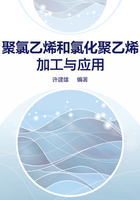
3.4 塑料管件
管件是管路中的重要组成部分,也是必不可少的部分。它起到管件与管材的连接、控制或关闭管内流动介质及分配或改变管内输送物的流量和方向的作用。当然,在塑料管线中所应用的管件应该是用塑料材料制作的。塑料管件的结构设计及加工质量直接影响到整个管线的质量。管路中经常出现的泄漏、堵塞等现象往往是由于管件的结构不合理或管件的制作质量较差而造成的。随着塑料管道的普遍应用及新兴塑料材料的不断出现,塑料管件的结构设计及加工工艺已越来越受到重视。
根据热塑性塑料的特点,普遍采用模塑成型来加工生产中、小口径的管件。由于设备的限制等原因,大口径管件还是由手工来制作。本节着重讨论塑料管件的注塑成型加工工艺。
在塑料成型加工中注塑成型是主要的加工方法之一,也是最早能将塑料材料制作成有一定形状的制品的加工方式。塑料加工技术的发展包含了注塑成型加工技术的发展。
在挤出成型加工中挤出机是主要设备,而在注塑成型加工中注塑机为主要设备。与挤出机一样,注塑机也有料筒和螺杆。这两种加工方式的不同为挤出生产是连续的,而注塑生产是间歇性的。它们的共同点是塑料原料都必须经过“塑化”这一过程。注塑成型加工中聚合物的塑化过程也是在注塑机的料筒中完成的。因此在注塑成型加工中“塑化”技术仍是加工技术的关键。注塑机的螺杆和料筒的原理和作用也与挤出机相似:塑料在螺杆和料筒中需经历“态”的变化,所以在螺杆上仍然划分了加料段、塑化段和均化段三个区段。在料筒外表安装了加热圈,塑料在料筒内依靠加热圈所提供的热量和通过螺杆与料筒的相对运动所产生对物料的挤压力、摩擦力和剪切力的作用而产生的热量,再由物料分子间的运动将热量传递,使物料达到熔融塑化状态。注塑机的螺杆或柱塞对熔融塑化后物料施以强大的压力,使物料通过喷嘴注入闭合模具的流道和浇口直至充满整个型腔。
不同的塑料原料具有不同的加工性能。因此各种不同的原料的加工条件都不一样,甚至差别很大。因而对注塑机的螺杆结构及其相应功能的需求也不一样。随着塑料工业的不断发展,注塑机械的品种和性能有了很大的创新和提高。塑化能力和塑化质量正在不断提高,注射速度也有较大的提高,注射压力已提高到超高压水平,使注塑制品的成型收缩率大大降低。电脑自动化控制的应用不仅避免了操作错误的发生,同时可在生产现场及时和准确地修改工艺参数,使产品质量趋于完美。专用型注塑机的发展使一些具有特殊性能的热塑性塑料制品得以发展。
国产注塑机的制造从无到有,发展很快,尤其是在其性能上的提高更是迅速。但与欧洲一些先进的注塑设备相比仍有一定的差距。特别是在大型和特大型注塑机的制造方面还属空白。对中小型注塑机而言,国内产品的成型精密度还有待提高,控制系统中的温度、压力及时间等传感器及其相应的仪表误差较大,油路中的关键部件及控制系统都存在一定的缺陷,漏油现象比较普遍。尤其是背压的控制经常发生故障。随着塑料工业的发展,许多新颖的高性能材料不断出现,注塑机螺杆和料筒的结构对某些塑料的加工还不完全适合。如氯化聚氯乙烯(CPVC)材料,其流动性较差,黏性大,且有一定的吸湿性,而通用螺杆的结构对这类材料的塑化和排气不够理想,因而易造成物料的分解或产品性能下降的现象。PPR材料的注塑加工难度虽然不大,但用通用注塑机所加工的管件分子取向明显,成型时产生的内应力较大,使PPR注塑管件的性能比PPR材料的性能有较大的下降。
3.4.1 PVC、CPVC管件的加工条件
(1)设备 PVC与CPVC管件的主要生产设备是注塑机。通常采用通用注塑机并将螺杆配成PVC挤出螺杆。图3-25为国产海天HTF630注塑机外形图。

图3-25 注塑机外形图
不同型号的注塑机的注射量不同,因此可根据管件的尺寸及生产量的大小选用不同型号的注塑机。表3-22为部分型号的注塑机的注射量。
表3-22 部分型号的注塑机注射量

