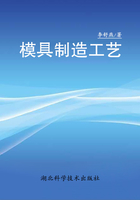
2.4 定位基准的选择
在制定零件加工的工艺规程时,正确地选择工件的定位基准有着十分重要的意义。定位基准选择的好坏,不仅影响零件加工的位置精度,而且对零件各表面的加工顺序也有很大的影响。
2.4.1 基准的概念
零件是由若干表面组成,各表面之间有一定的尺寸和相互位置要求。模具零件表面间的相对位置要求包括两方面:表面间的距离尺寸精度和相对位置精度(如同轴度、平行度、垂直度和圆跳动等)要求。研究零件表面间的相对位置关系离不开基准,不明确基准就无法确定零件表面的位置。基准是用来确定生产对象上几何要素间的几何关系所依据的那些点、线、面。如果要计算和测量某些点、线、面的位置和尺寸,基准就是计算和测量的起点依据。
基准按其作用不同可分为设计基准和工艺基准两大类。
1.设计基准
在零件图上用以确定其他点、线、面的基准称为设计基准。例如图2-4所示的零件,其轴心线O-O'是各外圆表面和内孔的设计基准;端面A是端面B, C的设计基准;内孔表面D体现的轴心线O-O'是φ40h6外圆表面径向圆跳动和端面B端面圆跳动的设计基准。

图2-4 零件图
2.工艺基准
零件在加工和装配过程中所使用的基准,称为工艺基准。工艺基准按用途不同,分为工序基准、定位基准、测量基准和装配基准。
(1)工序基准。在工序图上用来确定本工序所加工表面加工后的尺寸、形状、位置的基准称为工序基准。工序图是一种工艺附图,加工表面用粗实线表示,其余表面用细实线绘制,如图2-5所示。外圆柱面的最低母线B为工序基准。模具生产属于小批生产,除特殊情况外一般不绘制工序图。

图2-5 工序基准
(2)定位基准。在加工时,为了保证工件相对于机床和刀具之间的正确位置所使用的基准称为定位基准。例如图2-4所示零件,零件套在心轴上磨削φ40h6外圆表面时,内孔即为定位基准。
(3)测量基准。零件检验时,用以测量已加工表面尺寸及位置的基准,称为测量基准。
如图2-4所示,当以内孔为基准(套在检验心轴上)检验φ40h6外圆的径向圆跳动和端面圆跳动时,内孔即为测量基准。
(4)装配基准。装配时用以确定零件在部件或产品中位置的基准,称为装配基准。例如,图2-4所示零件φ40h6及端面B即为装配基准。
2.4.2 工件的安装方式
为了在工件的某一部位上加工出符合规定技术要求的表面,在机械加工前,必须使工
件在机床上相对于工具占据某一正确的位置。通常把这个过程称为工件的“定位”。工件定位后,由于在加工中受到切削力、重力等的作用,还应采用一定的机构将工件“夹紧”,使其确定的位置保持不变。工件从“定位”到“夹紧”的整个过程,统称为“安装”。
工件安装的好坏是模具加工中的重要问题,它不仅直接影响加工精度、工件安装的快慢、稳定性,还影响生产率的高低。为了保证加工表面与其设计基准间的相对位置精度,工件安装时应使加工表面的设计基准相对机床占据一正确的位置。如图2-4所示,为了保证加工表面φ40h6径向圆跳动的要求,工件安装时必须使其设计基准(内孔轴心线O-O')与机床主轴的轴心线重合。
在各种不同的机床上加工零件时,有各种不同的安装方法。安装方法可以归纳为直接找正法、划线找正法和采用夹具安装法等三种。
1.直接找正法
采用这种方法时,工件在机床上应占有的正确位置,是通过一系列的尝试而获得的。具体的方式是在工件直接装在机床上后,用千分表或划针,以目测法校正工件的正确位置,一边校验,一边找正,直至合乎要求。
直接找正法的定位精度和找正的快慢,取决于找正方法、找正工具和工人的技术水平。它的缺点是花费时间多,生产率低,且要凭经验操作,对工人技术水平要求高。故仅用于单件、小批量生产中。此外,对工件的定位精度要求较高,例如误差小于0.01~0.05mm时,如果采用夹具,因其本身有制造误差,而难以达到要求,就不得不使用精密量具和由较高技术水平的工人用直接找正法来定位,以达到其精度要求。
2.划线找正法
此法是在机床上用划针按毛坯或半成品上所划的线来找正工件,使其获得正确位置的一种方法。显而易见,此法要多一道划线工序。划线本身有一定宽度,在划线时尚有划线误差,校正工件位置时还要观察误差。因此,该法多用于生产批量较小,毛坯精度较低,以及大型工件等不宜使用夹具的粗加工中。
3.采用夹具安装法
夹具是机床的一种附加装置,它在机床上相对刀具的位置,在工件未安装前已预先调整好,所以在加工一批工件时,不必再逐个找正定位,就能保证加工的技术要求,既省工又省事,是先进的定位方法,在成批和大量生产中广泛应用。夹具在现代生产中已得到了大量应用。
2.4.3 定位基准的选择
定位基准不仅要影响工件的加工精度,而且对同一个被加工表面所选用的定位基准不同,其工艺路线也可能不同。所以选择工件的定位基准是十分重要的。机械加工的最初工序只能用工件毛坯上未经加工的表面作定位基准,这种定位基准称粗基准。用已加工过的表面作定位基准称为精基准。在制定零件机械加工工艺规程时,总是先考虑选择怎样的精基准定位把工件加工出来,然后考虑选择什么样的粗基准定位,把用作精基准的表面加工出来。
工件定位时,究竟要选用几个表面作为定位基准方能保证加工要求呢?按照六点定位原理,要根据加工时对工件应限制的自由度个数来确定。如图2-6所示的支承块,为了获得尺寸h1,用铣刀加工顶面时,需要限制自由度,选择底面(F面)定位即可。

