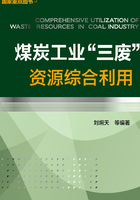
1.4 循环流化床锅炉传热特性
如前所述,循环流化床锅炉由主循环回路和尾部对流受热面两部分构成。在主循环回路中,除了完成燃烧之外,还要在燃烧的同时完成一定量的换热,使得燃烧的放热量的一部分被受热面吸收,保证主循环回路的出口也就是主循环回路的温度控制在合理水平。
1.4.1 燃烧室受热面的传热
循环流化床锅炉由于炉膛内部有高浓度的物料循环,因而其传热机理与常规的煤粉炉或层燃炉不同。煤粉炉和层燃炉的炉膛内由于烟气携带的飞灰浓度很低,因此主要通过辐射的方式将燃料燃烧释放的热量传递给受热面。为了保证足够的传热量,设计中要求煤粉炉的炉膛温度比较高。而循环流化床锅炉则不同。由于其炉膛内部有大量的固体物料的循环运动,因此不可忽视颗粒和气体的对流传热作用。而且因为循环流化床的床温保持在850~900℃这个较低的范围内,所以辐射传热量的份额也比较小。因此,循环流化床锅炉炉膛内部的传热既要考虑到对流传热的影响,也要考虑到辐射传热的作用。循环流化床锅炉的燃烧室中床对壁面的总体传热系数可达200W·m-2·℃-1,远大于一般的煤粉炉和固定床锅炉[11]。
在循环流化床锅炉内,气体与固体颗粒之间的传热系数是相当大的。这是因为,床内气固之间的滑移速度大,热边界层比较薄,传热热阻小。虽然单个细颗粒的滑移速度比较小,但是由于在悬浮段细颗粒有团聚行为而形成大尺寸的颗粒团,因此和气体之间仍能保证较大的滑移速度。而固体颗粒之间的频繁碰撞也导致其热边界层较薄,强化了传热。因此,气体与固体颗粒以及固体颗粒间的传热系数很大,使得炉膛温度表现出相当程度的均一性。
具体来说,循环流化床中的传热方式沿炉膛高度是不同的。在讨论床料与受热面之间的传热问题时,要分别考虑密相区和悬浮段的传热情况。
在炉膛底部的密相区内,由于物料浓度很高,返混流动剧烈,因此其传热方式以颗粒对流换热为主。这与鼓泡床埋管受热面的传热是一致的。在炉膛上部的悬浮段中,固体颗粒在上升气流中集聚形成颗粒团。大部分床料沿床中间区域上升,而在靠近壁面的区域内以颗粒团的形式贴壁下滑。在下滑过程中,这些颗粒团又会被近壁处的上升气流打散而随之向上运动,在向上的运动中再次形成新的颗粒团贴壁下滑,周而复始。因此向壁面的传热包括了气体的对流传热,固体颗粒的导热及气固流体对受热面的辐射传热等形式。
首先,悬浮固体物料的浓度对传热系数的影响是最主要的。传热系数随着物料浓度的增大而增大。固体颗粒对对流传热系数的影响非常明显,而烟气对流仅占总传热系数的10%~20%[11]。大量的研究表明,物料浓度是床对燃烧室内受热面传热系数的最大影响因素。有的研究认为循环流化床中传热系数与悬浮物密度的平方根成正比。由于悬浮段的固体物料浓度分布沿床高是按照指数形式衰减的,也就是说不同高度上的物料浓度是不同的,因此传热系数在不同的炉膛高度上也是不同的。其中辐射传热和对流传热所占的份额也是随之变化的。由此可见循环流化床锅炉中气固流体的流动对传热有重要影响。
其次,燃烧室的温度对传热系数也有较大的影响。床温的升高,不但加强了辐射传热,而且会提高气体的热导率,减小颗粒贴壁层的热阻,从而有效地提高总传热系数。近壁区贴壁下降流的温度有比中心区温度低的趋势,边壁下降流减少了辐射传热系数,而水平截面方向上的横向搅混有助于形成良好的近壁区物料与中心区物料的质交换,同时近壁区与中心区的对流和辐射的热交换使截面方向的温度趋于一致,综合作用的结果:近壁区物料向壁面的辐射加强,总辐射换热系数明显提高。因此,有些循环流化床锅炉在循环量不能达到设计要求的情况下,采用提高床温的办法来提高传热系数,保证锅炉出力。