表3-22中,机型即注塑机的合模力。例如,机型为150的注塑机的合模力为150kN。理论注射量以密度为1.05g/cm3的聚苯乙烯(PS)作为参照量。不同材料的塑料,因密度不一样,注射量也会有所不同。最大PVC注射量是经验值。另外,用配方不同,物料流动性就不同,因而注射量也会有所不同。正常生产时的注射量通常以PS的理论注射量的60%~70%进行核算。PVC的注射量可以在PS注射量的基础上乘以经验系数1.3。过去曾以注射量作为注塑机型号的标志,但它很不明确,而注射容积的参数比注射量的参数更明确。
由于注塑过程是一个复杂的过程,因此注射压力、注射速率、塑化能力、移模行程、拉杆内间距、理论注射容积、理论注射量、合模力等均是注塑机的主要参数。合模力与注射压力及注射量有一定的匹配关系,因而它也成为注射机的型号标志。
生产CPVC管件对注塑机的要求较高,由于CPVC材料有较大的吸湿性,且加工难度也较大,因此,要求注塑机采用排气式螺杆,塑化能力能达到A级,具有三级注射、三级保压、背压可调节控制系统,并且由电脑程序控制,并设有按钮和显示屏,操作时可按动按钮设置工艺参数,并在屏幕中显示。这种电脑控制系统尤其适合工艺参数范围较窄的材料的成型加工。
无论是PVC物料还是CPVC物料,受热后易分解,其分解后产生的物质容易腐蚀加工设备,所以,设备在停止工作前需用ABS树脂将PVC或CPVC物料排出料筒,以保证设备的良好性能。
此外,与挤出加工一样,必须要有混料设备。混料设备的合适与否,会影响混料效果,并最终影响产品质量。混料设备的选择可参考PVC挤出加工设备。
(2)模具 塑料管件的成型是通过塑料注塑模具完成的。注塑模具的设计和制造质量能直接影响塑料管件的质量。因此,合理的模具结构和良好的制造质量是生产塑料管件的又一重要加工条件。在模具设计中应重视以下几个方面。
①喷嘴的构型 熔融的PVC物料通过喷嘴进入模具的流道内,它在预塑、注射、保压等注塑过程中起着非常重要的作用。喷嘴的结构形式应根据物料的黏性和流动状态来决定。考虑到PVC是一种易分解、黏性大且流动性差的材料,所以采用直通式喷嘴形式较为合理。图3-26为PVC-U排水管件用喷嘴形式示意图。

图3-26 喷嘴形式
不同几何形状及壁厚的塑料管件,直通喷嘴的出料孔的孔径和平直段的长度是不一样的。另外,出料孔的孔径应与模具流道入口处的孔径相匹配。PVC-U喷嘴的出料段宜短不宜长,孔径宜大不宜小,锥孔宜长不宜短。合理的喷嘴结构是管件质量的关键。否则,即使配方再好,管件质量也可能不理想。
②流道 模具中的流道是PVC熔融物料进入模具型腔的流动通道。流道有主流道和分流道。从喷嘴射出的PVC熔融料首先注入主流道。主流道的几何形状、尺寸大小及表面光洁度等直接影注射的全过程。对PVC这类流动性差的热敏性塑料,主流道应设计为圆锥形,锥度为8°~10°,其截面积宜大不宜小。对于较大口径管件的模具,其主流道的截面积应相应增加。主流道设在浇口套内,其目的是可以使用更优质的材料,提高热处理质量和加工精度,便于装拆和更换。主流道结构不合理会使成型后的管件表面产生红纹、黄纹及气泡等不正常现象。
分流道是PVC熔融物料由主流道进入浇口的通道。用于注塑PVC管件的分流道的截面形状宜采用圆形,以减少压力损失和料流阻力。但是圆形断面的分流道的加工难度较大,所以多数管件模具的分流道采用U形断面。有多个分流道时,可以一模八腔或一模十二腔等。分流道的分布应对称均布,以确保进料的均匀性。分流道的断面形状、面积及长度等对PVC物料所受的压力及其流动状态都有直接的影响,在设计分流道时必须考虑与主流道的配合,以保证主、分流道内料流的稳定性。
③浇口 浇口是熔融的塑料进入型腔的进料口,是浇注系统中最关键,也是最短小的部位。它的断面形状、尺寸大小、在模具中分布的位置及其厚度都直接影响到注塑制品的质量。PVC注塑管件的浇口的断面形状应采用圆形。浇口宜大不宜小,尽量避免产生过高的剪切应力。浇口的制作很难一步到位,需在试模时不断修改和完善。
