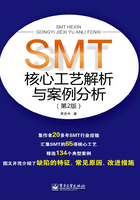
上篇 表面组装核心工艺解析
第1章 表面组装基础知识
1.1 SMT概述
1.1 SMT概述(1)
SMT概述
表面组装技术,英文名称为Surface Mount Technology,缩写为SMT,是一种将表面组装元器件(SMD)安装到印制电路板(PCB)上的板级组装技术,它是现代电子组装技术的核心,如图1-1为采用SMT制造的印制板组件。

图1-1 表面组装印制板组件
表面组装技术,在电子工程业界,也称之为“表面安装技术”、“表面组装技术”。它最早起源于20世纪60年代的厚膜电路外贴元件技术,在20世纪80年代随着彩色电视机电子调谐器的大规模生产而得到迅速发展,到了20 世纪90年代中期基本成熟,成为现代主流的电子组装技术。
1.SMT的优势
相对于THT(插装技术),SMT带给电子产品四大优势:
(1)高密度。由于表面组装元器件采用了无引线或短引线、I/O端面阵布局等封装技术,元器件的尺寸大大减小,I/O引出端大大增加,从而使PCB的组装密度得到大幅度的提高。
(2)高性能。表面组装元器件的无引线或短引线特点,降低了引线的寄生电感和电容,提高了电路的高频高速性能以及器件的散热效率。
(3)低成本。由于表面组装元器件封装的标准化和无孔安装特点,特别适合自动化组装,大幅度降低了制造成本。
(4)高可靠性。自动化的生产技术,保证了每个焊点的可靠连接,从而提高了电子产品的可靠性。
正是由于SMT的这四大优势,促进了其广泛应用,反过来也推动了SMT本身的不断发展。
2.SMT的技术组成
SMT是一个系统工程技术,包括工艺技术、工艺设备、工艺材料与检测技术,如图1-2所示。

图1-2 SMT的组成
需要指出的是,虽然我们把SMD与PCB分别作为表面组装的对象和基板看待,但SMD的封装结构、PCB的制造质量,是与表面组装的直通率有直接紧密的相关性的。从控制SMT焊接质量的角度出发,广义上的SMT,应该包括电子元器件的封装技术和PCB的制造技术,这也是很多有关SMT的专著把电子元器件的封装技术和PCB的制造技术列为其中内容的原因。
1.1 SMT概述(2)
SMT概述
3.SMT的核心
俗话讲“内行看门道,外行看热闹”。就SMT来讲,技术核心是什么?是设备还是工艺?在国内的学术交流会上,大家讨论最多的往往是设备,比的也是设备;其实,设备只是实现工艺的手段而已,真正核心的是工艺,它是实现高品质生产的保证。
SMT工作的目标是制造合格的焊点,良好焊点的形成有赖于合适的焊盘设计、合适的焊膏量、合适的再流焊接温度曲线,这些都是工艺条件。使用同样的设备,有些厂家焊接的直通率比较高,有些却比较低,差别就是工艺不同,它体现在“科学化、精细化、规范化”上,比如,钢网厚度与开窗的设计、印刷的支撑与参数调整、贴片的程序设定、温度曲线的设置以及进炉间隔、装配时的工装配备情况等,这些往往需要企业花很长的时间探索、积累并规范化,而这些经过验证并固化的技术文件、工艺方法、工装设计就是“工艺”,就是SMT的核心。
1.2表面组装基本工艺流程
基本工艺流程类型
表面组装印制电路板组件(Print Circiut Board Assembly,PCBA)的焊接,主要有再流焊接和波峰焊接两种工艺,它们构成了SMT组装的基本工艺流程。
1.再流焊接工艺流程
再流焊接是指通过熔化预先印刷在PCB焊盘上的焊膏,实现表面组装元器件焊端或引脚与PCB焊盘之间机械和电器连接的一种软钎焊工艺。
1)工艺特点
(1)焊料(以焊膏形式)的施加与加热分开进行,焊点大小可控;
(2)焊膏通过印刷的方式分配,每个焊接面一般只采用一张钢网进行焊膏印刷;
(3)再流焊炉主要的功能就是对焊膏进行加热,它是对置于炉内的PCBA整体加热,在进行第二次焊接时,第一次焊接好的焊点会重新熔化。
2)工艺流程
印刷焊膏→贴片→再流焊接,如图1-3所示。

图1-3 再流焊接工艺流程
2.波峰焊接工艺流程
波峰焊接是指将熔化的软钎焊料(含锡的焊料),经过机械泵或电磁泵喷流成焊料波峰,使预先装有元器件的PCB通过焊料波峰,实现元器件焊端或引脚与PCB插孔/焊盘之间机械和电器连接的一种软钎焊接工艺。
1)工艺特点
(1)对PCB施加焊料与热量。
(2)热量的施加主要通过熔化的焊料传导,施加到PCB上的热量大小主要取决于熔融焊料的温度和熔融焊料与PCB的接触时间(焊接时间)。
(3)焊点的大小、填充性主要取决于焊盘的设计、孔与引线的安装间隙。换句话说,就是波峰焊接焊点的大小主要取决于设计。
(4)焊接SMD,存在“遮蔽效应”,容易发生漏焊现象。所谓“遮蔽效应”,是指片式SMD的封装体阻碍焊料波接触到焊盘/焊端的现象。
2)工艺流程
点胶→贴片→固化→波峰焊接,如图1-4所示。

图1-4 波峰焊接工艺流程
1.3 PCBA组装流程设计
1.3 PCBA组装流程设计(1)
PCBA组装流程设计方式
PCBA的组装流程设计决定了PCBA正反面元器件的布局,主要布局设计如图1-5~图1-9所示。