粒径的减小会提高颗粒对受热面的对流传热系数。在循环流化床条件下,燃烧室内部的物料颗粒粒径变化较小,在较小范围内的粒径变化时传热系数的变化不大。
受热面的结构尺寸如鳍片的净宽度、厚度等对平均传热系数的影响也是非常明显的,鳍片宽度对物料颗粒的团聚产生影响,另一方面宽度与扩展受热面的利用系数有关。
此外,受热面的垂直长度也对传热系数有影响。炉内颗粒浓度较高时,当受热面的垂直长度较长时,顺着壁面下滑的颗粒团有足够的时间被冷却,从而形成一个比炉膛中心区温度低的热边界层,部分削弱了中心区对受热面的辐射换热影响。
H.Fang等建立了基于颗粒团交替模型的颗粒对壁面的局部辐射和对流换热模型,该模型和R.L.Wu等的实验结果吻合得较好[17]。B.Leckner认为在存在边界颗粒下降流的情况下,壁面与颗粒层之间存在一个颗粒很少的气体层,其中的温度梯度很大,这样由气体层和颗粒层构成了一个热力边界层。燃烧室中气固两相流对边壁的传热是通过边界层的传热来实现的。锅炉容量越大,边界层越厚。分析靠近壁面气固两相的质量、动量和能量平衡情况,可以得到床向壁面传热的详细情况[18]。P.Basu等认为循环流化床中对流和辐射会同时对气固温度场和热流形态产生影响,它们不具有线性叠加性,而交替传热模型更合理,认为在快速流态化下,颗粒团和分散相交替流过受热面。总的传热系数由对流传热系数和辐射传热系数直接相加得到。两项传热系数中的每一项再按颗粒团和分散相覆盖壁面的时间比例线性叠加[19]。B.Leckner的边界层分析方法比较复杂,与之相比,交替传热模型显得简单一些,用来解释循环流化床中的许多现象比较有效,但是难以考虑下降流对辐射的阻碍作用和粒径分布较广时的情形,所用的关联式并不能广泛地应用于各种工况,因而仍是比较粗糙的。
近年来,清华大学建立了循环流化床锅炉燃烧室受热面包括水冷屏、汽冷屏、水冷壁的传热系数计算方法,得到了实践验证,广泛用于工程设计,并被推荐为标准计算方法[20]。
1.4.2 其他部件传热
除水冷壁之外,循环流化床锅炉还有一些其他的换热部件,如冷却式分离器、外置换热器、冷渣机(器)等。
(1)分离器传热
对绝热式分离器而言,传热仅仅表现为散热损失;而对于冷却式分离器,受热情况较为复杂,由于分离器各位置上的流动情况存在差异,各处烟气中的固体物料浓度不同,因此详细的传热计算比较困难。一般的可采用燃烧室的近似计算方法[7],该处理方法不会引起较大的误差。
(2)外置换热器传热
将分离器分离下的循环物料的一部分分流至一个特定的流化床换热器进行换热,然后再返回炉膛,这样的换热器称为外置式换热器。调节直接返送物料量(返回炉膛的物料温度较高)与进入换热床的物料量(返回炉膛的物料温度较低)的比例可以调节床温,扩大燃料适应性,改善脱硫效率;同时可以调节蒸汽温度,因此外置式换热器在大型循环流化床锅炉上得到使用。外置式换热器有各种形式,但其原理基本是一样的。换热床实际是鼓泡流化床,受热面可以是过热器、再热器或蒸发受热面。利用鼓泡床的埋管传热计算方法,可以进行外置式换热器的传热计算,相应的结果已经得到了工程验证[20]。
(3)尾部对流受热面传热
布置在分离器出口之后的过热器、再热器、省煤器、蒸发对流管束和空气预热器,这些受热面都用来吸收烟气的热量。这部分的传热计算与传统煤粉锅炉基本一致。但由于分离器出口的烟气中含尘颗粒的粒度和形态与煤粉炉不同,由于未经高温熔化,灰分中碱金属化合物的蒸发较少,因此对尾部受热面的污染远远小于煤粉炉,尤其在较高温度时,这一区别更为明显,因此循环流化床锅炉的尾部烟道中受热面高温段的热有效系数比相应的煤粉炉高0.1~0.25,循环流化床锅炉的过热器若按煤粉炉传热计算方法设计,必然导致超温[20]。