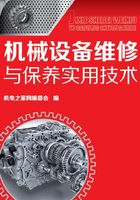
第1章 橡胶机械设备
1.1 概论
橡胶机械是用以制造轮胎等各种橡胶制品的机械,按照使用范围可分为通用设备和专用设备。其中通用设备包括炼胶设备、挤出设备、压延设备等;专用设备包括硫化机、成型机、裁断机等。按照加工过程的特点可分为炼胶设备、成型设备、硫化设备,检测设备、实验设备等。
1.1.1 橡胶机械的历史及现状
(1)橡胶机械发展历史
从1493年哥伦布将橡胶带回欧洲之后,橡胶制品逐渐进入人类的日常生活。1820年,汉冠克在英国伦敦建立了第一个橡胶厂,生产单辊炼胶机。此后1826年,欧洲人发明了开炼机。
1831~1839年间,古特异发明了硫化方法。
1843年,压延机问世。
1856年,可用于生产海底电缆的活塞式注射机出现。
1916年,班德利发明了橡胶密炼机。
20世纪40年代,出现了冷喂料挤出机。
20世纪70年代,随着计算机应用的普及,橡胶机械初步数字化,工作效率越来越高。
进入21世纪以后,随着高分子科学的发展,橡胶机械迎来全新的发展时期。
(2)我国橡胶机械发展现状
我国是世界橡胶机械的生产大国,是世界橡胶机械发展最快的地区,正成为世界橡胶机械的中心。我国橡胶机械工业生产连年飙升,销售扶摇直上,呈现井喷式发展之势。我国橡胶机械正在世界东方崛起,并开始确立大国地位。
2004年,中国橡胶机械行业销售收入突破60亿元,实现了跨越式发展,其中,26家企业销售收入达45.7亿元,同比增长57%;出口交货值4.53亿元,同比增长171%;产品销售率达到99.2%。2005年,中国橡胶机械行业的增长速度较2003年和2004年的“井喷”式行情明显放慢,但利润持续增长,出口创汇也有较大幅度增长。
2006年,中国橡胶机械29个主要单位实现橡胶机械产值52.6亿元,比上年增长16.1%;销售收入52.48亿元,比上年增长14.8%。以此估算,中国橡胶机械销售收入达到72亿元,比上年增长10.8%。
2007上半年,中国25家主要橡胶机械生产企业实现销售收入26.86亿元,同比增长17.4%,实现利润同比增长53.7%,表明橡胶机械行业经济效益进一步好转。
中国橡胶机械产业在不断发展的同时,科技创新和产业化能力还有待加强,现有的专利主要集中在少数企业,且主要集中在硫化机、成型机上,在数量上也与国外存在较大差距,而实际在科技成果转化方面还有较大潜力可挖。中国橡胶机械品牌意识及影响力不足也是制约其做“强”的一大因素,而且大多企业的国际化步伐较慢,此外,产品的售后服务更是软肋,还没有建立起完善的全球服务体系。
中国橡胶机械厂家必须建立自己的科技创新体系,加大产品开发的力度,开发出一批具有自主知识产权的新产品。并树立全球大市场的观念,加速从“国内型”工厂向“国际化”企业的转换。同时,企业还要树立品牌意识,争创中国的橡胶机械名牌,进而争创世界的橡胶机械名牌。
“十一五”期间,橡胶制品将全面更新换代,这向国内橡胶机械行业提出了新要求,也提供了新商机,国内橡胶机械企业还需进一步跟上和满足橡胶制品技术进步的要求,尤其要注重非轮胎橡胶制品橡机的开发,以实现和橡胶工业的同步发展。“十一五”期间,中国轮胎年总产量将达到3亿条,子午化率将达到70%,其中,全钢胎要发展无内胎及公制轮胎,半钢胎要发展宽断面、高速度级别产品,工程胎子午化也势在必行,这些都需要橡胶机械制造厂提供新型设备,同时还要满足橡胶工业安全、节能、环保的发展要求。除轮胎设备外,橡胶机械企业还应将目光转向非轮胎橡胶制品设备。
1.1.2 橡胶机械发展趋势
橡胶机械设备种类繁多,各设备在生产能力和生产效率相比以往都有提高,本文篇幅所限,不能一一介绍,仅对几个典型设备的发展趋势进行阐述。
1.1.2.1 开炼机的发展方向
开炼机是橡胶工业中的基本设备之一,也是三大炼胶设备之一,它是橡胶工业中使用最早、结构比较简单的最基本的橡胶机械。早在1820年就出现了人力带动的单辊槽式炼胶机。双辊筒炼胶机于1826年应用在橡胶加工生产中,至今已有180多年的历史。我国设计制造大型开炼机始于1955年。近五十年来,开炼机的设计和制造水平有了很大提高。近几年来国产新型结构开炼机不断地涌现。有力地促进了开炼机的发展。到目前为止,国产开炼机已成为系列,并完成了部分规格的定型设计工作,并已出口国外。
