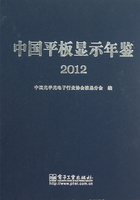
2011年全球彩色滤光片产业现状与发展
一、市场分析
近年来,光电显示产业中以薄膜晶体管液晶显示器件(TFT-LCD)为首的平板显示(FPD)产业得到了迅速发展。由于TFT-LCD具有一系列突出的优点,其产品几乎涵盖整个信息应用领域,包括电视、个人计算机、笔记本电脑、手机、GPS、PDA、仪器仪表和公共显示等方面,应用领域非常广泛,具有巨大的市场潜力。它将计算机、办公自动化、电视、通信和仪器仪表等产品推向了一个崭新的发展阶段。国际著名咨询公司DisplaySearch研究表明,全球FPD产业2011年整体产值达到了1109亿美元,2012年全球FPD产业产值将达到1278亿美元。整体FPD产业2011年以前年复合增长率为20%以上,以后增幅趋稳,将维持在10%左右,显示出FPD产业仍处于增长期。
从产业链配套来说,彩色滤光片(Color Filter,CF)是TFT-LCD重要的关键配套件之一,也是显示器件真彩色化的必要组件。在TFT-LCD显示面板制作工艺中,每块LCD显示面板就需要搭配一片CF玻璃基板,以构成一块完整的LCD显示面板,可以说两者是一个共同体。近年来,随着国内液晶面板厂商的不断兴建,CF生产厂商也随着面板厂商的发展不断进行新世代设备的投资。特别是充分利用现代物流业的发展,内置(In-house)方式供应CF已越来越明显。内置的实现可减少产品库存,降低运送风险及材料成本。
根据DisplaySearch的报告显示,目前全球在建CF生产线如表1所示。
表1 全球在建CF生产线统计

资料来源:DisplaySearch2012Q1
1. 国内外现状
CF是LCD面板实现彩色化显示的关键原材料,必须与LCD面板一对一同样大小搭配使用,因此CF的技术发展与LCD面板的技术发展息息相关。日本、韩国是早期制造CF的国家,虽然近几年我国企业也在努力追赶,但目前生产CF的许多关键技术、重要生产设备以及光刻胶等关键原材料仍主要掌握在日韩厂商手中。随着2003年以来全球彩屏手机的兴起和迅速普及,以及液晶显示器、笔记本电脑、液晶电视等产品销量的快速增长,带动了TFT-LCD彩色面板市场快速扩张,生产LCD面板的关键原材料CF的产量也随之获得大幅增长。韩国、中国台湾和中国大陆抓住LCD行业发展的机遇,推动本地CF产业快速发展。
在TFT-LCD用CF方面,目前日本的凸版印刷(Toppan)、大日本印刷(DNP)和Toray仍是CF专业制造商;韩国和中国台湾的主要液晶面板厂多数选择CF内置(In-house);目前国内TFT-LCD用CF的生产基本也已实现内置(In-house)。其中韩国面板厂由于拥有多条大尺寸面板生产线,CF的产量也最多,占到全球总产量的40%左右;日本的专业CF制造商则以生产第6代线以下所用的CF为主。各厂商产能分布情况统计如图1所示。

图1 各厂商产能分布情况统计
资料来源:DisplaySearch2012 Q1。
2.市场分析
作为与TFT-LCD的共同体,每块LCD显示面板需要搭配一片CF玻璃基板,以构成一块完整的LCD显示面板,因此TFT-LCD的广阔市场将同样是CF的广阔市场。CF市场供需趋势如图2所示。

图2 CF市场供需趋势
资料来源:DisplaySearch2012 Q1。
注:供需比=(供给-需求)/供给,根据研究表明,10%~15%为合理的供需配置。供给与需求数量折合为19英寸显示屏计算。
根据DisplaySearch的报告显示,2011年第四季度CF的供给超过需求,2012年第二季度,CF将处于短缺局面,供需情况呈现波动。
2011年CF全球需求量达到11.6亿片,比2010年增长4%,2012年预计将达到13.35亿片,增幅达到15%。其中液晶电视用CF需求最大,占比达到50%左右(见图3)。