图1-5 双面SMD布局设计

图1-9 底面采用移动喷嘴选择性波峰焊接的布局设计
1.全SMD布局设计
随着元器件封装技术的发展,基本上各类元器件都可以用表面组装封装,因此,尽可能采用全SMD设计,有利于简化工艺和提高组装密度。
根据元器件数量以及设计要求,可以设计为单面全SMD或双面全SMD布局(见图1-5)。对于双面全SMD布局,布局在底面的元器件应该满足顶面焊接时不会掉下来的最基本要求。
装配工艺流程如下。
(1)底面:印刷焊膏→贴片→再流焊接。
(2)顶面:印刷焊膏→贴片→再流焊接。
之所以先焊接底面,是因为一般底面上所布局的SMD考虑到了不能掉下来的焊接要求。
2.顶面混装,底面SMD布局设计
这是目前常见的布局形式,根据插装元器件的焊接方法,可以细分为三类布局,即波峰焊接、托盘选择性波峰焊接和移动喷嘴选择性波峰焊接或手工焊接。由于焊接工艺不同,设计要求略有不同。
1)底面采用波峰焊接的布局设计
底面采用波峰焊接的布局设计如图1-6所示,这类布局适合复杂表面组装元器件(不适合波峰焊接的SMD)可以在一面布局下的情况。

图1-6 底面采用波峰焊接的布局设计
底面一般只能够用波峰焊接的封装,如0603~1206范围内的片式元件、引线间距大于等于1mm的SOP等。
波峰焊接的布局设计,其上的SMD必须先点胶固定。采用的装配工艺流程如下:
(1)顶面:印刷焊膏→贴片→再流焊接。
(2)底面:点胶→贴片→固化。
(3)顶面:插件。
(4)底面:波峰焊接。
之所以先焊接顶面,一方面,因为裸的PCB在焊接前比较平整;另一方面,因为底面胶的固化温度比较低(≤150℃),不会对顶面上已经焊接好的元件构成不良影响。
1.3 PCBA组装流程设计(2)
PCBA组装流程设计方式
2)底面采用托盘选择性波峰焊接的布局设计
底面采用托盘选择性波峰焊接的布局设计如图1-7所示,这类布局适合SMD数量多、一面布局不下,又有不少插装元器件的情况。

图1-7 底面采用托盘选择性波峰焊接的布局设计
底面布局要求比较多,一是SMD元件不能太高;二是波峰焊接元器件与托盘保护的SMD之间的间隔要满足工装、温度的设计要求。
托盘选择性波峰焊接的布局设计,其装配工艺流程如下:
(1)底面:印刷焊膏→贴片→再流焊接。
(2)顶面:印刷焊膏→贴片→再流焊接。
(3)顶面:插件。
(4)底面:加托盘波峰焊接,如图1-8所示。

图1-8 托盘
3)底面采用移动喷嘴选择性波峰焊接的布局设计
底面采用移动喷嘴选择性波峰焊接的布局设计如图1-9 所示,这类布局适合SMD数量多、一面布局不下,只有少数插装元器件的情况。
底面布局与双面全SMD基本一样,只要插装引脚与周围元器件的间隔满足喷嘴焊接要求即可。
底面采用移动喷嘴选择性波峰焊接的布局设计,其装配工艺流程如下:
(1)底面:印刷焊膏→贴片→再流焊接。
(2)顶面:印刷焊膏→贴片→再流焊接。
(3)底面:移动喷嘴选择性波峰焊接。
1.4 表面组装元器件的封装形式
1.4表面组装元器件的封装形式(1)
表面组装元器件的封装形式分类
表面组装元器件(SMD)的封装是表面组装的对象,认识SMD的封装结构,对优化SMT工艺具有重要意义。
SMD的封装结构是工艺设计的基础,因此,在这里我们不按封装的名称而是按引脚或焊端的结构形式来进行分类。按照这样的分法,SMD的封装主要有片式元件(Chip)类、J形引脚类、L形引脚类、BGA类、BTC类、城堡类,如图1-10所示。

图1-10 SMD的封装形式分类
片式元件类封装
1.范围
片式元件类一般是指形状规则、两引出端的片式元件,主要有片式电阻、片式电容和片式电感,如图1-11所示。

图1-11 片式元件类常见封装
1.4表面组装元器件的封装形式(2)
片式元件类封装
2.耐焊接性
根据PCBA组装可能的最大焊接次数以及IPC/J-STD-020的有关要求,一般片式元件具备以下的耐焊接性:
1)有铅工艺
(1)能够承受5次标准有铅再流焊接,温度曲线参见IPC/J-STD-020D。
(2)能够承受在260℃熔融焊锡中10s以上的一次浸焊过程。
2)无铅工艺
(1)能够承受3次标准有铅再流焊接,温度曲线参见IPC/J-STD-020D。
(2)能够承受在260℃熔融焊锡中10s以上的一次浸焊过程。
3.工艺特点
片式电阻/电容的封装比较规范,有英制和公制两种表示方法。在业内多使用英制,这主要与行业习惯有关。
常用片式电阻/电容的封装代号与对应尺寸,见表1-1。
表1-1 常用片式电阻/电容的封装代号与对应尺寸(单位:mm)

0603及以上尺寸的封装工艺性良好,正常工艺条件下,很少有焊接问题;0402及以下尺寸的封装,工艺性稍差,一般容易出现立碑、翻转等不良现象。
1.4表面组装元器件的封装形式(3)
J形引脚类封装
1.范围
J形引脚类封装(J-lead),是SMT早期出现的一类封装形式,包括SOJ、PLCCR、PLCC,如图1-12所示。