④冷料穴 由于注塑加工是间歇式生产,在间歇过程中会产生冷料。冷料穴的设置就可将这种冷料储存起来,并阻止它进入型腔。冷料穴的设置对注塑PVC管件尤为重要,结构合理的冷料穴可以消除制品中经常会出现在浇口处的冷料斑(又称蝴蝶斑)。PVC管件注塑膜的冷料穴应设置在主流道的末端,其直径必须大于主流道的大端直径。适用于PVC-U制品的冷料穴形式通常有三种:一种是带顶杆的冷料穴;另两种是带顶杆的倒锥形或圆柱形冷料穴。PVC-U注塑料的冷料穴要有足够的长度,以确保冷凝料被全部储存起来。有时为了更好地阻止冷料带入型腔,在分流道末端处也可增设冷料穴。图3-27为三种冷料穴的示意图。

图3-27 冷料穴示意图
1—定模;2—冷料穴;3—顶杆;4—动模
⑤排气 PVC-U材料在注塑成型时会由于物料内的水分及其所含的低分子挥发物等在高温下产生气体,同时在型腔内也存在着气体。这些气体在注塑过程中如不能顺利排出,将使制品产生气泡,并严重影响其内在质量。一般情况下,在注射时气体会通过模具分型面的间隙及型芯与顶杆间的间隙等模具中活动部件的间隙进行排气,只有当利用间隙不能满足排气要求的情况下才考虑在模具上开设排气槽。排气槽的位置应开在分型面的型腔一面上,这样更有利于气体的排溢。如PVC-U管件产生了气泡,则一般不会出现在浇口附近,而是离浇口处最远的部位或壁厚最薄的部位,前一种情况是因为气体在物料最后到达处被封闭。后一种情况是因为壁厚的不同,其阻力就不同,气体最容易聚集在阻力较小的空间。此外,浇口位置应当设置在容易排出气体的部位。
采用排气式螺杆的注塑机排气效果较好。这种排气式螺杆的第二段为排气段,此段的加工温度应低于其它各段,以利于气体的排出。排气式螺杆能使熔融物料在注射前就先将所含的水分和其它挥发物排除,然后再进行注射成型。这种螺杆非常合适CPVC等有一定吸湿性的材料的注塑成型加工。
(3)原料 经注塑成型加工的PVC制品所采用的原料仍以PVC树脂为主,但其牌号与挤出加工的PVC制品所用原料不同。由于注塑成型加工要求物料具有较好的流动性,因此,应选用聚合度低的树脂。一般选用的PVC树脂的型号为S700或S800,即SG-8型或SG-7型,通常情况下S700(SG7)的流动性更好,更适合于注塑成型加工。
生产CPVC管件的原料也应选择注塑型CPVC树脂,它相对于挤出型CPVC树脂来说,流动性要好一些,加工难度也略低一些。
与生产PVC、CPVC管材一样,除了树脂外,还需稳定剂、润滑剂等辅助材料。这些辅料中有些与可挤出加工的辅料通用,有些则略有区别。
3.4.2 PVC管件的生产
PVC管件按使用要求分,有两大类别,即非压力管件和压力管件。非压力管件是指在使用过程中无需承受压力的管件,它包括建筑排水管件、排污管件、线缆护套管件等。压力管件是指在使用过程中必须承受一定压力的管件如给(饮)水管件、化工用管件等。对于不同使用要求的管件,其加工要求也不相同。但是生产PVC管件的主要条件是选择合适的注塑设备、合理的模具及正确牌号的树脂。
(1)PVC建筑用排水管件 PVC建筑排水管件是用量较大的管件品种之一,其特点是种类多,多种规格的管件可达一百多种。由于PVC建筑排水管件是直接安装在建筑物内(或外)的,在使用过程中不易更换,因此其质量要求较高,且由于其种类繁多,因此模具结构也较复杂。
生产PVC建筑排水管件对设备的要求已在上文中简述,但它的模具品种较多,有管箍、三通、弯头等多种,这也导致了物料的流动等差异。因此在生产PVC建筑排水管件中配方及工艺参数显得尤为重要。
①原料
a.PVC树脂 注塑成型加工所选用的树脂型号为S700(SG-8)或S800(SG-7),但最好选用S700(SG-8)。
b.稳定剂 热稳定剂的类型通常选用铅盐类稳定剂。如三碱式硫酸铅(3PbO·PbSO4·H2O)、二碱式亚磷酸铅(2PbO·PbHPO3·)及含一定润滑体系的铅盐复合稳定剂。由于注塑成型加工过程中注射压力大,物料流速快,摩擦热大,容易引起物料分解,所以热稳定剂的用量应比挤出产品多。
c.润滑剂 在PVC注塑过程中,分子之间的作用力比挤出加工时大,内摩擦力较大,所以必须重视对内润滑剂的选用。常用的内润滑剂有硬脂酸(HSt)和高效内润滑剂G-30等。而外润滑剂的作用是可以克服物料与设备及模具接触面的黏附性,改善表观质量和脱模性。常用的外润滑剂有石蜡和高效外润滑剂G-70等。