图3 CF需求预测——根据产品分类
资料来源:DisplaySearch2012 Q1。
3.内置CF是TFT-LCD产业发展的趋势
三星、LGD、友达、奇美、京东方等全球领先的液晶面板厂新建的TFT-LCD工厂大多选择CF内置(In-house)方式,其中LGD、奇美、京东方的CF内置率已超过70%,CF内置化是产业发展的趋势。CF内置和专业制造产能比较如图4所示。

图4 CF内置和专业制造产能比较
资料来源:DisplaySearch2012 Q1。
目前以京东方为首的国内厂商也开始实现了CF内置,包括京东方成都第4.5代TFT-LCD生产线、北京第8.5代TFT-LCD生产线、合肥第6.5代TFT-LCD生产线、鄂尔多斯第5.5代AM-OLED生产线;天马武汉第4.5代TFT-LCD生产线、厦门第5.5代LTPS生产线;华星深圳第8.5代TFT-LCD生产线等均已实现或规划CF内置。
TFT-LCD与CF的同步建设和同步运营,CF和LCD设计一体化对于降低成本,持续改善LCD产品的品质和性能,增强市场竞争力具有非常重要的作用。
二、CF目前主要量产技术分析
CF制造工艺一般分为颜料分散法、染料分散法、印刷法和电镀法四种。几种主要CF制作工艺的性能比较如表2所示。
表2 制作工艺的性能比较

现在国际上广泛使用的是颜料分散法。颜料分散法是将颜料分散在感光胶中,通过掩膜曝光,被曝光部分的感光胶聚合,不易为显影液溶解,在显影时保留下来,其余部分被冲洗掉,如此重复数次,形成彩色膜层。
颜料分散法常用的颜料为酞青类等,粒径应小于0.2µm。在颜料生产中首先形成的是线度为0.1~0.5µm的单晶,称为一次粒子。它们易聚集成线度为0.1~10µm的二次粒子,所以必须分散后才能使用。
彩色光刻胶是一种用于生产CF红、绿、蓝三原色的感光材料,CF一般是通过在玻璃基板上涂布彩色光刻胶,再使用曝光技术形成像素图案来制造。
光刻胶由多种成分构成,包括通过曝光形成硬化诱因的光引发剂、形成图案的光刻胶聚合物、着色颜料、使颜料分散的分散剂、用于形成图案的多官能团单体,以及用以实现整洁涂布的溶剂。
目前使用的光刻胶为负性材料,利用曝光部分会交联固化,通过碱性显影液不溶的性质来绘制图案。其中,形成色彩的颜料种类格外少。而且,颜料原本就不溶于有机溶剂,要想使颜料稳定分散于有机溶剂中,需要使用分散剂。分散剂通常使用特制聚合物。此外,形成图案的聚合物则使用数种聚合物,一般多使用丙烯酸类聚合物,使用丙烯酸类聚合物的原因在于可轻松发挥碱溶解性。而且,通过改变官能团,还可赋予各种各样的功能。通过这些手段,便可控制光刻性能及永久性能。光刻胶反应机理如图5所示。

图5 光刻胶反应机理
上述这种颜料分散法,工艺简单,光敏性好,是目前大生产中用得最多的。制成的滤色片有很高的热稳定性,可耐250℃高温,而且化学稳定性、耐湿性和耐磨性也很好。
精工爱普生曾于2006年开发出了采用喷墨技术制造液晶面板CF的装置,并向夏普制造大屏幕电视专用液晶面板的龟山第2工厂供货,但由于种种原因未被大规模普及采用。
2012年6月,DNP公开发表了使用柔性玻璃作为基板以卷对卷(R2R)方式制造CF的工艺,该工艺所使用的是厚度仅为0.05~0.07mm的极薄玻璃基板。由于非常薄,即使弯曲也不会破裂,该滤光片的最小弯曲半径为3cm。由于R2R要求基板可以弯曲,因此以前普遍使用树脂薄膜作为基板。如果能够使用玻璃基板,不仅能够扩大成膜工艺的选择范围,而且玻璃具有耐热性、气密性、伸缩性等特点,比树脂薄膜更为有利。该工艺预计于2014年度开始量产。
以上四种工艺各有各自的市场,其中,颜料分散法以其优越的热、光稳定性已逐步取代染色法成为当今最具竞争力的CF制作方法,占据了国际市场90%以上的份额,目前世界主流的CF制造厂商包括CF内置生产的液晶面板厂商均采用颜料分散法。
三、CF发展方向
1. 高分辨率
自2010年以来,高分辨率液晶面板就已经引起了市场更多的关注。在手机等小尺寸面板上最成熟的高分辨产品,又被称为“视网膜(Retina)屏幕”,它可以将960×640的像素压缩到一个3.5英寸的显示屏内——这样高的像素密度,甚至超过了人类视网膜的分辨能力,因此可以带来“最接近真实”的柔滑显示效果。此种面板被应用在苹果手机上,取得了非常好的市场效果。2012年日本显示器公司开发出了分辨率高达651ppi的2.3英寸1280×800像素液晶面板(见图6)。作为直视型显示器,“实现了世界最高水平的分辨率”新产品的像素间距仅为39µm。

