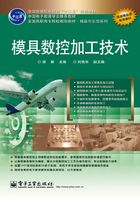
学习情境1 模具数控加工技术导论
要点链接



项目1.1 数控机床的认识
职业能力 具备正确认识数控机床及数控系统的能力。
任务1.1.1 数控机床加工原理及过程的认识
任务描述 了解数控机床加工原理及过程,并掌握数控机床坐标系的确定。
任务分析 本任务是进行数控加工及编程的最基本内容,要完成本任务,需掌握数控机床加工原理及过程、数控系统的构成,并掌握数控机床坐标系统的理论知识。技能方面需掌握数控机床坐标系的确定。
相关知识
1. 数控加工原理
数控机床(Numerical Control Machine Tool)是模具零件的主要加工设备,按照零件加工的技术要求和工艺要求,编写零件的加工程序,然后将加工程序输入到数控装置,通过数控装置控制机床的主轴运动、进给运动、更换刀具,以及工件的夹紧与松开,冷却、润滑泵的开与关,使刀具、工件和其他辅助装置严格按照加工程序规定的顺序、轨迹和参数进行工作,从而加工出符合图纸要求的零件。
数控机床是一种综合运用了计算机技术、自动控制、精密测量和机械设计等新技术的机电一体化典型产品。它的诞生标志着机械制造生产方式和制造技术发生了革命性的变革。
2. 数控系统的基本组成
数控机床一般由输入/输出设备、CNC数控装置、主轴单元、进给伺服驱动装置、可编程控制器及电气控制装置、机床本体及位置检测装置(开环机床无)等组成,如图1-1-1所示。除机床本体外的部分,统称数控系统。

图1-1-1 数控系统的基本组成
1)数控装置
数控系统一般由输入/输出装置、数控装置、驱动装置、机床电器逻辑控制装置四部分组成,机床本体为被控对象。
(1)采用计算机数控装置的数控系统称为CNC。
(2)现代数控系统的开关量控制采用PLC。
(3)FANUC 0i-C数控系统的主要部件:数控装置(显示器、数控键盘)、操作面板、伺服放大器、伺服电动机、I/O单元等。
FANUC 0i-C数控系统的部件连接:
经FANUC串行伺服总线FSSB,用一条光缆与多个进给伺服放大器(αi系列)相连。进给伺服电动机使用αis系列,最多可接4个进给轴电动机。伺服电动机上装有脉冲编码器,标配为1000000脉冲/转。编码器既用做速度反馈,又用做位置反馈。系统支持半闭环控制和使用直线尺的全闭环控制。检测器的接口有并行口(A/B相脉冲)和串行口两种。位置检测器可用增量式或绝对式。
2)输入/输出装置
开关量输入/输出装置通过输入接线端子板和继电器板,作为输入/输出接口的转接单元用,以方便连接及提高可靠性。开关量控制用于主轴启停、正反转、冷却液启停、刀架(刀库)换刀等的信号开关控制。
按下操作面板上的“循环启动”按钮后,就向CNC装置发出中断请求。一旦CNC装置所处状态符合启动条件,则CNC装置就响应中断,控制程序转入相应的控制机床运动的中断服务程序。进行插补运算,逐段计算出各轴的进给速度,插补轨迹等;并将结果输出到进给伺服控制接口及其他输出接口,控制工作台(或刀具)的位移和其他辅助动作。这样,机床就自动地按照零件加工程序的要求进行切削运动。
3. 数控加工的过程
与传统加工比较,数控加工与普通机床加工在方法与内容上有许多相似之处,不同点主要表现在控制方式上。以机械加工为例,用普通机床加工零件时,工步的安排、机床运动的先后次序、位移量、走刀路线及有关切削参数的选择等,都是由操作者自行考虑和确定的,并且采用手工操作的方式进行控制。操作者总是根据零件和工序卡的要求,在加工过程中不断改变刀具与工件的相对运动轨迹和加工参数(位置、速度等),使刀具对工件进行切削加工,从而获得合格的零件。而在CNC机床上,传统加工过程中的人工操作均被数控系统的自动控制所替代。其工作过程如图1-1-2所示,具体步骤为:

图1-1-2 数控加工过程
(1)首先阅读零件图纸,充分了解图纸的技术要求,如尺寸精度、形位公差、表面粗糙度、工件的材料、硬度、加工性能,以及工件数量等;
(2)根据零件图纸的要求进行工艺分析,其中包括零件的结构工艺性分析,材料和设计精度合理性分析,大致工艺步骤等;
(3)根据工艺分析制定出加工所需要的一切工艺信息——如加工工艺路线、工艺要求、刀具的运动轨迹、位移量、切削用量(主轴转速、进给量、吃刀深度)及辅助功能(换刀、主轴正转或反转、切削液开或关)等,并填写加工工序卡和工艺过程卡;
(4)根据零件图和制定的工艺内容,再按照所用数控系统规定的指令代码及程序格式进行数控编程;
(5)将编写好的程序通过传输接口,输入到数控机床的数控装置中,调整好机床并调用该程序后,就可以加工出符合图纸要求的零件。
4. 数控机床的坐标系统
数控机床加工时的横向、纵向等进给量都是以坐标数据来进行控制的,如数控车床、数控线切割机床等是属于两坐标控制的,数控铣床则是三坐标控制的,还有四坐标轴、五坐标轴甚至更多的坐标轴控制的加工中心机床等。
在数控编程时,为了描述机床的运动,简化程序编制的方法及保证记录数据的互换性,数控机床的坐标系和运动方向均已标准化,ISO和我国都拟定了命名的标准。
1)机床坐标系
(1)机床相对运动的规定。在机床上,我们始终认为工件静止,而刀具是运动的。这样编程人员在不考虑机床上工件与刀具具体运动的情况下,就可以依据零件图样,确定机床的加工过程。
(2)机床坐标系的规定。在数控机床上,机床的动作是由数控装置来控制的。为了确定数控机床上的成形运动和辅助运动,必须先确定机床上运动的位移和运动的方向,这就需要通过坐标系来实现,这个坐标系称为机床坐标系。
例如铣床上,有机床的纵向运动、横向运动及垂向运动,如图1-1-3所示。在数控加工中就应该用机床坐标系来描述。

图1-1-3 立式数控铣床的坐标系
标准机床坐标系中X、Y、Z坐标轴的相互关系用右手笛卡儿直角坐标系决定:伸出右手的大拇指、食指和中指,并互为90°。则大拇指代表X坐标,食指代表Y坐标,中指代表Z坐标。大拇指的指向为X坐标的正方向,食指的指向为Y坐标的正方向,中指的指向为Z坐标的正方向。围绕X、Y、Z坐标旋转的旋转坐标分别用A、B、C表示,根据右手螺旋定则,大拇指的指向为X、Y、Z坐标中任意轴的正向,则其余四指的旋转方向即为旋转坐标A、B、C的正向,如图1-1-4所示。

图1-1-4 右手笛卡儿直角坐标系
(3)坐标轴正方向的规定。增大刀具与工件距离的方向,即为各坐标轴的正方向。
2)数控机床各坐标轴方向的确定
在确定机床坐标轴时,一般先确定Z轴,然后确定X轴和Y轴,最后确定其他轴。
(1)先确定Z轴:以平行于机床主轴的刀具运动坐标为Z轴,Z轴正方向是使刀具远离工件的方向。如立铣类,主轴箱的上、下或主轴本身的上、下即可定为Z轴,且是向上为正,若主轴不能上下动作,则工作台的上、下便为Z轴,此时工作台向下运动的方向定为正向;对于卧铣类,一般是工作台离开主轴前移为+Z方向;对于卧式车床,刀架拖板远离主轴朝尾座移动为+Z方向。
(2)再确定X轴:X轴为水平方向且垂直于Z轴并平行于工件的装夹面。
对于立铣或立式加工中心,工作台往左(刀具相对向右)移动为X正向。
对于卧铣或卧式加工中心,工作台往右(刀具相对向左)移动为X正向。
对于数控车床,视刀架前后放置方式不同,其X正向也不相同,但都是由轴心沿径向朝外的,如图1-1-5所示。