d.填充剂 填充剂在PVC注塑制品中不仅仅起到增量作用,其主要作用是能改善制品的尺寸稳定性、降低收缩率。另外,少量填充料的加入在一定程度上可降低物料的黏度,有利于注塑成型。常用的填充剂是轻质碳酸钙(CaCO3)或活性轻质碳酸钙(α-CaCO3)。CaCO3的细度对制品的影响较大,过细或过粗的CaCO3都会影响它在PVC树脂中的分散性,同时还会影响到其它配料在PVC树脂中的分散性。
e.加工助剂 目前使用的国产螺杆式注塑机多采用单螺杆,塑化能力一般,而PVC注塑对塑化质量的要求较高。为了能缩短物料的凝胶化时间、提高混炼效果、促进塑化、增加制品光泽、消除料流伤痕,在配方中需加入一定量的加工助剂。常用的加工助剂为丙烯酸酯类聚合物,如ACR-21、ACR-401或高效助剂PA-20、PA-21等。
f.改性剂 聚氯乙烯材料具有良好的力学性能和耐化学腐蚀性,阻燃性能也较好。但是它的低温脆性大,抗冲击性较差。为了改善PVC性能,在配方中加入一定量的改性剂,通过共混达到改善其性能的目的。常用的改性剂有氯化聚乙烯(CPE)、乙烯-醋酸乙烯酯共聚物(EVA)、ABS、MBS等。
②配方 根据对以上原辅材料的分析,可以设计出注塑生产PVC建筑排水管件的配方。以下配方可供参考。
a.PVC建筑排水管件配方一
b.PVC建筑排水管件配方二
③生产工艺 PVC建筑排水管件的生产工艺不复杂,但是必须对其进行控制,确保其处于受控状态,以保证产品质量处于稳定状态。
注塑管件的生产过程是:将配方料经过高速混料机混合,再由低速拌和机冷拌后直接送入注塑机的加料斗而进入注塑机的螺杆,通过料筒电热圈的加热和由螺杆运动产生的剪切力、挤压力和摩擦力的作用,使PVC物料在一定的温度下成为熔融黏流态,随后在螺杆的推动下,熔融物料由喷嘴射出,并经主、分流道快速进入模腔。在模腔内冷却定型后即可取出,最后对制品上的区边及浇口部位进行整修后即可。这种工艺过程是用粉料直接注塑。其工艺流程如下:
在上述工艺中,高速混合的温度为115~125℃,低速冷拌温度为40℃。注塑机料筒一区温度为180~185℃;二区温度排气式螺杆为175~180℃,非排气式螺杆为185~188℃;三区温度为185~190℃。螺杆冷却油温为80~100℃,螺杆转速为40~65r/min。
在实际操作中,除工艺温度外,还需设定其它参数。如注塑生产ф110mm顺水三通,可设定如下的工艺参数:
一级压力:40~60MPa,保压40~60MPa;
二级压力:50~65MPa,保压50~65MPa;
三级压力:30~40MPa,保压30~40MPa;
保压时间:3s;
注射时间:9~12s;
冷却定型时间:55~65s;
模具冷却温度:30~50℃。
工艺参数是根据设备性能、模具特性及制品规格和结构等综合条件来确定的。生产条件不同,工艺参数也有所不同。与挤出加工一样,注塑加工的关键技术也是物料的塑化。物料的塑化状态和流动性好,则注塑制品的内在质量和外观质量都比较好。采用对空注射的方法可判断物料的塑化质量,如果空射物料流畅光亮,则物料的塑化质量好,可以正常生产。反之,则应调整工艺参数,或将配方料造粒后再进行注塑。
(2)PVC难燃绝缘冷弯电线电缆导管管件
PVC难燃绝缘冷弯电线电缆导管管件也属非压力管件的范畴,其生产过程和工艺参数与PVC建筑排水管相同。由于对电线电缆导管管件的质量要求略低一些,因此,为考虑降低生产成本,在设计配方时与建筑排水管管件应略有不同。以下为它的配方,供参考。
①PVC难燃绝缘冷弯电线电缆导管管件配方一
②PVC难燃绝缘冷弯电线电缆导管管件配方二