图6 日本显示器公司公布的2.3英寸651ppi的显示器
随着美国苹果公司iPad3的上市,高分辨的争夺战逐渐延伸至中大尺寸液晶显示器上,人们对分辨率的认识上升到一个新的阶段。
在大尺寸的液晶电视应用方面,2012年4月,夏普正式发布了采用IGZO材料的新型高分辨率液晶面板产品,包括:32英寸的4K×2K分辨率的显示器面板(140ppi),10英寸具有WQXGA分辨率2560×1600的笔记本电脑用面板(300ppi),以及7英寸分辨率为1280×800的平板电脑用面板(217ppi)。
高分辨率液晶面板对CF提出了高分辨率的要求,越来越高的分辨率要求像素越来越小。不过,液晶面板高精细化到400ppi以上时存在技术课题。由于平均每一个像素的开口率较低,因此背光源的光利用效率下降,容易导致亮度降低及耗电量上升。实际上,从面板开口率来看,403ppi产品为50%,498ppi产品为41%~49%,651ppi产品为32%,为了保持与现在的产品具有相同的开口率,黑矩阵(BM)的线宽越来越细。凸版印刷制作高精细黑矩阵在330ppi时线宽已达到5.5µm,预计在440ppi时线宽可以细至4µm,针对500ppi的分辨率,黑矩阵线宽要求达到3µm(见图7)。

图7 LTPS-LCD需求预测黑矩阵(BM)线宽与开口率的关系
CF高精细的趋势对材料和设备提出了新的挑战,普通的黑矩阵材料在应对高精细时容易出现膜层脱落,遮光性能不足等,坡度角太小,在线宽很小时导致对比度降低。各大材料厂商在改善高分辨率的黑矩阵材料方面不遗余力。在CD Bias、坡度角形状与角度、角段差以及与玻璃基板的黏附力以及高遮光方面入手进行改善。
同时,对于高精细的追求也进一步刺激了对设备改造的市场,最初应用于普通分辨率的曝光机,如日立的接近式曝光机的改造需求显得尤为迫切,过滤掉多余的曝光波段或提升光线的垂直度都成为改造的选择。
2. 高光透过率
高的分辨率对光透过率的要求也越来越严格,一方面,高分辨率要求像素越来越小,为了保持现有产品的透过率,可以通过降低黑矩阵线宽以提高开口率,也可以通过材料改进来提升透过率。目前材料厂商主要从以下几方面入手。
1)颜料细化
颜料颗粒粒径如果太大,就会直接导致光线被阻挡而未能全部通过;如果是小粒径颜料与大粒径颜料混合而成的彩色光刻胶的话,就容易产生光的散射,结果会使光透过率下降,同时对比度也会不同程度下降。要想提高透过率与对比度,就必须统一颜料的粒径且尽可能小。只要减小粒径,形状及粒径不均现象就会减轻,但如果颜料颗粒粒径过小的话,颜料就会发生团聚现象,仍会形成大粒径的颜料,这部分问题可通过纳米技术来解决,如图4所示。