图1-1-5 数控车床的坐标轴确定
(3)最后确定Y轴:在确定了X、Z轴的正方向后,即可按右手定则定出 Y轴正方向。对于立铣或立式加工中心,工作台往前(刀具相对向后)为 Y 正向,如图1-1-6所示。

图1-1-6 立式铣床的坐标轴确定
对于卧铣或卧式加工中心,主轴箱带动刀具向上移动为Y正向。
3)机床原点的设置
机床坐标系的原点是由厂家确定的,用户一般不可更改,机床原点是指在机床上设置的一个固定点,即机床坐标系的原点。它在机床装配、调试时就已确定下来,是数控机床进行加工运动的基准参考点。
(1)数控车床的原点。在数控车床上,机床原点一般取在卡盘端面与主轴中心线的交点处,如图1-1-7所示。同时,通过设置参数的方法,也可将机床原点设定在X、Z坐标的正方向极限位置上。

图1-1-7 数控车床的机床原点
(2)数控铣床的原点。在数控铣床上,机床原点一般取在X、Y、Z坐标的正方向极限位置上,如图1-1-8所示。

图1-1-8 铣床的机床原点
4)机床参考点
机床参考点是用于对机床运动进行检测和控制的固定位置点。
机床参考点是机床上的一个固定点,用于对机床工作台、滑板与刀具相对运动的测量系统进行标定和控制。其位置由机械挡块或行程开关来确定。机床参考点对机床原点的坐标是一个已知定值,也就是说,可以根据机床参考点在机床坐标系中的坐标值间接确定机床原点的位置。在机床接通电源后,通常都要做回零操作,使刀具或工作台退离到机床参考点。当回零操作完成后,显示器即显示出机床参考点在机床坐标系中的坐标值,表明机床坐标系已自动建立。可以说回零操作是对基准的重新核定,可消除由于种种原因产生的基准偏差。机床参考点已由机床制造厂测定后输入数控系统,并且记录在机床说明书中,用户不得更改。
一般数控车床、数控铣床的机床原点和机床参考点位置如图1-1-7和图1-1-8所示,也有些数控机床的机床原点与机床参考点重合。
数控机床开机时,必须先确定机床原点,而确定机床原点的运动就是刀架返回参考点的操作,这样通过确认参考点,就确定了机床原点。只有机床参考点被确认后,刀具(或工作台)移动才有基准。
任务巩固
通过课后阅读,了解数控加工原理与数控系统的基本组成,掌握数控机床的基本结构组成和零件从编程到数控加工的大致过程。在数控机床上练习机床坐标系的确定。
任务1.1.2 数控机床类型识别
任务描述 根据所加工的内容,正确选择数控加工。
任务分析 选择合适的加工机床类型,是数控加工工艺编制的第一步,完成该任务,需了解数控机床多轴联动加工和伺服系统控制方式。
相关知识
1. 按轮廓加工控制的坐标轴数分类
1)两轴联动数控机床
同时可以控制两个轴,但数控机床可以多于两个轴;如机床有X、Y、Z三个坐标,则两轴联动可以同时控制其中两个。如图1-1-9所示的加工直线型母线曲面轮廓,只要同时控制X、Y坐标即可。

图1-1-9 两轴联动
2)两轴半联动数控机床
用于三轴及以上的数控机床,但控制装置只能同时控制两个坐标,而第三个坐标只能做等距周期移动,如X、Y坐标联动,另一个轴(Z坐标)做周期性间歇进给。如图1-1-10所示的用行切法在数控铣床上加工三维曲面,数控装置在ZOX坐标平面内控制X、Z两坐标联动来加工垂直面内的轮廓表面,Y坐标做定期等距移动,即可加工出零件的空间曲面。

图1-1-10 两轴半联动
3)三轴联动数控机床
三轴联动即X、Y、Z三个直线坐标方向的联动,或除同时控制其中两个直线坐标的联动外,还同时控制围绕某一坐标轴旋转的旋转坐标。例如,在数控铣床或加工中心上用球头铣刀加工如图1-1-11所示的三维曲面。

