰ类错误的可能性减小;紧缩控制限,可使犯第Ⅱ类错误的可能性减小,但同时避免两种错误却是不可能的。
控制图的种类很多,下面按计量值、计数值控制图来说明统计控制图的做法。
1.计量值控制图
这些控制图主要用于质量特征是长度、重量、强度、密度、纯度、时间等计量值的情况。各种计量值控制图在应用条件和选择的统计量上有所区别,表4-1列出了各种控制图的适用场合、特点及其各种统计量。
表4-1 计量值控制图

上述符号的意义及计算公式如下:
(1):总平均值。
,
为第i组样本的平均值。
(2):极差平均值。
,Ri为第i组样本的极差。
(3):标准差平均值。
,
, Si是第i组样本的标准差。
(4):中位数的平均值。11 k i i x~x~= ∑k =,x~为第i组样本的中位数。
(5):
图中的特征量x的平均值,
,k为累积抽样的个数。
(6):移动极差的平均值。
,RSi= xi-xi-1。
其他均是与样本大小有关的系数,可以在控制图系数表中查到。
2.计数值控制图
常用的计数值控制图有:不合格品率控制图(p图)、不合格品数控制图(pn图)、单位缺陷数控制图(u图)和缺陷数控制图(c图)。这些图不要求质量特征值X近似服从正态分布,但计数值一般服从二项分布。当质量特征难以计量测定,或者考察质量着眼于不合格品或缺陷时,宜采用计数值控制图。计数值控制图当然不像计量值控制图那么精密,但也有其长处,即比较省事,且可采用现成的统计资料。表4-2列出了各种计数值控制图的适用场合、特点及其各种统计量。
表4-2 各种计数值控制图

3.控制图的观察分析
控制图是按3σ原则构造的,其犯第Ⅰ类错误的概率α=0.27%,这就是说当过程处于控制状态时,仍有0.27%的极小可能使测量数字的点跑到控制界限以外。由于α值取得比较小,则犯第Ⅱ类错误的概率β就较大,这就是说当过程稍有变化时,测量数据的相应点也可能不会越出控制界限。为此,对控制图有如下判断原则,判断过程是否处于稳定的控制状态,必须同时满足下列两个条件:
(1)控制图上的点全都在控制界限以内,即没有点出界。
(2)界限内的点排列正常。
1)界限外的判断
关于第一个条件,因为用少量数据作控制图容易产生错误判断,所以规定至少在下述情况下才可以认为过程处于控制状态。
(1)连续25点以上处于控制界限内。
(2)连续35点仅有1点超出控制界限。
(3)连续100点中不多于两点超出控制界限。
2)界限内的判断
在稳定的控制状态下,点是在界限内随机波动的,没有特别明显的规律性和顺序性,且多数点在中心线附近,只有少数点散落在控制界限附近。界限内的点如有下列情形,就不能判断过程为控制状态。
(1)多数点处于中心线的一侧:一系列点连续出现在中心线一侧时,这种现象称为“链”,链的长度用链内所含点的数量来衡量,如图4.5所示。
① 出现5点链时,应注意过程的变化;出现6点链时,应开始调查原因;出现7点链时,判断过程为异常,需采取措施。
② 连续11点中至少有10点位于同侧,或连续l4点至少有12点位于同侧,或连续17点至少有14点位于同侧,或连续20点至少有16点位于同侧,判断过程为异常。