图8 颜料粒径大小影响光的透过性
2)开发高透过率新材料
通过开发新的CF光刻胶组成成分,可适当提升彩膜的透过率,开发的主要对象有:①颜料;②分散剂;③粘黏剂。
由于形成色彩的颜料种类格外少,因此颜料的开发不仅体现在寻找新种类颜料上,也在于不同颜料之间的组合。同时,颜料原本就不溶于有机溶剂,要想使颜料稳定分散于有机溶剂中,需要使用分散剂。分散剂随着颜料会最终固化成为CF中的组成部分,分散剂对光的透过率有较大影响,因此寻找和合成高透过率的分散剂也是提升CF性能的必要途径。而形成图案的聚合物粘黏剂则使用数种聚合物,一般多使用丙烯酸类聚合物。使用丙烯酸类聚合物的原因在于可轻松发挥碱溶解性。而且,通过侧链官能团的不同修饰,还可赋予各种各样的功能。通过这些手段,便可控制光的透过性(见图9)。

图9 高透过性的光刻胶组成材料提升光透过率
3)染料
由于形成色彩的颜料的种类格外少,对于形成色彩物质的不断探索使开发者们将目光投向了另一种形成色彩的物质——染料。
由于染料的可溶解特性,因此对光的阻挡和散射非常小,相比较于颜料有非常大的提高,但是由于染料的不稳定性和制成品的光敏感度差的问题,限制了其在CF中的使用。目前各光刻胶生产厂商主要的突破点在蓝色染料方面,且是部分颜料和染料的混合体,如图6所示。

图10 颜料+染料混合型应用于光刻胶中对光的透过率的影响
另外,作为制造高亮度面板的方法,在TFT阵列上形成彩色滤光层的“Color Filter On Array(COA)”技术能够降低黑色矩阵的线宽,大大提高开口率,透过率也会相应大幅度提高,从而可以降低功耗。
四、新技术
1. RGBW技术
随着显示技术的发展以及人们消费水平的提高,消费者在挑选显示器时已经不仅仅注重显示器的技术性能和价格,图像显示的视觉感受已经成为选择显示器的一个重要方面。而对于图像的显示效果来说,颜色和亮度又是最直观、最容易被人眼所感受的因素。目前所广泛使用的显示设备,特别诸如手机、笔记本电脑等便携式设备,多存在亮度不足的缺陷,而要提高显示的亮度、扩大色域,就要增加功耗,这对于便携式设备来说是致命的。
RGBW技术可以说是应运而生。它是把一种白色子像素W添加到红、绿、蓝三色子像素组成的传统的RGB条纹排列中,然后再应用相应的子像素成像技术,以人眼看见图像的方式对那些子像素进行排列,从而实现图像显示。RGBW技术的最大优势在于,因彩色滤光片中除RGB三色以外增加了W白色透光区域,从而可以显著提高LCD对背光的利用率,增加LCD的显示亮度,降低显示功耗。
图11所示为两种常见的RGBW排列方式,目前各大公司多采用传统的条纹状RGBW方式,而事实上由于列驱动IC成本比行驱动IC成本高,棋盘状排列的RGBW结构成本明显会低得多。然而,棋盘状RGBW排列的使用却面临着专利限制,这也是目前各大公司多采用条纹状RGBW方式的原因。

图11 RGBW排列方式图
RGBW结构的显示器因其亮度高、功耗低,同时也提高了电池的使用寿命,对移动便携式显示器有着巨大的吸引力。目前,三星、LG等各大公司纷纷投入RGBW相关技术与产品的开发,如索尼开发的“White Magic”液晶屏技术等。
2. COA技术
传统的TFT-LCD面板制作方式是由一片TFT面板玻璃,与另一片CF玻璃贴合而成,两层玻璃中间再灌入液晶分子。这样TFT玻璃与CF玻璃在贴合中的对位必须非常精准,同时就会造成显示屏的开口率较低。为了克服这个问题,业内提出了COA技术的概念。
COA(CFon Array)的技术原理为在下玻璃基板上完成TFT制程后,紧跟着进行CF制程,而上玻璃仅单纯做ITO涂覆处理,具体结构如图12所示。