图1-12 J形引脚类常见封装
2.耐焊接性
J形引脚类封装耐焊接性比较好,一般具备以下的耐焊接性。
1)有铅工艺
能够承受5次标准有铅再流焊接,温度曲线参见IPC/J-STD-020D。
2)无铅工艺
能够承受3次标准有铅再流焊接,温度曲线参见IPC/J-STD-020D。
3.工艺特点
(1)引脚间距为1.27mm。
(2)J形引脚类封装引线引线间距大且不容易变形,一般工艺水准下,都不会出现焊接不良问题,具有非常好的工艺性。
(3)不足之处就是封装尺寸大,I/O数受限制。
L形引脚类封装
1.范围
L形引脚,也称鸥翼形引脚(Gull-wing lead),此类封装有很多种,主要有SOIC、BQFP、QFP、SQFP和QFPR、TSSOP,如图1-13所示。之所以种类复杂,是因为它们源自不同的标准,如IPC、EIAJ、JEDEC,从工艺的角度我们可以简单地把它归为SOP、QFP两类。

图1-13 L形引脚类常见封装
1.4表面组装元器件的封装形式(4)
L形引脚类封装
2.耐焊接性
L形引脚类封装耐焊接性比较好,一般具备以下的耐焊接性。
1)有铅工艺
能够承受5次焊接峰值温度为235℃、225℃以上最少持续30s的再流焊接过程。
2)无铅工艺
能够承受3次焊接峰值温度为260℃、250℃以上最少持续30s的再流焊接过程。
3.工艺特点
(1)引脚间距形成标准系列,如1.27mm、0.80mm、0.65mm、0.635mm、0.50mm、0.40mm、0.30mm。其中1.27mm只出现在SOIC封装上,0.635mm只出现在BQFP封装上。
(2)L引脚类封装全为塑封器件,容易吸潮,使用前需要确认吸潮是否超标。如果吸潮超标,应进行干燥处理。
(3)0.65mm及以下引脚间距的封装引脚比较细,容易变形。因此,在配送、写片等环节,应小心操作,以免引脚变形而导致焊接不良。如不小心,掉到地上,捡起来后应进行引脚共面度和间距的检查与矫正。
(4)0.40mm及其以下引脚间距的封装,对焊膏量非常敏感,稍多可能桥连,稍少又可能开焊。因此,在应用0.40mm及其以下引脚间距的封装时,必须确保稳定、合适的焊膏量。
BGA类封装
1.范围
BGA类封装(Ball Grid Array),按其结构划分,主要有塑封BGA(P-BGA)、倒装BGA(F-BGA)、载带BGA(T-BGA)和陶瓷BGA(C-BGA)四大类,如图1-14所示。

图1-14 BGA类的封装形式

图1-14 BGA类的封装形式(续)
1.4表面组装元器件的封装形式(5)
BGA类封装
2.工艺特点
(1)BGA引脚(焊球)位于封装体下,肉眼无法直接观察到焊接情况,必须采用X光设备才能检查。
(2)BGA属于湿敏器件,如果吸潮,容易发生“爆米花”、变形等焊接缺陷或不良,因此,组装前必须确认是否符合工艺要求。
(3)BGA也属于应力敏感器件,四角焊点应力集中,在机械应力作用下很容易被拉断,因此,在PCB设计时应尽可能将其布放在远离拼板边和安装螺钉的地方。
总体而言,焊接的工艺性比较好,但有许多特有的焊接问题,详细参见IPC-7095。
BTC类封装
1.范围
BTC,即Bottom Termination Surface Mount Component的缩写,可翻译为底部焊端器件,它是比较新的一类封装,其特点是外面的连接端与封装体内的金属(也可以看做引线框架)是一体化的,如图1-15所示,具体封装名称很多,但实际上为两大类,即周边方形焊盘布局和面阵圆形焊盘布局。

图1-15 BTC类封装的特点
1.4表面组装元器件的封装形式(6)
BTC类封装
在IPC-7093中列出的BTC类封装形式有QFN(Quad Flat No-Lead package)、SON(Small Outline No-Lead)、DFN(Dual Flat No-Lead)、LGA(land Grid Array)、MLFP(Micro Leadframe Package),如图1-16所示。

图1-16 BTC类的封装形式
2.工艺特点
(1)BTC的焊端为面,与PCB焊盘形成的焊点为“面-面”连接。
(2)BTC类封装的工艺性比较差,换句话讲,就是焊接难度比较大,经常发生的问题为焊缝中有空洞、周边焊点虚焊或桥连。
这些问题产生的原因主要有两个:一是封装体与PCB之间间隙过小,贴片时焊膏容易挤连,焊接时焊剂中的溶剂挥发通道不畅通;二是热沉焊盘与I/O焊盘面积相差悬殊,I/O焊盘上焊膏沉积率低时,容易发生“元件托举”现象即热沿焊盘上熔融焊料将元件浮起的现象。经验表明,确保I/O焊盘上焊膏合适转移比减少热沉焊盘上的焊膏量更有效。
1.5 印制电路板制造工艺
1.5印制电路板制造工艺(1)
PCB概述
PCB,即Printed Circuit Board的缩写,中文译为印制电路板,它包括刚性、挠性和刚-挠结合的单面、双面和多层印制板,如图1-17所示。