(3)PVC-U压力管件 PVC-U压力管件应具有一定的承压能力,其所能承受的压力不可低于同系列(等级)的管材所能承受的内压。因此,管的壁厚不能小于同系列(等级)的管材壁厚。由于压力管道的系列(等级)有0.6MPa、1MPa和1.6MPa等,为了减少模具数量,通常同一规格尺寸的管件仅采用一种壁厚,一般ф50mm以下的管件取1.6MPa系列的壁厚,ф50mm以上的管件取1MPa系列的壁厚。因此,压力管件的壁厚较厚,属厚壁注塑制品,这就使得PVC-U压力管件的重量比PVC排水管件的重量要大得多。就材料本身而言,加工时其注射难度也相对较大。同时对注塑机性能、模具结构、配方、工艺控制等的要求也比排水管件高出许多。用于饮用水管路中的压力管件还应有严格的卫生要求,其卫生指标应符合GB/T 10002.2—2003及GB/T 17219—1998中有关规定。
①设备 首先注塑机的螺杆一定要是PVC螺杆,最好是排气式螺杆。其次,要求注射过程具备三级注射和三级保压。其三,工艺参数最好由电脑储存和控制,由显示器荧屏显示。目前国产注塑机基本上已能达到上述性能要求。
②模具 压力管件的模具其主、分流道的容积应比排水管件大,浇口也应比排水管件大。由于壁厚的差异,相同规格的压力管件的注射量比排水管件大,因此冷料穴的容积也应相应增加,注射过程中的排气也比非压力管件更为重要。
虽然在设计和制作压力管件的注塑模具时基本上可参照排水管件注塑模具,但其设计参数的严谨性及制作要求的严格性均要高于非压力管件。
③配方 PVC-U压力管件的配方中所用原辅材料与建筑排水管件基本相同,但由于PVC压力管件的产品性能要求高于非压力管件,因此相对于PVC非压力管件来说,其配方要求更高。
用于饮水管路中的管件,配方设计时还应考虑其应达到的卫生指标。而铅盐类稳定剂中铅含量太高,不能达到卫生指标要求。因此,一般采用有机锡稳定剂如T395作为热稳定剂。它用量少,热稳定性高,且能保持制品的卫生性能,是目前热稳定性能最好的稳定剂。以下所列的PVC-U压力管件配方可供参考。
a.适用于粉料直接注射的给水用PVC-U管件配方
b.适用于粒料注射的给水用PVC-U管件配方
c.适用于粉料直接注射的饮水用PVC-U管件配方
d.适用于粉料直接注射的饮水用PVC-U管件配方(采用钙/锌稳定剂)
e.适用于粉料直接注射球阀阀体配方
f.适用于粉料直接注射的球阀阀芯配方
注:球阀手柄用PP材料注塑而成,球阀密封圈可用EVA材料注塑而成。
④生产工艺 PVC-U给(饮)水用管件的生产工艺流程与生产PVC建筑排水管件相同,即原辅料按配方配好后经高、低速混合,然后直接送入注塑机,或将混合后的粉料经造粒后再送入注塑机进行注塑成型加工。
在生产饮水用管件时必须采用有机锡稳定剂,而有机锡稳定剂多为液体。为了能使液体的有机锡稳定剂在PVC树脂中均匀分散,充分发挥其有效作用,在物料混合时应先将PVC树脂与有机锡稳定剂在高速混合机中单独混合2~3min,然后再加入其它辅料按正常程序混合。另外,凡是使用硫醇有机锡稳定剂的生产现场包括混料间在内,必须与使用铅盐类稳定剂包括带润滑体系的复合铅盐稳定剂的生产场所隔离,以免产生污染,使产品发黑。这是因为硫醇有机锡中的硫与铅盐稳定剂中的铅易起化学反应而产生黑色的硫化铅,从而使产品,特别是白色产品受到污染。
由于给(饮)水管件为压力管件,其壁厚较厚,且性能指标要求也较非压力管件高。因此,其工艺温度参数较排水管件有所改变。
PVC-U给(饮)水用管件的注塑工艺参数如下。
注塑机料筒温度:1区175~180℃;2区180~185℃;3区190~198℃;喷嘴195℃。
各级压力与保压设定值:
预塑:60~70MPa;一级压力:30~40MPa,保压:40~60MPa;二级压力:40~50MPa,保压40~60MPa;三级压力:40~50MPa,保压40~60MPa。
以上参数仅供参考,实际生产中还需根据各自的设备、模具及原辅材料进行调整,以找到合适的工艺参数。
(4)PVC管件的主要性能及测试
①PVC排水管件的主要性能及测试 GB/T 5836.2—2006《建筑排水用硬聚氯乙烯(PVC-U)管件》标准中已规定了PVC建筑排水管件的质量性能指标,合格的PVC建筑排水管件的壁厚、物理机械性能等应能符合这一标准。管件的壁厚应大于等于符合国际的同规格管件的壁厚。其外观、壁厚及物理机械性能等应符合表3-23中所列要求。根据表中所列的要求,在生产过程中,可随时检查产品的质量,以保证产品的稳定性。