图4.5 异常过程示意图
(2)上升(或下降)趋势:连续7点上升(或下降)时,应判断过程异常,如图4.6所示。

图4.6 上升、下降趋势示意图
(3)点出现在控制界限附近:在中心线与控制线间作三等分线,若在最外侧的1/3带形区域内存在下列情况之一,即可判定过程异常。
① 连续3点中有两点处于此带内。
② 连续7点至少有3点处于此带内。
③ 连续10点至少有4点处于此带内。
(4)点的排列显示周期趋势:当点的排列显示周期性时,有必要调查是否存在异常原因。
4.2 过程能力
产品是生产制造出来的,与其质量直接有关的是生产过程,过程稳定是产品质量的保证。过程是5M1E因素同时起作用的结果,显然随着影响质量因素的变化,过程也经常不断地发生波动。过程波动主要反映出生产过程的稳定与否,但这种波动最终体现在质量波动上,因此需要通过质量变异的分析来刻画。过程能力是指过程在一定时间内处于统计控制状态下的实际加工能力。过程处于控制状态是指:①原材料或半成品按照标准要求供应;②过程按作业标准实施并应在影响过程质量各主要因素无异常的条件下进行;③过程完成后,产品检测按标准要求进行。
在稳定的生产状态下,影响过程能力的偶然因素近似地服从正态分布,为便于过程能力的量化,用3σ原理来确定其分布范围:由于分布范围取μ± 3σ时,产品质量合格的概率可达99.73%,因此用6σ为标准来衡量过程的能力是具有足够的精确度和良好的经济特性的。实际计算中记过程能力为B,则B=6σ。
4.2.1 过程能力指数
1.过程能力指数的定义
由于受到5M1E的影响,要使同一批产品的质量特性完全一样根本做不到,于是人们转而求其次,给产品质量制定一个容许变化的界限,只要质量特性在这个范围之内波动都是可以接受的,一旦超出才被定性为不合格。人们关注的是有没有不符合规格标准的产品出现,所以,除了考查6σ值的大小外,还要把它与规格容许变化的范围(即公差)进行比较。
令T为公差范围,又称公差带,TU为公差上限,TL为公差下限,T=TU-TL
过程能力指数又称工序能力指数、工艺能力指数,用Cp表示,定义为

显然,过程能力指数是产品质量规定的变化范围与产品质量实际变化范围相比较的结果。通常,人们就是依据Cp来判断过程实际能力的。
2.过程能力指数的计算
1)双向公差
如果公差的范围既有上限要求也有下限要求,这就是双向公差问题。对于双向公差过程能力指数的计算,要区分质量总体均值μ与公差中心M是否相等两种情况。
(1)如果质量总体均值μ与公差中心M相同,即μ=M,可以直接运用公式计算过程能力指数。但有两点需要注意:
① σ是总体质量离散性指标,事先需要用样本资料进行估计。
② 如何判断μ是否等于M,由于μ是总体质量均值,也是不知道的,故只能根据样本均值x与M的比较来确定。
【例4-1】 某零件内径尺寸公差为,从加工这种零件的生产线上抽取了200个做检查,得到
, s=0.008,试计算工序能力指数Cp。
解:由给定的资料,公差中心为

由于,可以直接利用公式进行计算,得到

(2)μ≠M。按道理,当质量特征均值与公差中心要求不相符时应该调整过程,如果是系统性原因造成的,首先应重点加以消除。但有的时候μ与M的差别很小不值得调整,或者调整过程困难较大,这时也可以计算过程能力指数。计算的公式为

其中,k和Cp
′确定的方法是

【例4-2】 某零件内径尺寸公差为,从加工这种零件的生产线上抽取了200个做检查,得到
, s=0.008,试计算过程能力指数Cp。
解:由给定的资料,公差中心为

由于,所以先计算k,

再计算Cp,

2)单向公差
仅仅规定了上限或下限的公差,称为单向公差。如电子产品要求使用寿命不能低于多少小时,成品的杂质率不能超过一定的百分比等。
单向公差的过程能力指数的计算公式可由双向公差的过程公式引申而来,具体计算方法是

由正态分布的对称性,应有TU-μ=μ-TL;并用x替代μ,用s替代σ。
所以,对于只有公差上限的,
对于只有公差下限的,。
【例4-3】 在流水线上抽取样本容量为100的样本20个,测得不合格品有80个,当允许样本不合格品数(np)μ=10,试计算过程能力指数C p。
解:首先计算