图1-17 PCB的类别
PCB为电子产品最重要的基础部件,用做电子元件的互连与安装基板,如图1-18所示。

图1-18 PCB的作用
不同类别的PCB,其制造工艺也不尽相同,但基本原理与方法却大致一样,如电镀、蚀刻、阻焊等工艺方法都要用到。在所有种类的PCB中,刚性多层PCB应用最广,其制造工艺方法与流程最具代表性,也是其他类别PCB制造工艺的基础。了解PCB的制造工艺方法与流程,掌握基本的PCB制造工艺能力,是做好PCB可制造性设计的基础。
本节内容,我们将简单介绍传统刚性多层PCB和高密度互连PCB的制造方法与流程以及基本工艺能力。
1.5印制电路板制造工艺(2)
刚性多层PCB
刚性多层PCB是目前绝大部分电子产品使用的PCB,其制造工艺具有一定的代表性,也是HDI板、挠性板、刚-挠结合板的工艺基础。
1)工艺流程
刚性多层PCB制造流程如图1-19所示,可以简单分为内层板制造、叠层/层压、钻孔/电镀/外层线路制作、阻焊/表面处理四个阶段,详细如图1-20~图1-23所示。

图1-19 刚性多层PCB制造流程

图1-20 内层板制作工艺方法与流程

图1-23 阻焊/表面处理工艺方法与流程
阶段一:内层板制作工艺方法与流程如图1-20所示。
1.5印制电路板制造工艺(3)
刚性多层PCB
阶段二:叠层/层压工艺方法与流程如图1-21所示。

图1-21 叠层/层压工艺方法与流程
阶段三:钻孔/电镀/外层线路制作工艺方法与流程如图1-22所示。

图1-22 钻孔/电镀/外层线路制作工艺方法与流程
1.5印制电路板制造工艺(4)
刚性多层PCB
阶段四:阻焊/表面处理工艺方法与流程如图1-23所示。
2)工艺能力
刚性多层板的工艺能力源于厂家,包括一般加工能力与加工精度。
(1)最大层数:40。
(2)PCB尺寸:584mm×1041mm。
(3)最大铜厚:外层4OZ,内层4OZ。
(4)最小铜厚:外层1/2OZ,内层1/3OZ。
(5)最小线宽/线距:0.10mm/0.10mm。
(6)最小钻孔孔径:0.25mm。
(7)最小金属化孔孔径:0.20mm。
(7)最小孔环宽度:0.125mm。
(8)最小阻焊间隙与宽度:0.75mm/0.75mm。
(9)最小字符线宽:0.15mm。
(10)外形公差:±0.10mm(与尺寸有关)。
1.5印制电路板制造工艺(5)
HDI板
随着0.8mm及其以下引线中心距BGA、BTC类元器件的使用,传统的层压印制电路制造工艺已经不能适应微细间距元件的应用需要,从而开发了高密度互连(HDI)电路板制造技术。
所谓HDI板,一般是指线宽/线距小于等于0.10mm、微导通孔径小于等于0.15mm的PCB。
在传统的多层板工艺中,所有层一次性堆叠成一块PCB,采用贯通导通孔进行层间连接,而在HDI板工艺中,导体层与绝缘层是逐层积层,导体间是通过微埋/盲孔进行连接的。因而,一般把HDI板工艺称为积层工艺(BUP,Build-up Process或BUM,Build-up Mutiplayer)。根据微埋/盲孔导通的方法来分,还可以进一步细分为电镀孔积层工艺和应用导电膏积层工艺(如ALIVH工艺和B2IT工艺)。
1.HDI板的结构
HDI板的典型结构是“N+C+N”,其中“N”表示积层层数,“C”表示芯板,如图1-24所示。随着互连密度的提高,全积层结构(也称任意层互连)也开始使用。

图1-24 积层工艺HDI板的结构
2.电镀孔工艺
在HDI板的工艺中,电镀孔工艺是主流的一种,几乎占HDI板市场的95%以上。它本身也在不断发展中,从早期的传统孔电镀到填孔电镀,HDI板的设计自由度得到很大提高,如图1-25所示。

图1-25 HDI板的发展路线图
1.5印制电路板制造工艺(6)
HDI板
1)工艺流程
电镀孔积层工艺核心流程如图1-26所示。

图1-26 电镀孔积层工艺核心流程
2)工艺能力
电镀孔积层板的设计,主要考虑积层的层数以及埋孔、微盲孔的结构和微盲孔的尺寸。设计要求比较多,在此不详细说明,仅举例说明。
(1)微盲孔的结构至少有12 种,比如“二阶微孔+次外层机械埋孔”,设计时请参考有关标准,如IPC-2226(高密度互连印制板设计规范)、IPC-2315(高密度互连与微导通孔设计导则)等。
(2)积层介质厚度(h):40~80μm(决定了微盲孔的直径)。
(3)微盲孔尺寸(见图1-27)。

图1-27 微盲孔结构与尺寸说明
微盲孔孔径(B):≥0.10mm,一般取0.125mm。
微盲孔孔盘直径(A):≥0.30mm。
微盲孔捕获盘直径(C):≥0.30mm。
1.5印制电路板制造工艺(7)
HDI板
3.ALIVH工艺
此工艺为松下公司开发的全积层结构的多层PCB制造工艺,是一种应用导电胶的积层工艺,称为任意层填隙式导通互连技术(Any Layer Interstitial Via Hole,ALIVH),它意味着积层的任意层间互连全由埋/盲导通孔来实现。工艺的核心是导电胶填孔。
ALIVH工艺特点:
1)使用无纺芳酰胺纤维环氧树脂半固化片为基材;
2)采用CO2激光形成导通孔,并用导电膏填充导通孔。
ALIVH工艺流程如图1-28所示。

图1-28 ALIVH工艺流程
4.B2IT工艺
此工艺为东芝公司开发的积层多层板制造工艺,这种工艺称为埋入凸块互连技术(Buried Bump Interconnection Techonology,B2IT)。工艺的核心是应用导电膏制成的凸块。
B2IT工艺流程如图1-29所示。