表3-23 PVC建筑排水管件的物理机械性能及测试方法

②PVC建筑用绝缘电工套管管件 PVC建筑用绝缘电工套管管件同属于非压力管件,它除了要有较高的耐热性能、阻燃性能及电气性能外,其它物理机械性能要求不高。当然,对外观、壁厚等也有一定的要求。具体指标可参阅国家建工标准JC/T3050—1998中有关章节。以下列出PVC建筑用绝缘电工套管管件的性能要求,以供参考。
a.坠落性能
指标:无震裂、破碎。
试验方法:管件装在三根760mm长的套管上,(-20±1)℃冷冻2h后取出立即进行试验,将套管与混凝土地面呈45°角,且装有管件的一端朝下;自由落下。第二次使试样与混凝土地面平行,自由落下。下落高度为试样最低点距离混凝土地面高1500mm。
b.耐热性能
指标:Di≤2mm
试验方法:将管件及耐热试验仪一起放入温度为(60±2)℃的烘箱内,在试样上放置下端带有直径为5mm的钢珠锥形物,在20N压力作用下保持1h后取出,然后测出Di值。
c.阻燃性能
a)自熄时间:tc=30s。
试验方法:采用液化石油气为燃气源,喷嘴内径为9mm的本生灯及秒表。点燃本生灯,使火焰高度为100mm,将管件垂直固定在燃烧装置上,与蓝色火焰接触。试样被点燃后应无明显的火焰传播。撤去火源后,用秒表测量熄灭的时间。
b)氧指数:OI≥32%
试验方法:GB/T 2406测定氧指数,并按GB 50222规定其技术要求。
d.介电性能
指标:15min内不击穿,R≥100MΩ。
试验方法:略。
③PVC给(饮)水管件的主要性能及测试 PVC给(饮)水管件属压力管件,除了对外观及壁厚要求较高外,其物理性能指标要求也相对较高,尤其是饮水用管件还必须要求卫生指标。GB 10002.2—2003《给水用硬聚氯乙烯(PVC-U)管件》严格规定了该产品的多项质量性能指标。表3-24列出了PVC给(饮)水管件的物理机械性能及测试方法,供参考。
表3-24 PVC给(饮)水管件的物理机械性能

对于饮水用压力管件,其卫生指标也有相应的标准可依。以下所列为PVC饮水用管件的卫生指标及测定方法。
a.铅的萃取值 第一次小于1.0mg/L,第三次小于0.3mg/L。试验方法按GB 9644规定测定。
b.锡的萃取值 第二次小于0.02mg/L。试验方法按GB 9644规定测定。
c.镉的萃取值 三次萃取值均不大于0.01mg/L。试验方法按GB 9644规定测定。
d.汞的萃取值 三次萃取值均不大于0.001mg/L。试验方法按GB 9644规定测定。
e.氯乙烯单体含量 氯乙烯单体≤1.0mg/kg。试验方法为:在管件的管壁上切取0.3~0.5g试样,按GB 4615规定测定。
从以上数据可知,PVC饮水用管件在生产过程中除了对树脂有一定要求外,应严格控制使用含铅、锡、镉、汞等重金属的辅助材料。除以上所列内容外,国家标准对饮水用管件也有较为严格的要求。管件生产企业应予以重视。
(5)在PVC-U管件的注塑过程中常见的问题及其产生原因和解决方法
在注塑加工过程中,经常会出现产品质量不正常现象,这时,就必须分析原因,寻找解决方法。通常,丰富的实践经验有助于及时发现问题,并得到解决方法。以下是在PVC-U管件注塑加工过程中几种常见的问题及排除方法,以供参考。
①制品不能注满 注塑管件在加工时常会遇到模具不能注满的现象。在注塑机刚刚开始工作时,由于模具温度太低,PVC熔融物料的热量损失大,容易产生早期凝固,模腔的阻力较大,物料无法充满型腔。这种现象是正常的,也是暂时的,连续注射数模后即会自动消失。如果模具一直不能注满,则要考虑以下情况,并作适当调整。
a.注射物料温度偏低,流动性差,可适当提高加热温度,以提高物料的塑化性和流动性。
b.设定的注塑成型周期偏短,或供料不足,可适当增加成型周期或增加供料量。
c.设定的注射压力偏低或从注射压力转换到保压压力的时间过早,可适当提高注射压力或调整保压转换时间。