将下限公式变形为

【例4-4】 某电子元件的使用寿命其规格要求至少要达到3000小时,现从一批产品中随机抽取200件,经过实验得到, s=100,试计算过程能力指数Cp。
解:这里仅规定了公差下限,所以

4.2.2 过程能力评价
过程能力对产品质量而言至关重要,过程能力大,生产过程稳定,产品质量变化就小;反之,过程能力小,过程波动程度大,出现不合格品的机会就多。可以说,过程能力折射着生产合格品的水平。
由过程能力指数的计算公式可知,过程能力的大小同σ的关系十分密切。σ的值大,过程能力小,反之亦然。实践中,人们根据质量保证要求、生产费用等方面的综合考虑,给出了Cp的参考值:
(1)C p>1.67。对于普通产品而言,Cp大于1.67说明加工能力过剩,为了降低费用,可以适当放宽对产品质量波动的限制。
(2)1.33<C p≤1.67。这表明过程能力充足,一般不会出现不合格品,对非关键性的质量特性可以放宽波动的要求,日常的质量控制应该用控制图进行。
(3)1.00<C p≤1.33。就普通产品来说,这时的过程能力尚可,但需要用控制图进行严密观察,以防出现较大的波动,特别是Cp接近于1.00时,出现不合格品的可能性非常大,应加强对5M1E因素的检查。
(4)0.67<C p≤1.00。过程能力不足,应重视分析造成波动较大的原因,并采取相应的改进措施,另外,要加强产品检查力度。
(5)C p≤0.67。Cp小于0.67,说明过程能力较差,经常出现不合格品,这时应该对过程进行大幅度的调整,对已经生产出来的产品最好进行全检。
需要指出的是,以上给出的评价标准适用于一般产品的制造过程,不能把它们理解为统一不变的模式。有些高精尖产品,过程能力指数往往要求大于2。
4.2.3 过程能力控制图
1.分析用控制图
分析用控制图用于分析生产过程是否处于统计控制状态。若经分析后,生产过程处于统计控制状态且满足质量要求,即工序能力达到了设定标准,则可以把分析用控制图转为控制用控制图;若经分析后,生产过程处于非统计控制状态,则应查找过程失控的异常原因,并加以消除,去掉异常数据点,重新计算中心线和控制界限线。若异常数据点比例过大,则应改进生产过程,再次收集数据,计算中心线和控制界限线;若经分析后,生产过程虽然处于统计控制状态,但不满足质量要求,则应调整生产过程的有关因素,直到满足要求方能转为控制用控制图。
2.控制用控制图
控制用控制图由分析用控制图转化而成,它用于对生产过程进行连续监控。按照确定的抽样间隔和样本大小抽取样本,计算统计量数值并在控制图上描点,判断生产过程是否异常。控制用控制图在使用一段时间以后,应根据实际情况对中心线和控制界限线进行修改。
4.3 抽样检验
从居家过日子到国家重大经济决策都离不开抽样检验。比如说,到水果摊买橘子,于是你从一大堆橘子中抽取一个尝一尝,你尝的目的是要通过这一个橘子的质量情况来推断这一大堆橘子的质量情况。显然抽样检验的目的是:通过样本推断总体。样本是样品的集合,一个样本可由一个样品组成,也可由多个样品组成。欲达到通过样本推断总体这样的目的,要通过3个步骤:抽样、检验、推断。其中抽样这个步骤含有两个内容:怎么抽;抽多少。检验这个步骤与抽样检验的理论没有关系,不同的产品、不同的质量特性使用不同的检测设备,有不同的检验方法。推断即用对样本的检测结果来对总体进行推断。抽多少与怎样推断就构成了抽样方案。
4.3.1 抽样检验的由来与发展
抽样检验的研究起始于20世纪20年代,那时就开始了利用数理统计方法制定抽样检查表的研究。1944年,道奇和罗米格合著发表了《一次和二次抽样检查表》,目前这套抽样检查表在国际上仍被广泛地应用。1974年,ISO发布了《计数抽样检查程序及表》(ISO 2859—1974)。
我国也在ISO标准同等采用基础上建立了抽样检验国家标准GB 2828—87《逐批检查计数抽样程序及抽样表》。此外,我国于1991年发布了GB/T 13262—91《不合格品率的计算标准型一次抽样检查及抽样表》(适用于孤立批的检查)等国家标准。
4.3.2 抽样检验的定义
在检验过程中,通常根据是否检验全部商品,可以分为全数检验和抽样检验两种形式。
所谓全数检验,就是对全部产品逐个地进行测定,从而判定每个产品合格与否的检验。它又称全面检验、100%检验。其处理对象是每个产品。
抽样检验不是逐个检验作为总体的检验批中的所有单位产品,是按照规定的抽样方案和程序仅其中随机抽取部分单位产品组成样本,根据对样本逐个测定的结果,并与标准比较,最后对检验批做出接收或拒收判定的一种检验方法。简言之,按照规定抽样方案,随机地从一批或一批过程中抽取少量个体进行的检验称抽样检验。
4.3.3 基本概念及术语
1.群体与样本
群体就是被调查(或检查)的对象,或者称采取措施的对象,也常称为批,群体(批)大小常以N表示,也称批量N。