图1-29 B2IT工艺流程
1.6 表面组装工艺控制关键点
SMT关键控制点
据统计,名列PCBA焊接不良前五位的是虚焊、桥连、少锡、移位和多余物,而这些不良现象的产生在很大程度上与焊膏印刷、钢网设计、焊盘设计以及温度曲线设置有关,也就是与工艺有关。如果说提升SMT的终极目标是为了获得优质焊点的话,那么就可以说工艺是SMT的核心。
SMT工艺,按照业务划分,一般可分为工艺设计、工艺试制和工艺控制,如图1-30所示,其核心目标是通过合适焊膏量的设计与一致的印刷沉积,减少开焊、桥连、少锡和移位,从而获得预期的焊点质量。

图1-30 工艺控制点
在每项业务中,有一组工艺控制点,其中焊盘设计、钢网设计、焊膏印刷与PCB的支撑,是工艺控制的关键点。
随着元器件焊盘以及间隔尺寸的不断缩小,钢网开窗的面积比以及钢网与PCB印刷时的间隙越来越重要。前者关系到焊膏的转移率,而后者关系到焊膏印刷量的一致性以及印刷的良好率。
为了获得75%以上的焊膏转移率,根据经验,一般要求钢网开窗与侧壁的面积比大于等于0.66;要获得符合设计预期的、稳定的焊膏量,印刷时钢网与PCB的间隙越小越好。要实现面积比大于等于0.66,不是一件困难的工作,但是要消除钢网与PCB的间隙就是一件非常难的工作,这是因为钢网与PCB的间隙与PCB的设计、PCB的翘曲、印刷时PCB的支撑等很多因素有关,有时受制于产品设计和使用的设备是不可控的,而恰恰这是精细间距元器件组装的关键!像0.4mm引脚间距的CSP、多排引脚QFN、LGA、SGA的焊接不良几乎百分之百与此有关。因此,在先进的专业代工厂,发明了很多非常有效的PCB支撑工装,用于矫正PCB的翅曲,以保证零间隙印刷。
1.7 表面润湿与可焊性
表面润湿
表面润湿,是指焊接时熔融焊料铺展并覆盖在被焊金属表面上的现象。
润湿表示液态焊料与被焊接表面之间发生了溶解扩散作用,形成了金属间化合物(IMC),它是软钎焊接良好的标志。
当我们把一片固态金属片浸入液态焊料槽时,金属片和液态焊料间就产生接触,但这不意味着金属片已经被液态焊料所润湿,因为它们之间有可能存在着阻挡层,只有把小片金属从焊料槽中抽出才能看出是否润湿。
润湿只有在液态焊料和被焊金属表面紧密接触时才会发生,那时才能保证足够的吸引力。如果被焊表面上有任何牢固的附着污染物,如氧化膜,都会成为金属的连接阻挡层,从而妨碍润湿。在被污染的表面上,一滴焊料的表现和沾了油脂的平板上一滴水的表现是一样的,如图1-31所示,不能铺展,接触角θ大于90°。

图1-31 在氧化了平板上的焊料液滴无法润湿
如果被焊表面是清洁的,那么它们金属原子的位置紧靠着界面,于是发生润湿,焊料会铺展在接触的表面上,如图1-32所示。此时,焊料和基体原子非常接近,因而在彼此相吸的界面上形成合金,保证了良好的电接触与附着力。

图1-32 在清洁平板上的焊料液滴润湿并在界面生长出扩散层
可焊性
可焊性,是指被焊接母材在规定的时间、温度下能被焊接的能力。它与被焊接母材(元件或PCB焊盘)的热容量、加热温度以及表面清洁度有关。
可焊性,通常采用浸渍法或润湿平衡法评价,此两种方法本质上是一致的,就是看被焊接母材在规定的时间、温度下能否被润湿。因此,可以说可焊性与润湿性是密切相关的。
在浸渍法试验中,从熔融焊料槽中拿出的式样表面,可以观察到下列一个或几个现象。
(1)不润湿:表面又变成了未覆盖的样子,没有任何可见的与焊料的相互作用,被焊接表面保持了它原来的颜色。如果被焊表面上的氧化膜过厚,在有效的焊接时间内焊剂无法将其除去,这时就出现不润湿现象。
(2)润湿:把熔融的焊料排除掉,被焊接表面仍然保留了一层较薄的焊料,证明发生过金属间相互作用。完全润湿是指在被焊接金属表面留下一层均匀、光滑、无裂纹、附着好的焊料。
(3)部分润湿:被焊接表面一些地方表现为润湿,一些地方表现为不润湿。
(4)弱润湿:表面起初被润湿,但过后焊料从部分表面缩会成液滴,而在弱润湿过的地方留下很薄的一层焊料。
1.8 金属间化合物
1.8金属间化合物(1)
IMC
1.焊点的形成过程
焊点的形成过程可分为三个阶段:焊料润湿(铺展)、基底金属熔合/扩散和金属间化合物(IMC)的形成,如图1-33所示。

图1-33 焊接的工艺过程
2.金属间化合物
金属间化合物,英文全称为Intermetallic Compound,缩写为IMC,它是界面反应的产物,也作为形成良好焊点的一个标志。
在各种焊料合金中,大量的Sn是主角,它是参与IMC形成的主要元素。其余各元素仅起配角作用,主要是为了降低焊料的熔点以及压制IMC的生长,少量的Cu和Ni也会影响IMC的结构。
在有铅工艺条件下,锡铅焊料与Cu、Ni界面形成的IMC典型形态如图1-34所示。焊料中只有Sn参与IMC的形成,IMC的成分固定。