随着橡胶工业的不断发展,开炼机在逐步地完善和不断地更新。在自动化流水混炼作业线中,由于挤出压片机、密炼机和连续混炼机等设备的应用和发展,开炼机的使用范围已显著缩小,但在中、小型工厂中,特别在再生胶和小批量特殊胶种以及胶料的生产中,应用仍较为普遍。国外人士认为,密炼机并没有代替开炼机,密炼机只是制造出接近完成的胶料,而以后的加工,最好还是用开炼机去继续完成。国外开炼机系列都无多大变化,结构上已趋于定型,只不过是在零部件方面不断创新。其发展的动向是提高机械化自动化水平,改善劳动条件,提高生产效率,减小机台占地面积,完善附属装置和延长使用寿命等方面。
今后发展方向如下。
(1)控制方面,实现自动化操作,改善劳动条件。
(2)调距方面。
(3)轴承方面。
(4)安全装置(全方位刹车)。
(5)传动方面,采用双出轴。
(6)辊筒的材质及铸造方法。
1.1.2.2 橡胶挤出机的发展趋势
橡胶挤出机设备将向以下几个方面发展。
(1)多螺杆
螺杆挤出机螺纹元件的啮合区具有较大的速度梯度,因此,在啮合区有利于物料的充分混合。双螺杆、“一”字型三螺杆、三角形三螺杆和四螺杆挤出机的啮合区个数分别为1个、2个、3个、4个,由于啮合区个数的增加,物料混合能力也逐渐增强,三角形三螺杆和四螺杆挤出机具有特殊的结构——中心区。中心区的物料形成环流,环流的存在促进了中心区物料的混合,增加了物料在中心区的混合时间。经过分析,物料不会滞留于中心区。双螺杆、“一”字型三螺杆、三角形三螺杆和四螺杆挤出机的流量、回流量、回流系数以及平均剪切速率依次逐渐增大,从理论上验证了多螺杆挤出机在物料输运能力以及物料混合能力等方面均具有较佳的生产能力,多螺杆挤出机更适合聚合物的加工。
(2)多流道
MCT挤出机沿螺杆轴向分为进料段、传递混合段和出料段。在传递混合段,螺杆和机筒内壁有螺旋相反的螺纹,在螺杆上流道数逐增、螺纹深度逐减,在混合传递区中部达到极值后逐渐恢复原状,在螺杆流道增多的过程中,机筒内壁上流道数与螺杆上流道数相反、流道深度也与螺杆相反。
MCT挤出机与普通冷喂料螺杆挤出机在本质上有很大的区别,普通螺杆挤出机是利用摩擦作用进行塑化,而MCT挤出机胶料塑化是依靠机械作用进行的,摩擦力很小,因此,MCT挤出机的螺杆长度远比普通挤出机的螺杆长度要短,仅为螺杆直径的7倍左右。
MCT挤出机不仅能用于生产易挤出的载重轮胎胎面胶等混炼胶及半成品,还能用于生产较难挤出的高合成橡胶组分物料,并且表面质量和外轮廓边角形状好。MCT挤出机的螺杆比普通型挤出机螺杆短,易于将两个或三个MCT挤出机组合在一起,实现复杂制品的“复合”,共挤出。如可以由一台95mm主MCT挤出机和两台50mm副MCT挤出机组成“三复合”挤出机。由于MCT挤出机的塑化混合区很短(约2.5D),流道内没有障碍干扰元件,螺翅和流道对物料有助推作用,物料在机内的温升低,使得螺杆转速高,生产能力大,一般MCT挤出机在螺杆、机头、轴承和加料区设置调温口,在温升相同的条件下,MCT挤出机的生产能力大于销钉机筒挤出机,更大于光滑机筒挤出机。
(3)多复合
挤出机头是决定挤出制品最终质量的一个关键部件。传统的单螺杆挤出机头仅能用于挤出单一品种胶料的制品,机头结构比较简单,机头压力也比较低,因此,技术问题容易处理。随着挤出工艺的发展和生产的需要,挤出机头的结构和技术与十多年前相比,有了很大的发展,特别是轮胎生产中要求采用不同性能的胶料在机头内复合挤出胎面、胎侧和三角胶等部件,为此,从20世纪60年代起,由德国Troester公司和Berstorff公司首先开发了用于挤出两种胶料的双复合挤出机头,到了20世纪80年代和90年代开发了三复合和四复合挤出机头,正在研制开发五复合挤出机头,不久将有产品问世。
(4)新驱动
随着挤出工艺对挤出机性能要求的提高和驱动技术的进步,挤出机的驱动系统发生了许多变化,传统的交流电动机定速驱动、整流子电动机变速驱动及交流电动机齿轮箱有级变速驱动在国内外现代挤出机中已被淘汰,取而代之的是直流电动机无级变速驱动。直流电动机在低速时具有良好的扭矩性能,调速范围广。国内直流电动机在西门子技术的支持下已达到国际一流水平,已在各种冷喂料挤出机上得到广泛应用。