工序间、成品、进出库检验以及购入检验等经常以整批的形式交付检验的。不论是一件件的产品,还是散装料,一般都要组成批,而后提交检验。有时候,中间产品由于条件的限制不允许组成批以后再提交给下一道工序,也可采用连续抽样检验(如每小时抽取1台产品进行检验)的抽样方式。
样本就是指从群体(或批)中抽取的部分个体。抽取的样本数量常以n表示。
2.批的组成
构成一个批的单位产品的生产条件应尽可能相同,即应当由原、辅料相同,生产员工变动不大,生产时期大约相同等生产条件下生产的单位产品组成批。此时,批的特性值只有随机波动,不会有较大的差别。这样做主要是为了抽取样品的方便及抽样品更具有代表性,从而使抽样检验更为有效。如果有证据表明,不同的机器设备、不同的操作者或不同批次的原材料等条件的变化对产品质量有明显的影响时,应当尽可能以同一机器设备、同一操作者或同—批次的原材料所生产的产品组成批。构成批的上述各种条件通常很少能够同时满足。如果想使它们都得到满足,往往需要把批分得比较小,这样品质一致而且容易追溯。但这样做,会使检验工作量大大增加,反而不能达到抽样检验应有的经济效益。所以,除产品品质时好时坏、波动较大、必须采用较小的批以保证批的合理性外,当产品品质较稳定时(比如生产过程处于统计控制状态),采用大批量是经济的。当然,在使用大批量时,应当考虑到仓库场地限制以及不合格批的返工等可能造成的困难。
3.批量
一批产品中所包含的单位产品的总数叫做批量,通常用英文大写N表示。一批塑胶料由1000袋组成,可以说这批塑胶料的批量为1000。对于500双袜子来讲,一个单位产品只可能是一双(对)而绝不可能是一只,批量就是500。一批100kg合成纤维,如果规定每10g纤维为一个单位产品,那么这批产品的批量为10000。
当从成品、半成品、零部件中抽取一部分样本加以测定分析时,决不是仅为获取抽出样品本身的信息或状况,而是要从样本的检验结果判定群体(或该批量,或该工程)的状态,以便对群体采取措施。
4.取样及数据的信赖性
进行取样及记录数据是为了将来采取行动措施。如果取样及数据记录是不可靠的,必然导致将来采取的行动措施出现偏差或无效。
为了取样可靠,应以随机抽样为原则,也就是说取样要能反映群体的各处情况,群体中的个体被取样的机会要均等。例如,按以下方法执行,能大致符合随机抽样的精神。
(1)物品在不断移动时,可用一定间隔抽取样本或设定时间抽取样本的方法,但一定间隔本身也要以随机规定为宜。
(2)在已经包装好零部件的箱中取样。尽可能用上、中、下层均等取样。如纸箱是一捆捆包装的,从顶部抽样当然方便,但并不合理。
(3)如果是流体物品,则应尽可能搅拌均匀后再取样。
(4)按比例抽样。如果组成一个批的产品的原材料来源不同、生产日期与班组不同,有可能对产品品质有较大影响,此时应把此批产品分为若干层,按比例在各层抽检,即尽可能抽检到每批材料、每个生产日期与每个班组。
4.3.4 抽样方案分类
1.按产品质量特性分类
(1)计数抽样方案:单位产品质量特征值为计点值(缺陷数)或计件值(不合格品数)的抽样方案。
根据规定的要求,用计数方法衡量产品质量特性,把样本的单位产品仅区分为合格品或不合格品(计件),或计算产品的缺陷数(计点),据其测定结果与判定标准比较,最后对其做出接收或拒收决定的抽样方案。
(2)计量抽样方案:单位产品质量特征值为计量值(强度、尺寸等)的抽样方案。
凡对样本中的单位产品的质量特征进行直接定量计测,并用计量值为批判定标准的抽验方案称为计量抽验方案。这类检验的优点是计算检验的信息多、判定明确,一般适用于关键特性的检验。
对一般的成批成品抽验常采用计数抽验方法;对于那些需作破坏性检验以及费用极大的项目,一般采用计量抽样方法。
2.按抽样方案的制定原理来分类
(1)标准型抽样方案:该方案既保护生产方利益,同时保护使用方利益,预先限制生产方风险α的大小而制定的抽样方案。
(2)挑选型抽样方案:所谓挑选型方案,是指对经检验判为合格的批,只要替换样本中的不合格品;而对于经检验判为拒收的批,必须全检,并将所有不合格全替换成合格品。
(3)调整型抽样方案:该类方案由一组方案(正常方案、加严方案和放宽方案)和一套转移规则组成,根据过去的检验资料及时调整方案的宽严,以控制质量波动,并刺激生产方主动、积极地不断改进质量。该类方案适用于连续批产品。图4.7所示为调整方案的转移规则示意图。
① 正常转为加严。在采用一般检查水平抽检时,如果质量变为低劣,则应由正常检验转换为加严检验。加严意味着样本大小n不变,但合格判定数A变小。
② 加严转换为正常。当采用加严方案时,如果连续5批抽检合格,则转为正常抽检。
③ 正常转为放宽。如果连续批检验发现质量稳定,则可将正常检验方案转为放宽方案。