图1-34 Cu6Sn5与Ni3Sn4的形态
在无铅工艺条件下,由于使用的无铅焊料种类比较多,IMC的成分与形态比较复杂。如在使用SAC305焊料时,焊料与Ni基界面形成的IMC为(Cu、Ni)6Sn5和(Cu、Ni)3Sn4双层三元合金层,如图1-35 所示,这点不同于有铅焊接。

图1-35(Cu、Ni)6Sn5与(Cu、Ni)3Sn4的形态
1.8金属间化合物(2)
IMC的形成与发展
普遍认为,很厚的IMC是一种缺陷。因为IMC比较脆,与基材(封装时的电极、零部件或基板)之间的热膨胀系数差别很大,如果IMC长得很厚,就容易产生龟裂。因此,掌握界面反应层的形成和成长机理,对确保焊点的可靠性非常重要!
IMC的形成与发展,与焊料合金、基底金属类型、焊接的温度与时间以及焊料的流动状态有关。一般而言,在焊料熔点以下温度,IMC的形成以扩散方式进行,速度很慢,其厚度与时间开方成正比;在焊料熔点以上温度,IMC的形成以反应方式进行,温度越高、时间越长,其厚度越厚,如图1-36 所示。因此,过高的温度、过长的液态时间,将会导致过厚的IMC。

图1-36 IMC的生长厚度与温度的关系
在有铅工艺条件下,由于有Pb的抑制作用,Cu与SnPb焊料形成的IMC一般不超过2.5μm。但在无铅工艺条件下,由于Cu在熔融的SAC305中的熔解度比在Sn63/Pb37中的熔解度高8.6倍,因而在与SAC反应时会形成较厚的IMC层,这点不利于无铅焊点的可靠性。
还有一个现象值得进一步研究,就是当Cu与SAC305首次再流焊接(包括BGA植球过程)形成的IMC较厚时(≥10μm),如果再次过炉焊接,有可能形成超宽的、不连续的块状IMC,如图1-37所示。这是一种抗拉强度比较低的IMC组织,如果出现在BGA焊点上很可能带来可靠性方面的隐患。

图1-37 超宽、不连续的块状IMC
1.8金属间化合物(3)
与界面扩散有关的断裂失效
1.金脆失效
如果Au太厚(针对电镀Ni/Au而言,一般应小于0.08μm),则在使用过程中,弥散在焊料中的Au会扩散到Ni/Sn界面附近,形成带状(Ni-Au)Sn4金属间化合物。该IMC在界面上的富集常常导致金脆失效。
2.界面耦合现象
PCB焊盘界面上的反应不但与本界面有关,也与器件引脚材料及涂层有关。如焊盘为Ni/Au,而器件引线为Cu合金时,Cu常常会扩散到Ni/Sn界面从而导致界面形成(Cu、Ni)3Sn4—(Cu、Ni)6Sn5,它会导致焊点大规模失效。
3.kirkendall空洞
ENIG镀层容易发生著名的kirkendall空洞,如图1-38所示。

图1-38 kirkendall空洞现象
kirkendall空洞与高温老化时间有关,时间越长,空洞越多。如果在125℃条件下,40天就会形成连续的断裂缝。
1.9 黑盘
1.9黑盘(1)
黑盘
“黑盘”是由Puttlitz在1990年第一次提出的。
1.定义
因为焊点断裂面呈灰色、黑色,所以被称为黑盘,如图1-39所示。
与黑盘有关的断裂都发生在Sn—Ni界面的IMC下。焊盘颜色越深、IMC越薄,从黑色到黑灰色!

图1-39“黑盘”颜色
1.9黑盘(2)
2.与黑盘有关的三个典型特征
1)断裂面(IMC下)可以观察到腐蚀裂纹(泥浆裂缝),如图1-40所示。裂纹越多,焊点的连接强度越低(裂纹完全不润湿),也越难形成IMC。由于无铅焊点比较硬,受到应力后直接传导到界面,因此,无铅焊点因黑盘失效的情况更多见。

图1-40“黑盘”的泥浆裂缝特征
2)从磨光的横截面可以观察到“腐蚀”已经渗透,甚至穿透Ni层到Cu基体,俗称“金刺”特征,如图1-41所示。
黑盘

图1-41“黑盘”的“金刺”特征
3)Ni近表面P含量比较高(达到20%左右,为正常的两倍),但需要指出的是富磷不是导致焊点失效的直接原因。
1.10 工艺窗口与工艺能力
1.10工艺窗口与工艺能力(1)
工艺窗口
工艺窗口通常用来描述工艺参数可用的极限范围,是“用户规格范围(USL-LSL)”概念在SMT工艺领域的专业用语。
例如,按照经验,再流焊接的最低温度一般要比焊料熔点高11~12℃,当使用Sn63Pb37时,合金的熔点为183℃,其最低的再流焊接温度为195℃左右。在J-STD-020B中,规定元件的最高温度为245℃,这样有铅工艺可用的工艺窗口为50℃,而不是“245-183”所得的理论上的62℃。这里一定要注意“可用”两字。
1.10工艺窗口与工艺能力(2)
工艺窗口指数(PWI)
工艺窗口指数(Process Window Index,PWI),是衡量用户确定的工艺极限值范围内工艺能力适应程度的指标,换句话说,就是使用工艺窗口的最大百分比,用于简单说明工艺是否满足技术规范的要求,其值基本上是Cp倒数的百分数。PWI越大,工艺稳定性越差,反之,亦然。
PWI=100×Max{(测量值-平均极限值)/最大极限范围/2}
例如,贴片机的工艺窗口指数(见图1-42):