d.注射速率偏低,可适当提高注射速率。
e.浇注系统结构尺寸偏小,可适当增加主、分流道的容积或将浇口改大。
f.模具排气不良,可适当修改浇口位置或开设排气槽。
g.薄壁处充模困难,可调整制品结构或改善浇注系统。
②缩痕严重 此类问题的产生原因与注料不足的产生原因有共同之处。
a.设定的注射压力偏低,可适当提高注射压力。
b.设定的保压时间不够,可适当增加保压时间。
c.设定的冷却时间不够,可适当增加冷却时间。
d.供料略有不足,可适当增加供料。
e.模具冷却不均匀,可调整冷却回路,使模具各部位的冷却均匀。
f.浇注系统结构尺寸偏小,可加大浇口或增加主、分流道截面大小。
③熔接痕线 在PVC-U压力给(饮)水管件或较大口径的排水管件上,经常会发现有明显的熔接痕线,严重时会影响管件的内在质量,特别是压力管件在承受压力时破裂现象会发生在熔接痕线处,其产生原因及排除方法如下。
a.熔融物料温度偏低,可适当提高料筒加热温度,尤其应提高喷嘴温度。
b.注射压力或注射速率偏低,可适当增加注射压力或注射速率。
c.模具温度偏低,可适当提高模具温度。
d.浇口偏小或流道截面太小,可适当增大流道或加大浇口。
e.模具排气不良,改善模具排气性能,增设排气槽。
f.冷料穴容积偏小,可适当加大冷料穴的容积。
g.配方中润滑剂和稳定剂用量偏多,可调整它们的用量。
h.镶嵌件设置不合理,可调整其布局。
④制品光泽差 PVC注塑制品的表面光泽很大程度上与PVC物料的流动性能有关。因此,提高物料的流动性是提高制品光泽的重要措施。具体表现如下。
a.由于熔融物料温度偏低而形成了物料的流动性差,可适当提高物料的加热温度,尤其要提高喷嘴处的温度。
b.配方不合理,使物料的塑化不到位或填充剂太多,应调整配方,通过加工助剂的合理配合提高物料的塑化质量和流动性,控制填充剂的用量。
c.模具冷却不够,改善模具的冷却效果。
d.浇口尺寸偏小或流道截面偏小,阻力过大,可适当加大流道截面,加大浇口,减小阻力。
e.原料中水分或其他挥发物含量偏高,可将原料充分干燥,或通过造粒排除水分或挥发物。
f.排气不良,可增加排气槽或改变浇口位置。
⑤管件上产生气泡 气泡的产生原因,如物料中水分或其他挥发物过多、工艺温度过高,工艺参数设置不当及模具原因等,具体分析如下。
a.因加热温度偏高而产生热泡。过高的工艺温度会使原料中的挥发物产生气泡,且还会使PVC物料有部分分解而产生气泡,这类气泡即俗称热泡。可适当降低加热温度。
b.注射速度太快。因为PVC-U注塑制品的成型加工宜采用较低的注射速度和较高的注射压力。可适当调整注射速度。
c.浇口偏小或流道截面偏小,料流阻力太大。可加大浇口和流道截面积,减少熔体流动阻力。
d.原辅料中的水分或其它挥发物含量过高或原辅料存放时间过长而吸收了空气中的水分。采购辅料时严格控制原辅料中的挥发物含量,在空气中湿度较大的期间或地区原辅料不宜存放太久。
⑥分层剥离现象 分层剥离现象是注塑PVC管件中较常见的现象,尤其易出现在厚壁制品上。这种现象大多是由于材料的注塑流动性能差而发生的。因此,只有采用合理的配方以提高物料的流动性能,降低物料黏度,降低塑化温度和凝胶时间,才能阻止分层剥离现象的产生。配方中内、外润滑作用要达到相对平衡,填充剂及润滑剂的用量不宜过多。此外,工艺温度偏低也是产生制品分层剥离的原因之一。适当提高工艺温度,尤其是喷嘴温度有利于改善这一现象。
⑦冷料斑(又称蝴蝶斑或花斑) PVC-U注塑制品在浇口附近出现冷料斑是经常发生的现象,特别是在注塑成型加工厚壁制品如PVC-U给(饮)水管件时,几乎普遍存在这种现象。这种现象的发生原因复杂,因此要改善这一现象,是一个技术难题。根据我们的经验,要从三个方面全面考虑,并加以合理的调整,才能消除这一现象。
首先是配方设计。一是应重点考虑物料在注塑加工中的塑化性能。配方中所使用的加工助剂品质要高,性能要好。二是要提高物料的流动性。配方中改性剂的选用应重点考虑改善PVC的流动性能,填充剂的用量必须控制在最小程度。