图4.7 调整方案的转移规则示意图
3.按抽样的程序分类
(1)一次抽样方案:仅需从批中抽取一个大小为 n 的样本,如果样本的不合格品个数 d不超过某个预先指定的数c,判定此批为合格,否则判为不合格,如图4.8所示。

图4.8 一次抽样方案(n, A)
一次抽样的优点在于方案的设计、培训与管理比较简单,抽样量是常数,有关批质量的情报能最大限度地被利用。其缺点是抽样量比其他类型大;在心理上仅依据一次抽样结果就做判定欠慎重。
如果采用方案(n, c)来检验,那么“判断此批合格品”的概率或者说“接收概率”就要依赖于批不合格品率p。p越大,接收概率越小,即这个“接收概率”是批不合格品率p的函数,记为L(p), L(p)又称为抽检方案(n, c)的抽检函数。把L(p)画在坐标上,就得到了抽样特性曲线,简称OC曲线,如图4.9所示。

图4.9 理想的抽样方案
由生产者和消费者协商确定一个批不合格品率 p0,当 p<p0时,要求100%地接收,即L(p)=1;当p>p0时,要求100%地拒收,即L(p)=0。这就构成个理想的抽样方案,要想达到这种理想境界,唯一的办法是进行准确无误的全检。因此,这样的抽样方案实际上是不存在的,因为即使100%全检,有时也会有错检和漏检。
检验过程中,存在如下两种错误:
① 第一种错误,就是可能把合格批判为不合格的。当 N=1000, n=10, c=0时,作出的OC曲线,不合格品率的标准是p=5%。假如实际检验的p是2%时,比标准要求的质量要高,应判合格。但从OC曲线可以看出,在100次检查中,仍有2次左右被判为不合格,这就产生了第一种错误,对生产者是不利的,所以又称生产者风险,用α表示。
② 第二种错误,假如实际检验为20%,质量很差但是由于是抽样检验,在100次中,仍有10次可能判为合格而被接收,于是生产了第二种错误:把不合格批判为合格批。这对消费者不利,所以称为消费者风险,用β表示。
(2)二次抽样方案:抽样可能要进行两次,对第一个样本检验后,可能有3种结果:接收、拒收、继续抽样。若得出“继续抽样”的结论,抽取第二个样本进行检验,最终做出接收还是拒收的判断,如图4.10所示。