图1-42 PWI的概念
以再流焊接曲线为例说明,工艺曲线主要控制参数有升温速率、预热时间、预热结束时间、峰值温度和熔点以上时间,通过测量与计算,取四个参数中PWI最大的值作为温度曲线的PWI。
工艺能力指数(Cp)
工艺能力指数Cp,台湾企业称为制程能力指数。反映了用户的规格范围(δ)内有多少个6σ,数值越大,工艺的稳定性越高。
Cp=(USL-LSL)/6σ
其中,σ标准偏差,反映了数据各点到其平均数距离的平均值,即正态分布“钟”形图形的宽窄,越窄说明工艺能力越强;USL为用户规格上限,LSL为用户规格下限。
一般选取核心工艺指标进行测量。如再流焊接炉,我们可以测量峰值温度的在不同负载率的情况下的波动。
工艺能力管理指数(Cp k)
工艺能力管理指数 Cpk,反映的是正态分布“钟”形图形的居中性,即 Cp k=(USL-μ)/3σ或(μ-LSL)/3σ的最小值。其中μ为用户规格的中心值。
注意最小值的概念。
1.11 焊点质量判别
1.11焊点质量判别(1)
插装元器件焊点
焊点质量的判别,一般按照IPC-A-610的要求进行外观检查。由于焊点类别有多种,难以简单的描述,因此,IPC把焊点分解为多个维度用单一要求进行评价。这是处理复杂问题的一种方法,值得学习。
插装元器件焊点的合格要求如图1-43所示。

图1-43 插装元器件焊点的合格要求
底部焊端
底部焊端焊点的合格要求如图1-44所示。

图1-44 底部焊端焊点的合格要求
1.11焊点质量判别(2)
冒形端电极(电阻、电容、MELF,包括1,7,5焊接面)
冒形端电极焊点的合格要求如图1-45所示。

图1-45 冒形端电极焊点的合格要求
L形引脚(QFP、SOP)
L形引脚焊点的合格要求如图1-46所示。

图1-46 翼形引脚焊点的合格要求
1.11焊点质量判别(3)
J形引脚(PLCC)
J形引脚焊点的合格要求如图1-47所示。

图1-47 J形引脚焊点的合格要求
球形引脚(BGA、CSP)
球形引脚焊点的合格要求如图1-48所示。

图1-48 球形引脚焊点的合格要求
X射线影像中,空洞面积不超过焊点面积的25%;
焊点圆而均匀,边界清晰;
塌落高度符合要求;
焊点无桥接、球窝、冷焊、开焊;
注意:IPC-A-610C标准可接受条件为偏移25%,其D版本不再以偏移为标准。
PQFN
PQFN焊点的合格要求如图1-49所示。

图1-49 PQFN焊点的合格要求
1.11焊点质量判别(4)
城堡形焊点的合格要求如图1-50所示。

图1-50 城堡形焊点的合格要求
城堡形(CLCC)
1.12 片式元件焊点剪切力范围
1.12片式元件焊点剪切力范围(1)
推力范围
由于各家公司使用的焊盘尺寸不同以及元件封装尺寸公差比较大的原因,IPC标准没有给出每类封装的剪切力标准,也没有给出焊点剪切力与可靠性之间有什么对应关系。
根据IPC标准焊盘设计的试验板所做的片式元件焊点的剪切力实验结果见表1-2。
表1-2 片式元件焊点的剪切力(参考)

1.12片式元件焊点剪切力范围(2)
推力范围
说明:
(1)本表数据摘自《电子工艺技术》2010年第4期《片式元件焊点剪切力比较实验研究》一文;
(2)实验条件:
FR-4,元件与焊盘镀层Sn63/Pb37。
实验设备,WDW-500万能实验机。
(3)测试方法:
实验依据标准为:日本JIS Z7198-7。
实验卡具距PCB的间隙小于元件厚度的1/4,移动速度5~30mm/min,如图1-51所示。

图1-51 剪切实验示意图
说明
有些工厂用推力计检测焊接的强度,但需要注意到推力计测量的推力不等于剪切力,因为推力方向不完全相同,手持推力计推力方向一般为45°。表1-3是两家公司有铅焊点的标准,可参考。
表1-3 采用推力计焊点强度的判断标准

1.13 P-BGA封装体翘曲与吸潮量、温度的关系
1.13 P-BGA封装体翘曲与吸潮量、温度的关系(1)
P-BGA的变形规律
由于P-BGA的结构类似双金属片的原理,焊接温度越高,P-BGA的变形也越大,焊接的问题也越多。
BGA的变形,通常采用莫尔条纹法(Shandow moire)进行测量。
P-BGA的内部构造如图1-52 所示,随温度的翘曲变形一般规律如图1-53所示。

图1-52 P-BGA的一般内部构造

图1-53 P-BGA变形规律
1.13 P-BGA封装体翘曲与吸潮量、温度的关系(2)
P-BGA的变形规律
常见的问题:
(1)导致焊点热应力断裂;
(2)导致BGA四脚焊点桥连,如图1-54所示。

图1-54 角部焊点桥连机理
危害
温度、吸潮、尺寸对翘曲变形量的影响
湿度、温度对P-BGA翘曲变形的影响,参考图1-55和图1-56所示。

图1-55 湿度对翘曲变形的影响

图1-56 温度、尺寸对翘曲变形的影响
1.13 P-BGA封装体翘曲与吸潮量、温度的关系(3)
温度、吸潮、尺寸对翘曲变形量的影响
BGA翘曲变形对焊接良率的影响,参考图1-57所示。