图12 COA结构图
COA技术具有以下优点:
(1)上下基板自对准,省却了对准工艺。在传统结构中,当上下两片玻璃分别加工完成薄膜晶体管和CF层后,需要将两片玻璃上相应的像素位置对准后再封盒,对准工艺的准确性直接影响产品的质量。而采用COA技术后,两者都在一片玻璃上,可以自对准,省却了对准工艺,简化了加工过程,提高了产品质量。
(2)降低了生产成本。由于将彩色滤光层制备在薄膜晶体管上,简化了CF的制作工艺,提高了生产效率,同时可减少材料使用量,有效地降低了成本,有助于提升产品竞争力。
(3)提高了产品性能,增大了开口率,提高了光透过率。采用COA技术可降低黑色矩阵的线宽,大大提高开口率,光透过率也会相应大幅度提高,同时降低功耗。
由于COA技术具备上述优点,目前各大厂商纷纷投资进行相关研究。自东芝公司发布COA技术以来,三星、LG、夏普、Hannstar等厂商都开发了自己的原型技术。据韩国eTimesinternet报道,三星电子已经开始采用COA技术生产TFT-LCD产品。
3. TP In-Cell技术
随着近几年苹果iPhone系列的热卖,触控(TP)显示逐渐为广大消费者认可,目前几乎已被视为高端智能手机产品的必需元素。目前发展最好的触摸屏是电容式触摸屏,其基本组成是:在一块玻璃基板上制作第一层Sensor感应层,接着再制作第二层Sensor感应层,最后在表面覆盖一层保护膜,形成电容式触摸屏,然后将触摸屏和TFT-LCD液晶面板贴合,就能实现触控功能。
然而,随着电子产品设计日趋更轻、更薄的发展要求,上述传统的外挂式触控显示(TP Out Cell)显得越来越笨重,而内嵌式触控技术(包括On-Cell和In-Cell两种)被各界看好,很有机会“抢攻”大中小尺寸触摸屏应用市场,目前已经成为热门话题。
内嵌式触控技术可以真正实现一站式无缝生产,On-Cell和In-Cell技术也被称为触控显示的最终解决方案。其缺点在于对良品率要求很高,如果触控模块出现问题则会影响整块面板,但由于内嵌式技术一方面能够简化生产流程且触摸屏能做到最轻薄,另一方面由于面板厂商集成触控模块只需要5~10美元的成本,其相对Out Cell外挂式触控的方式能够节省35%的成本,因此各面板厂商非常有动力提升良品率,以早日实现内嵌式触摸屏技术的盈利。
TP On-Cell技术可以称为半集成方式,将触控屏Sensor直接做在LCD显示屏CF板的背面,目前该技术比较成熟,主要应用在三星Super AM-OLED屏上。而TP In-Cell技术则将触控层完全集成到LCD面板中,近期LGD等厂家声称已解决了触控层对LCD的干扰问题,剩下的只需要提升良品率,2013年中期有望小批量试生产,但要量产仍有待时日。
五、CF产线未来的发展方向
从长远来看,未来LTPS技术、OLED技术将会是显示市场的主流,未来CF生产厂商何去何从,根据目前市场和技术的发展趋势,主要有以下几种。
1. Touch Panel On Cell
相对于将触摸面板外置在液晶面板上的方法,越来越有发展空间和前景的是将触摸面板功能与液晶面板集成一体化(见图13和图14)。这类集成一体化包括“In-Cell”方法和“On-Cell”方法。In-Cell是指将触摸面板功能嵌入到TFT晶体管、CF上的方法。On-Cell是指将触摸面板功能与CF基板集成到一张玻璃基板上,目前市场上还没有大批量供货的案例,包括日本、韩国企业,以及国内的京东方等都在积极布局On-Cell并已经有样品试产。

图13 普通液晶盒结构(无TP层)