图4.10 二次抽样方案示意图
(3)多次抽样:多次抽样可能需要抽取两个以上具有同等大小样本,最终才能对批做出接受与否判定。是否需要第i次抽样要根据前次(i-1次)抽样结果而定。多次抽样操作复杂,需做专门训练。ISO 2859的多次抽样多达7次,GB 2898—87为5次。因此,通常采用一次或二次抽样方案。
知识拓展
5M1E分析法
造成产品质量的波动的原因主要有6个因素。
(1)人(Man/Manpower):操作者对质量的认识、技术熟练程度、身体状况等。
(2)机器(Machine):机器设备、工夹具的精度和维护保养状况等。
(3)材料(Material):材料的成分、物理性能和化学性能等。
(4)方法(Method):这里包括加工工艺、工装选择、操作规程等。
(5)测量(Measurement):测量时采取的方法是否标准、正确。
(6)环境(Environment):工作地的温度、湿度、照明和清洁条件等。
由于这6个因素的英文名称的第一个字母是5个M和1个E,所以常简称为5M1E。6要素只要有一个发生改变就必须重新计算。
精益质量管理中“精益”的核心工具是“JIT指令”,即实现生产经营各环节间“准确的产品、准确的数量、准确的时间”。根据作业系统的构成,JIT指令可逐层分解形成作业系统的JIT指令、各作业子系统JIT指令、各作业工序的JIT指令。JIT指令的特征是要求各作业子系统间的协作,要求各子系统中各作业工序间的协作。“精益”的管理目标是通过各级JIT指令的实现以达到整个作业系统的JIT,从订单交付角度看就是要达到订单交付时“准确的产品、准确的数量、准确的时间”,实现客户满意。
JIT指令包含产品质量上、产品数量上、交付时间上的三方面要求,JIT向企业生产系统提出了很高的挑战,企业生产系统中质量保证、效率保证、数量衔接是JIT应用的基础。实施JIT指令必然需要企业对生产作业系统进行评估和优化。即要在准确分析各工序的生产能力、工序能力、资源耗用及价值创造等基础上,优化组合形成保证JIT实现的作业流程。
精益质量管理中“质量”的核心工具是“Cpk指标”,即工序能力评价指数。根据作业系统的构成,Cpk指标在作业工序Cpk指标基础上,根据作业体系构成,形成各作业子系统Cpk指标和作业系统的Cpk指标。Cpk指标是衡量作业工序加工精确度和加工准确度的综合指标。Cpk指标是作业工序质量能力评价的指标,可作为质量的要求,也可反应实际质量状况。Cpk指标是保证JIT实现的重要条件。
JIT三方面要求均可借鉴六西格玛管理中西格玛水平度量方法进行评价,Cpk指标也可用西格玛水平来近似评价。总体看,精益质量管理针对效率和质量分别提出了JIT要求和Cpk指标,并可总体用西格玛水平来度量。管理改进的重要基础就是度量,精益质量管理通过对作业系统和作业工序的定量化度量以促进管理改善。
