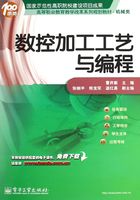
任务一 外圆柱面Ⅰ数控加工程序的编制
一、项目任务书
外圆柱面数控加工程序的编制项目任务书,见表1-1。
表1-1 项目任务书

二、学习导读
1.数控编程的内容
数控编程的内容主要包括分析图样并确定加工工艺过程、数值计算、编写零件加工程序、程序输入、程序校验和试切削。
(1)分析图样并确定加工工艺过程:分析图样,根据零件的材料、形状、尺寸、精度、毛坯形状和热处理要求等确定加工方案,选择合适的数控机床。然后确定加工工艺过程,主要考虑:确定加工方案,刀具、工夹具的设计和选择,选择对刀点,确定加工路线,确定切削用量等。
(2)数值计算:按已确定的加工路线和允许的零件加工误差,计算出所需的输入数控装置的数据。其主要内容是在规定的坐标系内计算零件轮廓和刀具运动的轨迹的坐标值。
(3)编写零件加工程序:根据所使用数控系统的指令、程序段格式,逐段编写零件加工程序。
(4)程序输入:将编制好的程序单上的内容输入至数控装置中。
(5)程序校验和试切削:通常采用空走刀校验、空运转画图校验等。
2.加工程序段的构成
数控加工程序的编制方法主要有两种:手工编程和自动编程。
手工编程指主要由人工来完成数控编程中各个阶段的工作。一般对几何形状不太复杂的零件,所需的加工程序不长,计算比较简单,用手工编程比较合适。
手工编程的特点是耗费时间较长,容易出现错误,无法胜任复杂形状零件的编程。据国外资料统计,当采用手工编程时,一段程序的编写时间与其在机床上运行加工的实际时间之比,平均约为 30∶1,而数控机床不能开动的原因中有 20%~30%是由于加工程序编制困难、编程时间较长造成的。
在数控装置中,程序的记录是由程序号来辨别的,调用某个程序可通过程序号来调出,编辑程序也要首先调出程序号。程序号由 4 位数(1~9999)表示。程序编号方式为O××××,可以在程序编号的后面注上程序的名字并用括号括起。程序名可用 16 位字符表示,要求有利于理解。程序编号要单独使用一个程序段。
程序段主要是由程序段序号和各种功能指令构成的:
N__ G__ X(U)__ Z(W)__ F__ M__ S__ T__;
其中 N——程序段序号;
G——准备功能;
X(U),Z(W)——工件坐标系中X、Z轴移动至终点的位置,X、Z为绝对坐标, U、W为相对坐标,X、Z与U、W在一个程序段内可以混用;
F——进给功能指令;
M——辅助功能指令;
S——主轴功能指令;
T——刀具功能指令。
3.加工程序的构成
一个完整的加工程序由若干程序段构成,程序的开头是程序名,结束时写有程序结束指令。例如:
O0001;//程序名 N10 G92 X0 Y0 Z200.0; N20 G90 G00 X50.0 Y60.0 S300 M03; N30 G01 X10.0 Y50.0 F150 ; …… N110 M30;//程序结束指令
其中第一个程序段“O0001”是整个程序的程序号,也叫程序名,由地址码O和四位数字组成。每一个独立的程序都应有程序号,它可作为识别、调用该程序的标志。不同的数控系统,程序号地址码可不相同,如 FANUC 系统用 O,AB8400 系统用 P,而西门子系统用%。编程时应根据说明书的规定使用,否则系统将不接受。每个程序段以程序段号“N××××”开头,用“;”表示程序段结束(有的系统用 LF、CR 等符号表示),每个程序段中有若干个指令字,每个指令字表示一种功能,所以也称功能字。功能字的开头是英文字母,其后是数字,如G90、G01、X100.0等。一个程序段表示一个完整的加工工步或加工动作。
一个程序的最大长度取决于数控系统中零件程序存储区的容量。现代数控系统的存储区容量已足够大,一般情况下已足够使用。一个程序段的字符数也有一定的限制,如某些数控系统规定一个程序段的字符数≤90 个,一旦大于限定的字符数,就把它分成两个或多个程序段。
4.指令应用举例
(1)快速点定位(G00)指令应用举例
快速点定位指令格式:
G00 X__ Z__ ; G00 U__ W__ ;
其中,(X,Z)、(U,W)为定位点坐标。
【例1-1】 如图1-1所示刀具快速点定位(快速进刀)运动(动作)编程如下:

图1-1 刀具快速点定位
G00 X50.0 Z6.0; 或 G00 U-70.0 W-84.0;
G00指令要求刀具以点位控制方式从刀具所在位置以最快的速度移动到指定位置。它只实现快速移动,并保证在指定的位置停止,在移动时对运动轨迹与运动速度并没有严格的精度要求。如果两坐标轴的脉冲当量和最大速度相等,则运动轨迹是一条 45°斜线;如果是一条非45°斜线,则刀具的运动轨迹可能是一条折线。
使用G00时,应注意以下几点。
① G00是模态指令。例如,由A点到B点实现快速点定位时,因前面程序段已设定了G00,所以后面程序段就可不再重复设定定义G00,只写出坐标值即可。
② 快速点定位移动速度不能用程序指令设定。其速度已由生产厂家预先调定或由引导程序确定。若在快速点定位程序段前设定了进给速度F,则该指令对G00程序段无效。
③ 快速点定位指令G00的执行过程是,刀具由程序起始点开始加速移动至最大速度,然后保持快速移动,最后减速到达终点,实现快速点定位,这样可以提高数控机床的定位精度。
(2)直线插补(G01)指令应用举例
直线插补也称直线切削,其特点是刀具以直线插补运算联动方式由某坐标点移动到另一坐标点,移动速度是由进给功能指令 F 设定的。当机床执行 G01 指令时,在该程序段中必须含有F指令。G01和F都是模态指令。
直线插补指令格式:
G01 X___ Z__ F__ ; G01 U__ W__ F__ ;
其中 (X,Z)、(U,W)——直线终点坐标;
F——进给指令,单位为mm/r(毫米/转)。
该指令用于直线或斜线运动,可沿X轴、Z轴方向执行单轴运动,也可沿XZ平面内任意斜率的直线运动。
【例1-2】 如图1-2所示外圆柱切削的编程如下:

图1-2 外圆柱切削
G01 X60.0 Z-80.0 F0.3; 或 G01 U0 W-80.0 F0.3;
5.阶梯轴的形式与车削
阶梯轴可分为低台阶轴和高台阶轴两种形式。与其相对应,阶梯轴的车削方法有低台阶车削法和高台阶车削法两种。当相邻两圆柱体直径差较小时,该阶梯轴为低台阶轴,可由车刀一次切出,如图1-3(a)所示,其加工路线为A→B→C→D→E,这就是低台阶车削法;当相邻两圆柱体直径差较大时,该阶梯轴为高台阶轴,需要采用分层切削,如图 1-3(b)所示,粗加工路线为 A1→B1,A2→B2、A3→B3,精加工路线为 A→B→C→D→E,这就是高台阶车削法。

图1-3 阶梯轴车削方法
切削用量的具体数值可参阅机床说明书、切削用量手册,并结合实际经验而定,表 1-2是参考了切削用量手册而推荐的切削用量参考表。
各种加工方法所能达到的表面粗糙度数值见表1-3,供制定加工工艺时参考选用。
表1-3 各种加工方法所能达到的表面粗糙度数值

注:① 实线为平常使用,虚线为不常使用;
② 表中最后一栏为平常使用的值与表面光洁度等级的大致对应关系。
三、任务解析
该零件由不同的外圆柱面组成,有一定的尺寸精度和表面粗糙度要求。零件材料为 45钢,切削加工性能较好,无热处理和硬度要求。
加工工艺路线:装夹→对刀→设置编程原点为零件右端面中心→粗车φ46、φ43、φ40 外圆→留1mm精车余量→精车φ40、φ43、φ46各段外圆及端面至要求尺寸。
编程过程中对具有公差的尺寸计算如下:

同理,φ 43外圆编程尺寸=42.969mm
φ40外圆编程尺寸=39.969mm

同理,40、72长度编程尺寸均为原值。
四、任务实施(零件加工工艺分析与编程)
1.工装
采用三爪自定心卡盘夹紧零件毛坯的外圆周面。
2.刀具选择
选用硬质合金90°偏刀,置于T01号刀位,数控加工刀具卡片见表1-4。
表1-4 数控加工刀具卡片

3.制作加工工艺卡
阶梯轴Ⅰ加工工步及切削用量列于加工工艺卡中,见表1-5。
表1-5 阶梯轴Ⅰ加工工艺卡

4.程序编制
阶梯轴Ⅰ数控加工程序清单见表1-6。
表1-6 阶梯轴Ⅰ数控加工程序清单

五、任务学习手记(见表1-7)
表1-7 任务学习手记