图1-1-11 三轴联动
4)四轴联动数控机床
四轴联动是同时控制X、Y、Z三个直线坐标及某一旋转坐标的联动,用来加工叶轮或圆柱凸轮。如图1-1-12所示为同时控制X、Y、Z坐标与工作台绕Y轴旋转(B坐标)的四轴联动。

图1-1-12 四轴联动
5)五轴联动数控机床
同时控制X、Y、Z三个直线坐标及两个旋转坐标(A、B、C三个旋转坐标中的任意两个)的联动为五轴联动。这样,刀具可以向空间的任意方向进给加工。如加工图1-1-13所示的两种空间曲面,控制刀具同时绕X轴和Y轴两个方向摆动,使刀具切削方向保持与加工曲面的切平面重合,提高被加工表面的加工精度。五轴联动加工特别适合各种复杂的空间曲面。

图1-1-13 五轴联动
2. 按数控机床加工原理分类
按数控机床加工原理可把数控机床分为普通数控机床和特种加工数控机床。
1)普通数控机床
如数控车床、数控铣床、加工中心、车削中心等各种普通数控机床,其加工原理是用切削刀具对零件进行切削加工。
2)特种加工数控机床
如线切割数控机床,对硬度很高的工件进行切割加工;如电火花成形加工数控机床,采用电火花原理对工件的型腔进行加工。
3. 按数控机床运动轨迹分类
数控机床运动轨迹主要有三种形式:点位控制运动、直线控制运动和连续控制运动。
1)点位控制运动
点位控制运动指刀具相对工件的点定位,一般对刀具运动轨迹无特殊要求,为提高生产效率和保证定位精度,机床设定快速进给,临近终点时自动降速,从而减小运动部件因惯性而引起的定位误差。
2)直线控制运动
直线控制运动指刀具或工作台以给定的速度按直线运动。
3)连续控制运动
连续控制运动也称为轮廓控制运动,指刀具或工作台按工件的轮廓轨迹运动,运动轨迹为任意方向的直线、圆弧、抛物线或其他函数关系的曲线。这种数控系统有一个轨迹插补器,根据运动轨迹和速度精确计算并控制各个伺服电动机沿轨迹运动。
4. 按进给伺服系统控制方式分类
由数控装置发出脉冲或电压信号,通过伺服系统控制机床各运动部件运动。数控机床按进给伺服系统控制方式分类有开环控制系统、闭环控制系统和半闭环控制系统三种形式。
1)开环控制系统
这种控制系统采用步进电动机,无位置测量元件,输入数据经过数控系统运算,输出指令脉冲控制步进电动机工作,如图1-1-14所示。这种控制方式对执行机构不检测,无反馈控制信号,因此称为开环控制系统。开环控制系统的设备成本低,调试方便,操作简单,但控制精度低,工作速度受到步进电动机的限制。

图1-1-14 开环控制系统
2)闭环控制系统
这种控制系统绝大多数采用伺服电动机,有位置测量元件和位置比较电路。如图1-1-15所示,测量元件安装在工作台上,测出工作台的实际位移值反馈给数控装置。位置比较电路将测量元件反馈的工作台实际位移值与指令的位移值相比较,用比较的误差值控制伺服电动机工作,直至到达实际位置,误差值消除,因此称为闭环控制。闭环控制系统的控制精度高,但要求机床的刚性好,对机床的加工、装配要求高,调试较复杂,而且设备的成本高。

图1-1-15 闭环控制系统
3)半闭环控制系统
如图1-1-16所示,这种控制系统的位置测量元件不是测量工作台的实际位置,而是测量伺服电动机的转角,经过推算得出工作台位移值,反馈至位置比较电路,与指令中的位移值相比较,用比较的误差值控制伺服电动机工作。这种用推算方法间接测量工作台位移,不能补偿数控机床传动链零件的误差,因此称为半闭环控制系统。半闭环控制系统的控制精度高于开环控制系统,调试比闭环控制系统容易,设备的成本介于开环与闭环控制系统之间。

图1-1-16 半闭环控制系统
任务巩固
通过对车间内不同数控机床的观察,练习对各种数控机床进行分类。