(5)控制系统
发达国家的挤出机已普遍采用现代电子和计算机控制技术,对整个挤出过程的工艺参数如熔体压力及温度、各段机身温度、主螺杆和喂料螺杆转速、喂料量,各种原料的配比、电动机的电流电压等参数进行在线检测,并采用微机闭环控制。有的公司已采用网上远程监测、诊断和控制,对挤出成型生产线进行网络控制。这对保证工艺条件的稳定,提高产品的精度都极为有利。
随着挤出机的复合化,其机械性能必然更为复杂,与之相匹配的控制系统也随之复杂化,控制精度也更高。因此,如何设计出合适的控制系统才能保证其经济、安全可靠地运行,且不至于在短时间内成为淘汰或过渡产品,是我们工程设计人员所必须考虑的问题。在多复合挤出机的控制中,总线技术、网络结构简单,技术性能稳定,不但大大减少了布线量,便于安装调试及维修,而且极大地增强了系统的灵活性与可靠性,在保证系统先进性的同时,也取得了良好的社会经济效益。
收缩变形小、尺寸精度高、挤出速度快的精密型挤出机新型螺杆挤出机开发、复合共挤技术的不断成熟,最近几年,橡胶工业飞速发展,带动中国橡胶挤出技术的迅速提升。其中子午线轮胎复合共挤技术可谓橡胶挤出技术水平的典型代表。
(6)精密技术
挤出成型是一种高效、连续、低成本、适应面宽的加工成型方法,但人们错误地认为,挤出成型是一种低精密度、低附加值的成型加工方法。随着各种高精密制品市场,如以光导纤维、医用导管、音像片基、照相胶片片基、投影胶片为代表的一系列高精密制品的市场需求与日俱增,对精密挤出成型设备与技术的要求也不断增加。对一些特殊的加工成型,如对一些危险和有毒物料的加工、反应挤出过程等需要严格控制温度、压力、物料停留时间及其分布等过程参数,以及反应物料与外界的热量传递等,这些用普通挤出机往往是不能胜任的,精密挤出成型机为各种复杂的反应挤出工艺提供了必要的装备条件。国内厂家在高速、精密设备方面与世界先进水平相比还有较大差距。专家认为,高产挤出设备无论是在实际水平,还是加工水平上都与国外先进水平存在 15~20年的差距。在实时工艺参数和制品参数监测,以及先进控制技术的采用方面存在的差距也很大。先进的高精度在线检测仪器主要依赖进口,国内的产品寥寥可数,且与国外产品的差距在10年以上。整体来说,中国精密挤出成型装备还处在起步阶段,发展空间很大。
1.1.2.3 橡胶硫化机的发展趋势
由于机械式硫化机本身结构的原因,机械式硫化机存在如下问题。
① 连杆、曲柄齿轮等主要受力件上的运动副,是由铜套组成的滑动轴承,易磨损,对精度影响较大。
② 上下模受到的合模力不均匀,对双模轮胎定型硫化机而言,两侧受力,大于两内侧的受力。
③ 上下热板的平行度、同轴度,机械手卡爪圆度和对下热板内孔的同轴度等精度等级低,特别是重复精度低。
合模力是曲柄销到达下死点瞬间由各受力构件弹性变形量所决定的,而温度变化使受力构件尺寸发生变化,合模力也随之发生变化,因此,生产过程中温度的波动将造成合模力的波动,使产品质量无法保证。而液压式硫化机在结构上能够很好地解决这个问题,从未使得液压式硫化机成为当前研究热点。
液压式硫化机结构上具有如下特点。
① 机体为固定的框架式,结构紧凑,刚性良好,在大合模力作用下变形小,有利于轮胎寿命和轮胎质量。虽然液压式硫化机也是双模腔,但从受力角度看,只是两台单模硫化机连接在一起,在合模力作用下,机架微小变形是以模具中心线对称的。
② 各动作快速平稳,大大减少了硫化机辅助时间。
③ 机器精度高,大大提高了轮胎定型精度。开合模时,上模部分仅做垂直上下运动,可保持很高的对中精度和重复精度;另一方面,对保持活络模的精度也较为有利。
④ 上下合模力受力均匀,不受工作温度影响。
⑤ 机器的左右机架可以各配一套控制系统,可进行单独控制,独立工作。
⑥ 机器各动作简单有效,在用户使用过程中,基本上没有易损件,备件需要更换,也不需要机械式硫化机那样定期中修、大修,大大减少了用户运行成本,增加了设备使用率。
由于以上优点,液压式硫化机正逐渐成为橡胶硫化设备的主流设备。