精益生产管理提出了JIT要求,却未借鉴六西格玛管理方法对JIT进行度量评价,精益生产提出了为下一道工序交付准确的产品,却未结合实际质量状况进行评价和应对,而以“零缺陷”一笔带过。六西格玛管理强调了度量的作业,并给出了“西格玛水平”这个度量工具,却未针对作业系统JIT要求进行度量。可见,综合精益生产和六西格玛各自优点的精益质量管理弥补了双方各自的不足,在针对作业系统和作业工序的JIT要求和度量、Cpk要求及评价方面具有应用价值,能克服原有孤立方法在作业系统管理改善效果方面的不足。
精益质量管理研究目的是质量、效率、成本的综合改善,基于制造企业质量、效率、成本影响因素的分析,可以得出相应的管理重点。作业工序是基本生产单元,是形成产品的基本过程,对产品质量有着关键影响。作业工序除显著影响质量外,对生产效率、生产成本均有直接影响,作业工序是精益质量管理的基础关键点,其管理的重点是质量。作业系统由作业工序组成,作业系统的结构和布局对生产效率有着关键影响,进而对生产成本有着直接影响,也影响到了产品质量。作业系统是精益质量管理的关键点,其管理的重点是效率。
精益质量管理研究对象是作业系统和作业工序,其中作业系统包含作业工序。精益质量管理“精益”的研究重点是作业系统,重点是效率改善,其核心工具是“JIT指令”;“质量”的研究重点是作业工序,重点是质量改善,其核心工具是“Cpk指标”。“精益”与“质量”研究中均要综合促进成本的改善,并通过自身的改善达到成本的改善。
针对作业工序的质量改善是精益质量管理的重点之一,是推行精益质量管理的切入点,也是精益质量管理推行成功的前提条件。对制造企业而言,质量是效率的基础,质量也是成本的基础。通过作业工序质量的改善,实现精益质量的基础保障之后,过渡到作业系统精益的改善,总体实现作业系统和作业工序质量、效率、成本的改善。由于作业系统和作业工序与外围管理的互动关系,通过对作业系统及作业工序的精益质量管理,可进一步实现外围管理系统改善。
思考题
1.统计质量控制的基本步骤是什么?如何加以实施?
2.什么是统计过程控制?它的主要分析工具是什么?
3.统计过程控制图有哪些基本类型?它们各自的特点及适用范围是什么?
4.过程能力分析的基本步骤是什么?过程控制指数有哪些类型?
5.怎样计算过程能力指数?如何对过程能力进行评价?
6.抽样方案的分类方法有哪些?
7.抽样检验实施过程应注意哪些问题?
实训与考核
实训项目:
××企业统计质量控制分析(小组项目),以报告的形式进行整理介绍。
深入企业,了解其质量管理工作实施情况,并尝试完成如下任务。
(1)搜集数据,绘制统计过程控制图,分析判断生产过程的稳定性,并形成相关结论。
(2)及时发现生产过程中的异常现象和缓慢变异,预防不合格品产生。
(3)查明生产设备和工艺装备的实际精度,以便做出正确的技术决定。
(4)为评定产品质量提供依据。
实训考核:
(1)搜集该企业生产过程的相关信息,填写X-R控制图数据表。
X-R控制图数据表

(2)根据计算的数据,绘制统计过程控制图,根据控制图,对企业运行状况进行判断。
(3)计算企业过程能力指数,并根据指数对企业的能力进行评价。
(4)针对企业生产过程的薄弱环节,进行影响因素分析,并有针对性地提出改进措施。
(5)最终将整个分析过程进行整理,以小组为单位形成研究报告。