图1-57 BGA翘曲变形对短路的影响
组装质量与翘曲变形量的关系
1.14 PCB的烘干
1.14 PCB的烘干(1)
吸潮水平与时间的关系
PCB在无铅工艺条件下,属于湿度敏感材料。如果不进行防潮包装,3个月后吸潮就可能引发PCB焊接时分层,如图1-58所示。

图1-58 分层
1.14 PCB的烘干(2)
吸潮水平与时间的关系
PCB的吸潮并非与时间成线性关系,很多时候表现为加速吸潮的关系,见表1-4、表1-5。
表1-4 储存3个月的吸潮水平

表1-5 储存4.5个月的吸潮水平

烘干
为了保证PCB的含水量低于0.1%,生产上一般采用125℃/5h的烘干工艺,这个条件远低于IPC标准规定的时间,但是实践表明是可行和有效的。
一般而言,使用双氰胺(dicy)作固化剂的板材容易吸潮。从实践看,无铅PCB应采用酚醛树脂(PN)作固化剂的板材。
由于无铅PCB焊接温度很高,吸潮后很容易分层。因此,无铅PCB的储存期不要超过3个月,这是一个重要的经验!
1.15 焊点可靠性与失效分析的基本概念
1.15焊点可靠性与失效分析的基本概念(1)
基本概念
1)可靠性
可靠性是指产品(这里指焊点)在给定的条件下和规定的时间内完成规定功能的能力。它是相对于一定载荷条件的概率,所以可靠性一定是指在某种载荷条件下的可靠性。
不同的电子产品其载荷条件会有所不同,比如汽车电子系统,它受到的是一种环境冷热周期性的载荷和振动载荷。热循环试验就是模仿这种热机械载荷来分析焊点的失效原因。
载荷条件是指任何加在系统上,使系统的性能恶化或影响可靠性的条件。载荷是一个广义的载荷,如热冲击、热循环,温度、湿度、电压、电流、机械振动等。
2)失效(Failure)
失效,丧失功能或降低到不能满足规定要求的现象。
3)失效模式(Failure Mode)
失效模式,失效现象的表现形式,与产生的原因无关,如开路、短路、参数漂移、不稳定等。
4)失效机理(Failure Mechanism)
失效机理,也就是因物理的、化学的、机械的等多种原因而使产品产生失效的过程,如蠕变-应力释放断裂、拉伸断裂、裂纹扩展断裂、电迁移短路,工程上有时也会把原因说成是失效机理。
之所以区别失效模式和失效机理,是因为有时相同的失效模式不一定是由同样的失效机理造成的,相反,相同的失效机理,在发生失效的形态上却存在着不同的失效模式。例如,代表半导体电路故障的“电迁移”,就其发生的形态,会形成短路、开路、特性恶坏等多种失效模式。
5)加速试验
加速试验,是一种快速试验方法。它是通过采用比设备(这里指焊点)在正常使用中所经受的环境更为严酷的试验环境来实现这一点的。由于使用了更高的应力,在进行加速试验时必须注意不能引入在正常使用中不会发生的失效模式。加速试验主要分为两类,每一类都有明确的目的:
(1)加速寿命试验——估计寿命;
(2)加速应力试验——确定(或证实)和纠正薄弱环节。
常用的加速试验有:
(1)周期固定的周期性应力试验(如热循环试验、热冲击试验);
(2)步进应力谱试验;
(3)渐进应力谱试验;
(4)高加速寿命试验(HALT)(设备级);
(5)高加速应力筛选(HASS)(设备级);
(6)高加速温度和湿度应力试验(HAST)(零件级)。
注意,在高可靠电子产品生产中用到环境应力筛选(ESS)试验,不是加速试验,它是一种消除缺陷焊点的筛选方法。
1.16 如何做工艺
1.16如何做工艺(1)
体会
1)工艺质量的控制
工艺质量控制的核心是工艺设计。
道理很简单,从工艺质量控制的“人、机、料、环、法”看,由“人、机、环”构成的现场工艺,除了“换换焊膏、修修钢网、调调曲线”,基本就做不了什么了。同样,“料”基本也没有多大的改善余地。真正能够影响的就只有“法”,而这个“法”的核心就是工艺设计。
工艺设计的对象是元器件的封装及其焊点,如图1-59所示。

图1-59 工艺设计的基准
2)基本认识
(1)工艺工作是系统工程。要获得稳定的工艺必须对物料、设计、现场工艺进行系统考虑、系统设计、系统管控,绝不可只盯住SMT环节。否则,将没完没了地现场“救火”。只有把工艺工作看做系统工程,从物料、设计、试制、控制等全过程进行有效控制,才能获得稳定的工艺。
(2)看问题要看本质。例如,0.5mm间距CSP球窝现象与0201葡萄球现象,表面看是两个问题,实质上都是一个微焊盘焊接的技术问题——焊盘小,焊膏就少;焊膏少,焊剂就少;焊剂少,去氧化物能力就弱,从而导致球窝现象或葡萄球现象。
(3)“经验”必须与时俱进。无铅焊膏与有铅焊膏组成和要求不同,决不能以有铅的概念考虑无铅的工艺问题。如有铅再流焊温度曲线,一般分为三段,但无铅就必须分为五段来考虑!熔点前后必须给于单独考虑!
(4)不能以现场的个案经验作普适原则,更不能以“道听途说”作原则。现场所用的方法解决了问题,但决不能认为彻底解决了问题。真正有效的解决方法,必须建立在系统的试验基础上,经得起工艺因素波动的考验。
(5)工艺是一门实践性很强的技术。工艺能力的提升,建立在“发现问题—解决问题—规范—控制”的实践经验基础上,在日本把这个过程叫做“学习故障,消除预期故障”。