图2-6 支承块
加工B、C表面时,为获得尺寸t和h2并保证加工面与基面A、F的垂直度和平行度要求,需要限制和Z︵五个自由度,应选择F面(主定位面)、A面(导向面)定位。
加工孔时为保证孔的位置尺寸s1、s2、20及孔与F面的垂直度要求,必须限制工件六个自由度,故应选择F面(主要定位面)、A面(导向面)和D面(止推面)三个基准面定位。
如何正确地选择定位基准,在生产中已总结出了一些规律。
1.精基准的选择
选择精基准时,主要应考虑减少定位误差和安装方便、准确。选择原则如下:
(1)基准重合原则。选择被加工表面的设计基准为定位基准,以避免因基准不重合引起基准不重合误差,容易保证加工精度。如图2-7所示,当加工表面B, C时,从基准重合的原则出发,应选择表面A(设计基准)为定位基准。加工后表面B、C相对A面的平行度取决于机床的几何精度,尺寸精度误差则取决于机床—刀具—工件等工艺系统的一系列因素。

图2-7 基准重合工件
(2)基准统一原则。应选择多个表面加工时都能使用的定位基准作精基准。这样便于保证各加工表面间的相互位置精度,避免基准变换所产生的误差,简化夹具的设计和制造工作。
例如,轴类零件的大多数工序都采用顶尖孔为定位基准,齿轮的齿坯和齿形加工多采用齿轮的内孔及基准端面为定位基准。
(3)自为基准原则。有些精加工或光整加工工序要求余量小而均匀,应选择加工表面本身作为精基准。而该表面与其他表面之间的位置精度,则用先行工序保证。
例如在导轨磨床上磨削导轨时,安装后用百分表找正工件的导轨表面本身,此时床脚仅起支撑作用。此外珩磨、铰孔及浮动镗孔等都是“自为基准”的例子。
(4)互为基准原则。当两个表面相互位置精度要求高,并且它们自身的尺寸与形状精度都要求很高时,可采用互为精基准的原则。
2.粗基准的选择
粗基准选择的好坏,对以后各加工表面加工余量的分配,以及工件加工表面和非加工表面间的相对位置均有很大的影响。因此,必须重视粗基准的选择。粗基准的选择有两个出发点:一是保证各加工表面有足够的余量;二是保证不加工表面的尺寸和位置符合图样要求。
选择原则如下:
(1)具有非加工表面的工件,为保证非加工表面与加工表面之间的相对位置要求,一般应选择非加工表面为粗基准。若工件有几个非加工表面,则粗基准应选位置精度要求较高者,以达到壁厚均匀、外形对称等要求。
如图2-8所示零件,外圆柱面1为不加工表面,选择柱面1为粗加工孔和端面,加工后能保证孔与外圆柱面间的壁厚均匀。

图2-8 粗基准的选择
(2)具有较多加工表面的工件在选择粗基准时,应按下述原则合理分配各加工表面的加工余量:①为保证各加工表面都有足够的加工余量,选择毛坯上加工余量最小的表面作为粗基准。②若零件必须首先保证其重要表面余量均匀,则应选择该表面为粗基准。③若有几个不加工表面,则粗基准应选位置精度要求较高者。
(3)粗基准的表面应尽量平整,没有浇口、冒口或飞边等其他表面缺陷,以使工件定位可靠,夹紧方便。
(4)由于粗基准是毛坯表面,比较粗糙,不能保证重复安装的位置精度,定位误差很大。因而,粗基准一般只使用一次。
3.辅助基准的应用
工件定位时,为了保证加工表面的位置精度,多优先选择设计基准或装配基准为定位基准,这些基准一般均为零件上的重要工作表面。但有些零件的加工,为了安装方便或易于实现基准统一,人为地造成一种定位基准,如图2-9所示车床小刀架的工艺凸台A应和定位面B同时加工出来,以使定位稳定可靠。辅助基准在零件工作中并无用途,完全是为了工艺上的需要,加工完毕后如有必要可以去掉辅助基准。

图2-9 具有工艺凸台的刀架毛坯