其二是工艺参数的调整。一旦确定配方上没有太大的问题后,就要考虑调整工艺温度,原则上工艺温度的调整可减少或消除冷料斑。注塑机的工作温度不仅仅来自加热圈的温度,物料的塑化温度与背压、螺杆转速有直接关系。因此,要能掌握通过调整背压(螺杆后退时的阻力)来调整物料的塑化温度的方法以达到较好的效果。
其三是考虑模具的浇注系统结构是否合理。在注塑模具设计中,合理的浇注系统是保证注塑制品质量的关键。一是观察模具冷料穴的容积大小或结构是否合理,如发现有问题,应进行修改。特别是PVC-U厚壁注塑制品的模具中的冷料穴要有足够的容积以防止冷料进入模腔,必要时在分流道上也应增设冷料穴。二是加大浇口尺寸。PVC-U厚壁制品的浇口尺寸必须大幅度地加大,主、分流道的截面积也宜大不宜小。
通过以上三方面的全面调整,可使冷料斑明显减少或消除。
⑧银丝、纹 PVC-U注塑制品上出现银丝或银纹,这也是生产过程中常见的现象,特别是加工深色厚壁制品如PVC-U压力管件,更容易出现这种问题。一般认为出现这一现象是由于原料中的水分形成的。但实际上还有其它原因会导致这一现象的发生。如物料在注塑机螺杆中挤压至喷嘴处时剪切力过大或温度梯度偏大,在整个注射过程中排气不良,注射速度过大或冷料穴偏小等都能产生银丝或银纹。因此,要消除这一现象,除对配方料进行干燥或通过造粒排除水分外,在具体操作时还应适当调整工艺温度、注射压力和速率等工艺参数,从而克服这一现象的发生。
⑨红、蓝斑纹等变色现象 在注塑成型加工白色制品如建筑排水管件等时,易出现红色或蓝色斑纹。这种现象的出现,同样与模具中的浇注系统有关。浇口是模具中非常重要的部位。由于浇口是熔体进入模腔的门户,在这里料流阻力最大,温度也最高,容易产生制品表面的变色现象。因此,在浇口设计中必须考虑能减少料流的阻力和温度的变化。这就是为什么在浇注系统设计中要遵循“浇口尺寸宜大不宜小、浇口流道宜短不宜长、宜厚不宜薄”的原则。此外,熔体温度过高、注射速度过快及模具排气不良等也会产生制品表面变色现象,这些都可以通过调整工艺温度和参数来得到解决。
PVC注塑产品的质量问题几乎均与浇口的设计有关,合理的浇口设计必定会使注塑成型过程顺利,从而获得较好的产品质量。
⑩溢料或飞边太多 注塑产品在成型加工过程中,往往会产生溢料或飞边太多的现象,这种现象的产生有模具方面的原因、注塑设备方面的原因,也有工艺方面的原因。如模具材料刚性不足、配合不好,是造成飞边的常见毛病。设备选用不当,合模力不够或设备的液压系统因长期工作使溢流阀调节螺丝松动、控制回路漏油、油泵漏油或损坏等造成系统压力不足而导致合模力的不足,从而产生溢料或飞边。在工艺控制上,温度偏高、注射压力偏大、注射压力转换到保压压力的转换时间过迟等也会造成飞边太多的现象。解决方法是寻找并消除其产生的原因。
脱膜困难 脱模困难有模具的原因,也有工艺不当的因素,但多数情况下是模具的脱模机构不当造成的。脱模机构中主要有:钩料机构,它负责将主、分流道及浇口处的冷料钩出;顶出机构,利用顶出脱模时要有足够的气体压力,否则也会产生脱模困难现象。另外,分型面的抽芯装置、螺纹退芯装置等均是脱模机构中的重要部件,设计不当会造成脱模困难现象。因此,在模具设计中,脱模机构也是必须重视的部位。在工艺控制方面,温度太高、供料太多、注射压力太高、冷却时间太长等也都会产生脱模困难现象。
综上所述,PVC-U注塑产品在加工过程中虽然会产生各种质量问题,但所有问题的产生原因都在于设备、模具、配方及工艺等方面的不足,只要具有完善的设备及模具,合理的配方及工艺,就能避免这些问题的产生。但是实际生产中,往往会产生这些问题,或产生了问题而不知原因和解决方法,这就要经验的积累。丰富的操作经验也是确保产品完美的条件之一。
3.4.3 其它塑料管件
除PVC塑料管件的生产以外,还有与其它塑料管材配套的塑料管件,例如CPVC(氯化聚氯乙烯)管件,PE(聚乙烯)管件,PPR(聚丙烯)管件等,这些管料的配方都不使用CPE(氯化聚乙烯)作用改性剂,因此在这里就省略了。