图14 触摸集成功能液晶盒结构
如果能使原本外置的触摸面板部件与液晶面板实现一体化,便有可能实现面板的薄型化。In-Cell技术的提案以前就提出过,但受制于成品率和噪声的影响,实用化未能取得进展。其原因在于,需要在TFT阵列基板上的像素内部嵌入触摸传感器功能。为此,必须使用复杂的半导体制造工艺,这成为提高成品率的绊脚石。另外,在像素内嵌入触摸传感器,可利用于显示的面积部分便会减少,这又是导致画质劣化的主要原因,同时,液晶面板产生的噪声会导致触摸传感器的灵敏度降低。
不过,随着On-Cell技术的亮相,液晶和触摸面板的一体化迎来了转机,也为未来CF生产厂商迎来了持续发展的契机。由于只需在CF基板和偏光板之间形成简单的透明电极图案等,因此容易确保成品率。另外,像素内的有效显示区域的面积也不会减小,几乎不会由此发生画质劣化现象。唯一需要解决的就是触摸面板的保护问题。
如果On-Cell方式等液晶一体化技术得到普及,就无需再使用外置的触摸面板部件。制造触摸面板的厂商很有可能从原来的外置触摸面板厂商转型为液晶面板和CF厂商。产品厂商从触摸面板厂商手中采购外置部件的原供应链也将完全改变。
2. 白色OLED
OLED作为下一代梦幻般的显示器,具有全固态、主动发光、高亮度、高对比度、超薄、低功耗、全视角、可实现柔性显示、透明显示等诸多优点,被业界认为最有发展前景的新型显示技术之一,是国际上高技术领域的一个竞争热点。OLED的彩色化技术适合量产大尺寸的暂时只有两种——白色OLED+彩色滤光膜(Color Filter)和RGB像素独立发光。
1)白色OLED+CF
此种技术是利用白光OLED结合彩色滤光膜,首先制备发白光OLED的器件,然后通过彩色滤光膜得到三基色,再组合三基色实现彩色显示。该项技术的关键在于获得高效率和高纯度的白光。它的制作过程不需要金属荫罩对位技术,可采用成熟的液晶显示器LCD的彩色滤光膜制作技术,所以是未来大尺寸全彩色OLED显示器具有潜力的全彩色化技术之一,但采用此技术造成了光利用率的降低。目前夏普、奇美以及LGD均采用白光搭配CF技术。
2)RGB像素独立发光
利用发光材料独立发光是目前采用最多的彩色模式。它是利用精密的金属荫罩与CCD像素对位技术,首先制备红、绿、蓝三基色发光中心,然后调节三种颜色组合的混色比,产生真彩色,使三色OLED元件独立发光构成一个像素。该项技术的关键在于提高发光材料的色纯度和发光效率,发光材料的发光效率和寿命都有待提高。不断地开发性能优良的发光材料应该是材料开发工作者的一项艰巨而长期的课题,同时金属荫罩刻蚀技术也至关重要。采用RGB像素独立发光的主要有韩国三星。
从材料的角度看,目前只有RGB像素独立发光技术和白色OLED+CF可量产大尺寸OLED。RGB像素独立发光的优势在于色彩和亮度,仅从技术角度考虑,大部分企业在生产OLED产品时会采用RGB技术,但是白光产品工艺简单、成品率高、成本较低,适合大规模低、成本生产。从行业的长远发展来看,RGB像素独立发光技术更有发展前景。
白色OLED+CF方式与分涂RGB三色发光材料的方式相比,除了容易实现大屏幕化外,还易于确保量产时的成品率。但存在的问题是,采用CF会导致耗电量增加,光透过率下降。不过可通过追加W(透明)CF,降低耗电量。与采用分涂RGB三色发光材料的方式相比,白色OLED+CF方式平均显示画面的耗电量稍高一些,但全白显示时的耗电量较低,W部分没有滤光片,因此具有可提高亮度的优点,显示某种特定颜色时,只需点亮W和RGB中的2种颜色即可,因此有利于提高OLED元件的寿命。不过为了达到高NTSC规格比,需要合理控制RGB层厚度,并且大多数都将CF形成于TFT底板上(Color Filter on Array)。
总之,2011年彩色滤光片产业呈现内置化、高分辨率、高光透过率的发展趋势。而展望未来,通过开展白色OLED+CF、RGB像素独立发光、TP内置化工艺等创新发展模式,彩色滤光片产业将迎来更加广阔的发展前景。